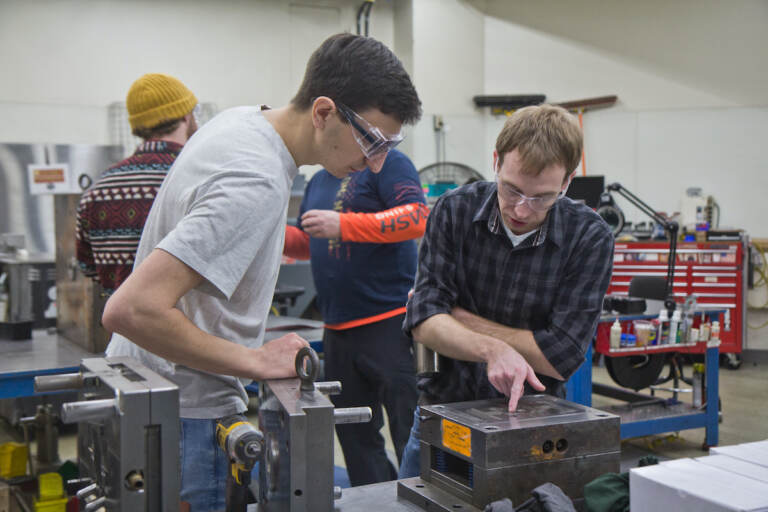
Advanced manufacturing is the application of new technology to improve products and processes. The technology used to achieve this can be classified as "advanced," "innovative," or "cutting edge." As the number of companies that use advanced manufacturing increases, these industries are increasingly integrating new and innovative technologies into their manufacturing processes. These are just a few examples of advanced manufacturing. These are the most popular technologies in advanced manufacturing.
Continuous manufacturing
Continuous manufacturing dates back as far as the 1700s. It was used to produce pigiron in blast furnaces. Since then, the concept has been adopted by many industries, including the automotive and food, oil and refinery, chemicals and pulp and and paper industries. Continuous manufacturing has gained a lot of traction in today's biopharmaceutical business, and is being sought after by top CMOs, as well big pharma players.
In a recent commentary, FDA and its collaborators discussed the benefits to continuous manufacturing when producing therapeutic proteins. This legislation would establish national standards and allow companies to create them. The industry's goal is to improve the process for creating and using medical devices. Companies would be encouraged to use continuous manufacturing for product development and improvement. However, continuous manufacturing must be safe.
Automated processes
Automating advanced manufacturing processes is a great way to increase efficiency and reduce costs. Automation is often the best method to make the most efficient use of floor space while also increasing productivity. In order to reduce costs and increase production efficiency, manufacturers can collect data and leverage automation technologies. Process industry automation also saves time and money. While the initial investment can be high, it will eventually increase the bottom line of a manufacturing company.
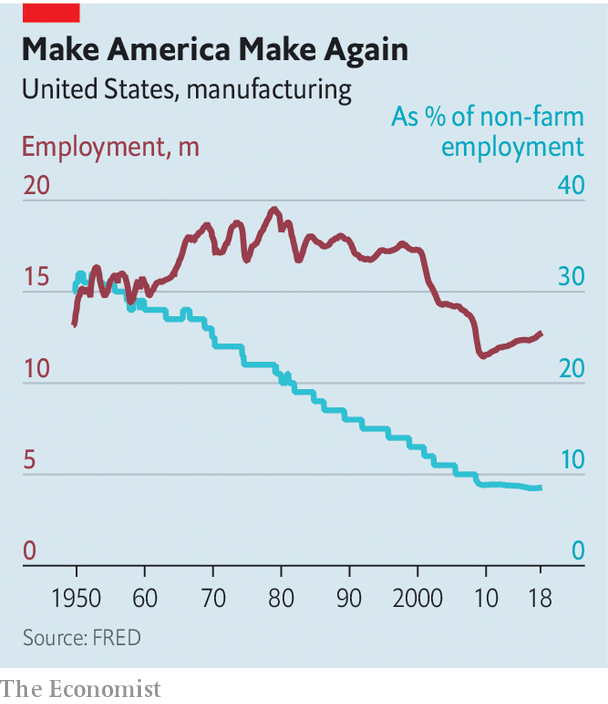
Companies are now combining automated manufacturing processes with advanced manufacturing processes. Audi is one example. They use automated welding and bonding processes to reduce their production time while also saving energy and weight. They also use advanced manufacturing techniques such as regenerative-braking conveyor systems. 3D printing represents the greatest advancement in manufacturing. It has been around for a while, but it is only now that it is mainstream. Why is 3D printing so appealing for manufacturers?
