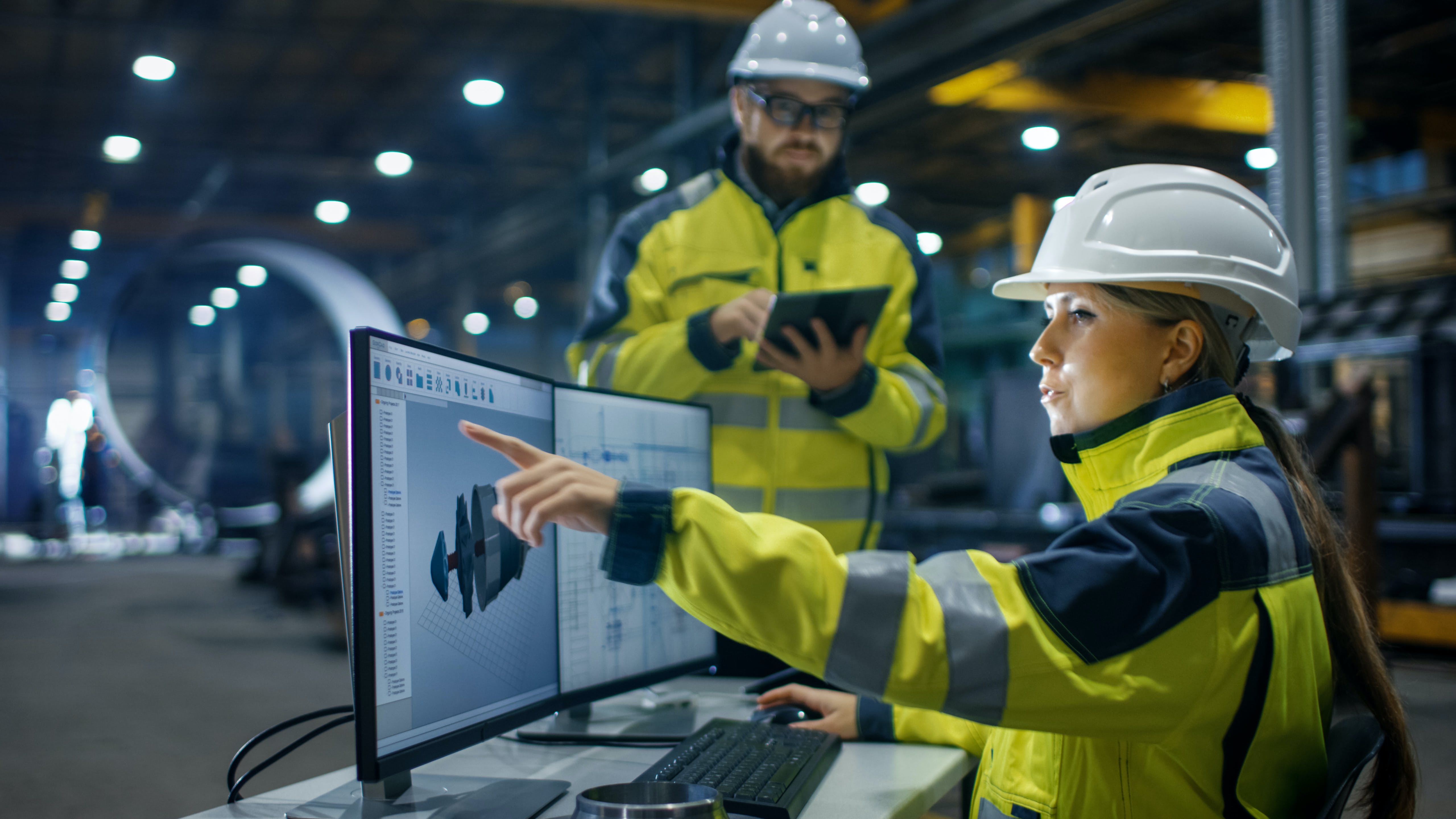
The duties of a technician in mechanical engineering will vary depending on their employer. They will test equipment, review blueprints and write purchase orders. They could also be exposed to potentially dangerous materials. These risks can be minimized if you follow the correct procedures.
