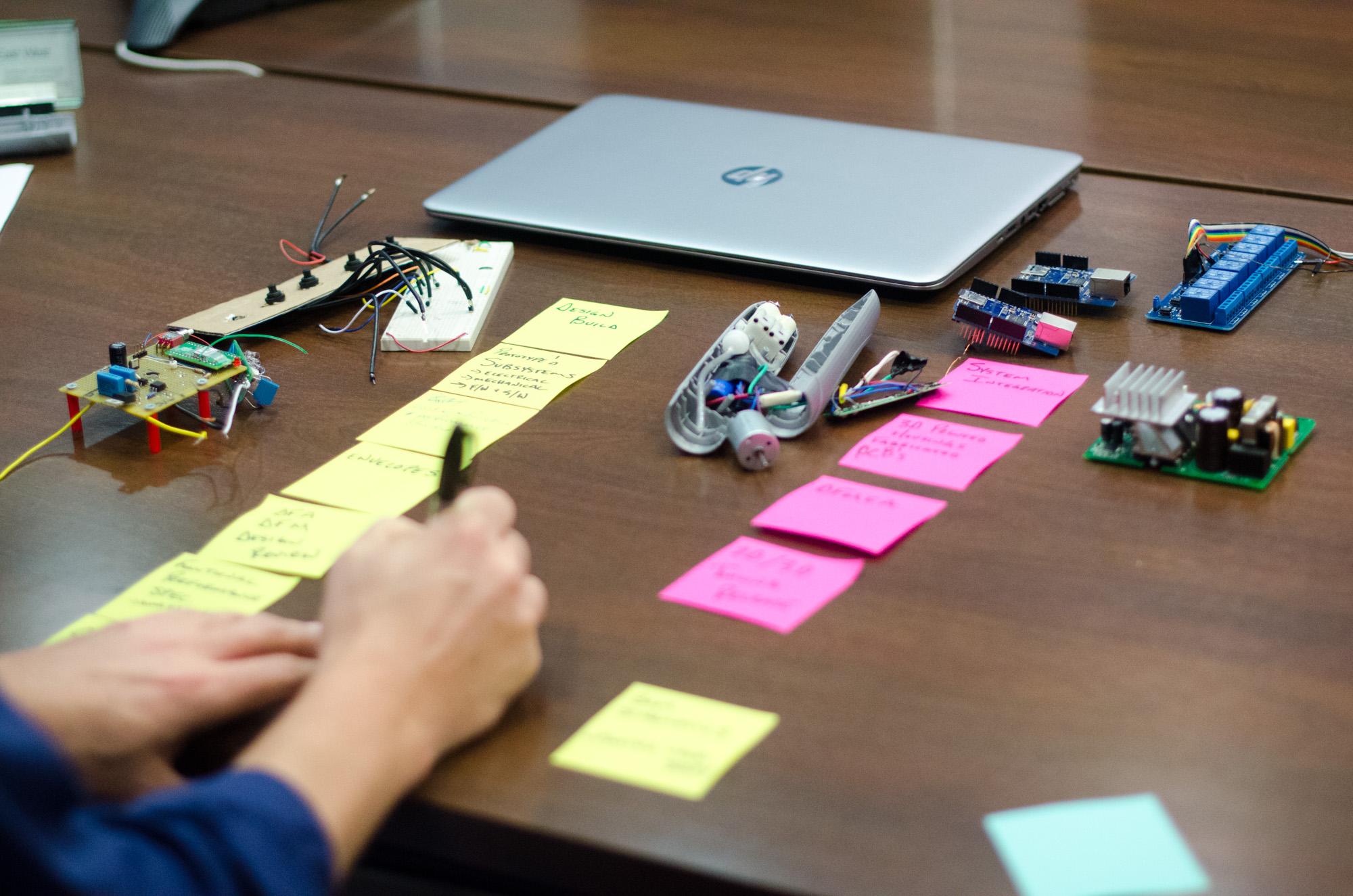
There are thousands of Connecticut manufacturing jobs waiting to be filled. There are 4,011 manufacturing companies in Connecticut, employing 159,000 people. Manufacturing is one of the state's largest contributors to the gross state product, and it pays an above-average salary statewide. The Connecticut Business and Industry Association released a survey about the state's manufacturing workforce requirements. The survey found that 13,000 jobs in manufacturing are vacant in Connecticut, and many companies struggle to find younger workers.
