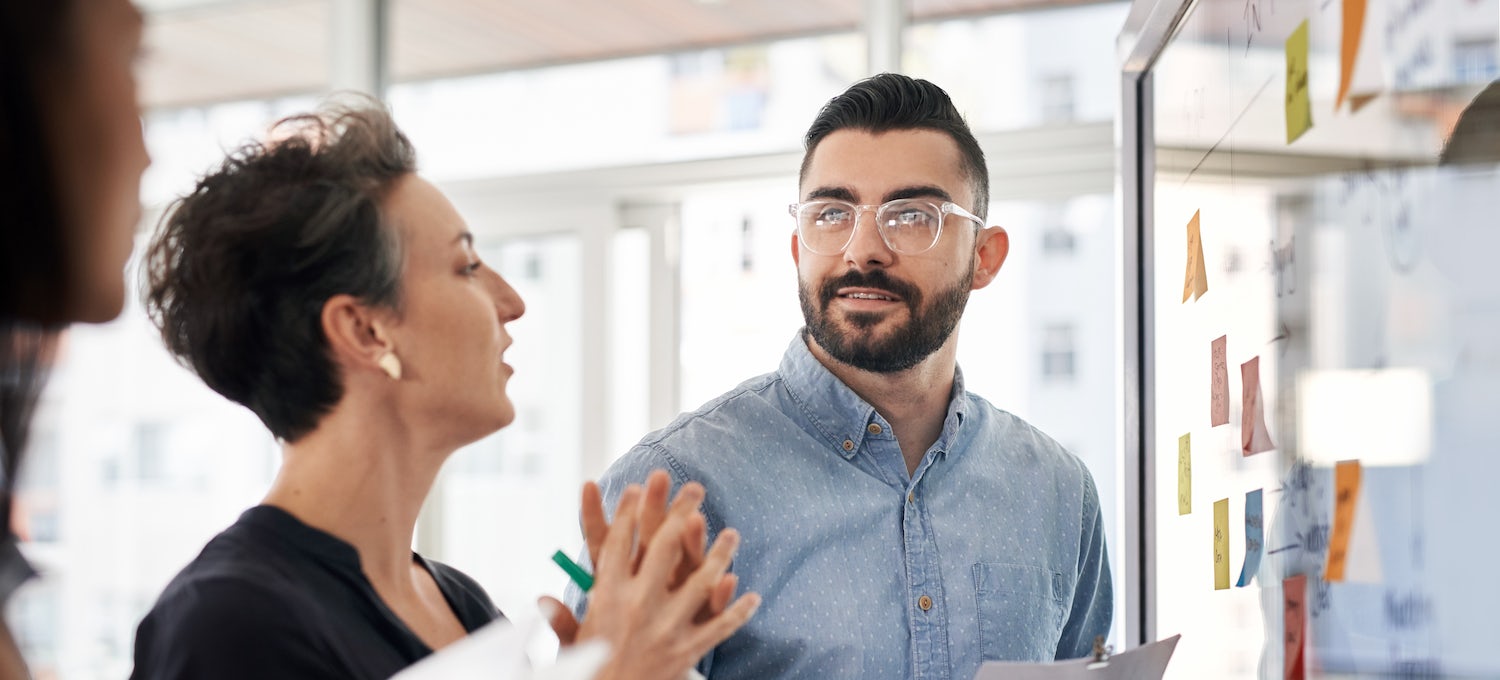
An educational degree in architecture or engineering is usually required to work as an architectural and engineering manager. While most of these professionals work from offices, some are also employed on construction sites. A majority of these professionals hold a bachelor's in architecture or engineering and have extensive work experience in the field. Many choose to complete a second graduate degree in business management to supplement their education. There are many paths to advancement in this profession. A MBA can help you to pursue a career in engineering management and architecture.
The Occupational Outlook for Architectural and Engineering Managers
Employment prospects for engineers and architects managers are good. In the next decade, there will be an increase in job opportunities by around two percent. This increase will reflect the growth of various industries. Nevertheless, competition for available jobs will be stiff. See the O*NET website for more information on the job outlook.
Engineering and architectural managers are responsible for planning and directing activities in engineering and architectural companies. Using their knowledge of architecture, they are responsible for the planning, design, construction, and management of a wide range of activities. This could include large-scale building design, construction and maintenance, as well as engineering research or site management. They also design new products. They have to establish the technical goals and make detailed plans to support them.
