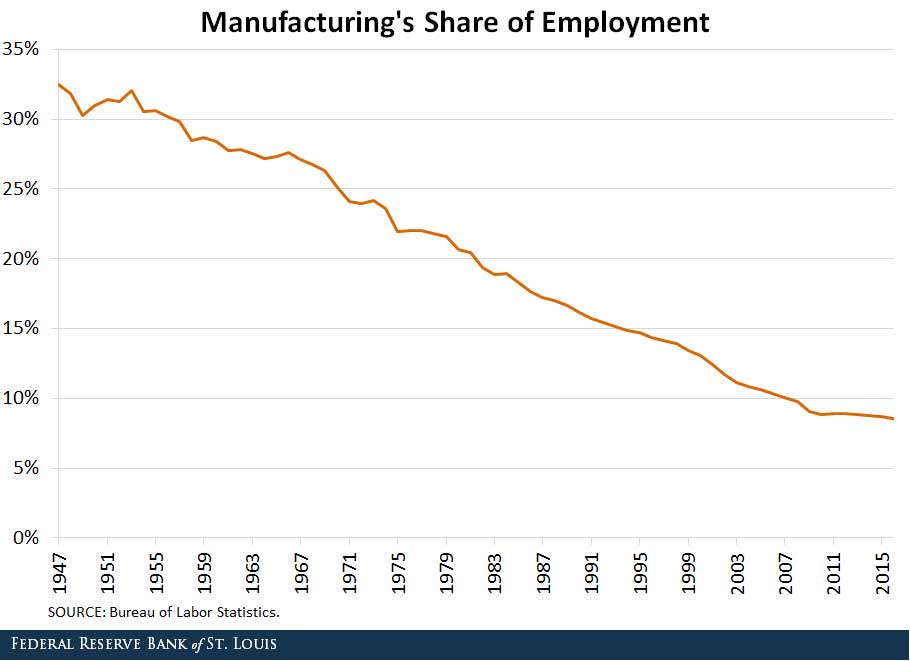
Lean training can reduce waste and streamline processes. Lean training improves team efficiency and helps to produce more product in a shorter time. However, it is important that everyone in an organization understands the benefits of lean. It is possible to do this with a customized training program that meets the individual needs of each team member.
Lean training is often delivered in classrooms with a hands-on approach, combining classroom instruction and intensive hands-on experience. On average, trainees are required to participate in the course for four to eight hours per week. Participants are trained to make suggestions and to improve their performance. By using tools like value stream mapping and Plan-Do-Check-Act (PDCA), participants can improve the performance of their organization's processes.
Many companies opt to have their lean training done in-house, or hire professionals. For example, Clemson University offers four different programs for their employees.
Lean training is essential to your organization's success. In fact, more companies are adopting the methodology. You should look for a training program that covers all of the key elements of lean.
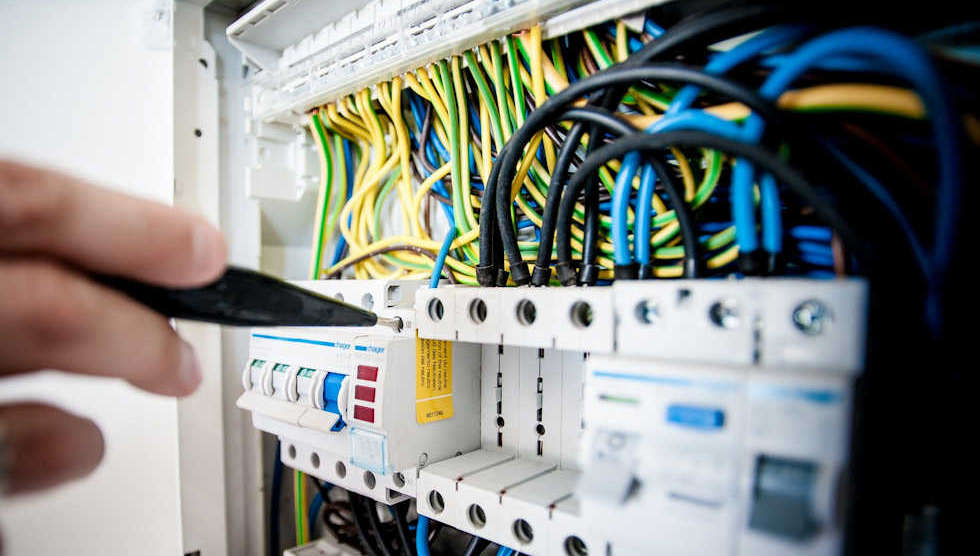
An introduction to lean should be the first step in your training. This workshop will cover the history and principles of lean as well as the basics. You'll also learn how to use lean tools like value stream mapping and kanban. You will also learn how you can improve your customer experience.
