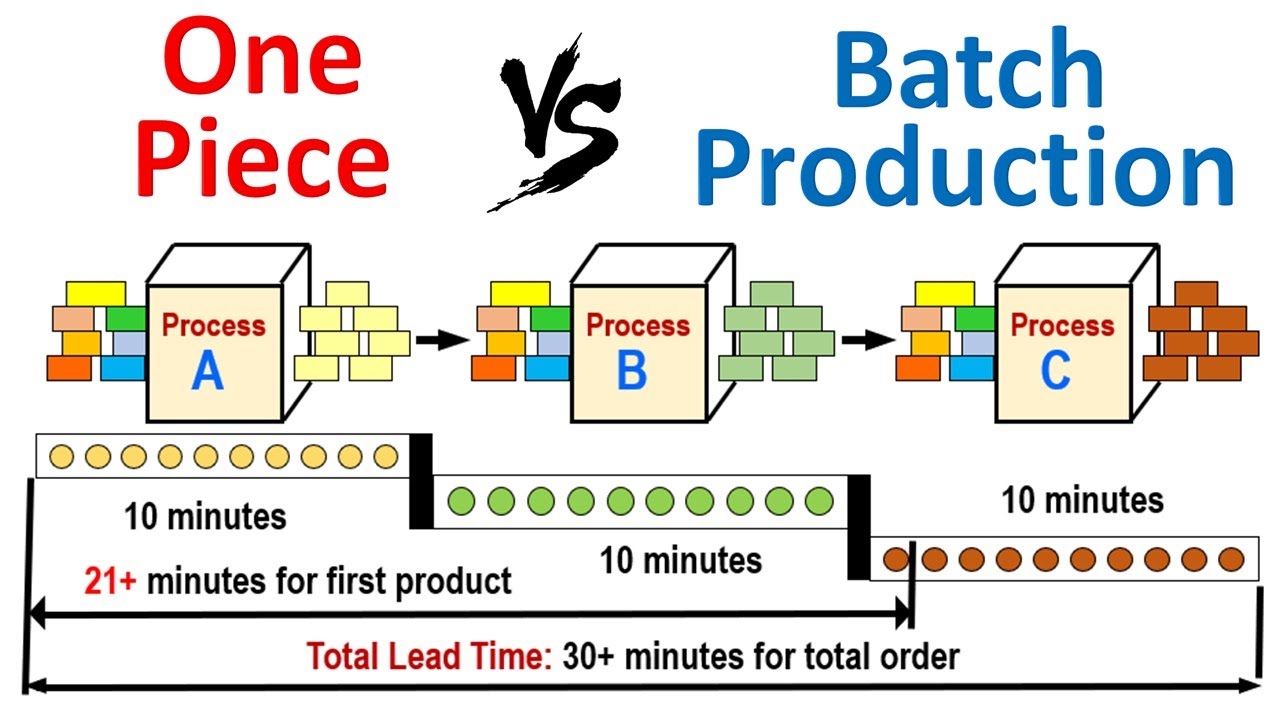
Purchasing Managers, also known as Materials Managers, are responsible for sourcing and coordinating all purchasing activities. They work with vendors, suppliers, and other purchasing agents. They need to know how to improve the company’s purchasing process. They must also know how to negotiate the best deal for the company.
Purchaser managers must also keep accurate and current purchasing records. They analyze customer needs, analyze financial reports, evaluate vendor capabilities, and evaluate price trends. They also coordinate purchasing activities with other departments. If the company requires supplies from foreign markets, they may have to work overtime.
They coordinate and manage logistics and inventory. They also determine the best purchasing method and make sure that all purchased items meet company quality standards. They also manage budgets, and collaborate with their staff in order to ensure that purchases are made for the best price. They are also able to negotiate contracts and find the best suppliers.
