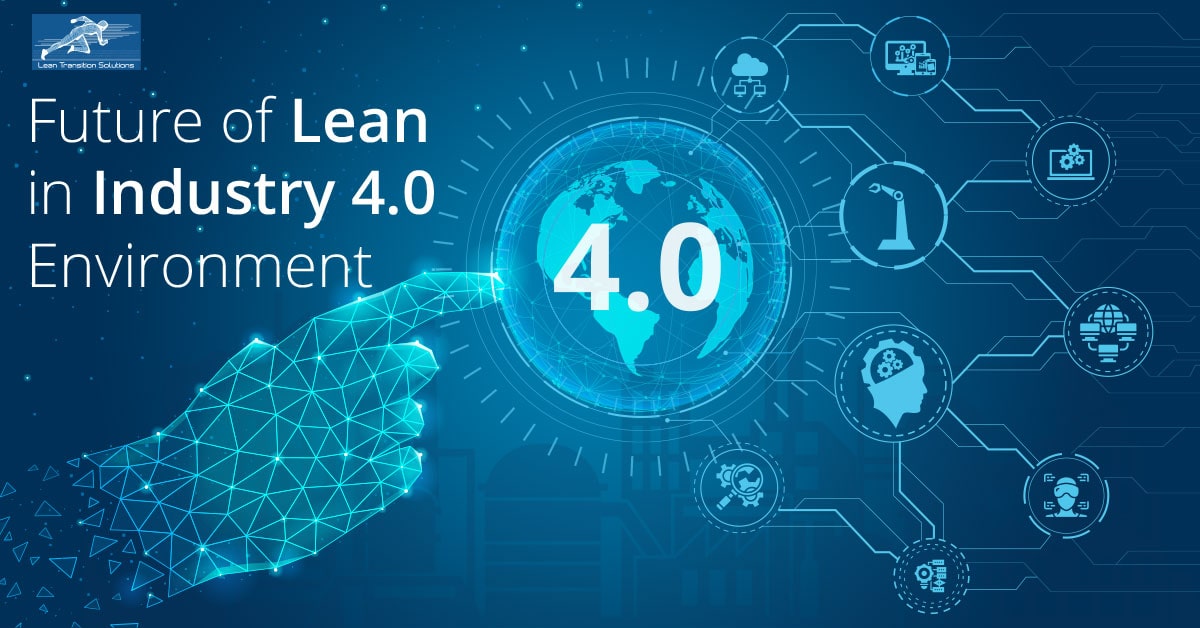
Supply networks can be described as complex adaptive systems where many firms are involved in the delivery of goods or services. A supply network includes a variety of interrelated businesses that supply raw materials, finished goods, or other commodities. A supply network serves many functions beyond its traditional ones. However, it can also be used in digital flows and resources.
As supply networks evolve, they come in all shapes and sizes. It is essential to design a system which is resilient to unanticipated events. This involves understanding the various supply networks and how they can respond to disruptions. This problem can be addressed using a variety of approaches.
One way to measure resilience is to look at the flow of information. The information flow between the end-customer and preceding organisations is a good place to start. It is also useful to gauge the strength a relationship. For example, if the first supplier is connected to second supplier, the manufacturer might be in a position to spot missing links.
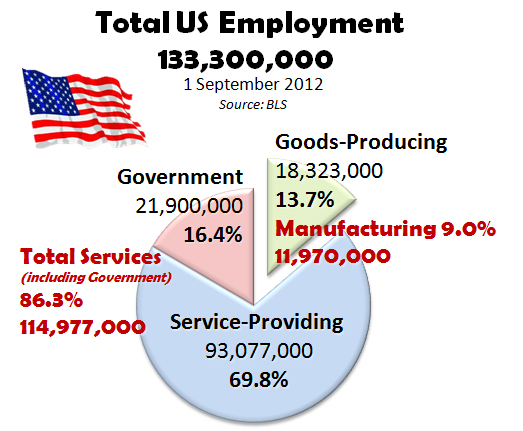
A supply network that facilitates this type of flow will be able to deliver the desired product or services to the end-customer. Implementing such a smart approach to supply chain management isn't as easy as it sounds. First, companies must find a way to overcome the constraints of existing networks. The second is to ensure that the way they manage information flows can withstand disruptions.
