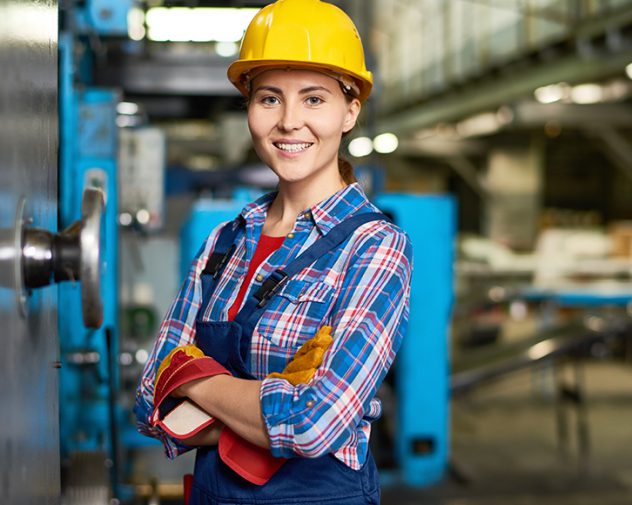
The director of manufacturing oversees the company's production process. Their role is crucial, as their role involves overseeing the whole process from design to manufacturing. To succeed in this role, the ideal candidate must have extensive experience in manufacturing and be familiar with new technologies. Some examples of such technologies include robotics and 3D printing. It is a benefit to a director who stays current with the latest technologies. As the manufacturing sector continues to develop, the director will find his or her role more complicated as he/she must coordinate with both engineering and operations. Quality control will also be a key focus.
Salary for a director in manufacturing
A Director of Manufacturing's salary can vary greatly, depending on the region they work in. Many directors are compensated in the low six-figure range, and some earn significantly more than others. The experience and education of a Director Manufacturing might also impact the salary. There are a few things that can influence the amount you earn in your region.
Although the salary of a Director of Manufacturing is variable, it is generally higher for those with more experience. Like many other positions, salary can be affected by the cost of living or where you live. While you may earn more if your location is a major city, it's possible to make a living in that area. When the opportunity presents itself, it is important to be open to negotiations to obtain a higher wage.
A Director of Manufacturing Operations can earn between $181 500 and $66,000 annually. The salary for a director of manufacturing operations is variable. It can vary up to 8% from one city to the next. Fremont's director manufacturing operations can expect to earn $128.493 to $164.500. This makes Fremont, CA a significantly better place than the national average. However, salaries for Director of Manufacturing Operations vary depending on location, experience, and company.
Education necessary
The director of manufacturing oversees the management and production of a facility. This role includes hiring new employees, overseeing quality inspection, collaborating with designers, meeting operations standards, and managing a production facility. A director of manufacturing usually reports to the top management team. He or she executes sales and policy initiatives. Candidates should have previous experience in manufacturing, and be able to communicate effectively. Different companies have different requirements for directors of manufacturing.
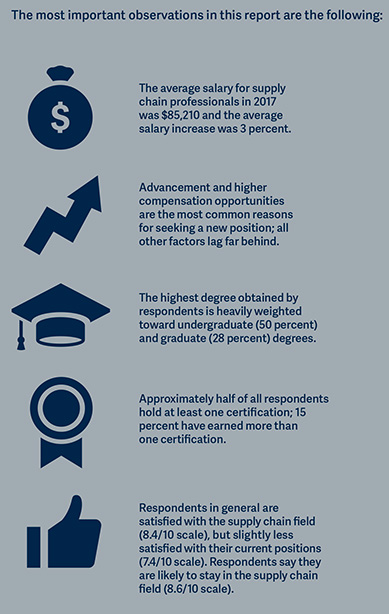
While a degree in engineering is not required for director-level manufacturing jobs, it will help you to build your knowledge and skills. An MBA program in industrial management or business administration is a great choice for this position, as it helps candidates to learn about management, economics, and organization. In the end, you will manage a diverse team of people.
You will be working closely with engineers and designers during product development. You will participate in the evaluation of new processes and setting quality standards before investing resources into larger productions. As well as overseeing production, directors can also serve as coaches to employees. They can mentor employees on risk mitigation and best practices. In addition to overseeing the entire production process, a manufacturing director must be able to develop strong problem-solving skills.
Experience required
This position often requires a bachelor's degree in a relevant area and five to ten years of progressive work experience. For this job, most manufacturing companies prefer to use their own employees. The ideal candidate will have a thorough understanding of the manufacturing process and business objectives. Some employers may prefer a graduate certificate. Employers may require candidates to complete additional training in their chosen fields or industries.