After mastering the basics of Lean Thinking, you can move onto the Lean Thinking unit. You'll learn about continuous flow, error-proofing and value stream mapping. All of these methods are essential to identifying and reducing waste in your business.
Afterwards you'll be able to learn about Plan-Do-Check-Act. PDCA (Plan-Do-Check-Act) is a Lean improvement method that's used by many practitioners. The course will also help you understand the root causes.
Learn how to create a lean-action plan. It outlines your current state, as well as any improvements you wish to make. A certificate will be issued to you for your accomplishments after completion. To get your Lean Management Certification, you will need to pass the multiple-choice exam.
After completing the program you will be able to apply what was learned to your own job. No matter whether you are a manager, supervisor or technician, this program will teach you how to manage change effectively and lead your team through it. Positive results will be yours.
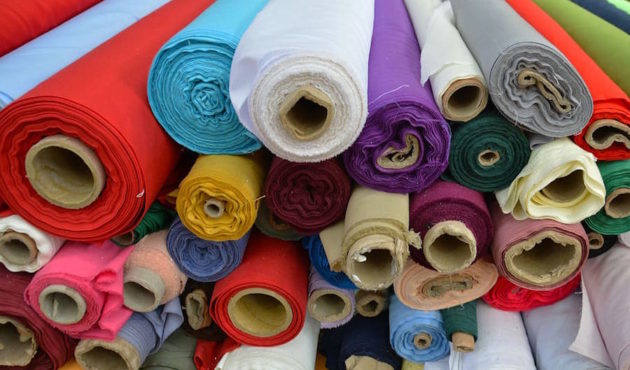
Finally, you can earn your Green Belt certificate. The Lean training program at Virginia University Medical Center (VUMC) is managed by April Saunders. Her 12+ years of experience in the manufacturing industry means that she can teach Lean to her students.
Lean Fundamentals can be accessed in several languages. Participants are taught how Lean concepts can be quickly implemented in their workplaces. There is a high likelihood that this class will have an immediate effect on your organization.
Whether you're interested in implementing lean in your organization, or you simply want to brush up on your skills, this workshop is a great start.
FAQ
What is the responsibility for a logistics manager
Logistics managers make sure all goods are delivered on schedule and without damage. This is done by using his/her experience and knowledge of the company's products. He/she also needs to ensure adequate stock to meet demand.
What skills is required for a production planner?
Being a production planner is not easy. You need to be organized and flexible. Communication skills are essential to ensure that you can communicate effectively with clients, colleagues, and customers.
What are the requirements to start a logistics business?
To run a successful logistics company, you need a lot knowledge and skills. For clients and suppliers to be successful, you need to have excellent communication skills. You must be able analyze data and draw out conclusions. You must be able manage stress and pressure under pressure. You must be creative and innovative to develop new ideas to improve efficiency. You must be a strong leader to motivate others and direct them to achieve organizational goals.
You should also be organized and efficient to meet tight deadlines.
What is the difference between manufacturing and logistics
Manufacturing is the process of creating goods from raw materials by using machines and processes. Logistics includes all aspects related to supply chain management, such as procurement, distribution planning, inventory control and transportation. As a broad term, manufacturing and logistics often refer to both the creation and delivery of products.
