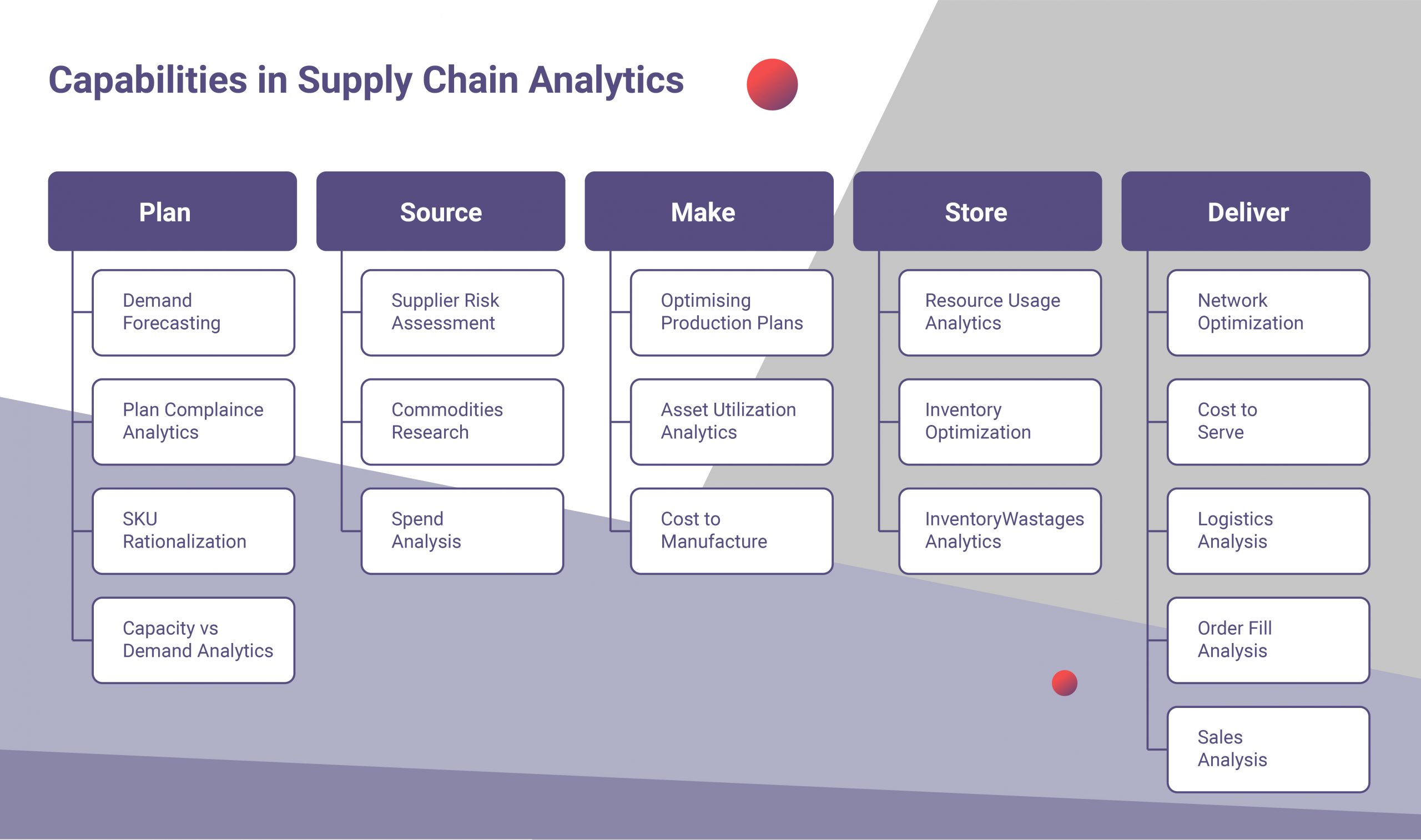
Material managers are responsible for purchasing and delivering materials. They are usually involved in inventory management or raw material management. It is important that they are knowledgeable about the types of raw material required to produce a product. They need to be resourceful in finding these raw materials. They should also have strong relationships with vendors to get the best price and delivery rates. A materials manager's salary is important. These are some tips to help get the job.
Job description
A materials manager is responsible to manage stock and purchasing operations. They must have excellent problem-solving and stock management skills. Material managers are responsible for managing inventory, budgets, and efficiency. This position is responsible for managing inventory and also coordinates the supply chain. It can also supervise subordinates. For this role, an advanced degree in management is required. The materials manager must also have previous experience in a similar position.
