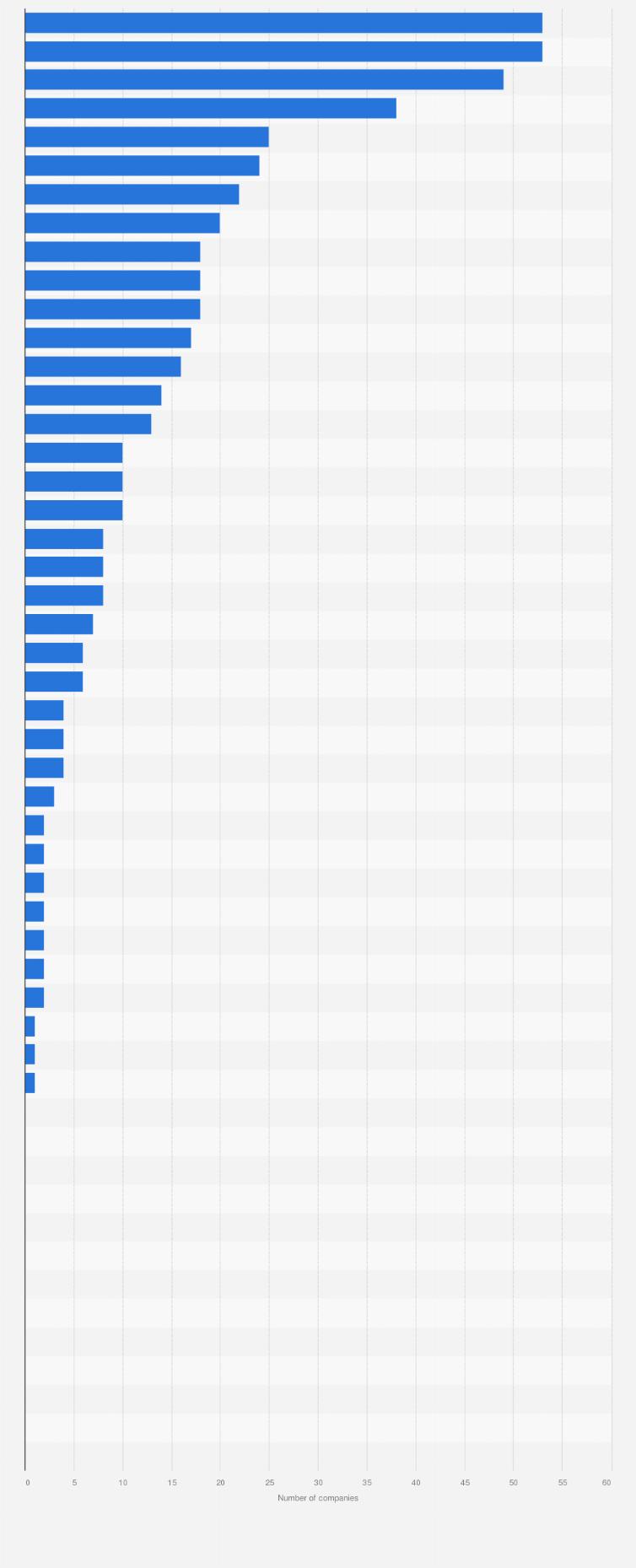
Businesses use just-in-time manufacturing to produce goods that meet their customers' needs. It relies on quality control and efficient workflows throughout manufacturing. This allows manufacturers to reduce inventory and use less space in the warehouse. These benefits are also beneficial for lower costs.
Although JIT has been proven to reduce overall costs for many companies, implementation can be complicated. JIT is not only dependent on operations coordination, but also the efficiency of the supply chains. This makes it susceptible to the disruptions that can occur on the global markets. Fortunately, there are several tools available to help manage the challenges of JIT.
When implemented properly, JIT can significantly reduce costs. It can also help improve the final product's quality. This technique can increase both machine and human efficiency. Additionally, it helps to increase the speed and smoothness of the production cycle. It reduces the time required to process non-essential output and will therefore have a positive impact on the environment.