The role of intermediaries is another important aspect of the supply-chain. These are entities that are not fully understood about their roles in the supply network. One example is a semiconductor producer moving work-inprocess material from fabrication into assembly. Manufacturers can improve the efficiency and speed of their production by moving the materials in the correct way. Similar to the above, a manufacturing company that heavily relies on purchasing subcomponents of other companies can scale down or up depending on its production demands.
Incorporating the various intermediaries into the supply network model can lead to unexpected results. Better communication can result, among other benefits, in higher productivity and efficiency. Additionally, strong partnerships can help organisations improve their service to customers.
High to moderate levels of complexity are common in supply networks. This is because suppliers are responsible for making decisions about which goods to buy and which items to re-sell. The overall network must also be functional. As a result, power imbalances are quite common. These are easily managed by a few key strategies.
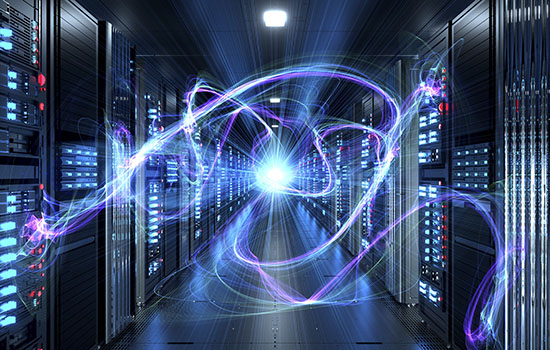
There are several ways to reduce this problem. One way is to set up a control tower that monitors and manages suppliers. Another way is to create a data center to analyse and gather data. A third option is to use an automated decision-making system. A rebalancing exercise can be used to correct imbalances, and a buffer is designed to protect the network from disruptions. Suppliers who are able predict and meet the clients' requirements may be better able than others to prevent a meltdown in their supply networks.
FAQ
What is the role of a logistics manager
A logistics manager makes sure that all goods are delivered on-time and in good condition. This is accomplished by using the experience and knowledge gained from working with company products. He/she also needs to ensure adequate stock to meet demand.
How important is automation in manufacturing?
Automation is essential for both manufacturers and service providers. Automation allows them to deliver services quicker and more efficiently. It also helps to reduce costs and improve productivity.
What is production management?
Production planning is the process of creating a plan that covers all aspects of production. This includes scheduling, budgeting and crew, location, equipment, props, and more. This document ensures that everything is prepared and available when you are ready for shooting. This document should include information about how to achieve the best results on-set. It should include information about shooting locations, casting lists, crew details, equipment requirements, and shooting schedules.
The first step in filming is to define what you want. You may have already chosen the location you want, or there are locations or sets you prefer. Once you have identified your locations and scenes it's time to begin figuring out what elements you will need for each one. One example is if you are unsure of the exact model you want but decide that you require a car. If this is the case, you might start searching online for car models and then narrow your options by selecting from different makes.
After you have selected the car you want, you can begin to think about additional features. What about additional seating? Or maybe you just need someone to push the car around. Maybe you want to change the interior color from black to white? These questions will help to determine the style and feel of your car. You can also think about the type of shots you want to get. You will be filming close-ups and wide angles. Maybe you want to show the engine and the steering wheel. These details will help identify the exact car you wish to film.
Once you have determined all of the above, you can move on to creating a schedule. The schedule will show you when to begin shooting and when to stop. Each day will include the time when you need to arrive at the location, when you need to leave and when you need to return home. This way, everyone knows what they need to do and when. It is possible to make arrangements in advance for additional staff if you are looking to hire. You don't want to hire someone who won't show up because he didn't know.
