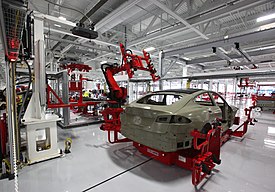
As Mechanical Technical Specialists, they analyze process data to provide troubleshooting assistance to maintenance staff. They assist with short-term outage planning and system improvement.
This field is increasing in popularity. A professional mechanic must be able to communicate with customers and demonstrate his or her knowledge. For this job, you will need to be able to communicate in technical language, manage time well, and work well with others.
These engineers also have the technical skills needed to work in sales and marketing, and have the ability to manage and troubleshoot problems. As demand grows for more efficient machinery, so does the expectation of these professionals to deliver high-quality work.
This field requires a high education. In order to achieve this goal, mechanical engineers must learn about the science behind the design and production of products. The field of heat engineer studies the heat flow through structures. Heat engineering also involves developing equipment for transportation and air conditioning.
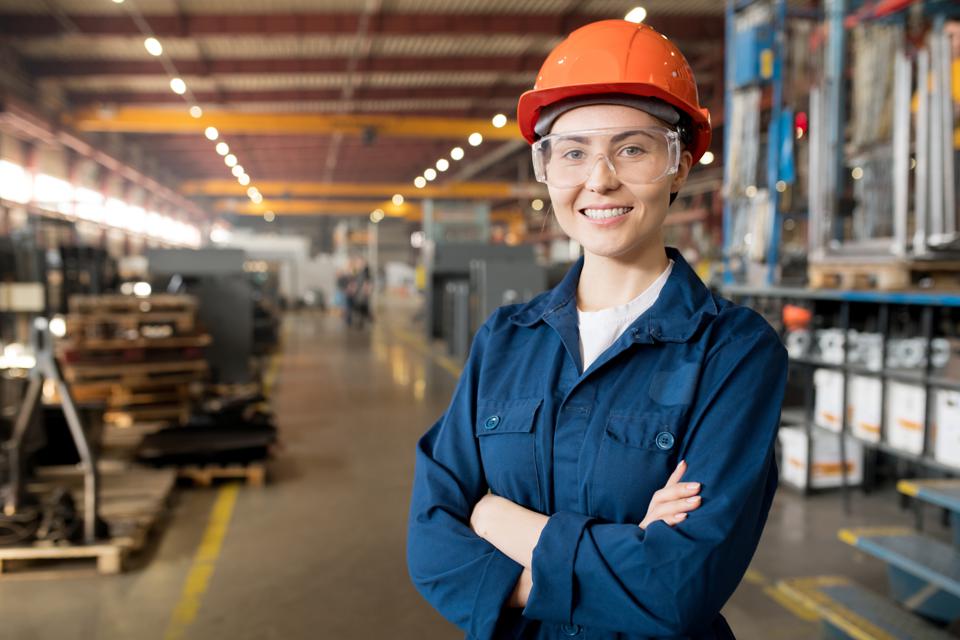
Mechanical engineers have been at the forefront technology for a long time. The advent of computer-aided designing has enabled mechanical engineers to create new designs, materials, and components for smaller and more complex machines. Nanotechnology has made it possible to design materials at the smallest scale. Composites are materials that combine multiple materials to create a single product.
These professionals use rationalized approaches to design and manufacture. One such approach is value engineering. This aims at making the most of available resources. Operations research is another approach.
The mechanic trade is always in demand and many want to create commercial partnerships with foreigners. They should be able communicate well in English to get a job overseas.
It is important to have a good vocabulary. You can improve your English as a mechanic by attending industry events or reading specialized magazines in English. A course online can be taken to enhance their skills.
Apart from these skills mechanics should be able and able to manage their own time. The minimum experience required to become a mechanical technician is two years. The ability to use diagnostic testing software, as well as exceptional analytical and critical thinking skills is essential for mechanics.