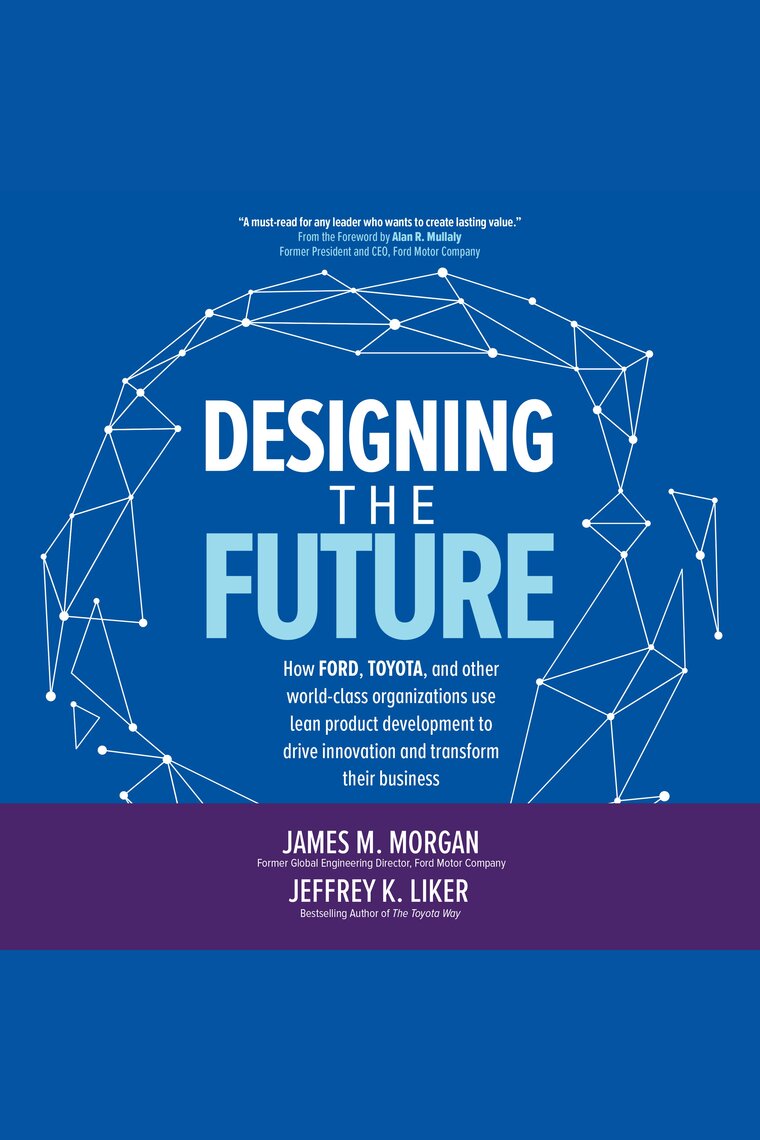
This field typically requires applicants to hold a minimum of a master's degree. It all depends on your choice of type of management role. For example, an engineering master's degree can prepare you for technical management positions, while a master's degree in business administration can help you gain broader management skills. Both types require at least one academic year to complete.
Education Required
Engineer and architectural managers need to have a solid education. These managers are responsible to oversee the day-to-day operations and management of engineering teams. They provide supervision and training for staff. They can also help mentor employees and propose budgets. You might also consider a bachelor’s degree in this field if this is something you want to do.
Many of these managers hold a bachelor's in architecture or engineering, but many also have advanced degrees in technology management or business administration. A master's degree in engineering management, or technology management, also known as MsEM will provide you with the necessary managerial skills. Not only will you need technical knowledge but also strong communication skills and analytical abilities.
Architects and engineering managers are responsible for implementing new projects while ensuring that the quality of the end product is high. They consider the environmental impact and the user's needs. These professionals develop detailed plans and budgets that are based upon technical specifications. They supervise teams of engineers to successfully execute projects.