Although they are usually supervised by an engineer, a mechanical engineering technician can perform their duties on their own. They are responsible for the maintenance and repair of machinery and equipment. They are responsible for ensuring safety and compliance with company policies. Customers' requirements must also be met.
A good mechanical engineering technician will be able to solve mechanical problems and make accurate calculations. They can also collaborate with engineers to improve manufacturing processes. They may also help design new equipment and test new materials.
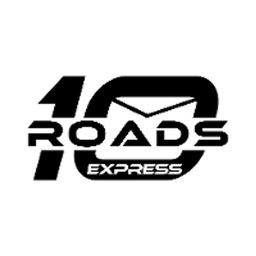
A mechanical engineering technician should have a good understanding of principles and practices in mechanical engineering to be able to do the best job. They will need to be proficient in using CAD software, which allows them to design and analyze machines. They will need to be able manage mechanical service records. In addition, they will need to be able show excellent time management skills.
Mechanical engineers technicians are most commonly responsible for testing equipment and making estimations. A mechanical engineering technician may also be involved in research to improve manufacturing processes. These findings are typically recorded and evaluated making them an important part a technician in mechanical engineering.
Another job of a mechanical engineer technician is to prepare drawings for components, interpret instructions, write work orders and interpret instructions. The mechanical engineer can test electrical equipment, materials and systems to determine their performance. They might also assist with the design of machinery and power plants. They may also perform statistical studies to analyze the costs of production.
You will need to have solid knowledge about mechanical engineering principles and critical thinking skills. Knowledge of new technology is also a requirement. Engineers will require you to draw and test mechanical systems under different operating conditions.
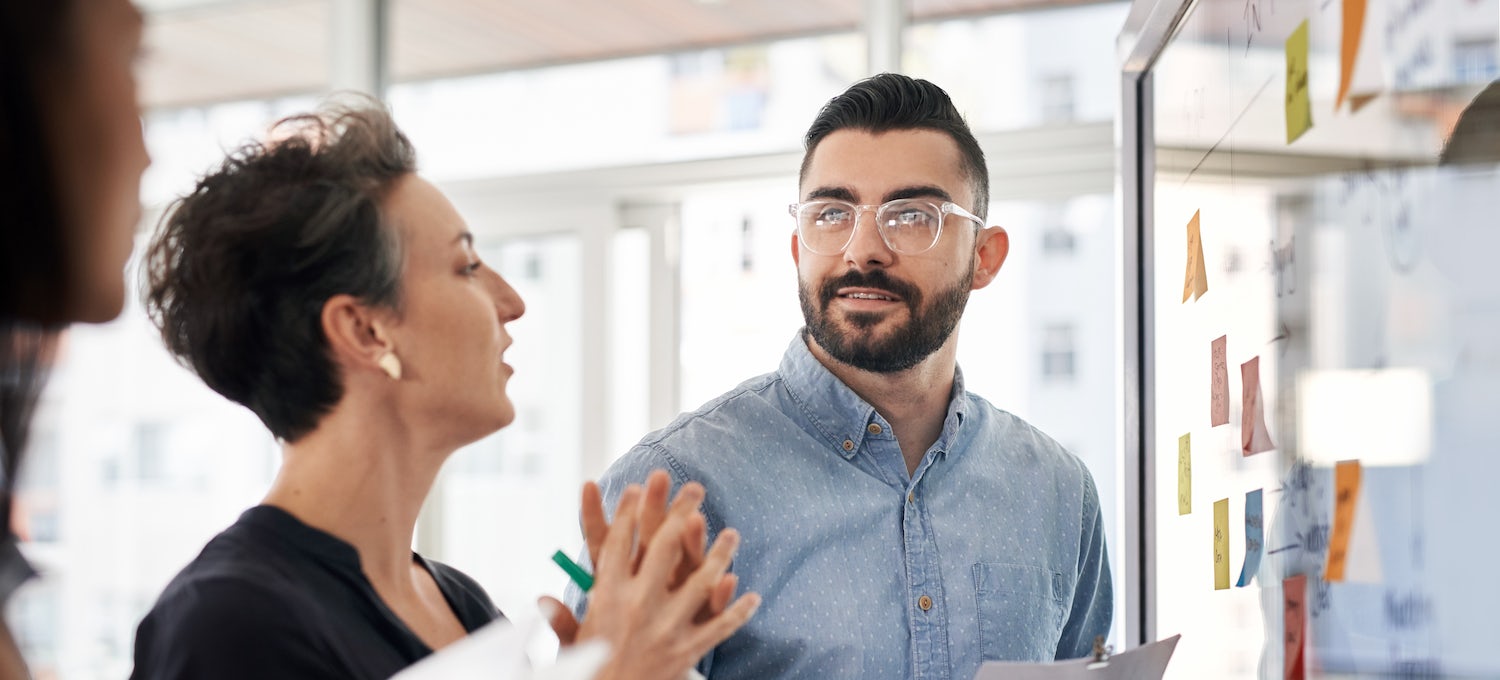
Quality control analysis is another important part of the job of a mechanical engineer technician. Engineers perform quality control analysis by comparing tool drawings to the original specifications. Engineers may make design improvements or suggestions and then record the results. They may submit the results to engineers.
Although they may be required to work alone, a mechanical engineering technician will often work in a regular schedule. They may also be required to work overtime. They might work in a laboratory, research facility, or manufacturing factory. They could work many hours and be exposed potentially hazardous materials.
An engineer in mechanical design may also be required to handle hydraulics and other power system issues. They will be expected to use power tools as well as rigging equipment daily and satisfy the needs of customers.
