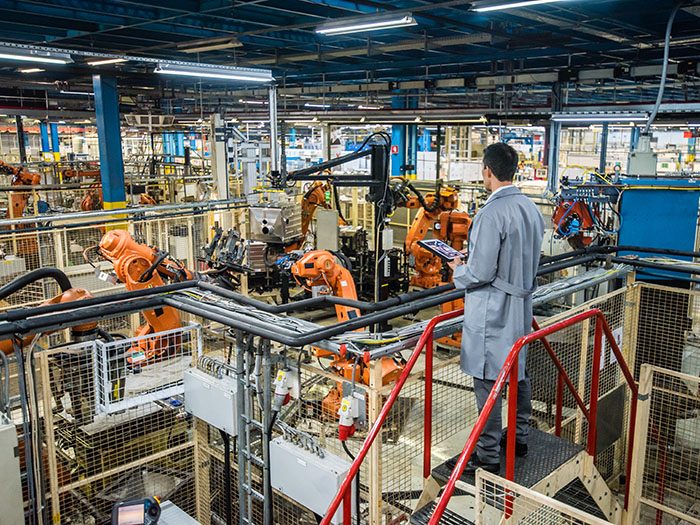
Three basic sectors are the basis of classical economics. Manufacturing, services, and financial activities can be classified into these three categories. The characteristics and risk factors that go into a business' classification are important. Below, you will learn more about each of the three sectors. This is a brief overview of the types of businesses in each sector. This information can be further explored if you are curious. Keep in mind, however, that these categories don't have to be mutually exclusive.
Economic activity
Factors such as production, inputs, outputs are key to determining the economic activity of any nation or country. The demand for particular goods or services is often the determinant of a region’s economic activity. There are two types economic activity: primary or secondary. Primary economic activities provide goods or services to satisfy daily human needs, while secondary economic activities add value to raw materials and combine them to make a more valuable product. Manufacturing and processing are two examples of secondary activities.
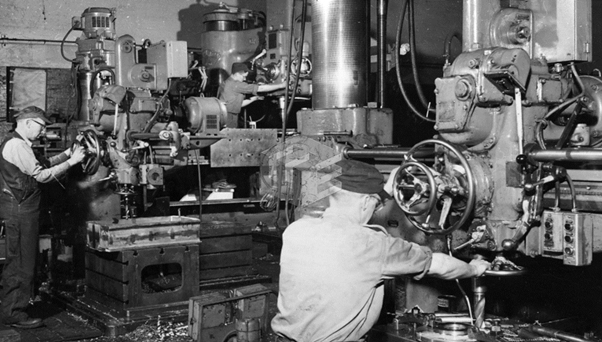
Classification of businesses
Business classification is the process of dividing businesses into groups based on the type of activities they perform. There are two major categories: primary and second. Primary businesses are those that mine and trade natural resources. The second category of businesses processes and converts raw materials to consumer-ready products. These two types of businesses have many differences. These are just a few of the differences between the two types. This article can be used to help you decide which business type is best for your company.
Characteristics
This discussion will explain the differences between primary, secondary and tertiary sector and focus on the economic impact of each. First, let's define sectors. Sectors are distinct economic entities that react differently to different factors. These situations may arise from repeated events such as business cycles or single events such as technological advances. These characteristics can be useful for identifying the most promising sectors and determining their relative importance in an economic economy.
There are always risks
Industry risk refers to the variability in performance between industries and companies. It is measured by the variation in return on equity and profitability. This can be adjusted depending on industry to reflect the performance stock markets. For example, a company that manufactures steel is considered to be high risk because of the potential for a major earthquake in the region. An analysis of these risks can help investors identify volatile sectors.
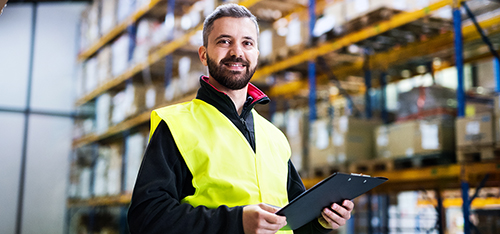
Making investments
While some investors may invest in specific companies or sectors, others might choose to invest in broader areas. Sectors can be found both in mutual funds as well as exchange-traded funds. They are safer and have lower risks. In addition, sector investing is becoming a popular investment strategy today. This article will explain how sector investing can help to find the right investments. For more information, please read on. Check out our free resource area for more information.
