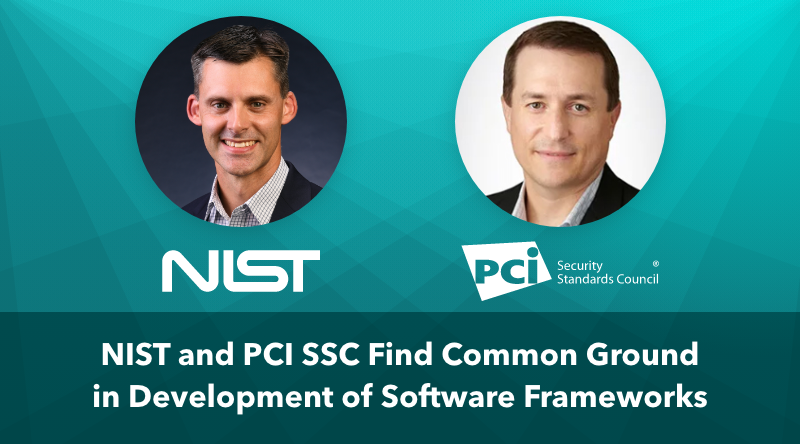
Lean manufacturing, a management method that helps to reduce waste and increase efficiency, is what it stands for. It's based on the principles of Henry Ford and KiichiroToyoda who were the presidents of Toyota Motor Corporation before World War II. Manufacturing is not simply an assembly line. Lean manufacturing refers to it as a whole process. Lean is based on five principles: reduce waste; streamline the process; create knowledge; optimize the whole; and use continuous improvement.
It is important to first identify what you are doing wrong. This can either be done quantitatively or qualitatively. Consider the price your customers pay to purchase your product. If you find that the price is higher than the value you are delivering, you have a problem.
A kaizen event is a way to measure the amount of waste generated by a process. The kaizen event involves everyone working together to solve incremental problems. Kaizen events can be used alone or in conjunction with other lean tools.
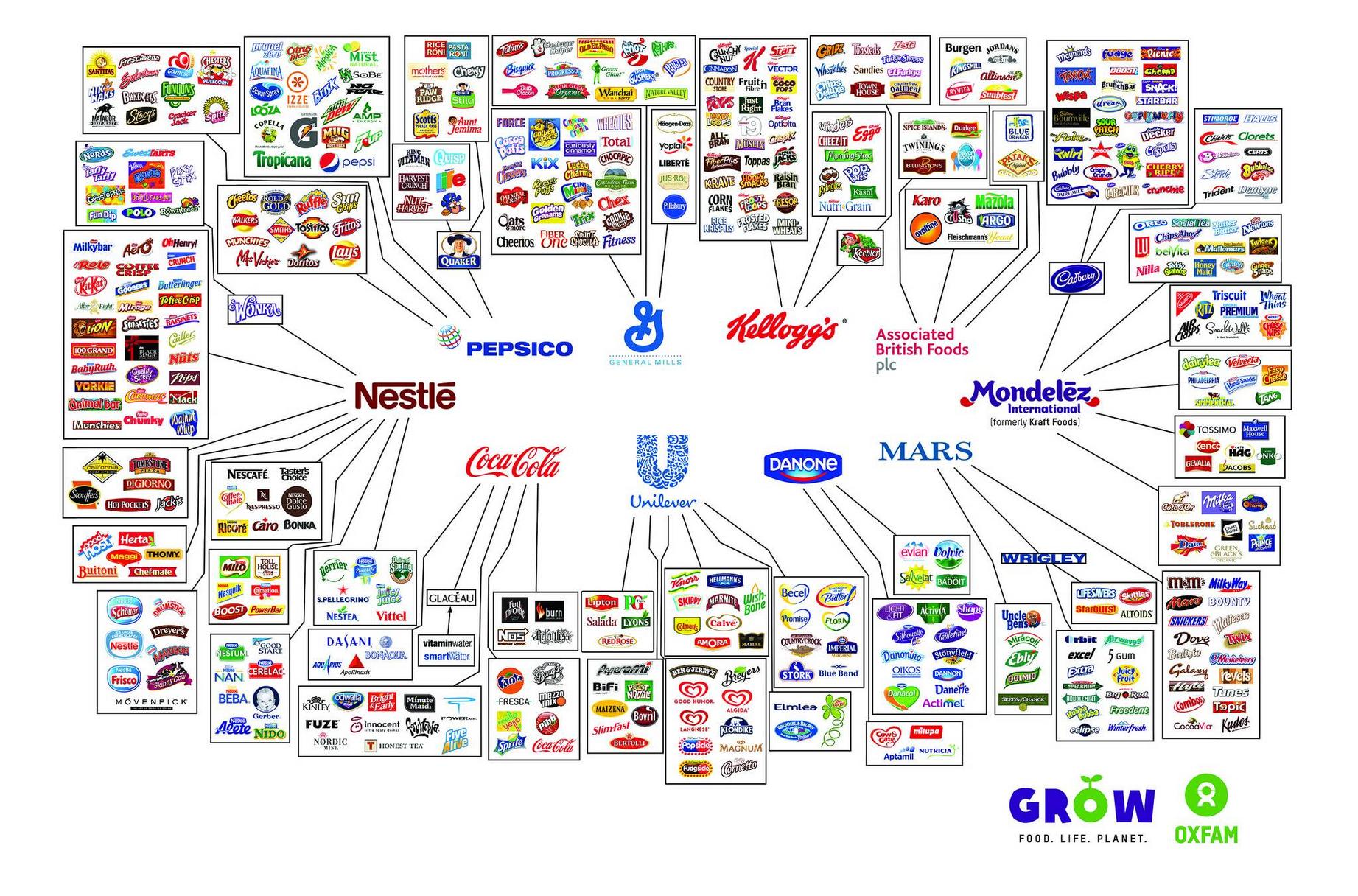
Value stream mapping is another way to identify production waste. VSM is a way for manufacturers to see the production steps and determine which are the most time-consuming.
Inventory, waiting and overproduction are all waste areas. These areas can be identified and improved by a lean team. They could be part of the supply chain or in a production zone, or all throughout the process.
Once you've identified the waste, it is time to begin implementing strategies that will eliminate it. These include developing cross-functional teams, flattening your workload, and training your employees to be multi-skilled. You may also want to use technologies such as just-in time or cellular manufacturing depending on your business. You can also utilize other lean tools such total productive maintenance or kanban administration.
