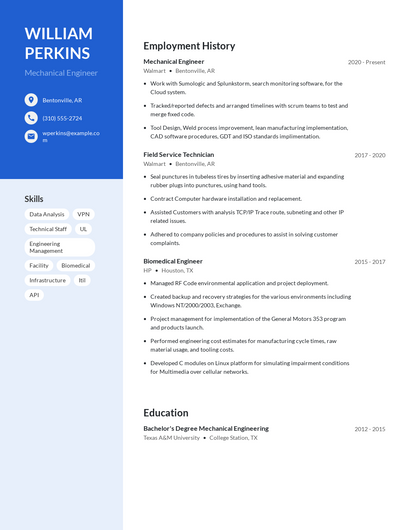
It's more than installing new technology. It's about changing your factory's mindset and adapting to new demands. With the right technology, you can help your customers, and help your business succeed in a new phase of manufacturing.
It is important to first decide what you want. A smart factory could be built to respond to extreme fluctuations in demand. Perhaps you want to support your global supply chains partners by building a smart plant. You may also want to build a smart factory to respond to an industry heavily dependent on manual labor. No matter what your goal, the next step in building an ecosystem to support it is to create that ecosystem.
Lack of connectivity is one key barrier to smart factories. This can be difficult to overcome when you have old machinery and equipment. It might also be difficult to find the right information about your machines or systems. The study showed that 33% thought a lack in IT infrastructure was a major barrier to smart factories.
Technology is the second most important factor. There are many advanced manufacturing technologies available. These technologies can be used to improve your quality and productivity. You can also use these technologies to make your plant more affordable.
Another factor to consider is people. You need to make investments in the right skill sets at the right times. You will need the right people as well as a talent strategy. It is important to have a clear scope and align everyone's priorities and timelines. You need to make sure that the right people are working on the right projects.
Process is the third most important aspect to be considered. You need to make sure that your applications and processes are able to connect to a network. This will make it possible to share information with other factories and systems. Last but not least, make sure you have analytics and data in place. This will enable you to make data-driven decision and self-heal.
People are the fourth most crucial factor. Your executive team must be committed to the initiative. It can help to have a convener that can help coordinate and align efforts across multiple vendors. It is also a good idea to have a convener who can coordinate and align efforts across multiple vendors.
Security is the fifth most critical factor. There are new technologies available that are designed to reduce the risk of cyberattacks in manufacturing environments. You should make sure that you have the best cybersecurity strategy. Also, you need to make sure that your cybersecurity strategy is always in place.
The final thing you should consider is how you will link your machines and equipment. Your current solutions are fine, but it might be worth exploring new options. This will help to create new data set that you can use for your smart factory projects.
FAQ
How is a production manager different from a producer planner?
The difference between a product planner and project manager is that a planer is typically the one who organizes and plans the entire project. A production planner, however, is mostly involved in the planning stages.
How important is automation in manufacturing?
Automation is important not only for manufacturers but also for service providers. It enables them to provide services faster and more efficiently. It helps them to lower costs by reducing human errors, and improving productivity.
Is it possible to automate certain parts of manufacturing
Yes! Yes! Automation has existed since ancient times. The Egyptians created the wheel thousands years ago. We now use robots to help us with assembly lines.
There are many applications for robotics in manufacturing today. These include:
-
Automated assembly line robots
-
Robot welding
-
Robot painting
-
Robotics inspection
-
Robots create products
Manufacturing can also be automated in many other ways. 3D printing is a way to make custom products quickly and without waiting weeks or months for them to be manufactured.
Statistics
- (2:04) MTO is a production technique wherein products are customized according to customer specifications, and production only starts after an order is received. (oracle.com)
- In the United States, for example, manufacturing makes up 15% of the economic output. (twi-global.com)
- You can multiply the result by 100 to get the total percent of monthly overhead. (investopedia.com)
- Job #1 is delivering the ordered product according to specifications: color, size, brand, and quantity. (netsuite.com)
- It's estimated that 10.8% of the U.S. GDP in 2020 was contributed to manufacturing. (investopedia.com)
External Links
How To
How to use the Just-In Time Method in Production
Just-in time (JIT), is a process that reduces costs and increases efficiency in business operations. It's a way to ensure that you get the right resources at just the right time. This means that only what you use is charged to your account. Frederick Taylor developed the concept while working as foreman in early 1900s. Taylor observed that overtime was paid to workers if they were late in working. He then concluded that if he could ensure that workers had enough time to do their job before starting to work, this would improve productivity.
JIT is a way to plan ahead and make sure you don't waste any money. You should also look at the entire project from start to finish and make sure that you have sufficient resources available to deal with any problems that arise during the course of your project. If you expect problems to arise, you will be able to provide the necessary equipment and personnel to address them. You won't have to pay more for unnecessary items.
There are different types of JIT methods:
-
Demand-driven JIT: You order the parts and materials you need for your project every other day. This will allow for you to track the material that you have left after using it. This will allow you to calculate how long it will take to make more.
-
Inventory-based: This type allows you to stock the materials needed for your projects ahead of time. This allows you to predict how much you can expect to sell.
-
Project-driven : This is a method where you make sure that enough money is set aside to pay the project's cost. You will be able to purchase the right amount of materials if you know what you need.
-
Resource-based JIT: This is the most popular form of JIT. Here, you allocate certain resources based on demand. You might assign more people to help with orders if there are many. If you don’t have many orders you will assign less people to the work.
-
Cost-based : This is similar in concept to resource-based. But here, you aren't concerned about how many people your company has but how much each individual costs.
-
Price-based: This approach is very similar to the cost-based method except that you don't look at individual workers costs but the total cost of the company.
-
Material-based: This approach is similar to cost-based. However, instead of looking at the total cost for the company, you look at how much you spend on average on raw materials.
-
Time-based: Another variation of resource-based JIT. Instead of focusing on the cost of each employee, you will focus on the time it takes to complete a project.
-
Quality-based: This is yet another variation of resource-based JIT. Instead of looking at the labor costs and time it takes to make a product, think about its quality.
-
Value-based JIT: One of the most recent forms of JIT. This is where you don't care about how the products perform or whether they meet customers' expectations. Instead, your goal is to add value to the market.
-
Stock-based: This is an inventory-based method that focuses on the actual number of items being produced at any given time. It's used when you want to maximize production while minimizing inventory.
-
Just-intime planning (JIT), is a combination JIT/sales chain management. It is the process that schedules the delivery of components within a short time of their order. It's important as it reduces leadtimes and increases throughput.