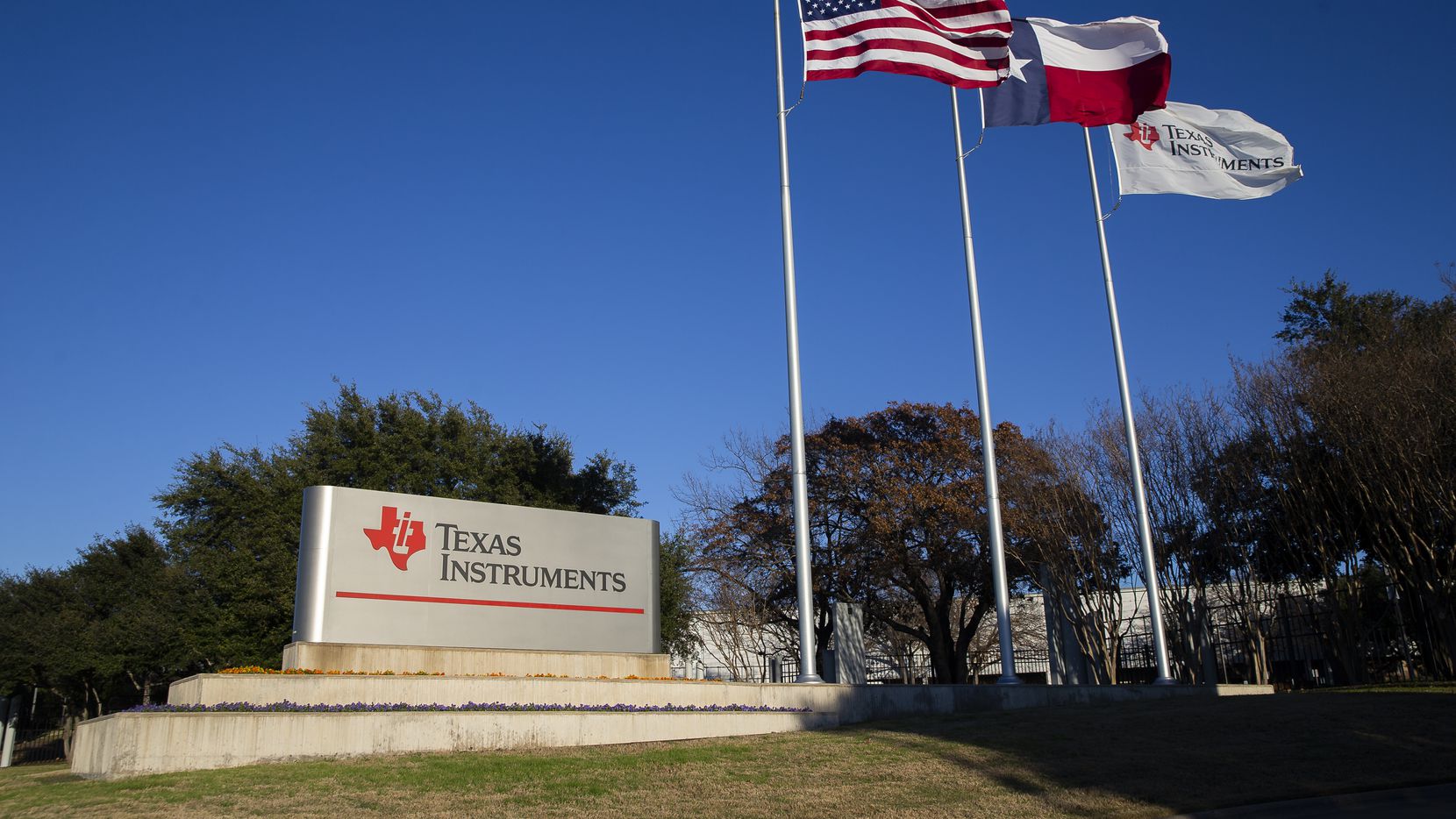
The time schedules of all purchasing staff are also monitored and managed by the Purchasing Managers. They evaluate the quality, speed, and cost of all purchased goods. They also contact sellers and suppliers and visit their distribution centers. They ensure that all suppliers adhere to the contract terms. They might also need to address disciplinary issues or team building.
