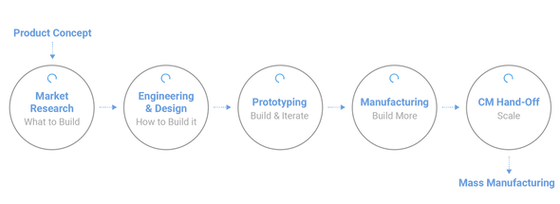
Your location and your specialization will affect the salary of a material engineering engineer. Apple, ConocoPhillips and Meta are some of the most highly-paid companies. Other places, like FedEx or Motorola Solutions, are also great places to work as a material engineer.
Materials engineers must understand the relationships between materials and processing methods. They must also be capable of identifying the causes and consequences of failures. In addition, they must be able to communicate engineering concepts to non-engineers. They are also responsible for identifying and implementing cost-efficient operation strategies. They may also need access to suppliers and other professionals. They may also be required to travel abroad to obtain samples for testing. Sometimes, they might work up to 40 hours per week.
Advanced degrees may be available for materials engineers. They may be able pursue a PhD degree in process engineering. They may also be able to find teaching positions or work in research. Senior material engineers could be responsible for more management responsibilities. They may also have the chance to engage in innovative research.
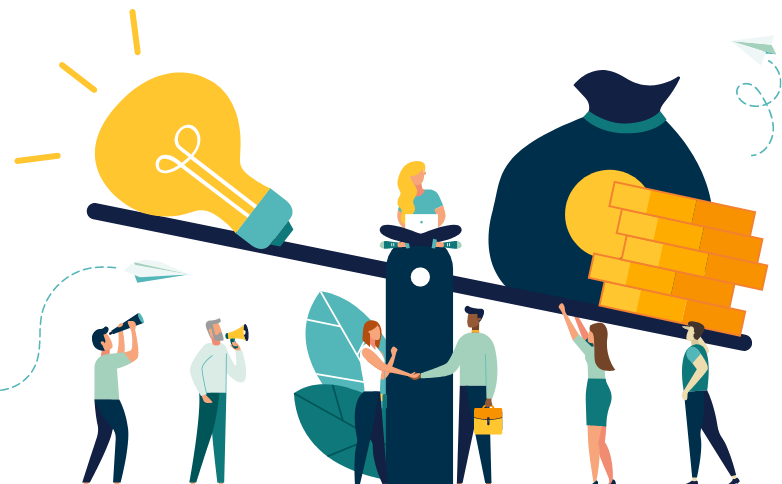
Materials engineers may work in manufacturing plants or offices, and may also travel to worksites to collect samples for testing. This industry is extremely competitive. It is therefore important to keep abreast of new developments and industry trends. They might also need to maintain good relationships with customers. They can assist product engineers in implementing green practices and improving their products. As a result, they may be able to develop a strong reputation in their field.
Materials engineers can also work in labs. Advanced math topics may be used for troubleshooting and design. They may also need to be able to communicate engineering concepts clearly and effectively. They may also be required travel to other countries in order to obtain samples or observe the manufacturing process.
Materials engineers are typically hired by technology companies, such as Apple and FedEx. Raytheon Technologies is one example of a company that employs materials engineers. This field is extremely competitive and it may prove difficult to land a job at these companies. Engineer consulting firms may also offer opportunities to become material engineers. In addition, they may start their own businesses, which can allow them to stay on top of their industry.
Materials engineers may also be required to work long hours. They might travel to work sites to collect samples or observe how materials are used in manufacturing plants. In addition, they may work more than 40 hours if they are working as a material engineer in a factory. This means they might need to have a strong work ethic.
