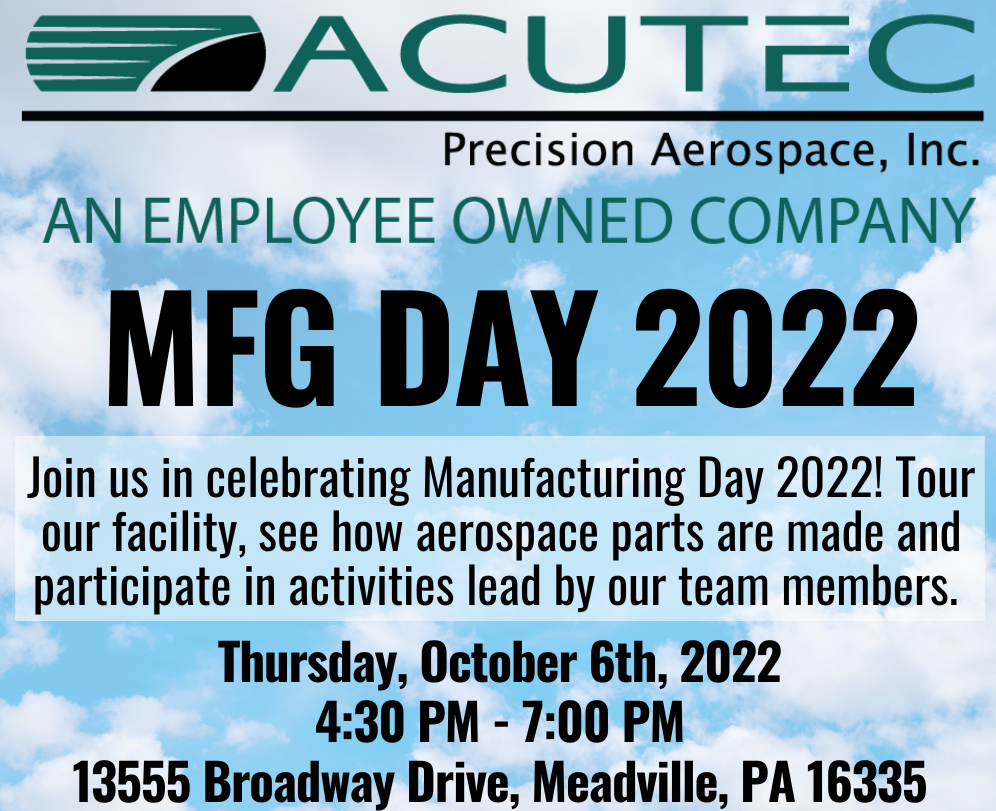
Dallas has a thriving, large and growing manufacturing industry. The city's reputation as a top-notch manufacturing center for everything from computers to medical devices to consumer electronics is world-class. Dallas is home to major high-tech firms such as Texas Instruments or Lockheed Martin.
Dallas Fed, which conducts state's factory survey monthly, estimates that manufacturing jobs grew in 2016 at a rate of 3.5 percent. This is lower than overall economic growth. About 2.2m jobs are supported by manufacturing, which includes those of various related industries.
The manufacture of computer and electronic products is an important, large subsector in the Texas manufacturing industry, with a Gross State Product (GSP) in 2015 of about $28,7 billion dollars. The Brookings Institution considers computer and electronic products manufacturers to be advanced manufacturing industries because they have a high share of workers with higher levels of scientific knowledge than the national average.
