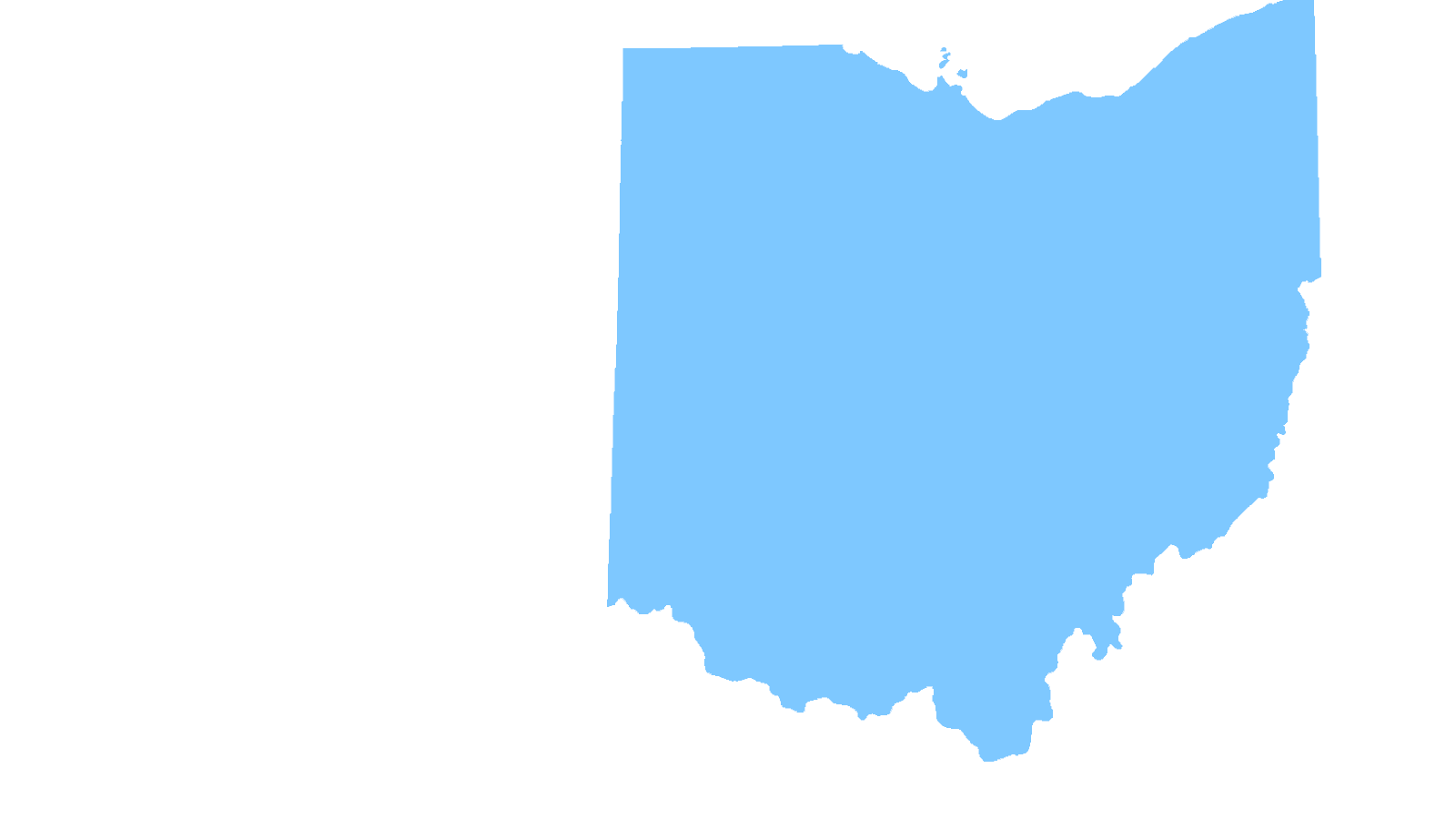
Lean 5 principles encourage the elimination and reduction of waste. Value stream mapping is also encouraged by the principles to help identify more efficient activities. The key to eliminating waste is to differentiate value-added (necessary) waste from non-value-added (unnecessary) waste. The simplest process can be made to use the most energy and time. This helps produce the highest quality products in the shortest amount of time, while keeping customers satisfied.
Value
The Value of the Lean 5 principles can help you improve your manufacturing process by eliminating waste. By identifying and eliminating the steps that do not add value, you can create a smooth flow from production to shipping. The process also eliminates excess inventory and helps you reduce work in progress and save time.