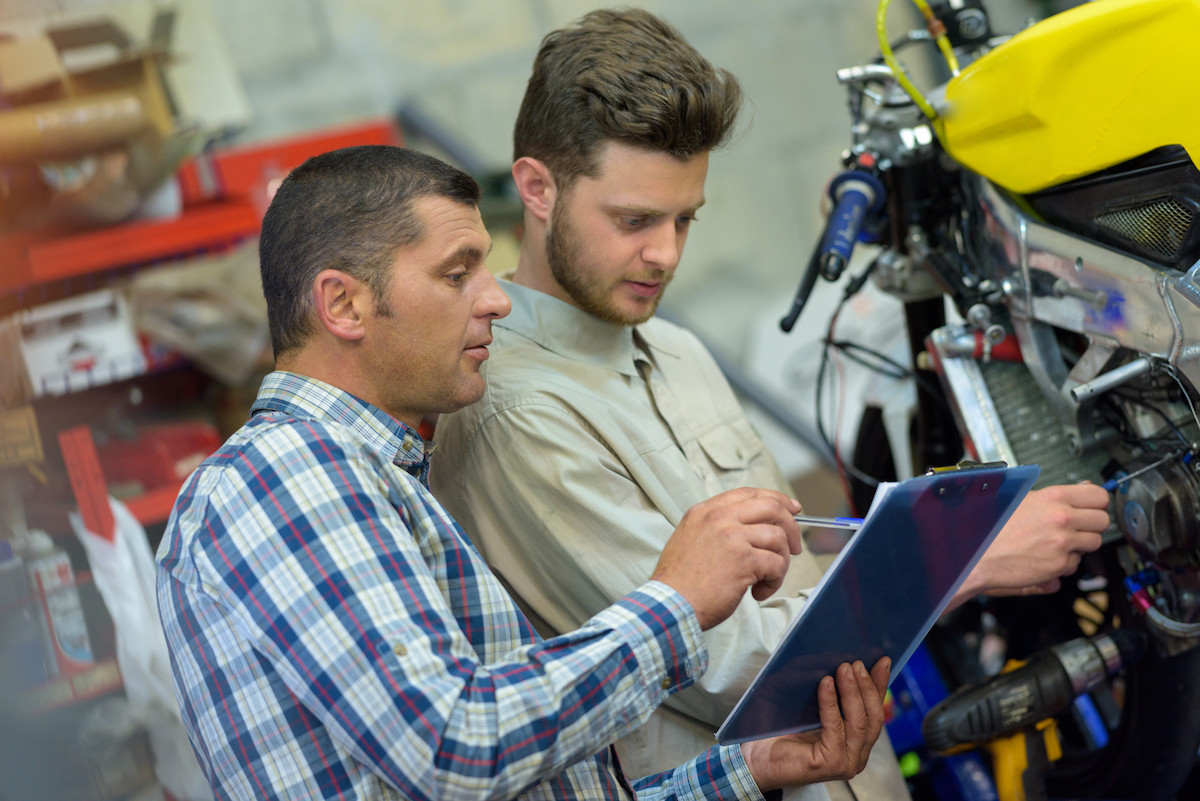
Material engineers might need to work in a team. They might need to communicate with clients and other professionals as well as with suppliers. They could also be responsible to make sure deadlines are met and budgets are met.
FAQ
What are my options for learning more about manufacturing
The best way to learn about manufacturing is through hands-on experience. However, if that's not possible, you can always read books or watch educational videos.
What are the main products of logistics?
Logistics involves the transportation of goods from point A and point B.
They cover all aspects of transportation, such as packing, loading, transporting and unloading.
Logisticians ensure the product reaches its destination in the most efficient manner. Logisticians help companies improve their supply chain efficiency by providing information about demand forecasts and stock levels, production schedules, as well as availability of raw materials.
They can also track shipments in transit and monitor quality standards.
What skills do production planners need?
Being a production planner is not easy. You need to be organized and flexible. Communication skills are essential to ensure that you can communicate effectively with clients, colleagues, and customers.
How can manufacturing efficiency improved?
The first step is to identify the most important factors affecting production time. The next step is to identify the most important factors that affect production time. If you don’t know how to start, look at which factors have the greatest impact upon production time. Once you identify them, look for solutions.
What do you mean by warehouse?
A warehouse, or storage facility, is where goods are stored prior to being sold. It can be an indoor space or an outdoor area. In some cases it could be both indoors and outdoors.