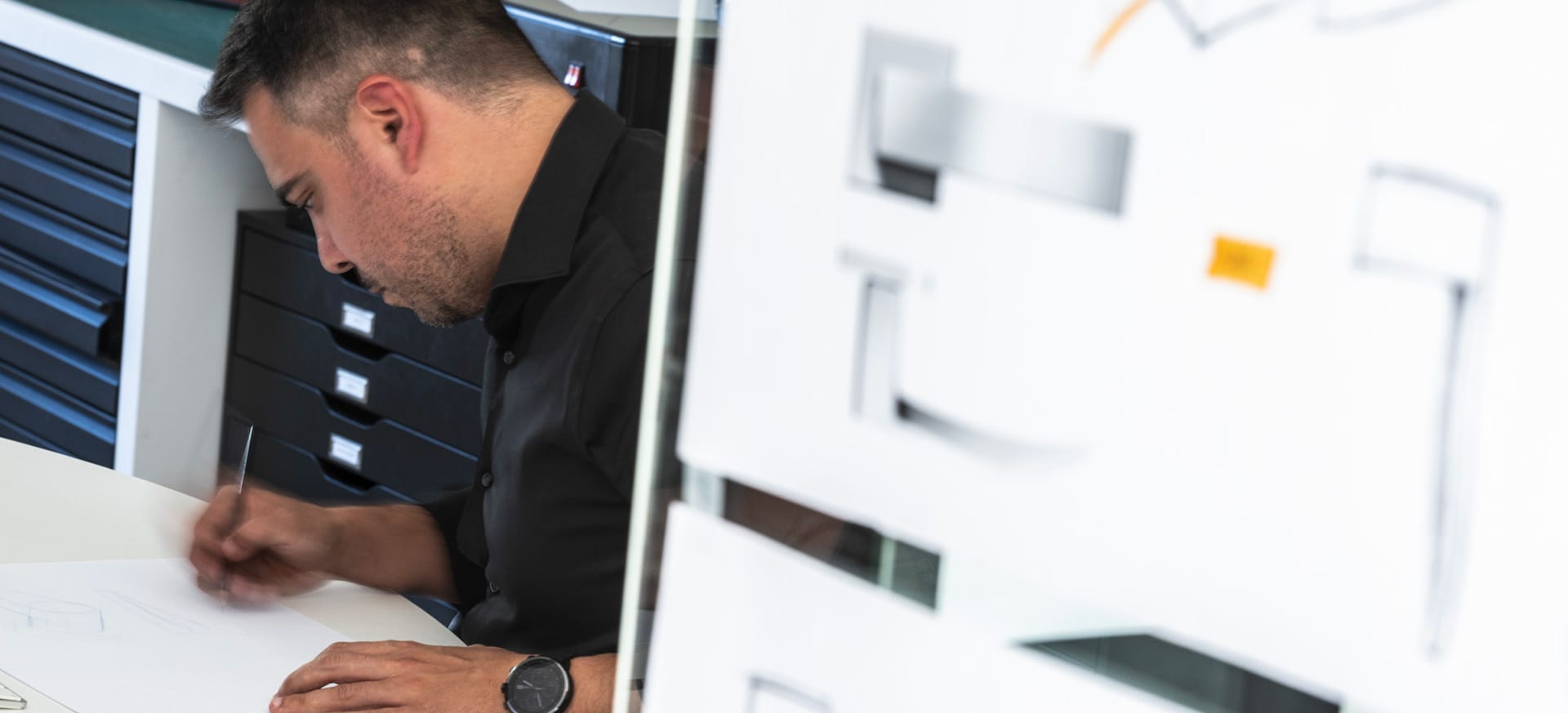
Texas is home to a large manufacturing sector that includes machine tool and machinery manufacturing. The subsector includes producers of mining, agricultural, construction and industrial machines. TWC estimates that this subsector creates about 88,000 manufacturing and support jobs in Texas, with another 117,000 indirectly.
This highly-industrialized subsector supports an enormous number of jobs across other sectors. It contributes around $11.3 billion annually to the economy and pays an average salary of approximately $98,000. The industry employs many scientists, technicians and engineers.
Manufacturers who specialize in fabricated metal products make a wide range of products, from cutlery to shipping containers. Houston's subsector employs 118,000 Texans.
