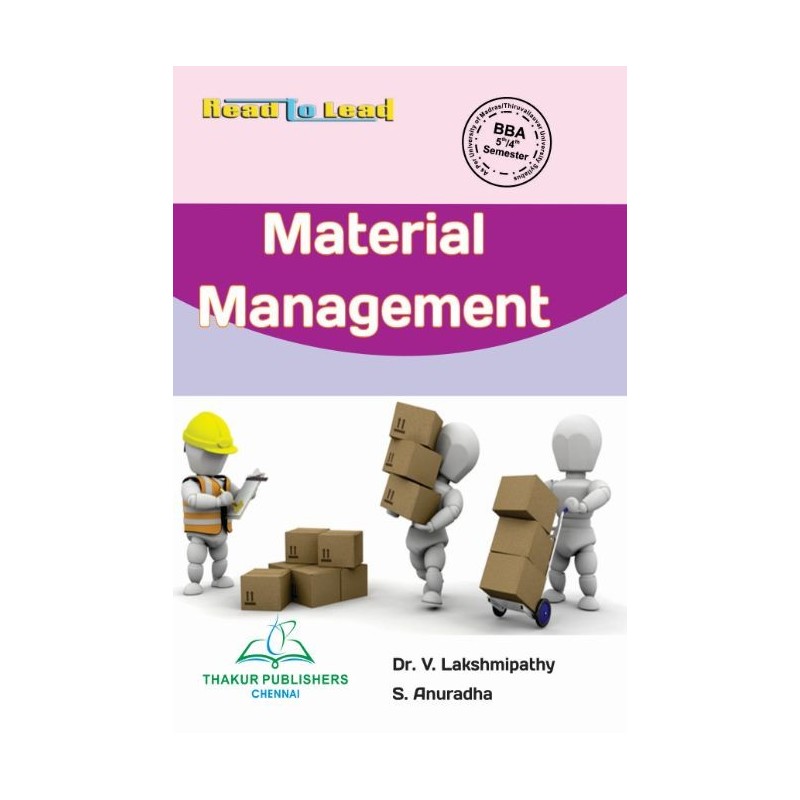
Durable goods are products that do not wear out easily and last a long time. They are not like nondurable products, which can be used only once. These products are durable, meaning they can continue to offer the same or more utility for many years. A car that's durable will serve you for many years.
Nondurable goods may be consumed immediately
Nondurable goods, unlike durable goods, have a short lifespan and are usually consumed quickly. Consumers tend to save money on nondurable goods during recessions, but they continue to buy durable goods. These items often have low prices, and can be purchased using cash. Examples of nondurable goods include meat, fruits, vegetables, dairy products, and bakery products. Other examples include detergent, dish soap, and cosmetics.
Nondurable goods are generally the cheapest type of goods. They last less three years. Nondurable goods can be bought relatively frequently, which allows consumers to purchase them often without worrying about their future value. Nondurable goods, like packaged food or laundry detergent, are often disposable and can only be purchased once. However, service goods are tangible and are made to meet consumer demands. Customers plan their purchases based upon how they perceive the product. This can differ depending on its price.
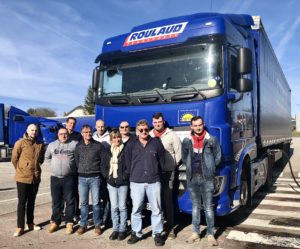
Durable goods on the other side are those products that will provide a continuous stream of utility over time. These products are commonly called consumer durables and include automobiles and household furniture, sporting goods and jewelry. Durables are more popular during economic booms, while nondurables can be bought in periods of economic recession.
Durable goods last longer than one year
Durable goods refer to tangible commodities that can last for at most one year when used as intended. You can divide them into two groups: consumer durables or producer durables. Consumer durables can include household goods like furniture, boats, and cars. Producer durables can include machinery, appliances, fine jewelry, as well as machinery.
Durable goods are expected to last at least three years, but they may require servicing or repair. Durable goods are designed to be durable and last for many years. Durable goods can be extended by proper care and maintenance for as long as 20 years.
The demand for durable goods can be a key economic indicator when the economy is growing. In order to increase employment and improve investment returns, durable goods should be sold more often. On the other hand, declining sales of durable products could signal a decline economic activity. This means that consumers spend less on new products and more on repair and maintenance of existing products. The result could be a slowdown or recession in durable goods.
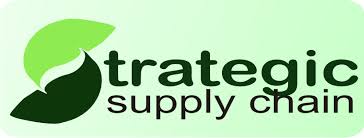
Impact of COVID-19 pandemic on durable goods
COVID-19 is a pandemic that has caused widespread illness and has had an impact on consumer spending, especially on durable goods. People stopped going to the gym and stopped attending social events as a result of the disease. The disease also caused people to stop hailing cabs. This resulted in a drop in consumer spending. Instead, people spent more time at home doing house production and leisure activities. This reduced consumer spending on services and restaurants.
The US economy has suffered a severe economic impact from the COVID-19 epidemic. The disease not only increased the demand for durable goods but also prompted strong fiscal policies to increase household disposable income. This may account for at least half the increase in durable goods consumer spending in 2020.
Individuals, communities and businesses have been affected by the COVID-19 pandemic. While attention has been focused on the effect on fast-moving items, less has been done on the impact on durable goods. NielsenIQ BASES has revealed that more than a third have purchased durable goods in response to the illness. Many consumers have also noticed a change in their purchasing habits due to the disease. This is because they spend more time at home with their children.
FAQ
What is production planning?