FAQ
What makes a production planner different from a project manger?
The difference between a product planner and project manager is that a planer is typically the one who organizes and plans the entire project. A production planner, however, is mostly involved in the planning stages.
Why is logistics important for manufacturing?
Logistics is an integral part of every business. They help you achieve great results by helping you manage all aspects of product flow, from raw materials to finished goods.
Logistics plays a significant role in reducing cost and increasing efficiency.
Is there anything we should know about Manufacturing Processes prior to learning about Logistics.
No. No. But, being familiar with manufacturing processes will give you a better understanding about how logistics works.
What is production planning?
Production Planning is the creation of a plan to cover all aspects, such as scheduling, budgeting. Location, crew, equipment, props and other details. This document is designed to make sure everything is ready for when you're ready to shoot. You should also have information to ensure the best possible results on set. This information includes locations, crew details and equipment requirements.
It is important to first outline the type of film you would like to make. You may have already decided where you would like to shoot, or maybe there are specific locations or sets that you want to use. Once you've identified the locations and scenes you want to use, you can begin to plan what elements you need for each scene. One example is if you are unsure of the exact model you want but decide that you require a car. If this is the case, you might start searching online for car models and then narrow your options by selecting from different makes.
After you have chosen the right car, you will be able to begin thinking about accessories. Do you need people sitting in the front seats? Perhaps you have someone who needs to be able to walk around the back of your car. You may want to change the interior's color from black or white. These questions will help determine the look and feel you want for your car. You can also think about the type of shots you want to get. Are you going to be shooting close-ups? Or wide angles? Perhaps you want to show the engine or the steering wheel? These things will help you to identify the car that you are looking for.
Once you have determined all of the above, you can move on to creating a schedule. You will know when you should start and when you should finish shooting. You will need to know when you have to be there, what time you have to leave and when your return home. So everyone is clear about what they need to do. You can also make sure to book extra staff in advance if you have to hire them. You don't want to hire someone who won't show up because he didn't know.