TWC's estimates indicate that during the oil slump of 2015, this sector lost a few positions. However, in 2016, it recovered rapidly. The subsector is comprised of manufacturers of boilers, valves and heat-exchangers for the chemical and petrochemical industries along upper Gulf Coast.
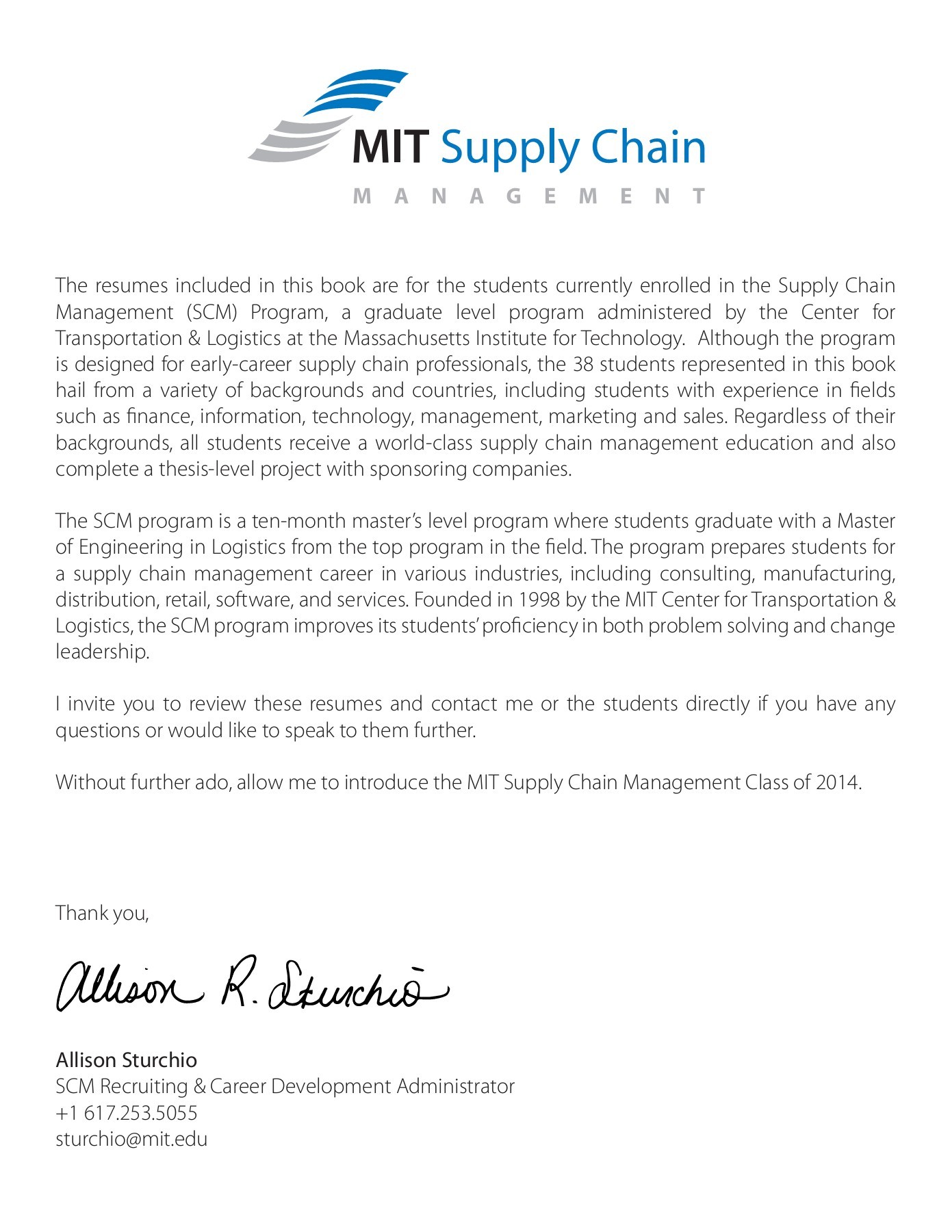
In addition to fabricated metal production, other important subsectors in this category include automotive parts, and equipment and parts used in aerospace and railroad rolling stock. According to Brookings, these are highly advanced industries when it comes to research and development expenditure per worker.