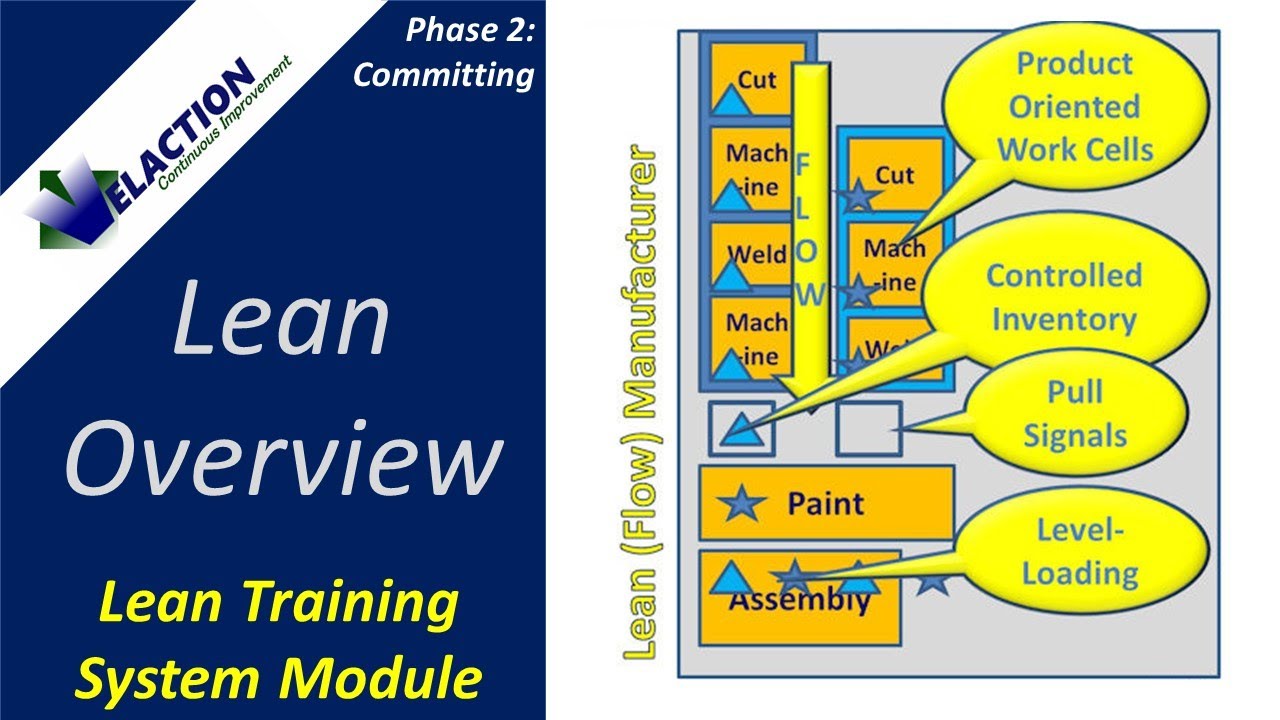
In Japan, just-in time production was first introduced during the rise of lean manufacturing. After World War II, Japanese companies were forced to rely heavily on limited resources. They needed to streamline manufacturing processes to survive. To maximize their output, they adopted JIT technologies.
Toyota's management team took the method and made it a success. They transformed their production from an inexplicable experiment to an exceptional case in just three years. These methods were so successful, other Japanese organizations started to notice them.
JIT is becoming a well-known technique in the Japanese market due to its effectiveness. However, it is important for manufacturers to fully understand the risks as well as the benefits associated with this system before they begin implementation. It is important to establish strong relationships with suppliers in order for a JIT implementation to be successful. Suppliers can help minimize stock-keeping requirements and increase the speed of deliveries.
There are two main types of JIT methods. Pull and push. Push is the traditional Make to Stock method of manufacturing. However, the push method puts pressure on other areas of the business. Moreover, the cost of retooling can be high. The pull method, in the same way, is based upon the actual demand for products.
