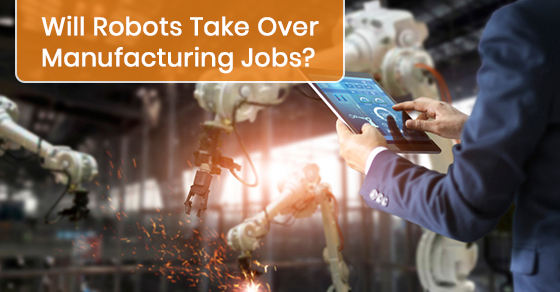
A nuclear engineer can easily make anywhere from six to seven figure salaries. Aside from their regular duties, they can supervise the construction of nuclear facilities and even oversee work in closed facilities. Sometimes, the job requires them to defend their work from the public. Many reasons make nuclear engineers highly desirable. They are highly skilled in leadership and technical expertise. This profession's salary depends on many factors including education, experience, and whereabouts.
A bachelor's degree is enough to earn a salary as a nuclear engineer.
The federal government has the highest number of nuclear engineers. The engineering, scientific research and development, and manufacturing sectors are also important employers. Due to increased interest in nuclear energy, the demand for nuclear engineers in engineering and research and design will grow over the next ten years. This new technology may increase the production of commercial nuclear power plant. However, they don't currently have many.
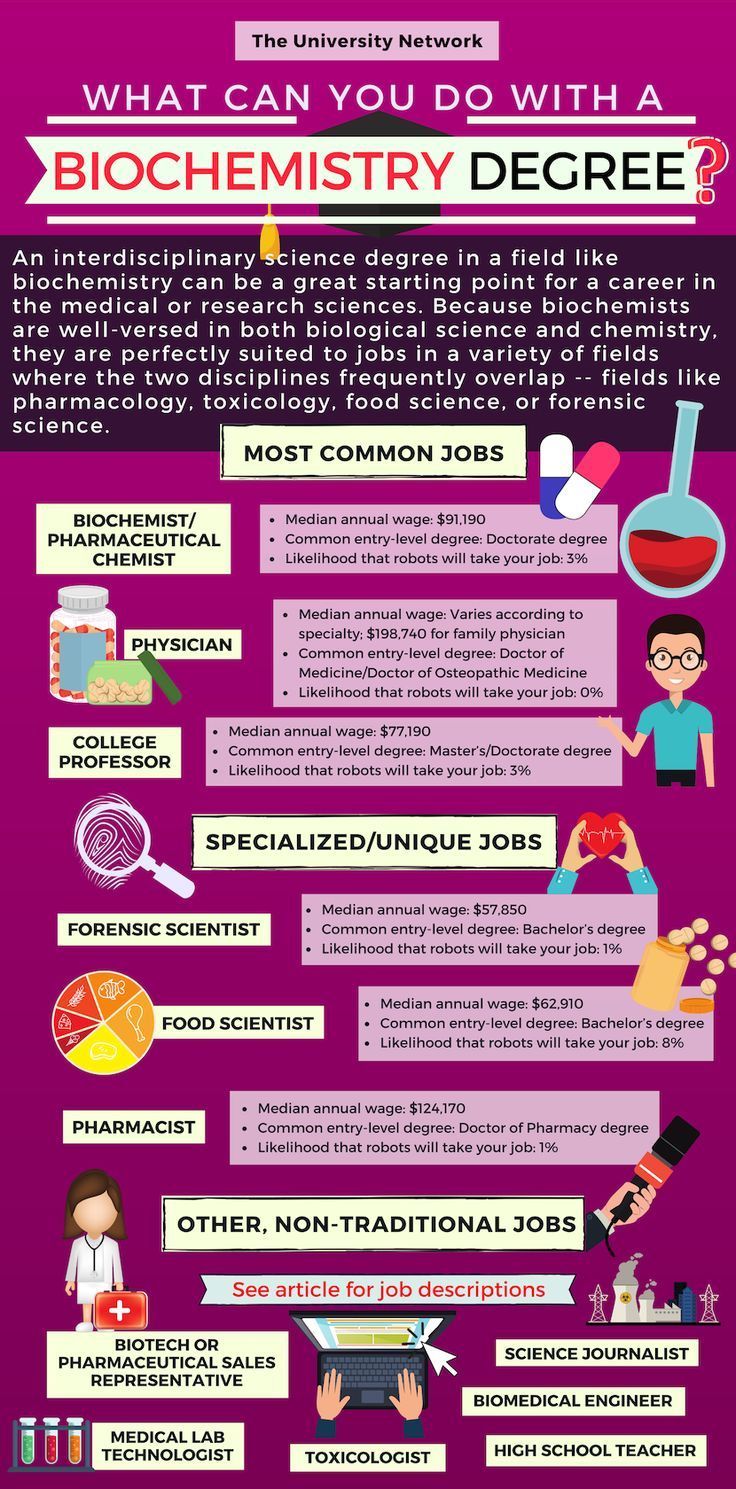
To become a Nuclear Engineer, you will need a Bachelor's Degree in Engineering or a closely related field. A bachelor's in nuclear engineering could lead to an entry-level position or a better career path for those who have completed a masters degree. Some positions may require state licensure, as well. For their first few years, nuclear engineers will work under an engineer who is experienced. This gives them the opportunity to gain responsibility and experience while they are working under him.