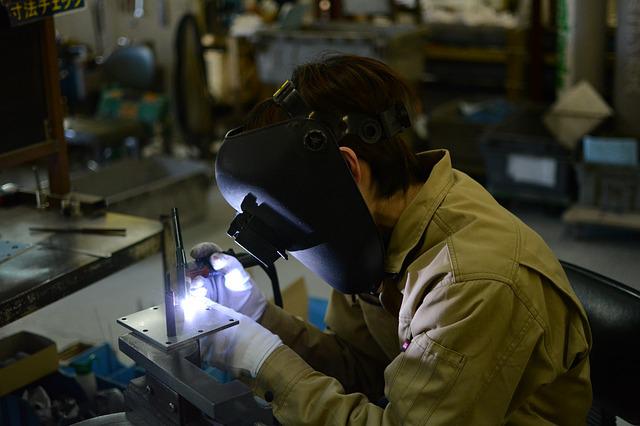
Value stream
The value stream of Lean Manufacturing is a way to eliminate waste from manufacturing processes. This process maps each step in a process and identifies the essential elements. It also eliminates those elements that aren't necessary. The entire life cycle of a product is considered when calculating the value stream. This includes the creation of the product, its use and eventual disposal. This is the key to eliminating all waste. There are three types of waste in a value stream.
Flow
The first of the five lean principles, flow, involves identifying customer needs and evaluating those. This is crucial for the development of new products or services, as customers don't always communicate their needs clearly. The second step in the process is to determine the value stream. It's the sequence of activities required to complete the project. This requires close collaboration from all project participants.
Pull
In a pull-system, a process starts only when there's a customer order. A pizza shop would not produce extra pizzas if they had received a customer order. They would waste time, resources and ingredients otherwise.
Perfection
One of the five lean principles is perfection. This concept defines perfection as a state that is perfect, precise, consistent, and complete. But perfection is not possible. The purpose of this concept is to encourage continuous improvement. Organizations can achieve a higher performance level by doing this.
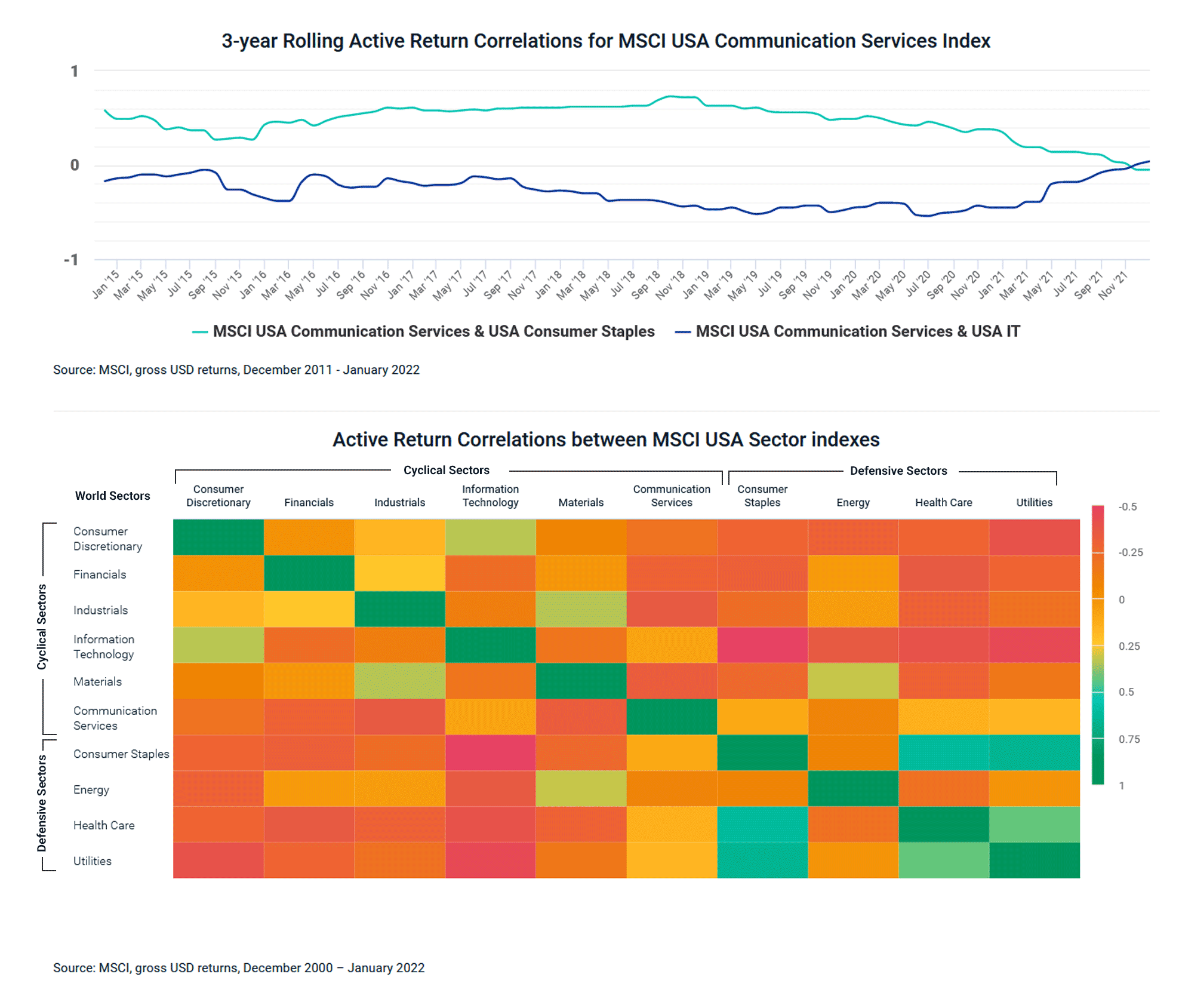
Collaboration of stakeholders
Collaboration with stakeholders is key to lean project management. It entails collaboration between project team members to solve problems and increase project value. Teams need to identify potential problems and areas for improvement during the planning stage. The doing phase is less about execution and more about gathering information that will assist them in their search for solutions. For collaboration, the team must also take into consideration the organizational structure.
FAQ
Can certain manufacturing steps be automated?
Yes! Yes! Automation has existed since ancient times. The Egyptians discovered the wheel thousands and years ago. Today, robots assist in the assembly of lines.
In fact, there are several applications of robotics in manufacturing today. These include:
-
Line robots
-
Robot welding
-
Robot painting
-
Robotics inspection
-
Robots that produce products
Automation can be applied to manufacturing in many other ways. For example, 3D printing allows us to make custom products without having to wait for weeks or months to get them manufactured.
Why is logistics important for manufacturing?