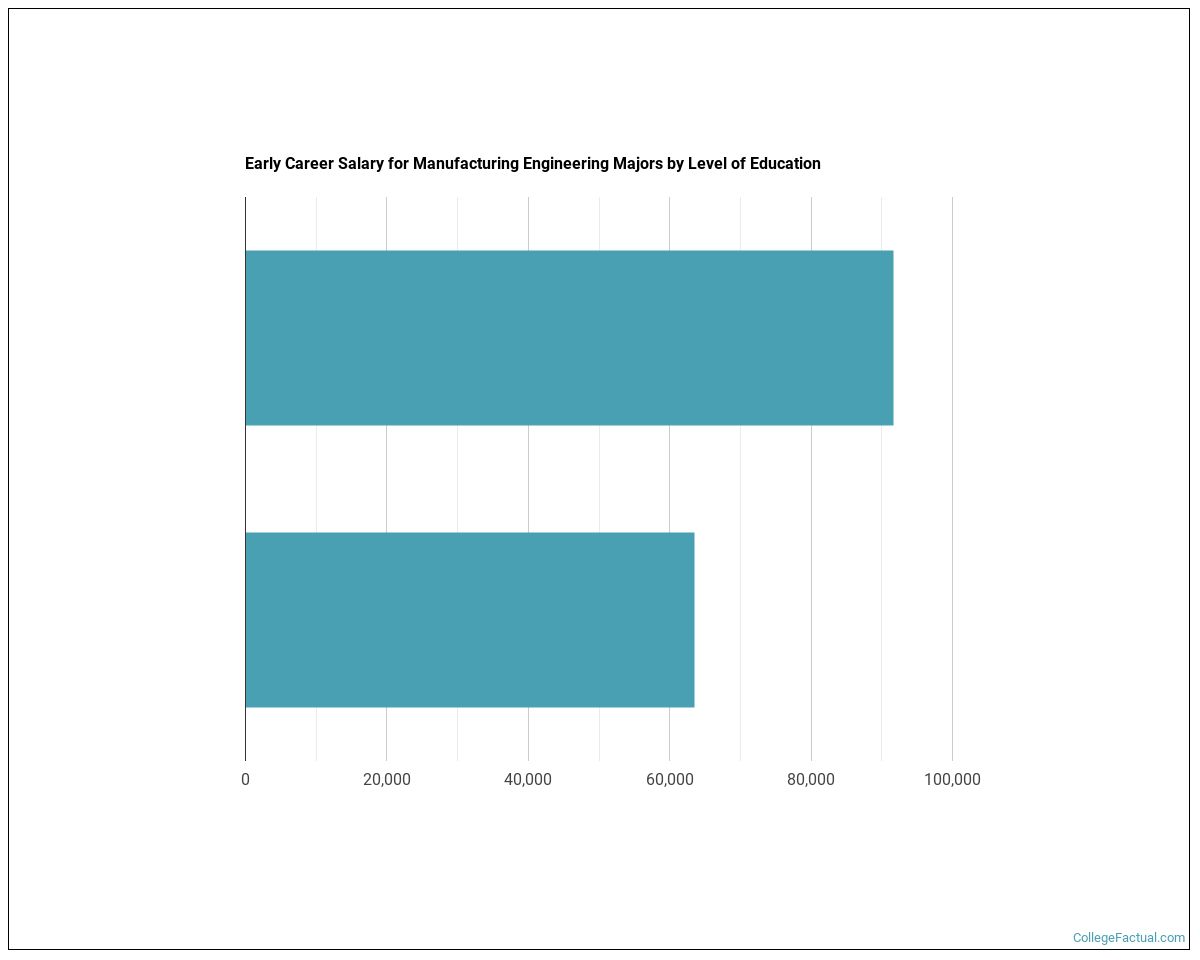
Many companies worldwide have successfully used these two methods. A successful implementation requires that all workers are empowered to resolve quality issues. JIT also has to be successful due to the complexity of manufacturing and the delay between manufacturer and supplier deliveries.
Ideally, a firm shouldn't have any stocks of raw materials or finished products. If it does, then it should have a small number of reusable containers called kanban.
JIT strives to reduce waste while also maximising the efficiency of both machine and human labor. It is important to identify and eliminate any potential quality problems before they begin to occur.
FAQ
What are the responsibilities of a logistic manager?
Logistics managers are responsible for ensuring that all goods arrive in perfect condition and on time. This is done using his/her knowledge of the company's products. He/she should also ensure enough stock is available to meet demand.
Why is logistics important in manufacturing?
Logistics are essential to any business. They help you achieve great results by helping you manage all aspects of product flow, from raw materials to finished goods.
Logistics plays a significant role in reducing cost and increasing efficiency.
What are the 4 types of manufacturing?
Manufacturing refers the process of turning raw materials into useful products with machines and processes. Manufacturing can include many activities such as designing and building, testing, packaging shipping, selling, servicing, and other related activities.
Why should you automate your warehouse?
Modern warehouses are increasingly dependent on automation. E-commerce has increased the demand for quicker delivery times and more efficient processes.