Excellent communication skills and analytical abilities are essential for purchasing managers. They also need to be strategic thinkers. They need to be able analyse the effects of various products on the company. They must also be able to manage suppliers and their relationships. They should also have the ability to make business decisions and to increase sales. They must be able deal with complicated purchases. They need to be able analyze potential vendors and choose the best one for their company.
Most purchasing managers have to have a bachelor's degree in business or a related field. It is also helpful if they have experience in inventory management and supply chain management. They must be proficient in Microsoft Office and other computer software programs.
The best purchasing manager should be able to find the best deals and negotiate the most favorable contracts. They should also have the ability to coordinate all purchasing activities. Manage inventories and track vendor and supplier performance. They should also be capable of managing a team consisting of purchasing agents.
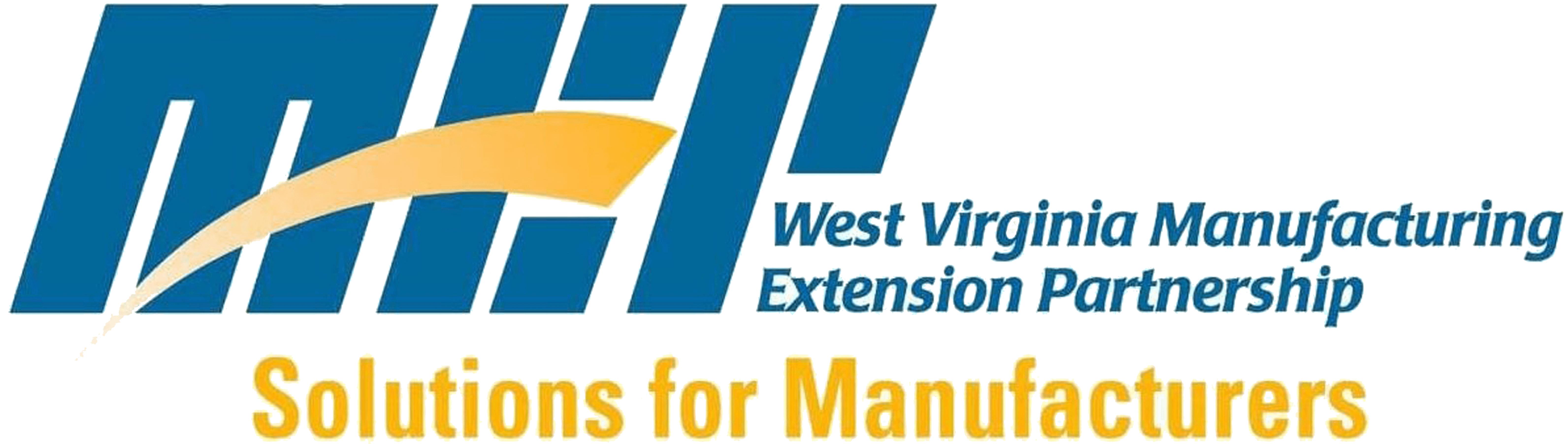
The purchase manager job description should also be able to mention how purchasing is essential to the company's success. It should also include how vital it is for the company that they stay ahead of their competitors. It should also describe how the company values work-life balance. The call to action should be included to encourage applicants to apply.
Sometimes, the Purchasing Manager may be required to work overtime in order to purchase equipment and materials for an international marketplace. They may also have to deal with vendors and sellers and attend trade shows.
FAQ
What is the best way to learn about manufacturing?
The best way to learn about manufacturing is through hands-on experience. You can read books, or watch instructional videos if you don't have the opportunity to do so.
Why automate your warehouse
Modern warehouses are increasingly dependent on automation. E-commerce has increased the demand for quicker delivery times and more efficient processes.
Warehouses should be able adapt quickly to new needs. Technology investment is necessary to enable warehouses to respond quickly to changing demands. The benefits of automating warehouses are numerous. These are some of the benefits that automation can bring to warehouses:
-
Increases throughput/productivity
-
Reduces errors
-
Accuracy is improved
-
Boosts safety
-
Eliminates bottlenecks
-
Companies can scale more easily
-
Workers are more productive
-
The warehouse can be viewed from all angles.