Internet of Things
The IIoT revolution transforms manufacturing by using sensors to monitor machines as well as their processes. These sensors collect data from various parts of the manufacturing process, and then feed it into a central station. This data can then be analyzed to help optimize processes and eliminate waste. Advanced manufacturers already use IIoT sensors for monitoring production and optimizing it. The IIoT sensors are the industrial version connected key fobs.
IIoT deployment requires a comprehensive roadmap, and the ability to develop capabilities to roll out use case in an effective and scalable fashion. The following road map from an automaker shows three waves of deployment:
Cost-effectiveness
Advanced manufacturing costs are not always comparable to conventional production systems. The cost-benefit analysis alone is not sufficient for evaluating economic benefits. A holistic approach that considers both the costs as well as the benefits of technology may be able to identify new opportunities and expedite decision-making. Munker and Schroer have developed a cost-benefit model that addresses key issues in AMS implementation.
Information technology advancements are quickly changing the face of manufacturing. The production systems are becoming more intelligent and networked. Cost pressure is increasing productivity and a company’s ability to respond quickly to customer requirements. The adoption of advanced manufacturing technologies is likely to accelerate the implementation and cost effectiveness of new technologies. Further, the adoption of such technologies will likely accelerate as the industry continues to digitize.
Human error reduction
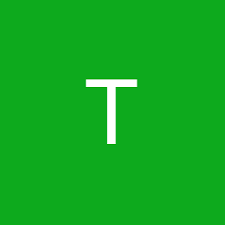
Humans make mistakes. However, the process that is used to make a product usually protects it. Employees can make mistakes if they don't follow instructions or fail to understand the written process. When they make drugs, pharmaceutical laboratories for example must follow certain procedures. In some cases, an employee may think they have mastered a process and understand the exact amounts of ingredients to use, so they proceed to make the mixture without consulting the written procedure.
A way to reduce human errors is to communicate effectively between junior and senior employees. People will make mistakes if they are treated badly. Managers must not punish employees for asking questions. Employees should feel at ease asking questions. If they don't feel comfortable asking questions they won't be inclined to take corrective action. Respect senior employees' opinions and communicate with them in a friendly and professional manner.
FAQ
What is the responsibility of a manufacturing manager?
A manufacturing manager must make sure that all manufacturing processes run smoothly and effectively. They must also be alert to any potential problems and take appropriate action.
They should also be able and comfortable communicating with other departments like sales and marketing.
They should also be aware of the latest trends in their industry and be able to use this information to help improve productivity and efficiency.
Can some manufacturing processes be automated?
Yes! Yes. The Egyptians invented the wheel thousands of years ago. Nowadays, we use robots for assembly lines.
There are many applications for robotics in manufacturing today. These include:
-
Robots for assembly line
-
Robot welding
-
Robot painting
-
Robotics inspection
-
Robots create products
Automation could also be used to improve manufacturing. 3D printing is a way to make custom products quickly and without waiting weeks or months for them to be manufactured.
What does manufacturing industry mean?
Manufacturing Industries are companies that manufacture products. Consumers are people who purchase these goods. These companies use a variety processes such as distribution, retailing and management to accomplish their purpose. These companies produce goods using raw materials and other equipment. This includes all types and varieties of manufactured goods, such as food items, clothings, building supplies, furnitures, toys, electronics tools, machinery vehicles, pharmaceuticals medical devices, chemicals, among others.
How can manufacturing avoid production bottlenecks
Production bottlenecks can be avoided by ensuring that processes are running smoothly during the entire production process, starting with the receipt of an order and ending when the product ships.