Average salary for nuclear engineers with master's degrees
The salary expectations for nuclear engineers are important to consider if you're thinking about a career. Although you can get a job at any nuclear power station, it is more common to work in an office environment. People interested in a career as a nuclear power generator engineer will likely work in power plants. They will also be working with mechanical and electrical engineers. These professionals will help them integrate systems they have designed. The majority of nuclear engineers work full time and can work for longer hours than their counterparts.
A nuclear engineer with a Master of Science degree will earn $124 27,272 annually, which is significantly more that the average wage for all US workers. The salary ranges for different positions can vary. An average salary for nuclear engineers is $185,550. The average starting wage is $74,800 and is among the highest paid in the field.
A nuclear engineer's starting salary
To be a successful career in nuclear engineering you will need to understand the average starting pay. You need to have a strong education and a lot of work experience. Nuclear engineers can expect steady career growth. However, they are also able to move into a similar field if needed. Nuclear engineers may also be involved in space exploration, manufacturing, and medical uses of radiological substances.
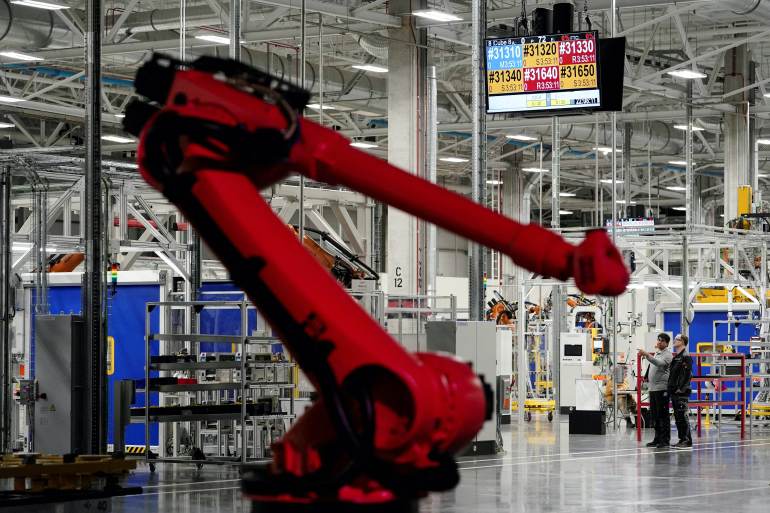
Nuclear engineers can work in many industries but the federal government is their largest employer. The operation of these facilities is overseen by Office for Nuclear Regulation. Other industries that are available to this profession include construction, manufacturing and scientific research, as well as scientific research, development, and other technical services. Future employment opportunities for nuclear engineers will increase as nuclear power is used more. However, the lack of graduates will reduce job prospects for those who have this degree. While the federal government does not currently have many jobs for nuclear engineers at this time, there are several companies that are seeking these professionals.
FAQ
How can I learn about manufacturing?
You can learn the most about manufacturing by getting involved in it. However, if that's not possible, you can always read books or watch educational videos.
What is the job of a logistics manger?
Logistics managers make sure all goods are delivered on schedule and without damage. This is done using his/her knowledge of the company's products. He/she should also ensure enough stock is available to meet demand.
How can we improve manufacturing efficiency?
The first step is to identify the most important factors affecting production time. The next step is to identify the most important factors that affect production time. You can start by identifying the most important factors that impact production time. Once you've identified them, try to find solutions for each of those factors.
What do you mean by warehouse?
Warehouses and storage facilities are where goods are kept before being sold. It can be an indoor space or an outdoor area. In some cases, it may be a combination of both.
What are the 7 Rs of logistics?
The acronym 7R's for Logistics stands to represent the seven basic principles in logistics management. It was created by the International Association of Business Logisticians and published in 2004 under its "Seven Principles of Logistics Management".
The acronym is made up of the following letters:
-
Responsible - ensure that all actions taken are within legal requirements and are not harmful to others.