Logistics is an integral part of every business. They are essential to any business's success.
Logistics play an important role in reducing costs as well as increasing efficiency.
What is the difference in Production Planning and Scheduling, you ask?
Production Planning (PP), is the process of deciding what production needs to take place at any given time. Forecasting demand is one way to do this.
Scheduling refers to the process of allocating specific dates to tasks in order that they can be completed within a specified timeframe.
Statistics
- It's estimated that 10.8% of the U.S. GDP in 2020 was contributed to manufacturing. (investopedia.com)
- Many factories witnessed a 30% increase in output due to the shift to electric motors. (en.wikipedia.org)
- According to a Statista study, U.S. businesses spent $1.63 trillion on logistics in 2019, moving goods from origin to end user through various supply chain network segments. (netsuite.com)
- You can multiply the result by 100 to get the total percent of monthly overhead. (investopedia.com)
- According to the United Nations Industrial Development Organization (UNIDO), China is the top manufacturer worldwide by 2019 output, producing 28.7% of the total global manufacturing output, followed by the United States, Japan, Germany, and India.[52][53] (en.wikipedia.org)
External Links
How To
How to Use 5S to Increase Productivity in Manufacturing
5S stands for "Sort", 'Set In Order", 'Standardize', & Separate>. Toyota Motor Corporation developed the 5S method in 1954. It allows companies to improve their work environment, thereby achieving greater efficiency.
The idea behind standardizing production processes is to make them repeatable and measurable. Cleaning, sorting and packing are all done daily. This knowledge allows workers to be more efficient in their work because they are aware of what to expect.
Implementing 5S requires five steps. These are Sort, Set In Order, Standardize. Separate. And Store. Each step requires a different action, which increases efficiency. Sorting things makes it easier to find them later. When items are ordered, they are put together. Then, after you separate your inventory into groups, you store those groups in containers that are easy to access. Finally, label all containers correctly.
Employees will need to be more critical about their work. Employees must be able to see why they do what they do and find a way to achieve them without having to rely on their old methods. They must learn new skills and techniques in order to implement the 5S system.
In addition to increasing efficiency, the 5S method also improves morale and teamwork among employees. They will feel motivated to strive for higher levels of efficiency once they start to see results.