FAQ
Is automation necessary in manufacturing?
Not only is automation important for manufacturers, but it's also vital for service providers. It allows them provide faster and more efficient services. It also helps to reduce costs and improve productivity.
What are the responsibilities of a production planner
A production planner ensures all aspects of the project are delivered on time, within budget, and within scope. They also ensure that the product/service meets the client’s needs.
What are my options for learning more about manufacturing
Hands-on experience is the best way to learn more about manufacturing. If that is not possible, you could always read books or view educational videos.
Statistics
- (2:04) MTO is a production technique wherein products are customized according to customer specifications, and production only starts after an order is received. (oracle.com)
- In the United States, for example, manufacturing makes up 15% of the economic output. (twi-global.com)
- You can multiply the result by 100 to get the total percent of monthly overhead. (investopedia.com)
- According to the United Nations Industrial Development Organization (UNIDO), China is the top manufacturer worldwide by 2019 output, producing 28.7% of the total global manufacturing output, followed by the United States, Japan, Germany, and India.[52][53] (en.wikipedia.org)
- In 2021, an estimated 12.1 million Americans work in the manufacturing sector.6 (investopedia.com)
External Links
How To
How to Use Lean Manufacturing in the Production of Goods
Lean manufacturing (or lean manufacturing) is a style of management that aims to increase efficiency, reduce waste and improve performance through continuous improvement. It was developed in Japan during the 1970s and 1980s by Taiichi Ohno, who received the Toyota Production System (TPS) award from TPS founder Kanji Toyoda. Michael L. Watkins published the first book on lean manufacturing in 1990.
Lean manufacturing, often described as a set and practice of principles, is aimed at improving the quality, speed, cost, and efficiency of products, services, and other activities. It emphasizes the elimination and minimization of waste in the value stream. Lean manufacturing is also known as just in time (JIT), zero defect total productive maintenance(TPM), and five-star (S). Lean manufacturing emphasizes reducing non-value-added activities like inspection, rework and waiting.
Lean manufacturing improves product quality and costs. It also helps companies reach their goals quicker and decreases employee turnover. Lean manufacturing is a great way to manage the entire value chain including customers, suppliers, distributors and retailers as well as employees. Lean manufacturing practices are widespread in many industries. Toyota's philosophy, for example, is what has enabled it to be successful in electronics, automobiles, medical devices, healthcare and chemical engineering as well as paper and food.
Five fundamental principles underlie lean manufacturing.
-
Define Value: Identify the social value of your business and what sets you apart.
-
Reduce Waste - Eliminate any activity that doesn't add value along the supply chain.
-
Create Flow. Ensure that your work is uninterrupted and flows seamlessly.
-
Standardize & simplify - Make processes consistent and repeatable.
-
Build Relationships- Develop personal relationships with both internal as well as external stakeholders.
Although lean manufacturing has always been around, it is gaining popularity in recent years because of a renewed interest for the economy after 2008's global financial crisis. Many businesses have adopted lean manufacturing techniques to help them become more competitive. In fact, some economists believe that lean manufacturing will be an important factor in economic recovery.
Lean manufacturing is now becoming a common practice in the automotive industry, with many benefits. These include higher customer satisfaction, lower inventory levels, lower operating expenses, greater productivity, and improved overall safety.
It can be applied to any aspect of an organisation. This is because it ensures efficiency and effectiveness in all stages of the value chain.
There are three main types of lean manufacturing:
-
Just-in Time Manufacturing, (JIT): This kind of lean manufacturing is also commonly known as "pull-systems." JIT stands for a system where components are assembled on the spot rather than being made in advance. This strategy aims to decrease lead times, increase availability of parts and reduce inventory.
-
Zero Defects Manufacturing (ZDM),: ZDM is a system that ensures no defective units are left the manufacturing facility. If a part needs to be fixed during the assembly line, it should be repaired rather than scrapped. This is true even for finished products that only require minor repairs prior to shipping.
-
Continuous Improvement (CI),: Continuous improvement aims improve the efficiency and effectiveness of operations by continuously identifying issues and making changes to reduce waste. Continuous improvement refers to continuous improvement of processes as well people and tools.