Also, consider how many days you will be filming your schedule. Some projects can be completed in a matter of days or weeks. Others may take several days. While creating your schedule, it is important to remember whether you will require more than one shot per day. Multiple shots at the same location can increase costs and make it more difficult to complete. If you are unsure if you need multiple takes, it is better to err on the side of caution and shoot fewer takes rather than risk wasting money.
Budgeting is another important aspect of production planning. A realistic budget will help you work within your means. Keep in mind that you can always reduce your budget if you face unexpected difficulties. It is important to not overestimate how much you will spend. If you underestimate the cost of something, you will have less money left after paying for other items.
Production planning is a very detailed process, but once you understand how everything works together, it becomes easier to plan future projects.
Statistics
- Many factories witnessed a 30% increase in output due to the shift to electric motors. (en.wikipedia.org)
- (2:04) MTO is a production technique wherein products are customized according to customer specifications, and production only starts after an order is received. (oracle.com)
- In 2021, an estimated 12.1 million Americans work in the manufacturing sector.6 (investopedia.com)
- You can multiply the result by 100 to get the total percent of monthly overhead. (investopedia.com)
- Job #1 is delivering the ordered product according to specifications: color, size, brand, and quantity. (netsuite.com)
External Links
How To
How to use the Just-In Time Method in Production
Just-in time (JIT), is a process that reduces costs and increases efficiency in business operations. It's the process of obtaining the right amount and timing of resources when you need them. This means that only what you use is charged to your account. Frederick Taylor, a 1900s foreman, first coined the term. He saw how overtime was paid to workers for work that was delayed. He decided that workers would be more productive if they had enough time to complete their work before they started to work.
JIT is an acronym that means you need to plan ahead so you don’t waste your money. You should also look at the entire project from start to finish and make sure that you have sufficient resources available to deal with any problems that arise during the course of your project. You'll be prepared to handle any potential problems if you know in advance. This way, you won't end up paying extra money for things that weren't really necessary.
There are many JIT methods.
-
Demand-driven: This JIT is where you place regular orders for the parts/materials that are needed for your project. This will let you track the amount of material left over after you've used it. This will allow to you estimate the time it will take for more to be produced.
-
Inventory-based: This is a type where you stock the materials required for your projects in advance. This allows for you to anticipate how much you can sell.
-
Project-driven: This is an approach where you set aside enough funds to cover the cost of your project. You will be able to purchase the right amount of materials if you know what you need.
-
Resource-based JIT: This is the most popular form of JIT. Here you can allocate certain resources based purely on demand. For instance, if you have a lot of orders coming in, you'll assign more people to handle them. You'll have fewer orders if you have fewer.
-
Cost-based: This is the same as resource-based except that you don't care how many people there are but how much each one of them costs.
-
Price-based pricing: This is similar in concept to cost-based but instead you look at how much each worker costs, it looks at the overall company's price.
-
Material-based: This is very similar to cost-based but instead of looking at total costs of the company you are concerned with how many raw materials you use on an average.
-
Time-based: This is another variation of resource-based JIT. Instead of focusing solely on the amount each employee costs, focus on how long it takes for the project to be completed.
-
Quality-based JIT is another variant of resource-based JIT. Instead of worrying about the costs of each employee or how long it takes for something to be made, you should think about how quality your product is.
-
Value-based: This is one of the newest forms of JIT. In this case, you're not concerned with how well the products perform or whether they meet customer expectations. Instead, you focus on the added value that you provide to your market.
-
Stock-based is an inventory-based system that measures the number of items produced at any given moment. It's useful when you want maximum production and minimal inventory.
-
Just-in time (JIT), planning: This is a combination JIT/supply chain management. It is the process of scheduling components' delivery as soon as they have been ordered. It's important as it reduces leadtimes and increases throughput.