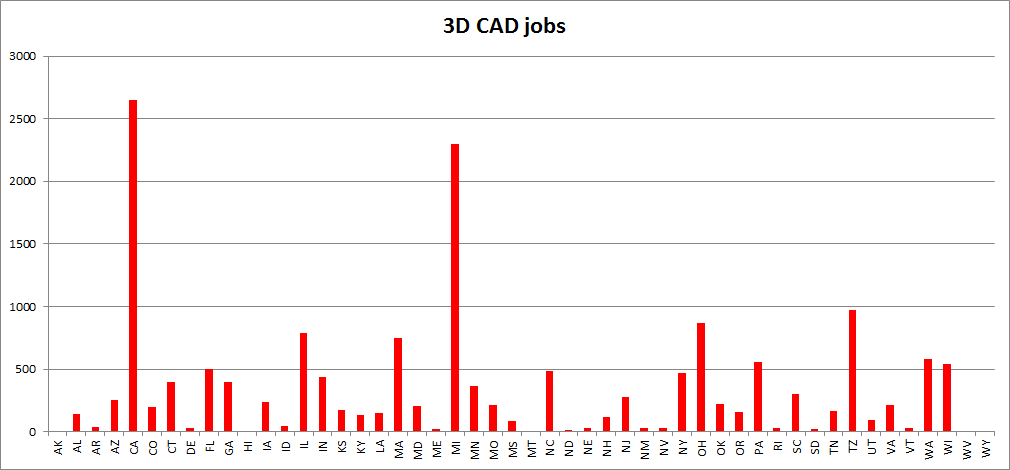
A director of manufacturing oversees the production process, including engineers, supervisors, and workers. They may be responsible in solving problems and creating solutions. They might also be responsible to develop and implement quality control programs. A director of manufacturing reports directly to the top executive of the manufacturing organization. Experience in manufacturing management is a must. Manufacturing management experience can make you a success in this role.
Experience as a manufacturing director is essential. Director must have at minimum 10 years experience in a manufacturing environment. Some of these people may have started as manufacturing supervisors or technicians. They should have excellent communication skills. The director of production should also have an in-depth understanding of the business strategy. A director of manufacturing must also be able and willing to collaborate with other departments. In this capacity, the director oversees the production process and ensures that it meets the highest quality standards.
FAQ
What is the importance of logistics in manufacturing?
Logistics is an integral part of every business. They are essential to any business's success.
Logistics plays a significant role in reducing cost and increasing efficiency.
What is the role of a manager in manufacturing?
A manufacturing manager must make sure that all manufacturing processes run smoothly and effectively. They should also be aware of any problems within the company and act accordingly.
They should also learn how to communicate effectively with other departments, including sales and marketing.
They must also keep up-to-date with the latest trends in their field and be able use this information to improve productivity and efficiency.
How important is automation in manufacturing?
Not only is automation important for manufacturers, but it's also vital for service providers. It allows them to offer services faster and more efficiently. It helps them to lower costs by reducing human errors, and improving productivity.
What is the responsibility of a production planner?
Production planners make sure that every aspect of the project is delivered on-time, within budget, and within schedule. A production planner ensures that the service and product meet the client's expectations.
Statistics
- In the United States, for example, manufacturing makes up 15% of the economic output. (twi-global.com)
- It's estimated that 10.8% of the U.S. GDP in 2020 was contributed to manufacturing. (investopedia.com)
- (2:04) MTO is a production technique wherein products are customized according to customer specifications, and production only starts after an order is received. (oracle.com)
- Many factories witnessed a 30% increase in output due to the shift to electric motors. (en.wikipedia.org)
- According to the United Nations Industrial Development Organization (UNIDO), China is the top manufacturer worldwide by 2019 output, producing 28.7% of the total global manufacturing output, followed by the United States, Japan, Germany, and India.[52][53] (en.wikipedia.org)
External Links
How To
Six Sigma: How to Use it in Manufacturing
Six Sigma is defined as "the application of statistical process control (SPC) techniques to achieve continuous improvement." Motorola's Quality Improvement Department developed it at their Tokyo plant in Japan in 1986. Six Sigma's basic concept is to improve quality and eliminate defects through standardization. This method has been adopted by many companies in recent years as they believe there are no perfect products or services. Six Sigma's primary goal is to reduce variation from the average value of production. It is possible to measure the performance of your product against an average and find the percentage of time that it differs from the norm. If there is a significant deviation from the norm, you will know that something needs to change.
Understanding how variability works in your company is the first step to Six Sigma. Once you understand that, it is time to identify the sources of variation. This will allow you to decide if these variations are random and systematic. Random variations occur when people do mistakes. Symmetrical variations are caused due to factors beyond the process. If you make widgets and some of them end up on the assembly line, then those are considered random variations. It would be considered a systematic problem if every widget that you build falls apart at the same location each time.
Once you've identified where the problems lie, you'll want to design solutions to eliminate those problems. The solution could involve changing how you do things, or redesigning your entire process. Test them again once you've implemented the changes. If they didn't work, then you'll need to go back to the drawing board and come up with another plan.