How can manufacturing avoid production bottlenecks
Avoiding production bottlenecks is as simple as keeping all processes running smoothly, from the time an order is received until the product ships.
This includes both quality control and capacity planning.
The best way to do this is to use continuous improvement techniques such as Six Sigma.
Six Sigma is a management system used to improve quality and reduce waste in every aspect of your organization.
It seeks to eliminate variation and create consistency in your work.
Statistics
- It's estimated that 10.8% of the U.S. GDP in 2020 was contributed to manufacturing. (investopedia.com)
- According to a Statista study, U.S. businesses spent $1.63 trillion on logistics in 2019, moving goods from origin to end user through various supply chain network segments. (netsuite.com)
- Many factories witnessed a 30% increase in output due to the shift to electric motors. (en.wikipedia.org)
- In 2021, an estimated 12.1 million Americans work in the manufacturing sector.6 (investopedia.com)
- In the United States, for example, manufacturing makes up 15% of the economic output. (twi-global.com)
External Links
How To
How to Use Lean Manufacturing in the Production of Goods
Lean manufacturing is an approach to management that aims for efficiency and waste reduction. It was developed by Taiichi Okono in Japan, during the 1970s & 1980s. TPS founder Kanji Takoda awarded him the Toyota Production System Award (TPS). Michael L. Watkins published the first book on lean manufacturing in 1990.
Lean manufacturing can be described as a set or principles that are used to improve quality, speed and cost of products or services. It emphasizes the elimination of defects and waste throughout the value stream. Lean manufacturing can be described as just-in–time (JIT), total productive maintenance, zero defect (TPM), or even 5S. Lean manufacturing focuses on eliminating non-value-added activities such as rework, inspection, and waiting.
Lean manufacturing improves product quality and costs. It also helps companies reach their goals quicker and decreases employee turnover. Lean manufacturing has been deemed one of the best ways to manage the entire value-chain, including customers, distributors as well retailers and employees. Lean manufacturing practices are widespread in many industries. Toyota's philosophy, for example, is what has enabled it to be successful in electronics, automobiles, medical devices, healthcare and chemical engineering as well as paper and food.
Five principles are the basis of lean manufacturing:
-
Define value - Find out what your business contributes to society, and what makes it different from other competitors.
-
Reduce waste - Get rid of any activity that does not add value to the supply chain.
-
Create Flow – Ensure that work flows smoothly throughout the process.
-
Standardize & simplify - Make processes consistent and repeatable.
-
Build relationships - Develop and maintain personal relationships with both your internal and external stakeholders.
Lean manufacturing, although not new, has seen renewed interest in the economic sector since 2008. To increase their competitiveness, many businesses have turned to lean manufacturing. Many economists believe lean manufacturing will play a major role in economic recovery.
Lean manufacturing is now becoming a common practice in the automotive industry, with many benefits. These include better customer satisfaction and lower inventory levels. They also result in lower operating costs.
It can be applied to any aspect of an organisation. It is especially useful for the production aspect of an organization, as it ensures that every step in the value chain is efficient and effective.
There are three types of lean manufacturing.
-
Just-in Time Manufacturing: This lean manufacturing method is commonly called "pull systems." JIT is a method in which components are assembled right at the moment of use, rather than being manufactured ahead of time. This approach is designed to reduce lead times and increase the availability of components. It also reduces inventory.
-
Zero Defects Manufacturing (ZDM),: ZDM is a system that ensures no defective units are left the manufacturing facility. You should repair any part that needs to be repaired during an assembly line. This also applies to finished products that need minor repairs before being shipped.
-
Continuous Improvement (CI),: Continuous improvement aims improve the efficiency and effectiveness of operations by continuously identifying issues and making changes to reduce waste. Continuous Improvement (CI) involves continuous improvement in processes, people, tools, and infrastructure.