Warehouses must be able to quickly adapt to changing demands. Technology investment is necessary to enable warehouses to respond quickly to changing demands. The benefits of automating warehouses are numerous. Here are some benefits of investing in automation
-
Increases throughput/productivity
-
Reduces errors
-
Improves accuracy
-
Safety enhancements
-
Eliminates bottlenecks
-
Allows companies to scale more easily
-
This makes workers more productive
-
This gives you visibility into what happens in the warehouse
-
Enhances customer experience
-
Improves employee satisfaction
-
Reducing downtime and increasing uptime
-
You can be sure that high-quality products will arrive on time
-
Human error can be eliminated
-
It helps ensure compliance with regulations
What are the goods of logistics?
Logistics refers to the movement of goods from one place to another.
They encompass all aspects transport, including packaging and loading, transporting, storage, unloading.
Logisticians make sure that the right product arrives at the right place at the correct time and in safe conditions. Logisticians help companies improve their supply chain efficiency by providing information about demand forecasts and stock levels, production schedules, as well as availability of raw materials.
They can also track shipments in transit and monitor quality standards.
Do we need to know about Manufacturing Processes before learning about Logistics?
No. No. Understanding the manufacturing process will allow you to better understand logistics.
Statistics
- In the United States, for example, manufacturing makes up 15% of the economic output. (twi-global.com)
- Job #1 is delivering the ordered product according to specifications: color, size, brand, and quantity. (netsuite.com)
- In 2021, an estimated 12.1 million Americans work in the manufacturing sector.6 (investopedia.com)
- It's estimated that 10.8% of the U.S. GDP in 2020 was contributed to manufacturing. (investopedia.com)
- Many factories witnessed a 30% increase in output due to the shift to electric motors. (en.wikipedia.org)
External Links
How To
How to use Lean Manufacturing in the production of goods
Lean manufacturing is a management system that aims at increasing efficiency and reducing waste. It was developed by Taiichi Okono in Japan, during the 1970s & 1980s. TPS founder Kanji Takoda awarded him the Toyota Production System Award (TPS). Michael L. Watkins published the original book on lean manufacturing, "The Machine That Changed the World," in 1990.
Lean manufacturing refers to a set of principles that improve the quality, speed and costs of products and services. It emphasizes the elimination and minimization of waste in the value stream. Lean manufacturing can be described as just-in–time (JIT), total productive maintenance, zero defect (TPM), or even 5S. Lean manufacturing eliminates non-value-added tasks like inspection, rework, waiting.
In addition to improving product quality and reducing costs, lean manufacturing helps companies achieve their goals faster and reduces employee turnover. Lean manufacturing can be used to manage all aspects of the value chain. Customers, suppliers, distributors, retailers and employees are all included. Lean manufacturing is widely practiced in many industries around the world. Toyota's philosophy is a great example of this. It has helped to create success in automobiles as well electronics, appliances and healthcare.
Five principles are the basis of lean manufacturing:
-
Define value - Find out what your business contributes to society, and what makes it different from other competitors.
-
Reduce Waste - Eliminate any activity that doesn't add value along the supply chain.
-
Create Flow: Ensure that the work process flows without interruptions.
-
Standardize and simplify - Make your processes as consistent as possible.
-
Building Relationships – Establish personal relationships with both external and internal stakeholders.
Lean manufacturing, although not new, has seen renewed interest in the economic sector since 2008. Many businesses have adopted lean production techniques to make them more competitive. Some economists even believe that lean manufacturing can be a key factor in economic recovery.
Lean manufacturing, which has many benefits, is now a standard practice in the automotive industry. These include better customer satisfaction and lower inventory levels. They also result in lower operating costs.
Any aspect of an enterprise can benefit from Lean manufacturing. It is especially useful for the production aspect of an organization, as it ensures that every step in the value chain is efficient and effective.
There are three types principally of lean manufacturing:
-
Just-in Time Manufacturing: This lean manufacturing method is commonly called "pull systems." JIT is a method in which components are assembled right at the moment of use, rather than being manufactured ahead of time. This approach reduces lead time, increases availability and reduces inventory.
-
Zero Defects Manufacturing (ZDM): ZDM focuses on ensuring that no defective units leave the manufacturing facility. If a part is required to be repaired on the assembly line, it should not be scrapped. This is also true for finished products that require minor repairs before shipping.
-
Continuous Improvement (CI): CI aims to improve the efficiency of operations by continuously identifying problems and making changes in order to eliminate or minimize waste. It involves continuous improvement of processes, people, and tools.