Also, you can incorporate standardized containers into your system that allows workers to count and know exact quantities. It is easier to determine if food, or other substances are mixed into the products using standardized containers. You can install safety mats near machine areas, which will cause a stoppage of the product if a person walks on them.
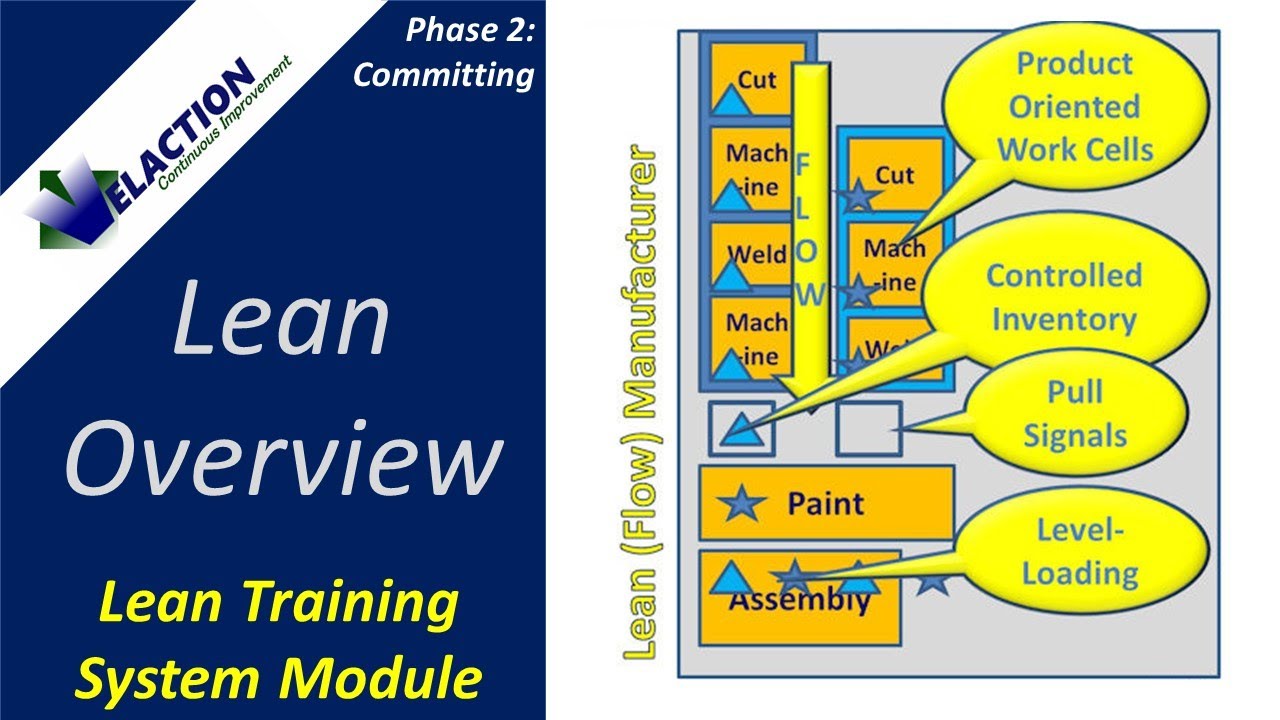
As with all lean initiatives, you will need a strong organizational culture in place. The culture should include communication skills, understanding the goal, and a longterm focus. To ensure your company's success, you must create a sustainable system for improvement.
A value stream map can be useful when you are looking for a machine. A value stream map can help you create an inventory of the products, raw materials, and customers that will be needed in the future. You can use this information to better predict when you'll need equipment and supplies. Similarly, you can create a scheduling system to ensure you can fulfill orders on time.
You can increase your company's efficiency and help you reach your goals by incorporating five key principles of lean production. There are many lean manufacturing websites that can help you learn more about the available techniques and resources.
FAQ
What is the role of a logistics manager
Logistics managers ensure that goods arrive on time and are unharmed. This is done by using his/her experience and knowledge of the company's products. He/she should ensure that sufficient stock is available in order to meet customer demand.
Can we automate some parts of manufacturing?
Yes! Yes! Automation has existed since ancient times. The Egyptians created the wheel thousands years ago. Today, robots assist in the assembly of lines.
Robotics is used in many manufacturing processes today. These include:
-
Automated assembly line robots
-
Robot welding
-
Robot painting
-
Robotics inspection
-
Robots create products
Manufacturing can also be automated in many other ways. For example, 3D printing allows us to make custom products without having to wait for weeks or months to get them manufactured.