Production Planning is the creation of a plan to cover all aspects, such as scheduling, budgeting. Location, crew, equipment, props and other details. This document ensures that everything is prepared and available when you are ready for shooting. It should also contain information on achieving the best results on set. It should include information about shooting locations, casting lists, crew details, equipment requirements, and shooting schedules.
First, you need to plan what you want to film. You may already know where you want the film to be shot, or perhaps you have specific locations and sets you wish to use. Once you have identified your locations and scenes it's time to begin figuring out what elements you will need for each one. For example, you might decide that you need a car but don't know exactly what model you want. To narrow your options, you can search online for available models.
Once you have found the right vehicle, you can think about adding accessories. You might need to have people in the front seats. Maybe you need someone to move around in the back. Maybe you want to change the interior color from black to white? These questions will help to determine the style and feel of your car. It is also worth considering the types of shots that you wish to take. What type of shots will you choose? Maybe you want to show the engine and the steering wheel. These things will help you to identify the car that you are looking for.
Once you have determined all of the above, you can move on to creating a schedule. You can use a schedule to determine when and where you need it to be shot. The schedule will show you when to get there, what time to leave, and when to return home. So everyone is clear about what they need to do. Book extra staff ahead of time if you need them. It's not worth paying someone to show up if you haven't told him.
Your schedule will also have to be adjusted to reflect the number of days required to film. Some projects may only take a couple of days, while others could last for weeks. It is important to consider whether you require more than one photo per day when you create your schedule. Multiple takes at the same place will result in higher costs and longer completion times. If you are unsure if you need multiple takes, it is better to err on the side of caution and shoot fewer takes rather than risk wasting money.
Budget setting is another important aspect in production planning. A realistic budget will help you work within your means. You can always lower the budget if you encounter unexpected problems. But, don't underestimate how much money you'll spend. Underestimating the cost will result in less money after you have paid for other items.
Planning production is a tedious process. Once you have a good understanding of how everything works together, planning future projects becomes easy.
What does "warehouse" mean?
Warehouses and storage facilities are where goods are kept before being sold. It can be indoors or out. Sometimes, it can be both an indoor and outdoor space.
How can manufacturing avoid production bottlenecks
The key to avoiding bottlenecks in production is to keep all processes running smoothly throughout the entire production cycle, from the time you receive an order until the time when the product ships.
This includes both planning for capacity and quality control.
Continuous improvement techniques such Six Sigma can help you achieve this.
Six Sigma Management System is a method to increase quality and reduce waste throughout your organization.
It emphasizes consistency and eliminating variance in your work.
Is automation necessary in manufacturing?
Automating is not just important for manufacturers, but also for service providers. It allows them provide faster and more efficient services. It helps them to lower costs by reducing human errors, and improving productivity.
What skills are required to be a production manager?
Production planners must be flexible, organized, and able handle multiple tasks. You must also be able to communicate effectively with clients and colleagues.
Why automate your factory?
Modern warehousing is becoming more automated. With the rise of ecommerce, there is a greater demand for faster delivery times as well as more efficient processes.
Warehouses need to adapt quickly to meet changing needs. To do so, they must invest heavily in technology. Automating warehouses has many benefits. Here are some benefits of investing in automation
-
Increases throughput/productivity
-
Reduces errors
-
Increases accuracy
-
Boosts safety
-
Eliminates bottlenecks
-
Allows companies to scale more easily
-
Makes workers more efficient
-
It gives visibility to everything that happens inside the warehouse
-
Enhances customer experience
-
Improves employee satisfaction
-
Minimizes downtime and increases uptime
-
This ensures that quality products are delivered promptly
-
Human error can be eliminated
-
It ensures compliance with regulations
Statistics
- In the United States, for example, manufacturing makes up 15% of the economic output. (twi-global.com)
- [54][55] These are the top 50 countries by the total value of manufacturing output in US dollars for its noted year according to World Bank.[56] (en.wikipedia.org)
- According to a Statista study, U.S. businesses spent $1.63 trillion on logistics in 2019, moving goods from origin to end user through various supply chain network segments. (netsuite.com)
- It's estimated that 10.8% of the U.S. GDP in 2020 was contributed to manufacturing. (investopedia.com)
- (2:04) MTO is a production technique wherein products are customized according to customer specifications, and production only starts after an order is received. (oracle.com)
External Links
How To
Six Sigma in Manufacturing
Six Sigma is defined by "the application SPC (statistical process control) techniques to achieve continuous improvements." Motorola's Quality Improvement Department developed it at their Tokyo plant in Japan in 1986. The basic idea behind Six Sigma is to improve quality by improving processes through standardization and eliminating defects. Since there are no perfect products, or services, this approach has been adopted by many companies over the years. Six Sigma seeks to reduce variation between the mean production value. If you take a sample and compare it with the average, you will be able to determine how much of the production process is different from the norm. If it is too large, it means that there are problems.
The first step toward implementing Six Sigma is understanding how variability works in your business. Once you understand that, it is time to identify the sources of variation. It is important to identify whether the variations are random or systemic. Random variations are caused by human errors. Systematic variations can be caused by outside factors. For example, if you're making widgets, and some of them fall off the assembly line, those would be considered random variations. But if you notice that every widget you make falls apart at the exact same place each time, this would indicate that there is a problem.
Once you identify the problem areas, it is time to create solutions. It might mean changing the way you do business or redesigning it entirely. To verify that the changes have worked, you need to test them again. If they don’t work, you’ll need to go back and rework the plan.