The Connecticut manufacturing workforce is older than average, with over a third of workers being over 55. Many companies relocated manufacturing facilities to lower labor costs, and other operations began using new machinery and automation. The reputation of manufacturing has improved. In the past, it was still considered dangerous and dirty. Today, companies offer apprenticeships, internships, and entry level positions. Manufacturing is Connecticut's third largest job-creator. Its high technology operations are a key competitive edge.
There are many programs available in Connecticut that help people get qualified for jobs in manufacturing. Manufacturing Innovation Fund supports comprehensive high schools and universities as well as vocational high schools. It also supports online training programs, pre-apprenticeships, and career activities for K-12 students.
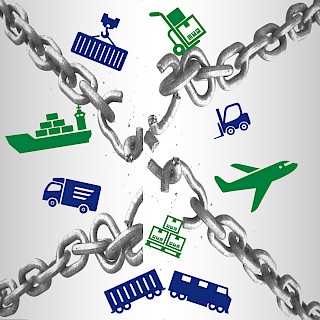
The backgrounds of advanced manufacturing workers are varied. Some work in manufacturing right out of highschool while others have worked in different fields for many years before switching to the field. Some may have gone to school for a degree or have been in the military for many years. Many companies will cover tuition for advanced manufacturing training programs. Some programs also offer wage subsidies to help with entry-level training.
In addition to reintroducing technical education options, the state's Comprehensive high schools have also started doing so. One example is Grasso Tech's welding program. This program will be available starting in fall 2019. Employers that employ students through the EB may be interested to hire Connecticutans. The Eastern Connecticut Manufacturing Pipeline, a program that supports advanced manufacturing companies in the area, is available. It is modeled after Eastern Connecticut Workforce Investment Board’s Manufacturing Pipeline.
The Manufacturing Careers Program was created to assist job seekers interested in manufacturing careers and demonstrate their readiness for entry-level work. It connects pre-screened job applicants with manufacturers and other employers. The program offers a CNC Basics training course as well as a career path that is industry-focused. The Advanced Manufacturing Employer Partnership provides wage subsidies and entry-level training to those who are enrolled in this program.
Young workers might not be aware of manufacturing or want to work in this industry. This may make it difficult for them participate in these education programmes. These programs are funded by the state with millions of dollars. These programs have a limited reach as young people are unaware of the existence of these jobs.
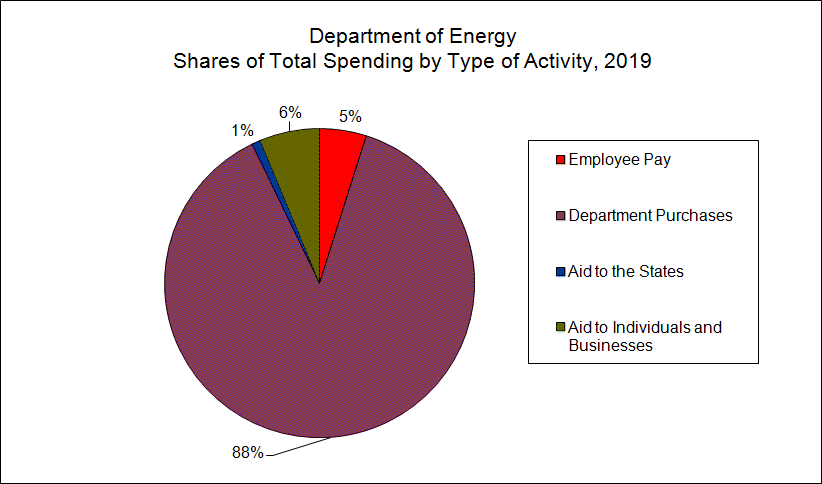
A statewide STEM Town initiative is one innovative way to address Connecticut's shortage of manufacturing jobs. This would involve reallocating funds and improving education to meet the needs.
FAQ
How can efficiency in manufacturing be improved?
First, determine which factors have the greatest impact on production time. We then need to figure out how to improve these variables. If you don’t know how to start, look at which factors have the greatest impact upon production time. Once you have identified them, it is time to identify solutions.
What skills are required to be a production manager?
You must be flexible and organized to become a productive production planner. Effective communication with clients and colleagues is essential.
What jobs are available in logistics?
There are different kinds of jobs available in logistics. These are some of the jobs available in logistics:
-
Warehouse workers - They load and unload trucks and pallets.