What does manufacturing industry mean?
Manufacturing Industries are companies that manufacture products. The people who buy these products are called consumers. To accomplish this goal, these companies employ a range of processes including distribution, sales, management, and production. They manufacture goods from raw materials using machines and other equipment. This includes all types of manufactured goods, including food items, clothing, building supplies, furniture, toys, electronics, tools, machinery, vehicles, pharmaceuticals, medical devices, chemicals, and many others.
What does "warehouse" mean?
A warehouse or storage facility is where goods are stored before they are sold. It can be an indoor space or an outdoor area. It could be one or both.
What are the responsibilities of a production planner
Production planners ensure that all project aspects are completed on time, within budget and within the scope. They make sure that the product and services meet client expectations.
Why automate your warehouse
Modern warehousing has seen automation take center stage. Increased demand for efficient and faster delivery has resulted in a rise in e-commerce.
Warehouses need to adapt quickly to meet changing needs. They must invest heavily in technology to do this. Automation of warehouses offers many benefits. Here are some reasons why it's worth investing in automation:
-
Increases throughput/productivity
-
Reduces errors
-
Accuracy is improved
-
Safety Boosts
-
Eliminates bottlenecks
-
Companies can scale more easily
-
Makes workers more efficient
-
This gives you visibility into what happens in the warehouse
-
Enhances customer experience
-
Improves employee satisfaction
-
It reduces downtime, and increases uptime
-
High quality products delivered on-time
-
Human error can be eliminated
-
This helps to ensure compliance with regulations
What are manufacturing and logistic?