It is important to understand your worth and how you can improve it by acquiring the right skills. The best way to achieve this is to partner with a contract manufacturing firm that can provide you with specialized services and expertise in production disciplines like 6S, Lean manufacturing, ISO and GMP. These services will help you to improve your bottom-line and become more competitive on the market.
FAQ
Do we need to know about Manufacturing Processes before learning about Logistics?
No. No. Knowing about manufacturing processes will help you understand how logistics works.
Can certain manufacturing steps be automated?
Yes! Yes. Automation has been around since ancient time. The Egyptians invented the wheel thousands of years ago. Robots are now used to assist us in assembly lines.
Actually, robotics can be used in manufacturing for many purposes. These include:
-
Automated assembly line robots
-
Robot welding
-
Robot painting
-
Robotics inspection
-
Robots that create products
Automation could also be used to improve manufacturing. For instance, 3D printing allows us make custom products and not have to wait for months or even weeks to get them made.
Is automation important in manufacturing?
Not only are service providers and manufacturers important, but so is automation. It allows them provide faster and more efficient services. In addition, it helps them reduce costs by reducing human errors and improving productivity.
What do you mean by warehouse?
A warehouse, or storage facility, is where goods are stored prior to being sold. It can be an indoor space or an outdoor area. In some cases it could be both indoors and outdoors.
What is the difference between manufacturing and logistics
Manufacturing is the process of creating goods from raw materials by using machines and processes. Logistics manages all aspects of the supply chain, including procurement, production planning and distribution, inventory control, transportation, customer service, and transport. Manufacturing and logistics can often be grouped together to describe a larger term that covers both the creation of products, and the delivery of them to customers.
How is a production manager different from a producer planner?
The major difference between a Production Planner and a Project Manager is that a Project Manager is often the person responsible for organizing and planning the entire project. While a Production Planner is involved mainly in the planning stage,
Statistics
- (2:04) MTO is a production technique wherein products are customized according to customer specifications, and production only starts after an order is received. (oracle.com)
- In 2021, an estimated 12.1 million Americans work in the manufacturing sector.6 (investopedia.com)
- Many factories witnessed a 30% increase in output due to the shift to electric motors. (en.wikipedia.org)
- According to the United Nations Industrial Development Organization (UNIDO), China is the top manufacturer worldwide by 2019 output, producing 28.7% of the total global manufacturing output, followed by the United States, Japan, Germany, and India.[52][53] (en.wikipedia.org)
- Job #1 is delivering the ordered product according to specifications: color, size, brand, and quantity. (netsuite.com)
External Links
How To
Six Sigma in Manufacturing:
Six Sigma can be described as "the use of statistical process control (SPC), techniques to achieve continuous improvement." Motorola's Quality Improvement Department, Tokyo, Japan, developed it in 1986. Six Sigma's basic concept is to improve quality and eliminate defects through standardization. This method has been adopted by many companies in recent years as they believe there are no perfect products or services. Six Sigma's primary goal is to reduce variation from the average value of production. If you take a sample and compare it with the average, you will be able to determine how much of the production process is different from the norm. If this deviation is too big, you know something needs fixing.
The first step toward implementing Six Sigma is understanding how variability works in your business. Once you've understood that, you'll want to identify sources of variation. Also, you will need to identify the sources of variation. Random variations are caused when people make mistakes. While systematic variations are caused outside of the process, they can occur. These are, for instance, random variations that occur when widgets are made and some fall off the production line. If however, you notice that each time you assemble a widget it falls apart in exactly the same spot, that is a problem.
Once you have identified the problem, you can design solutions. It might mean changing the way you do business or redesigning it entirely. You should then test the changes again after they have been implemented. If they don’t work, you’ll need to go back and rework the plan.