-
Enhances customer experience
-
Improves employee satisfaction
-
Reduces downtime and improves uptime
-
You can be sure that high-quality products will arrive on time
-
Removes human error
-
Helps ensure compliance with regulations
What is the role of a production manager?
Production planners ensure all aspects of the project are delivered within time and budget. They ensure that the product or service is of high quality and meets client requirements.
What skills does a production planner need?
A production planner must be organized, flexible, and able multitask to succeed. Effective communication with clients and colleagues is essential.
Statistics
- It's estimated that 10.8% of the U.S. GDP in 2020 was contributed to manufacturing. (investopedia.com)
- Many factories witnessed a 30% increase in output due to the shift to electric motors. (en.wikipedia.org)
- Job #1 is delivering the ordered product according to specifications: color, size, brand, and quantity. (netsuite.com)
- According to a Statista study, U.S. businesses spent $1.63 trillion on logistics in 2019, moving goods from origin to end user through various supply chain network segments. (netsuite.com)
- In the United States, for example, manufacturing makes up 15% of the economic output. (twi-global.com)
External Links
How To
How to use Lean Manufacturing in the production of goods
Lean manufacturing is a management style that aims to increase efficiency and reduce waste through continuous improvement. It was developed by Taiichi Okono in Japan, during the 1970s & 1980s. TPS founder Kanji Takoda awarded him the Toyota Production System Award (TPS). Michael L. Watkins published the book "The Machine That Changed the World", which was the first to be published about lean manufacturing.
Lean manufacturing, often described as a set and practice of principles, is aimed at improving the quality, speed, cost, and efficiency of products, services, and other activities. It emphasizes eliminating waste and defects throughout the value stream. Lean manufacturing can be described as just-in–time (JIT), total productive maintenance, zero defect (TPM), or even 5S. Lean manufacturing emphasizes reducing non-value-added activities like inspection, rework and waiting.
Lean manufacturing can help companies improve their product quality and reduce costs. Additionally, it helps them achieve their goals more quickly and reduces employee turnover. Lean Manufacturing is one of the most efficient ways to manage the entire value chains, including suppliers and customers as well distributors and retailers. Many industries worldwide use lean manufacturing. Toyota's philosophy is a great example of this. It has helped to create success in automobiles as well electronics, appliances and healthcare.
Five principles are the basis of lean manufacturing:
-
Define Value- Identify the added value your company brings to society. What makes you stand out from your competitors?
-
Reduce waste - Get rid of any activity that does not add value to the supply chain.
-
Create Flow - Make sure work runs smoothly without interruptions.
-
Standardize & simplify - Make processes consistent and repeatable.
-
Building Relationships – Establish personal relationships with both external and internal stakeholders.
Lean manufacturing isn’t new, but it has seen a renewed interest since 2008 due to the global financial crisis. Many businesses have adopted lean manufacturing techniques to help them become more competitive. Economists think that lean manufacturing is a crucial factor in economic recovery.
Lean manufacturing is becoming a popular practice in automotive. It has many advantages. These include higher customer satisfaction levels, reduced inventory levels as well as lower operating costs.
Lean manufacturing can be applied to almost every aspect of an organization. This is because it ensures efficiency and effectiveness in all stages of the value chain.
There are three types principally of lean manufacturing:
-
Just-in-Time Manufacturing (JIT): This type of lean manufacturing is commonly referred to as "pull systems." JIT is a method in which components are assembled right at the moment of use, rather than being manufactured ahead of time. This strategy aims to decrease lead times, increase availability of parts and reduce inventory.
-
Zero Defects Manufacturing, (ZDM): ZDM is focused on ensuring that no defective products leave the manufacturing facility. If a part needs to be fixed during the assembly line, it should be repaired rather than scrapped. This applies to finished products, which may need minor repairs before they are shipped.
-
Continuous Improvement (CI),: Continuous improvement aims improve the efficiency and effectiveness of operations by continuously identifying issues and making changes to reduce waste. It involves continuous improvement of processes, people, and tools.