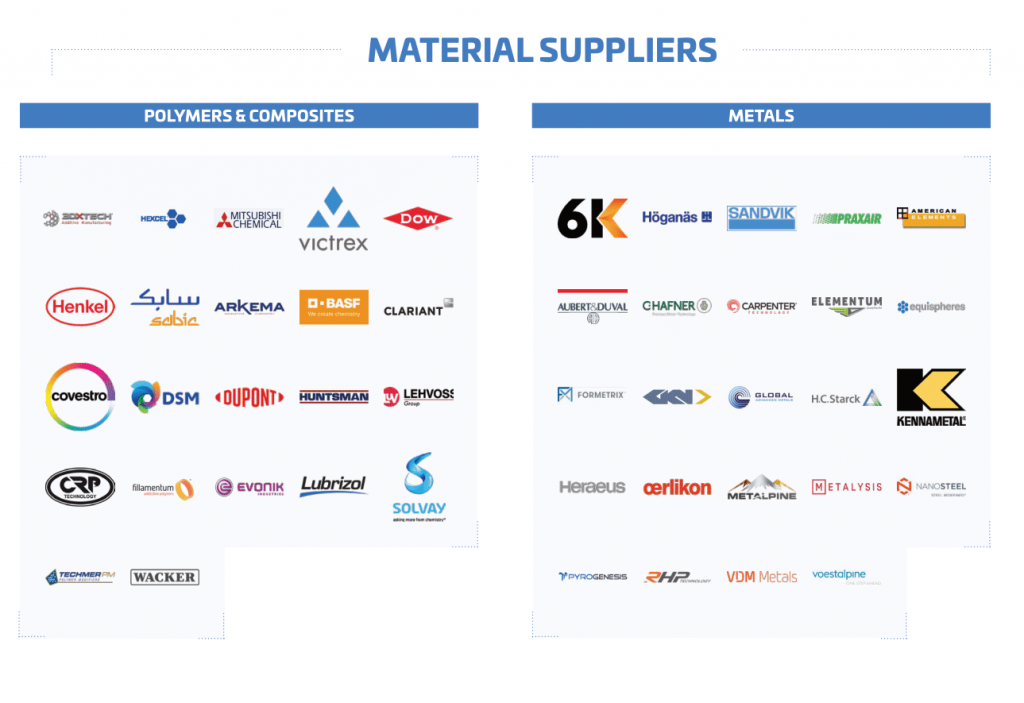
In the industrial manufacturing sector, there is increased global competition as well as a shortage skilled workers. Combined with increased supply chain volatility, the industrial manufacturing industry faces a challenging landscape in the 2020s. A comprehensive culture of innovation is required for the Industrial Products & Services sector to maximize growth in established markets while also maximizing growth opportunities in emerging markets.
According to a Deloitte and Manufacturing Institute report, the US manufacturing industry will face the largest shortage of skilled workers in its history. Over the next decade, 2 million jobs will remain vacant. Manufacturers must plan how they will improve their digital and innovation capabilities as the industry prepares for the future. Deloitte's Industrial Manufacturing team can assist manufacturers in navigating the industry landscape.
The fourth industrial revolution is continuing to disrupt the manufacturing industry. Industry must prepare workers for a future that involves networking within the "internet of things" and digital transformation. The Industrial Manufacturing team is skilled at establishing innovative management models that are grounded industry-specific expertise and deep industry knowledge. The team also offers a variety of digital transformation services to help manufacturers thrive in an era of digital disruption.
The Deloitte analysis is based upon extensive secondary data analysis on labor supply as well as interviews of executives from all sizes of manufacturing organizations. Economic projections are also included in the research. The findings also highlight the importance of a diverse workforce. Respondents cited adaptability to the company's values as key to their job satisfaction. A majority of respondents also stated that employees need to feel fulfilled at work if they want to be happy. Executives also think that millennials value environmental awareness and are increasingly interested in climate change issues.