-
Reliable - Have confidence in your ability to fulfill all of your commitments.
-
It is reasonable to use resources efficiently and not waste them.
-
Realistic – consider all aspects of operations, from cost-effectiveness to environmental impact.
-
Respectful - treat people fairly and equitably.
-
Be resourceful: Look for opportunities to save money or increase productivity.
-
Recognizable - provide customers with value-added services.
What are the four types in manufacturing?
Manufacturing is the process that transforms raw materials into useful products. Manufacturing can include many activities such as designing and building, testing, packaging shipping, selling, servicing, and other related activities.
Are there ways to automate parts of manufacturing?
Yes! Yes! Automation has existed since ancient times. The wheel was invented by the Egyptians thousands of years ago. Nowadays, we use robots for assembly lines.
In fact, there are several applications of robotics in manufacturing today. These include:
-
Automated assembly line robots
-
Robot welding
-
Robot painting
-
Robotics inspection
-
Robots that produce products
Manufacturing can also be automated in many other ways. For instance, 3D printing allows us make custom products and not have to wait for months or even weeks to get them made.
Statistics
- According to a Statista study, U.S. businesses spent $1.63 trillion on logistics in 2019, moving goods from origin to end user through various supply chain network segments. (netsuite.com)
- It's estimated that 10.8% of the U.S. GDP in 2020 was contributed to manufacturing. (investopedia.com)
- Many factories witnessed a 30% increase in output due to the shift to electric motors. (en.wikipedia.org)
- In 2021, an estimated 12.1 million Americans work in the manufacturing sector.6 (investopedia.com)
- You can multiply the result by 100 to get the total percent of monthly overhead. (investopedia.com)
External Links
How To
How to Use lean manufacturing in the Production of Goods
Lean manufacturing (or lean manufacturing) is a style of management that aims to increase efficiency, reduce waste and improve performance through continuous improvement. It was developed by Taiichi Okono in Japan, during the 1970s & 1980s. TPS founder Kanji Takoda awarded him the Toyota Production System Award (TPS). Michael L. Watkins published the "The Machine That Changed the World", the first book about lean manufacturing. It was published in 1990.
Lean manufacturing can be described as a set or principles that are used to improve quality, speed and cost of products or services. It emphasizes the elimination and minimization of waste in the value stream. Lean manufacturing is also known as just in time (JIT), zero defect total productive maintenance(TPM), and five-star (S). Lean manufacturing emphasizes reducing non-value-added activities like inspection, rework and waiting.
Lean manufacturing is a way for companies to achieve their goals faster, improve product quality, and lower costs. Lean manufacturing has been deemed one of the best ways to manage the entire value-chain, including customers, distributors as well retailers and employees. Lean manufacturing practices are widespread in many industries. For example, Toyota's philosophy underpins its success in automobiles, electronics, appliances, healthcare, chemical engineering, aerospace, paper, food, etc.
Five principles are the basis of lean manufacturing:
-
Define value - Find out what your business contributes to society, and what makes it different from other competitors.
-
Reduce Waste – Eliminate all activities that don't add value throughout the supply chain.
-
Create Flow: Ensure that the work process flows without interruptions.
-
Standardize and Simplify – Make processes as consistent, repeatable, and as simple as possible.
-
Building Relationships – Establish personal relationships with both external and internal stakeholders.
Lean manufacturing isn’t new, but it has seen a renewed interest since 2008 due to the global financial crisis. Many companies have adopted lean manufacturing methods to increase their marketability. Some economists even believe that lean manufacturing can be a key factor in economic recovery.
Lean manufacturing is now becoming a common practice in the automotive industry, with many benefits. These benefits include increased customer satisfaction, reduced inventory levels and lower operating costs.
It can be applied to any aspect of an organisation. However, it is particularly useful when applied to the production side of an organization because it ensures that all steps in the value chain are efficient and effective.
There are three main types:
-
Just-in Time Manufacturing, (JIT): This kind of lean manufacturing is also commonly known as "pull-systems." JIT refers to a system in which components are assembled at the point of use instead of being produced ahead of time. This approach reduces lead time, increases availability and reduces inventory.
-
Zero Defects Manufacturing - ZDM: ZDM focuses its efforts on making sure that no defective units leave a manufacturing facility. It is better to repair a part than have it removed from the production line if it needs to be fixed. This applies to finished products, which may need minor repairs before they are shipped.
-
Continuous Improvement (CI),: Continuous improvement aims improve the efficiency and effectiveness of operations by continuously identifying issues and making changes to reduce waste. Continuous Improvement (CI) involves continuous improvement in processes, people, tools, and infrastructure.