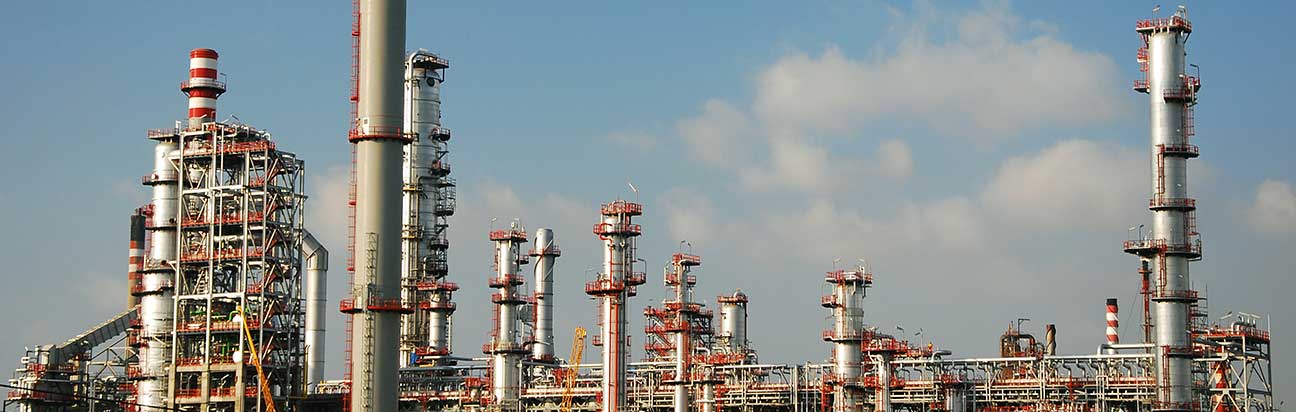
Over the years, global supply chain have experienced many changes. They have become a major economic problem, rather than being an industrial problem. It is worthwhile to be aware of the latest developments. Global supply chains are a complex system that interact in many ways.
Global value chains contain a combination of capital, intangibles, flows, and other resources. They reflect economies of size, long-standing relationships, and specialization. Some value chains have high capital requirements, but others are more regionalized.
Global supply chains are increasingly complex, multidimensional and dynamic. They are essential to global trade and the functioning economy. They are also vulnerable for disruptions. These disruptions are either short-term or long-lasting. To counter these disruptions, it is important to create a flexible, resilient, and diversified supply chain. This requires a comprehensive approach which includes structural reforms and prudent risk management. The first step to building a supply system that can withstand the next storm, is identifying the biggest problems and evaluating the solutions.
Additionally to considering the risks from supply chain disruptions companies need to consider the associated risks with manufacturing, energy, materials. To determine the impact of extreme supply-and demand disruptions, they should simulate them. They need to review their critical materials inventories and ensure that they have enough supply to meet any foreseeable demand. The strategic approach to developing a resilient supply supply chain is critical. It may require reprioritizing manufacturing, shifting manufacturing locations to more flexible locations, improving supply chains technology, and implementing reliable sources of supply.
The COVID-19 Pandemic caused serious disruptions to global supply chains. Numerous countries imposed tariffs and sanctions against each others. These tariffs have caused trade frictions which made it more difficult to sell certain products to China or other countries. These disruptions have increased price inflation. These disruptions have led to increased price inflation, but they have also made companies aware of the fragility in their supply chains. They have forced them into a rethink on the design and implementation their supply chains.
While the COVID-19 pandemic caused widespread disruption in global supply chains, the effects are still being felt. For example, the Suez Canal blockage has led to disruptions in supply chains for as long as six months. The result has been a dramatic rise in freight costs. Annual inflation in the UK has reached 9%.
It is difficult not to notice that China and America are at the center of a trade war. Supply chain leaders must question the logic of heavily relying on outsourced networks. They should also take into account the risks of labor shortages caused by economic shocks. Leaders in supply chains should also be aware of the potential benefits of cross-border finance as well as regulation that can help expand global integration.
Even with all the turmoil, the world is still a highly interconnected place. The benefits of global integration will be realized if firms are willing to take a more holistic approach to their supply chains.
FAQ
How can manufacturing avoid production bottlenecks
Avoiding production bottlenecks is as simple as keeping all processes running smoothly, from the time an order is received until the product ships.
This includes planning to meet capacity requirements and quality control.
Continuous improvement techniques like Six Sigma are the best way to achieve this.