Why is logistics so important in manufacturing?
Logistics are an integral part any business. They help you achieve great results by helping you manage all aspects of product flow, from raw materials to finished goods.
Logistics also play a major role in reducing costs and increasing efficiency.
Statistics
- According to the United Nations Industrial Development Organization (UNIDO), China is the top manufacturer worldwide by 2019 output, producing 28.7% of the total global manufacturing output, followed by the United States, Japan, Germany, and India.[52][53] (en.wikipedia.org)
- You can multiply the result by 100 to get the total percent of monthly overhead. (investopedia.com)
- Many factories witnessed a 30% increase in output due to the shift to electric motors. (en.wikipedia.org)
- In 2021, an estimated 12.1 million Americans work in the manufacturing sector.6 (investopedia.com)
- According to a Statista study, U.S. businesses spent $1.63 trillion on logistics in 2019, moving goods from origin to end user through various supply chain network segments. (netsuite.com)
External Links
How To
How to Use Lean Manufacturing for the Production of Goods
Lean manufacturing (or lean manufacturing) is a style of management that aims to increase efficiency, reduce waste and improve performance through continuous improvement. It was developed by Taiichi Okono in Japan, during the 1970s & 1980s. TPS founder Kanji Takoda awarded him the Toyota Production System Award (TPS). Michael L. Watkins published the "The Machine That Changed the World", the first book about lean manufacturing. It was published in 1990.
Lean manufacturing is often defined as a set of principles used to improve the quality, speed, and cost of products and services. It emphasizes the elimination of defects and waste throughout the value stream. Lean manufacturing is also known as just in time (JIT), zero defect total productive maintenance(TPM), and five-star (S). Lean manufacturing emphasizes reducing non-value-added activities like inspection, rework and waiting.
In addition to improving product quality and reducing costs, lean manufacturing helps companies achieve their goals faster and reduces employee turnover. Lean manufacturing is a great way to manage the entire value chain including customers, suppliers, distributors and retailers as well as employees. Lean manufacturing is widely used in many industries. Toyota's philosophy, for example, is what has enabled it to be successful in electronics, automobiles, medical devices, healthcare and chemical engineering as well as paper and food.
Five fundamental principles underlie lean manufacturing.
-
Define Value - Determine the value that your business brings to society. Also, identify what sets you apart from your competitors.
-
Reduce waste - Get rid of any activity that does not add value to the supply chain.
-
Create Flow. Ensure that your work is uninterrupted and flows seamlessly.
-
Standardize and simplify - Make your processes as consistent as possible.
-
Build relationships - Develop and maintain personal relationships with both your internal and external stakeholders.
Although lean manufacturing has always been around, it is gaining popularity in recent years because of a renewed interest for the economy after 2008's global financial crisis. Many businesses have adopted lean manufacturing techniques to help them become more competitive. Economists think that lean manufacturing is a crucial factor in economic recovery.
Lean manufacturing is now becoming a common practice in the automotive industry, with many benefits. These include improved customer satisfaction, reduced inventory levels, lower operating costs, increased productivity, and better overall safety.
The principles of lean manufacturing can be applied in almost any area of an organization. However, it is particularly useful when applied to the production side of an organization because it ensures that all steps in the value chain are efficient and effective.
There are three main types of lean manufacturing:
-
Just-in Time Manufacturing (JIT), also known as "pull system": This form of lean manufacturing is often referred to simply as "pull". JIT is a method in which components are assembled right at the moment of use, rather than being manufactured ahead of time. This method reduces lead times, increases availability, and decreases inventory.
-
Zero Defects Manufacturing (ZDM): ZDM focuses on ensuring that no defective units leave the manufacturing facility. Repairing a part that is damaged during assembly should be done, not scrapping. This is also true for finished products that require minor repairs before shipping.
-
Continuous Improvement (CI),: Continuous improvement aims improve the efficiency and effectiveness of operations by continuously identifying issues and making changes to reduce waste. Continuous improvement refers to continuous improvement of processes as well people and tools.