This includes planning to meet capacity requirements and quality control.
Continuous improvement techniques such Six Sigma are the best method to accomplish this.
Six Sigma is a management method that helps to improve quality and reduce waste.
It is focused on creating consistency and eliminating variation in your work.
Statistics
- Job #1 is delivering the ordered product according to specifications: color, size, brand, and quantity. (netsuite.com)
- According to a Statista study, U.S. businesses spent $1.63 trillion on logistics in 2019, moving goods from origin to end user through various supply chain network segments. (netsuite.com)
- (2:04) MTO is a production technique wherein products are customized according to customer specifications, and production only starts after an order is received. (oracle.com)
- According to the United Nations Industrial Development Organization (UNIDO), China is the top manufacturer worldwide by 2019 output, producing 28.7% of the total global manufacturing output, followed by the United States, Japan, Germany, and India.[52][53] (en.wikipedia.org)
- [54][55] These are the top 50 countries by the total value of manufacturing output in US dollars for its noted year according to World Bank.[56] (en.wikipedia.org)
External Links
How To
How to use lean manufacturing in the production of goods
Lean manufacturing is a management system that aims at increasing efficiency and reducing waste. It was developed in Japan between 1970 and 1980 by Taiichi Ohno. TPS founder Kanji Tyoda gave him the Toyota Production System, or TPS award. The first book published on lean manufacturing was titled "The Machine That Changed the World" written by Michael L. Watkins and published in 1990.
Lean manufacturing, often described as a set and practice of principles, is aimed at improving the quality, speed, cost, and efficiency of products, services, and other activities. It is about eliminating defects and waste from all stages of the value stream. The five-steps of Lean Manufacturing are just-in time (JIT), zero defect and total productive maintenance (TPM), as well as 5S. Lean manufacturing is about eliminating activities that do not add value, such as inspection, rework, and waiting.
Lean manufacturing can help companies improve their product quality and reduce costs. Additionally, it helps them achieve their goals more quickly and reduces employee turnover. Lean Manufacturing is one of the most efficient ways to manage the entire value chains, including suppliers and customers as well distributors and retailers. Lean manufacturing can be found in many industries. Toyota's philosophy has been a key driver of success in many industries, including automobiles and electronics.
Five basic principles of Lean Manufacturing are included in lean manufacturing
-
Define value - Find out what your business contributes to society, and what makes it different from other competitors.
-
Reduce Waste - Eliminate any activity that doesn't add value along the supply chain.
-
Create Flow - Make sure work runs smoothly without interruptions.
-
Standardize and simplify - Make your processes as consistent as possible.
-
Develop Relationships: Establish personal relationships both with internal and external stakeholders.
Lean manufacturing is not a new concept, but it has been gaining popularity over the last few years due to a renewed interest in the economy following the global financial crisis of 2008. Many businesses are now using lean manufacturing to improve their competitiveness. Some economists even believe that lean manufacturing can be a key factor in economic recovery.
With many benefits, lean manufacturing is becoming more common in the automotive industry. These include higher customer satisfaction levels, reduced inventory levels as well as lower operating costs.
Lean manufacturing can be applied to almost every aspect of an organization. This is because it ensures efficiency and effectiveness in all stages of the value chain.
There are three types of lean manufacturing.
-
Just-in-Time Manufacturing: Also known as "pull systems", this type of lean manufacturing uses just-in-time manufacturing (JIT). JIT refers to a system in which components are assembled at the point of use instead of being produced ahead of time. This approach aims to reduce lead times, increase the availability of parts, and reduce inventory.
-
Zero Defects Manufacturing (ZDM): ZDM focuses on ensuring that no defective units leave the manufacturing facility. Repairing a part that is damaged during assembly should be done, not scrapping. This applies to finished goods that may require minor repairs before shipment.
-
Continuous Improvement (CI),: Continuous improvement aims improve the efficiency and effectiveness of operations by continuously identifying issues and making changes to reduce waste. Continuous improvement involves continuous improvement of processes and people as well as tools.