Manufacturing refers the process of producing goods from raw materials through machines and processes. Logistics is the management of all aspects of supply chain activities, including procurement, production planning, distribution, warehousing, inventory control, transportation, and customer service. Logistics and manufacturing are often referred to as one thing. It encompasses both the creation of products and their delivery to customers.
Statistics
- According to the United Nations Industrial Development Organization (UNIDO), China is the top manufacturer worldwide by 2019 output, producing 28.7% of the total global manufacturing output, followed by the United States, Japan, Germany, and India.[52][53] (en.wikipedia.org)
- (2:04) MTO is a production technique wherein products are customized according to customer specifications, and production only starts after an order is received. (oracle.com)
- [54][55] These are the top 50 countries by the total value of manufacturing output in US dollars for its noted year according to World Bank.[56] (en.wikipedia.org)
- Job #1 is delivering the ordered product according to specifications: color, size, brand, and quantity. (netsuite.com)
- In the United States, for example, manufacturing makes up 15% of the economic output. (twi-global.com)
External Links
How To
How to Use Lean Manufacturing for the Production of Goods
Lean manufacturing is a management system that aims at increasing efficiency and reducing waste. It was first developed in Japan in the 1970s/80s by Taiichi Ahno, who was awarded the Toyota Production System (TPS), award from KanjiToyoda, the founder of TPS. The first book published on lean manufacturing was titled "The Machine That Changed the World" written by Michael L. Watkins and published in 1990.
Lean manufacturing can be described as a set or principles that are used to improve quality, speed and cost of products or services. It emphasizes the elimination of defects and waste throughout the value stream. Lean manufacturing is called just-in-time (JIT), zero defect, total productive maintenance (TPM), or 5S. Lean manufacturing is about eliminating activities that do not add value, such as inspection, rework, and waiting.
Lean manufacturing is a way for companies to achieve their goals faster, improve product quality, and lower costs. Lean Manufacturing is one of the most efficient ways to manage the entire value chains, including suppliers and customers as well distributors and retailers. Lean manufacturing can be found in many industries. For example, Toyota's philosophy underpins its success in automobiles, electronics, appliances, healthcare, chemical engineering, aerospace, paper, food, etc.
Five basic principles of Lean Manufacturing are included in lean manufacturing
-
Define Value- Identify the added value your company brings to society. What makes you stand out from your competitors?
-
Reduce Waste - Eliminate any activity that doesn't add value along the supply chain.
-
Create Flow: Ensure that the work process flows without interruptions.
-
Standardize and simplify – Make processes as repeatable and consistent as possible.
-
Build relationships - Develop and maintain personal relationships with both your internal and external stakeholders.
Although lean manufacturing isn't a new concept in business, it has gained popularity due to renewed interest in the economy after the 2008 global financial crisis. Many companies have adopted lean manufacturing methods to increase their marketability. Some economists even believe that lean manufacturing can be a key factor in economic recovery.
Lean manufacturing is becoming a popular practice in automotive. It has many advantages. These benefits include increased customer satisfaction, reduced inventory levels and lower operating costs.
Lean manufacturing can be applied to almost every aspect of an organization. Lean manufacturing is most useful in the production sector of an organisation because it ensures that each step in the value-chain is efficient and productive.
There are three main types in lean manufacturing
-
Just-in Time Manufacturing (JIT), also known as "pull system": This form of lean manufacturing is often referred to simply as "pull". JIT is a method in which components are assembled right at the moment of use, rather than being manufactured ahead of time. This method reduces lead times, increases availability, and decreases inventory.
-
Zero Defects Manufacturing (ZDM),: ZDM is a system that ensures no defective units are left the manufacturing facility. It is better to repair a part than have it removed from the production line if it needs to be fixed. This also applies to finished products that need minor repairs before being shipped.
-
Continuous Improvement (CI),: Continuous improvement aims improve the efficiency and effectiveness of operations by continuously identifying issues and making changes to reduce waste. Continuous improvement refers to continuous improvement of processes as well people and tools.