Your schedule will also have to be adjusted to reflect the number of days required to film. Some projects take only a few days while others can last several weeks. When you are creating your schedule, you should always keep in mind whether you need more than one shot per day or not. Multiple takes of the same location will lead to higher costs and take more time. If you are unsure if you need multiple takes, it is better to err on the side of caution and shoot fewer takes rather than risk wasting money.
Budgeting is another important aspect of production planning. As it will allow you and your team to work within your financial means, setting a realistic budget is crucial. It is possible to reduce the budget at any time if you experience unexpected problems. You shouldn't underestimate the amount you'll spend. You'll end up with less money after paying for other things if the cost is underestimated.
Planning production is a tedious process. Once you have a good understanding of how everything works together, planning future projects becomes easy.
What are the differences between these four types?
Manufacturing refers to the transformation of raw materials into useful products by using machines and processes. It involves many different activities such as designing, building, testing, packaging, shipping, selling, servicing, etc.
Statistics
- In the United States, for example, manufacturing makes up 15% of the economic output. (twi-global.com)
- Many factories witnessed a 30% increase in output due to the shift to electric motors. (en.wikipedia.org)
- Job #1 is delivering the ordered product according to specifications: color, size, brand, and quantity. (netsuite.com)
- According to the United Nations Industrial Development Organization (UNIDO), China is the top manufacturer worldwide by 2019 output, producing 28.7% of the total global manufacturing output, followed by the United States, Japan, Germany, and India.[52][53] (en.wikipedia.org)
- According to a Statista study, U.S. businesses spent $1.63 trillion on logistics in 2019, moving goods from origin to end user through various supply chain network segments. (netsuite.com)
External Links
How To
How to use the Just In-Time Production Method
Just-in-time is a way to cut costs and increase efficiency in business processes. This is where you have the right resources at the right time. This means that only what you use is charged to your account. Frederick Taylor first coined this term while working in the early 1900s as a foreman. After observing how workers were paid overtime for late work, he realized that overtime was a common practice. He decided to ensure workers have enough time to do their jobs before starting work to improve productivity.
JIT is a way to plan ahead and make sure you don't waste any money. Look at your entire project, from start to end. Make sure you have enough resources in place to deal with any unexpected problems. You will have the resources and people to solve any problems you anticipate. This way, you won't end up paying extra money for things that weren't really necessary.
There are several types of JIT techniques:
-
Demand-driven: This is a type of JIT where you order the parts/materials needed for your project regularly. This will allow for you to track the material that you have left after using it. This will allow you to calculate how long it will take to make more.
-
Inventory-based: You stock materials in advance to make your projects easier. This allows one to predict how much they will sell.
-
Project-driven: This method allows you to set aside enough funds for your project. Once you have an idea of how much material you will need, you can purchase the necessary materials.
-
Resource-based JIT: This type of JIT is most commonly used. You assign certain resources based off demand. You will, for example, assign more staff to deal with large orders. You'll have fewer orders if you have fewer.
-
Cost-based: This is the same as resource-based except that you don't care how many people there are but how much each one of them costs.
-
Price-based pricing: This is similar in concept to cost-based but instead you look at how much each worker costs, it looks at the overall company's price.
-
Material-based - This is a variant of cost-based. But instead of looking at the total company cost, you focus on how much raw material you spend per year.
-
Time-based: Another variation of resource-based JIT. Instead of worrying about how much each worker costs, you can focus on how long the project takes.
-
Quality-based JIT: This is another variation of resource based JIT. Instead of focusing on the cost of each worker or how long it takes, think about how high quality your product is.
-
Value-based: This is one of the newest forms of JIT. This is where you don't care about how the products perform or whether they meet customers' expectations. Instead, your goal is to add value to the market.
-
Stock-based. This method is inventory-based and focuses only on the actual production at any given point. It is used when production goals are met while inventory is kept to a minimum.
-
Just-intime (JIT), planning is a combination JIT management and supply chain management. This refers to the scheduling of the delivery of components as soon after they are ordered. It reduces lead times and improves throughput.