Using the Oxford Economic Model, Deloitte predicts that manufacturing GDP will grow at a moderate rate of 1.3 percent in 2020. However, this is expected to be half of the growth seen over the past few decades. This will force companies to rethink their supply chain assurance strategies. In addition to this, companies must focus on larger management initiatives, such increasing resilience in operations. According to Deloitte's study, manufacturers will be making decisions regarding work environments and work practices.
Manufacturing companies must create pathways to careers and foster an inclusive culture in order to be ready for the future. It is possible to improve manufacturing efficiency by increasing resilience and reduce waste. In addition, the combination of digital technologies and lean principles can also help reduce manufacturing variability.
Deloitte recently released a report that examines diversity within the US manufacturing market. Deloitte's "Beyond Reskilling" report discusses how diversity is essential to manufacturing's future, and it highlights the benefits of having a diverse workforce.
FAQ
How can manufacturing avoid production bottlenecks
Production bottlenecks can be avoided by ensuring that processes are running smoothly during the entire production process, starting with the receipt of an order and ending when the product ships.
This includes both planning for capacity and quality control.
Continuous improvement techniques such Six Sigma are the best method to accomplish this.
Six Sigma can be used to improve the quality and decrease waste in all areas of your company.
It seeks to eliminate variation and create consistency in your work.
What are the goods of logistics?
Logistics is the process of moving goods from one point to another.
They include all aspects of transport, including packaging, loading, transporting, unloading, storing, warehousing, inventory management, customer service, distribution, returns, and recycling.
Logisticians make sure that the right product arrives at the right place at the correct time and in safe conditions. They assist companies with their supply chain efficiency through information on demand forecasts. Stock levels, production times, and availability.
They keep track and monitor the transit of shipments, maintain quality standards, order replenishment and inventories, coordinate with suppliers, vendors, and provide support for sales and marketing.
What skills should a production planner have?
A production planner must be organized, flexible, and able multitask to succeed. It is also important to be able communicate with colleagues and clients.
Statistics
- Job #1 is delivering the ordered product according to specifications: color, size, brand, and quantity. (netsuite.com)
- Many factories witnessed a 30% increase in output due to the shift to electric motors. (en.wikipedia.org)
- It's estimated that 10.8% of the U.S. GDP in 2020 was contributed to manufacturing. (investopedia.com)
- According to a Statista study, U.S. businesses spent $1.63 trillion on logistics in 2019, moving goods from origin to end user through various supply chain network segments. (netsuite.com)
- [54][55] These are the top 50 countries by the total value of manufacturing output in US dollars for its noted year according to World Bank.[56] (en.wikipedia.org)
External Links
How To
Six Sigma and Manufacturing
Six Sigma is "the application statistical process control (SPC), techniques for continuous improvement." Motorola's Quality Improvement Department in Tokyo, Japan developed Six Sigma in 1986. Six Sigma's core idea is to improve the quality of processes by standardizing and eliminating defects. Many companies have adopted this method in recent years. They believe there is no such thing a perfect product or service. Six Sigma's primary goal is to reduce variation from the average value of production. This means that if you take a sample of your product, then measure its performance against the average, you can find out what percentage of the time the process deviates from the norm. If there is a significant deviation from the norm, you will know that something needs to change.
The first step toward implementing Six Sigma is understanding how variability works in your business. Once you have a good understanding of the basics, you can identify potential sources of variation. These variations can also be classified as random or systematic. Random variations occur when people make mistakes; systematic ones are caused by factors outside the process itself. Random variations would include, for example, the failure of some widgets to fall from the assembly line. But if you notice that every widget you make falls apart at the exact same place each time, this would indicate that there is a problem.
Once you've identified where the problems lie, you'll want to design solutions to eliminate those problems. You might need to change the way you work or completely redesign the process. After implementing the new changes, you should test them again to see if they worked. If they didn't work, then you'll need to go back to the drawing board and come up with another plan.