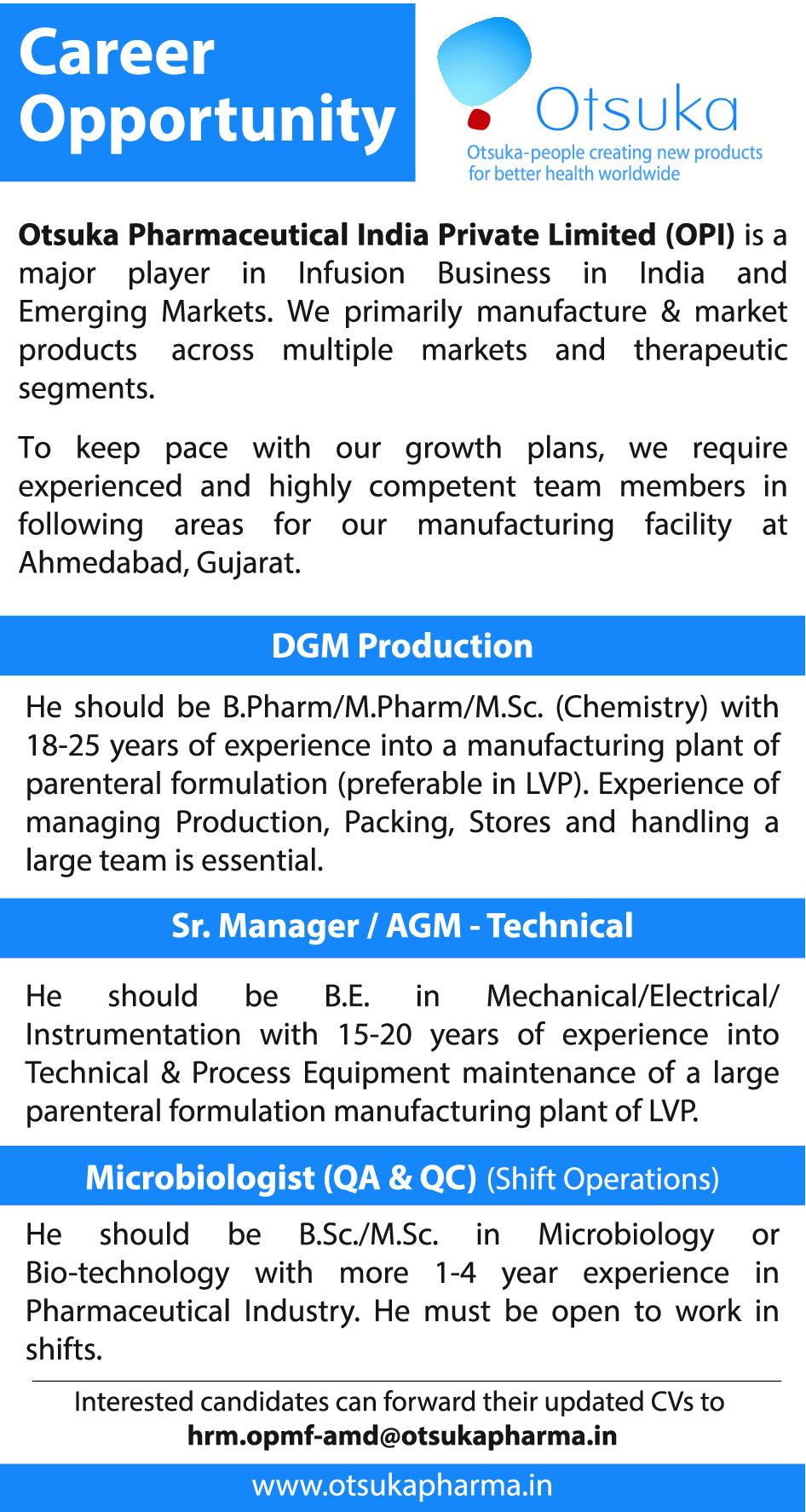
This field requires a solid understanding of computers and computer-aided design. A degree in mechanical engineering technology is an excellent option.
As a Mechanical Technical Specialist, crafts can use them to manage their day, analyze data, and give technical leadership to their employees. They are also able to solve problems that recur.
Mechanical engineers work closely with civil engineers, electrical engineers, and chemical engineers in order to improve the performance of vehicles, equipment and systems. They also contribute to research, design, or construction. Many mechanical engineers work full time or as an adjunct to their day job.
FAQ
What are the 4 types manufacturing?
Manufacturing refers the process of turning raw materials into useful products with machines and processes. Manufacturing can include many activities such as designing and building, testing, packaging shipping, selling, servicing, and other related activities.
How can manufacturing efficiency be improved?
The first step is to determine the key factors that impact production time. Then we need to find ways to improve these factors. If you aren't sure where to begin, think about the factors that have the greatest impact on production time. Once you have identified them, it is time to identify solutions.
What are manufacturing and logistic?