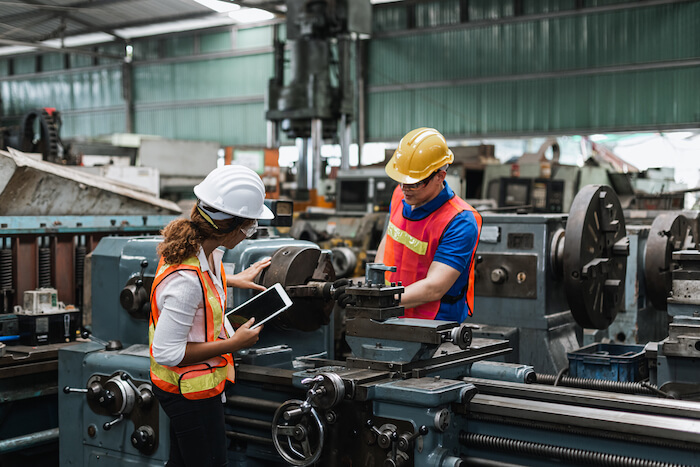
Earning potential
Over the next ten years, the earning potential to be an architect or engineer manager is expected increase by 13%. This field will see an increase in jobs as a result of the growing engineering industry. Despite the expected increase in the number of jobs within this industry, the competition will still be intense. The industry growth rate will not be the same as for all occupations.
The salary range for this profession depends on experience, education and geographic location. For an entry-level position, the salary is $75,190. A candidate with between four and five years of work experience will earn at least $104,800. For those with a minimum of ten years experience, they can make approximately $156,620 annually.
FAQ
What skills is required for a production planner?
A production planner must be organized, flexible, and able multitask to succeed. You must also be able to communicate effectively with clients and colleagues.
What does the term manufacturing industries mean?
Manufacturing Industries are businesses that produce products for sale. These products are sold to consumers. To accomplish this goal, these companies employ a range of processes including distribution, sales, management, and production. These companies produce goods using raw materials and other equipment. This includes all types and varieties of manufactured goods, such as food items, clothings, building supplies, furnitures, toys, electronics tools, machinery vehicles, pharmaceuticals medical devices, chemicals, among others.
What makes a production planner different from a project manger?
A production planner is more involved in the planning phase of the project than a project manger.
Can some manufacturing processes be automated?
Yes! Yes. Automation has been around since ancient time. The wheel was invented by the Egyptians thousands of years ago. To help us build assembly lines, we now have robots.
Robotics is used in many manufacturing processes today. These include:
-
Assembly line robots
-
Robot welding
-
Robot painting
-
Robotics inspection
-
Robots that make products
Automation can be applied to manufacturing in many other ways. 3D printing is a way to make custom products quickly and without waiting weeks or months for them to be manufactured.
Statistics
- In 2021, an estimated 12.1 million Americans work in the manufacturing sector.6 (investopedia.com)
- [54][55] These are the top 50 countries by the total value of manufacturing output in US dollars for its noted year according to World Bank.[56] (en.wikipedia.org)
- According to a Statista study, U.S. businesses spent $1.63 trillion on logistics in 2019, moving goods from origin to end user through various supply chain network segments. (netsuite.com)
- You can multiply the result by 100 to get the total percent of monthly overhead. (investopedia.com)
- In the United States, for example, manufacturing makes up 15% of the economic output. (twi-global.com)
External Links
How To
How to use 5S to increase Productivity in Manufacturing
5S stands to stand for "Sort", “Set In Order", “Standardize", and "Store". Toyota Motor Corporation created the 5S methodology in 1954. It assists companies in improving their work environments and achieving higher efficiency.
The idea behind standardizing production processes is to make them repeatable and measurable. This means that every day tasks such cleaning, sorting/storing, packing, and labeling can be performed. These actions allow workers to perform their job more efficiently, knowing what to expect.
Implementing 5S involves five steps: Sort, Set in Order, Standardize Separate, Store, and Each step is a different action that leads to greater efficiency. For example, when you sort things, you make them easy to find later. When you arrange items, you place them together. You then organize your inventory in groups. Make sure everything is correctly labeled when you label your containers.
Employees must be able to critically examine their work practices. Employees need to be able understand their motivations and discover alternative ways to do them. They will need to develop new skills and techniques in order for the 5S system to be implemented.
The 5S method increases efficiency and morale among employees. They will feel motivated to strive for higher levels of efficiency once they start to see results.