-
Transportation drivers: They drive trucks and trailers and deliver goods and make pick-ups.
-
Freight handlers, - They sort out and pack freight in warehouses.
-
Inventory managers - These are responsible for overseeing the stock of goods in warehouses.
-
Sales reps - They sell products and services to customers.
-
Logistics coordinators - They organize and plan logistics operations.
-
Purchasing agents – They buy goods or services necessary to run a company.
-
Customer service agents - They answer phone calls and respond to emails.
-
Ship clerks - They issue bills and process shipping orders.
-
Order fillers: They fill orders based off what has been ordered and shipped.
-
Quality control inspectors – They inspect incoming and outgoing products to ensure that there are no defects.
-
Others - There is a variety of other jobs in logistics. These include transportation supervisors and cargo specialists.
Is automation necessary in manufacturing?
Automation is essential for both manufacturers and service providers. They can provide services more quickly and efficiently thanks to automation. They can also reduce their costs by reducing human error and improving productivity.
Why automate your warehouse
Modern warehousing has seen automation take center stage. The rise of e-commerce has led to increased demand for faster delivery times and more efficient processes.
Warehouses must be able to quickly adapt to changing demands. Technology is essential for warehouses to be able to adapt quickly to changing needs. Automation warehouses can bring many benefits. Here are some of the reasons automation is worth your investment:
-
Increases throughput/productivity
-
Reduces errors
-
Accuracy is improved
-
Boosts safety
-
Eliminates bottlenecks
-
Allows companies to scale more easily
-
Increases efficiency of workers
-
Gives you visibility into all that is happening in your warehouse
-
Enhances customer experience
-
Improves employee satisfaction
-
This reduces downtime while increasing uptime
-
Quality products delivered on time
-
Removing human error
-
This helps to ensure compliance with regulations
What are the 7 Rs of logistics.
The acronym 7Rs of Logistics refers to the seven core principles of logistics management. It was developed by International Association of Business Logisticians (IABL), and published as part of their "Seven Principles of Logistics Management Series" in 2004.
The acronym consists of the following letters:
-
Responsible - to ensure that all actions are within the legal requirements and are not detrimental to others.
-
Reliable - have confidence in the ability to deliver on commitments made.
-
Reasonable - make sure you use your resources well and don't waste them.
-
Realistic – Consider all aspects, including cost-effectiveness as well as environmental impact.
-
Respectful - show respect and treat others fairly and fairly
-
You are resourceful and look for ways to save money while increasing productivity.
-
Recognizable is a company that provides customers with value-added solutions.
Statistics
- It's estimated that 10.8% of the U.S. GDP in 2020 was contributed to manufacturing. (investopedia.com)
- Job #1 is delivering the ordered product according to specifications: color, size, brand, and quantity. (netsuite.com)
- According to the United Nations Industrial Development Organization (UNIDO), China is the top manufacturer worldwide by 2019 output, producing 28.7% of the total global manufacturing output, followed by the United States, Japan, Germany, and India.[52][53] (en.wikipedia.org)
- [54][55] These are the top 50 countries by the total value of manufacturing output in US dollars for its noted year according to World Bank.[56] (en.wikipedia.org)
- (2:04) MTO is a production technique wherein products are customized according to customer specifications, and production only starts after an order is received. (oracle.com)
External Links
How To
How to Use 5S to Increase Productivity in Manufacturing
5S stands for "Sort", "Set In Order", "Standardize", "Separate" and "Store". Toyota Motor Corporation created the 5S methodology in 1954. It improves the work environment and helps companies to achieve greater efficiency.
This approach aims to standardize production procedures, making them predictable, repeatable, and easily measurable. This means that tasks such as cleaning, sorting, storing, packing, and labeling are performed daily. This knowledge allows workers to be more efficient in their work because they are aware of what to expect.
Implementing 5S requires five steps. These are Sort, Set In Order, Standardize. Separate. And Store. Each step requires a different action to increase efficiency. By sorting, for example, you make it easy to find the items later. When you set items in an order, you put items together. You then organize your inventory in groups. Finally, when you label your containers, you ensure everything is labeled correctly.
This process requires employees to think critically about how they do their job. Employees must be able to see why they do what they do and find a way to achieve them without having to rely on their old methods. To implement the 5S system, employees must acquire new skills and techniques.
In addition to increasing efficiency, the 5S method also improves morale and teamwork among employees. They will feel motivated to strive for higher levels of efficiency once they start to see results.