Manufacturing refers the process of producing goods from raw materials through machines and processes. Logistics includes all aspects related to supply chain management, such as procurement, distribution planning, inventory control and transportation. Manufacturing and logistics are often considered together as a broader term that encompasses both the process of creating products and delivering them to customers.
What is the difference between Production Planning and Scheduling?
Production Planning (PP), or production planning, is the process by which you determine what products are needed at any given time. This is accomplished by forecasting the demand and identifying production resources.
Scheduling is the process of assigning specific dates to tasks so they can be completed within the specified timeframe.
What is the best way to learn about manufacturing?
Experience is the best way for you to learn about manufacturing. But if that is not possible you can always read books and watch educational videos.
What is the difference between a production planner and a project manager?
The main difference between a production planner and a project manager is that a project manager is usually the person who plans and organizes the entire project, whereas a production planner is mainly involved in the planning stage of the project.
Statistics
- According to the United Nations Industrial Development Organization (UNIDO), China is the top manufacturer worldwide by 2019 output, producing 28.7% of the total global manufacturing output, followed by the United States, Japan, Germany, and India.[52][53] (en.wikipedia.org)
- Many factories witnessed a 30% increase in output due to the shift to electric motors. (en.wikipedia.org)
- In the United States, for example, manufacturing makes up 15% of the economic output. (twi-global.com)
- [54][55] These are the top 50 countries by the total value of manufacturing output in US dollars for its noted year according to World Bank.[56] (en.wikipedia.org)
- According to a Statista study, U.S. businesses spent $1.63 trillion on logistics in 2019, moving goods from origin to end user through various supply chain network segments. (netsuite.com)
External Links
How To
How to use Lean Manufacturing in the production of goods
Lean manufacturing is a management style that aims to increase efficiency and reduce waste through continuous improvement. It was developed in Japan during the 1970s and 1980s by Taiichi Ohno, who received the Toyota Production System (TPS) award from TPS founder Kanji Toyoda. Michael L. Watkins published the original book on lean manufacturing, "The Machine That Changed the World," in 1990.
Lean manufacturing can be described as a set or principles that are used to improve quality, speed and cost of products or services. It emphasizes eliminating waste and defects throughout the value stream. Lean manufacturing can be described as just-in–time (JIT), total productive maintenance, zero defect (TPM), or even 5S. Lean manufacturing eliminates non-value-added tasks like inspection, rework, waiting.
Lean manufacturing not only improves product quality but also reduces costs. Companies can also achieve their goals faster by reducing employee turnover. Lean manufacturing is a great way to manage the entire value chain including customers, suppliers, distributors and retailers as well as employees. Lean manufacturing can be found in many industries. Toyota's philosophy is the foundation of its success in automotives, electronics and appliances, healthcare, chemical engineers, aerospace, paper and food, among other industries.
Five basic principles of Lean Manufacturing are included in lean manufacturing
-
Define Value- Identify the added value your company brings to society. What makes you stand out from your competitors?
-
Reduce waste - Stop any activity that isn't adding value to the supply chains.
-
Create Flow: Ensure that the work process flows without interruptions.
-
Standardize and Simplify – Make processes as consistent, repeatable, and as simple as possible.
-
Build Relationships - Establish personal relationships with both internal and external stakeholders.
Lean manufacturing is not a new concept, but it has been gaining popularity over the last few years due to a renewed interest in the economy following the global financial crisis of 2008. Many businesses have adopted lean production techniques to make them more competitive. In fact, some economists believe that lean manufacturing will be an important factor in economic recovery.
Lean manufacturing is becoming a popular practice in automotive. It has many advantages. These benefits include increased customer satisfaction, reduced inventory levels and lower operating costs.
The principles of lean manufacturing can be applied in almost any area of an organization. It is especially useful for the production aspect of an organization, as it ensures that every step in the value chain is efficient and effective.
There are three main types:
-
Just-in Time Manufacturing, (JIT): This kind of lean manufacturing is also commonly known as "pull-systems." JIT stands for a system where components are assembled on the spot rather than being made in advance. This approach is designed to reduce lead times and increase the availability of components. It also reduces inventory.
-
Zero Defects Manufacturing: ZDM ensures that no defective units leave the manufacturing plant. You should repair any part that needs to be repaired during an assembly line. This is true even for finished products that only require minor repairs prior to shipping.
-
Continuous Improvement (CI): CI aims to improve the efficiency of operations by continuously identifying problems and making changes in order to eliminate or minimize waste. Continuous improvement refers to continuous improvement of processes as well people and tools.