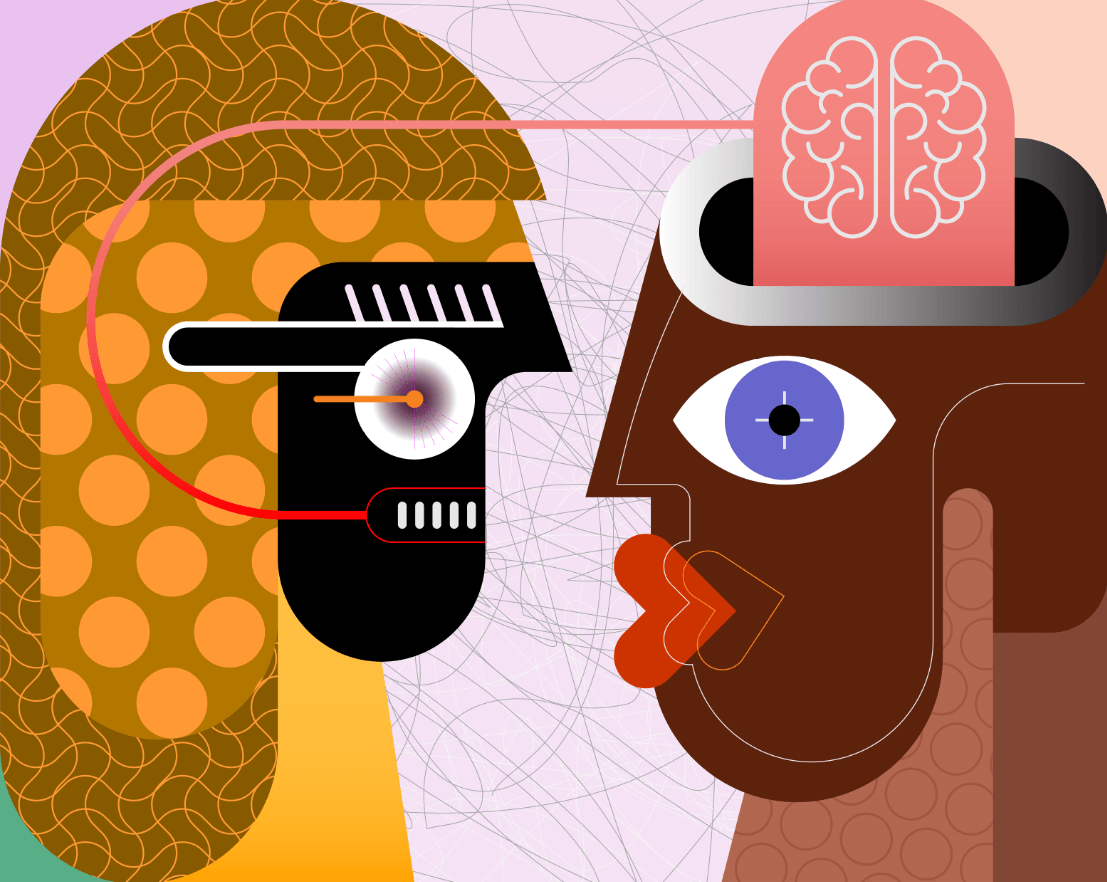
Lean manufacturing can be a cost-saving and time-saving tool. It also reduces setup and turnaround times. Lean manufacturing offers many benefits. It reduces costs and leads time, while improving customer satisfaction. These are the key benefits of lean manufacturing, which can help you grow your business. If you're still not convinced, read on for three reasons why it's the best way to make products and cut costs:
Lowers your costs
Lean manufacturing can lead to significant efficiencies. By reducing defects and rework, manufacturers can reduce their direct labor cost. This makes labor costs less motivating in decision-making. The elimination of hazardous waste is another benefit. The cost of direct labor in many industries is less than 15%. This makes outsourcing to low-cost areas more difficult. This can help lower manufacturing costs, and provide better customer service.
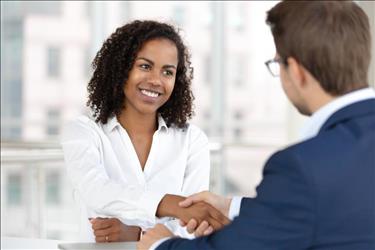
Increases lead time
Lean manufacturing offers many benefits. It can reduce waste and speed up lead times. It is a philosophy based on continuous improvement, or kaizen. It unites the talents of employees, encourages accountability and collaboration, and is a way to bring out the best in them. The process can improve lead times by as much as 20%. Lean manufacturing is about making small adjustments frequently to improve product quality.
Shortens set-up times
A significant way to reduce the amount of time required to produce a product is by reducing set-up times. The time it takes for a product to be switched from its last item to the new one is called setup time. This includes all activities related to preparation, replacement and location. These activities can either be internal, or external. While internal activities require an inactive process, such as a machine being moved or an item being positioned, external setup activities can be performed while the process is still operational.
Market time is reduced
The concept of Lean manufacturing, or the process of continuous improvement, was developed in Japan during the rebuilding period after World War II. It was developed to improve competition and reduce lead time. Companies can reduce the time required for products to reach the marketplace and meet customer demand. This will increase their profitability. This production approach can improve the efficiency of the manufacturing process and make the facility more efficient.