Six Sigma is a management system used to improve quality and reduce waste in every aspect of your organization.
It focuses on eliminating variation and creating consistency in your work.
How does a Production Planner differ from a Project Manager?
The major difference between a Production Planner and a Project Manager is that a Project Manager is often the person responsible for organizing and planning the entire project. While a Production Planner is involved mainly in the planning stage,
What are the responsibilities of a logistic manager?
A logistics manager makes sure that all goods are delivered on-time and in good condition. This is accomplished by using the experience and knowledge gained from working with company products. He/she should also ensure enough stock is available to meet demand.
How can I find out more about manufacturing?
The best way to learn about manufacturing is through hands-on experience. If that is not possible, you could always read books or view educational videos.
How can we improve manufacturing efficiency?
The first step is to identify the most important factors affecting production time. We then need to figure out how to improve these variables. If you don’t know how to start, look at which factors have the greatest impact upon production time. Once you've identified them, try to find solutions for each of those factors.
What is the role and responsibility of a Production Planner?
A production planner makes sure all project elements are delivered on schedule, within budget, as well as within the agreed scope. They also ensure the quality of the product and service meets the client's requirements.
What skills is required for a production planner?
Being a production planner is not easy. You need to be organized and flexible. Communication skills are essential to ensure that you can communicate effectively with clients, colleagues, and customers.
Statistics
- It's estimated that 10.8% of the U.S. GDP in 2020 was contributed to manufacturing. (investopedia.com)
- In 2021, an estimated 12.1 million Americans work in the manufacturing sector.6 (investopedia.com)
- (2:04) MTO is a production technique wherein products are customized according to customer specifications, and production only starts after an order is received. (oracle.com)
- You can multiply the result by 100 to get the total percent of monthly overhead. (investopedia.com)
- In the United States, for example, manufacturing makes up 15% of the economic output. (twi-global.com)
External Links
How To
How to Use Just-In-Time Production
Just-in-time (JIT) is a method that is used to reduce costs and maximize efficiency in business processes. It's the process of obtaining the right amount and timing of resources when you need them. This means that only what you use is charged to your account. Frederick Taylor developed the concept while working as foreman in early 1900s. After observing how workers were paid overtime for late work, he realized that overtime was a common practice. He realized that workers should have enough time to complete their jobs before they begin work. This would help increase productivity.
JIT is an acronym that means you need to plan ahead so you don’t waste your money. It is important to look at your entire project from beginning to end and ensure that you have enough resources to handle any issues that may arise. You will have the resources and people to solve any problems you anticipate. This way, you won't end up paying extra money for things that weren't really necessary.
There are several types of JIT techniques:
-
Demand-driven JIT: This is a JIT that allows you to regularly order the parts/materials necessary for your project. This will enable you to keep track of how much material is left after you use it. This will allow to you estimate the time it will take for more to be produced.
-
Inventory-based: This type allows you to stock the materials needed for your projects ahead of time. This allows you to predict how much you can expect to sell.
-
Project-driven : This is a method where you make sure that enough money is set aside to pay the project's cost. Once you have an idea of how much material you will need, you can purchase the necessary materials.
-
Resource-based: This is the most common form of JIT. This is where you assign resources based upon demand. You will, for example, assign more staff to deal with large orders. If there aren't many orders, you will assign fewer people.
-
Cost-based: This is the same as resource-based except that you don't care how many people there are but how much each one of them costs.
-
Price-based: This is very similar to cost-based, except that instead of looking at how much each individual worker costs, you look at the overall price of the company.
-
Material-based: This is quite similar to cost-based, but instead of looking at the total cost of the company, you're concerned with how much raw materials you spend on average.
-
Time-based: This is another variation of resource-based JIT. Instead of focusing on how much each employee costs, you focus on how long it takes to complete the project.
-
Quality-based JIT: This is another variation of resource based JIT. Instead of worrying about the costs of each employee or how long it takes for something to be made, you should think about how quality your product is.
-
Value-based JIT: One of the most recent forms of JIT. This is where you don't care about how the products perform or whether they meet customers' expectations. Instead, your goal is to add value to the market.
-
Stock-based: This inventory-based approach focuses on how many items are being produced at any one time. It's used when you want to maximize production while minimizing inventory.
-
Just-in-time planning (JIT): This is a combination JIT and supply-chain management. It's the process of scheduling delivery of components immediately after they are ordered. It's important as it reduces leadtimes and increases throughput.