Improves product quality
Lean manufacturing is all about reducing waste, increasing product quality and minimising costs. It has been used by large manufacturers and smaller companies alike. It decreases lead times, costs, and labor. Learn more about how lean production can help improve your business. Here are a few of the key areas to focus on. Lean principles will reduce lead time by 90% and increase product quality. It can also reduce costs.
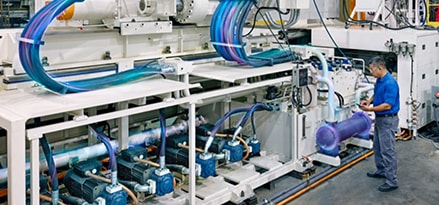
Reduces indirect labor costs
Reduced indirect labor costs is the low hanging fruit in lean manufacturing. Lean companies focus less on direct labor efficiency and look instead for ways to lower indirect labor costs. This includes eliminating management, material handling, inspection and management jobs as well as pushing production decisions to the floor. This is the same method used by Toyota and other lean manufacturing firms. This article will examine how lean manufacturing helps lower indirect labor costs.
FAQ
What are the 7 Rs of logistics.
The acronym 7R's of Logistic is an acronym that stands for seven fundamental principles of logistics management. It was published in 2004 by the International Association of Business Logisticians as part of their "Seven Principles of Logistics Management" series.
The acronym is made up of the following letters:
-
Responsible – ensure that all actions are legal and don't cause harm to anyone else.
-
Reliable - have confidence in the ability to deliver on commitments made.
-
Reasonable - make sure you use your resources well and don't waste them.
-
Realistic - consider all aspects of operations, including cost-effectiveness and environmental impact.
-
Respectful - treat people fairly and equitably.
-
Reliable - Find ways to save money and increase your productivity.
-
Recognizable: Provide customers with value-added service
What type of jobs is there in logistics
There are many types of jobs in logistics. Here are some:
-
Warehouse workers - They load and unload trucks and pallets.
-
Transport drivers - These are people who drive trucks and trailers to transport goods or perform pick-ups.
-
Freight handlers – They sort and package freight at warehouses.
-
Inventory managers – These people oversee inventory at warehouses.
-
Sales reps are people who sell products to customers.
-
Logistics coordinators - They organize and plan logistics operations.
-
Purchasing agents are those who purchase goods and services for the company.
-
Customer service representatives - They answer calls and emails from customers.
-
Ship clerks - They issue bills and process shipping orders.
-
Order fillers: They fill orders based off what has been ordered and shipped.
-
Quality control inspectors are responsible for inspecting incoming and outgoing products looking for defects.
-
Others - There are many types of jobs in logistics such as transport supervisors and cargo specialists.
Do we need to know about Manufacturing Processes before learning about Logistics?
No. It doesn't matter if you don't know anything about manufacturing before you learn about logistics. Understanding the manufacturing process will allow you to better understand logistics.
What are the main products of logistics?
Logistics are the activities involved in moving goods from point A to point B.
They include all aspects associated with transport including packaging, loading transporting, unloading storage, warehousing inventory management customer service, distribution returns and recycling.
Logisticians make sure that the right product arrives at the right place at the correct time and in safe conditions. Logisticians assist companies in managing their supply chains by providing information such as demand forecasts, stock levels and production schedules.
They monitor shipments in transit, ensure quality standards, manage inventories, replenish orders, coordinate with suppliers and other vendors, and offer support services for sales, marketing, and customer service.
What are the 4 types manufacturing?
Manufacturing refers the process of turning raw materials into useful products with machines and processes. It can involve many activities like designing, manufacturing, testing packaging, shipping, selling and servicing.
How can manufacturing prevent production bottlenecks?
Production bottlenecks can be avoided by ensuring that processes are running smoothly during the entire production process, starting with the receipt of an order and ending when the product ships.
This includes both quality control and capacity planning.
The best way to do this is to use continuous improvement techniques such as Six Sigma.
Six Sigma can be used to improve the quality and decrease waste in all areas of your company.
It seeks to eliminate variation and create consistency in your work.
Statistics
- (2:04) MTO is a production technique wherein products are customized according to customer specifications, and production only starts after an order is received. (oracle.com)
- Many factories witnessed a 30% increase in output due to the shift to electric motors. (en.wikipedia.org)
- You can multiply the result by 100 to get the total percent of monthly overhead. (investopedia.com)
- Job #1 is delivering the ordered product according to specifications: color, size, brand, and quantity. (netsuite.com)
- In the United States, for example, manufacturing makes up 15% of the economic output. (twi-global.com)
External Links
How To
How to use 5S to increase Productivity in Manufacturing
5S stands for "Sort", 'Set In Order", 'Standardize', & Separate>. The 5S methodology was developed at Toyota Motor Corporation in 1954. It improves the work environment and helps companies to achieve greater efficiency.
This method has the basic goal of standardizing production processes to make them repeatable. Cleaning, sorting and packing are all done daily. Because workers know what they can expect, this helps them perform their jobs more efficiently.
There are five steps that you need to follow in order to implement 5S. Each step requires a different action to increase efficiency. You can make it easy for people to find things later by sorting them. When items are ordered, they are put together. Once you have separated your inventory into groups and organized them, you will store these groups in easily accessible containers. Finally, label all containers correctly.
Employees will need to be more critical about their work. Employees must be able to see why they do what they do and find a way to achieve them without having to rely on their old methods. In order to use the 5S system effectively, they must be able to learn new skills.
The 5S method increases efficiency and morale among employees. They will feel motivated to strive for higher levels of efficiency once they start to see results.