Materials managers typically have a bachelor's in business administration or a related field. However, if the position requires a supervisor, a master's degree in a related field is advantageous. While an advanced degree is more beneficial than a job experience, education is still a valuable asset. A materials manager must have at least three years experience in an industrial or manufacturing setting before applying to a managerial job.
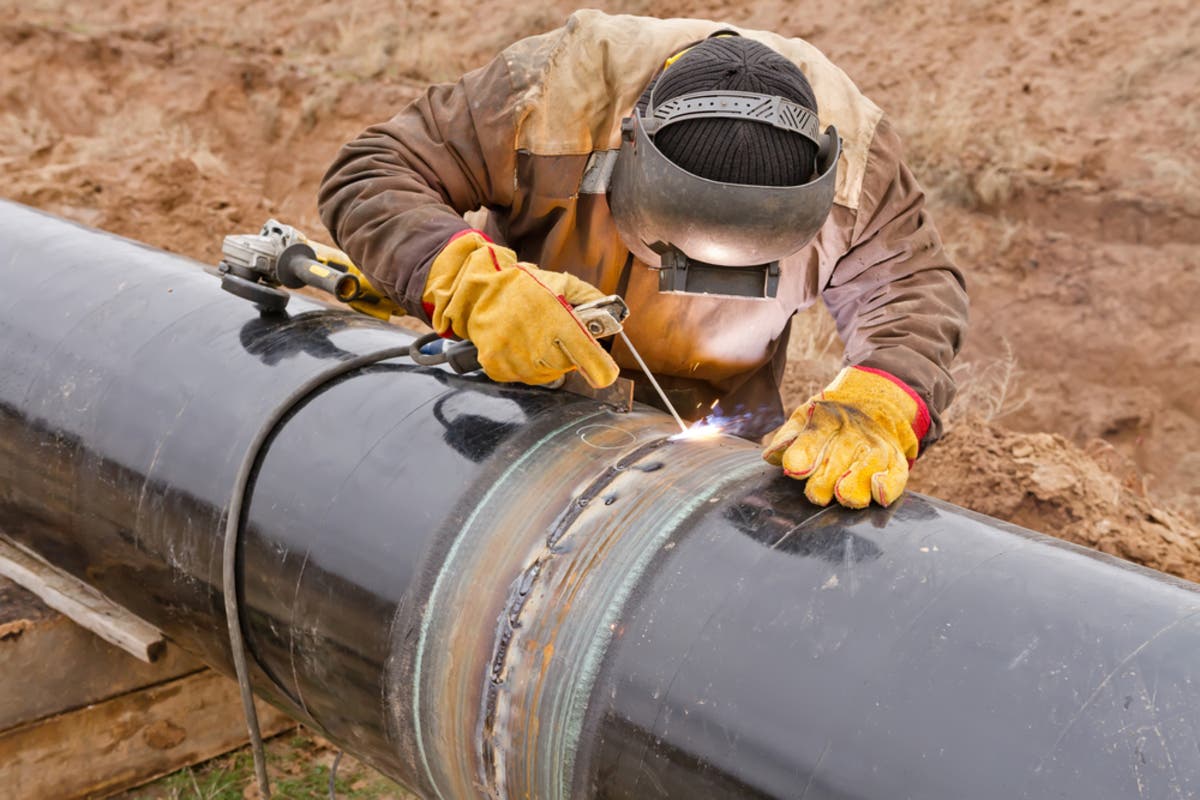
Responsibilities
The role of a materials manager is to evaluate existing projects and determine the material requirements for production. The materials manager may also keep track of inventory using the company's supply-chain management system. He or she could also be responsible for stocking spare parts to repair faulty products. He or she could also be responsible to train employees in proper use of inventory control system. These positions are critical in many companies. However not all of them require extensive education.
Job description: A material manger oversees the company's procurement. The material manager also oversees the distribution and storage of these materials. Experience in logistics, inventory management, and supply chain management are essential for the job. Experience in these areas is an advantage. They will also be working closely with vendors and purchasing departments to establish requirements and plan distribution. This position requires a bachelor's in business and strong analytical skills.
Education necessary
You should know the education requirements for a career in material management. This job requires management skills and knowledge of logistics and receiving. You will be working with QC personnel as well as higher-ranking managers. You will be responsible for planning and delegating work. As a manager, it is important to be able and able judge the performance of subordinates as well as foster harmonious working relationships.
Materials managers typically have a bachelor's degree in a related field. Some companies also require that a materials manager has at least two years' experience before hiring someone with that education. Higher-level positions may require additional education. Many material managers have certifications such as the American Purchasing Society (CPSCP), and the APICS (Association of Purchasing Professionals).
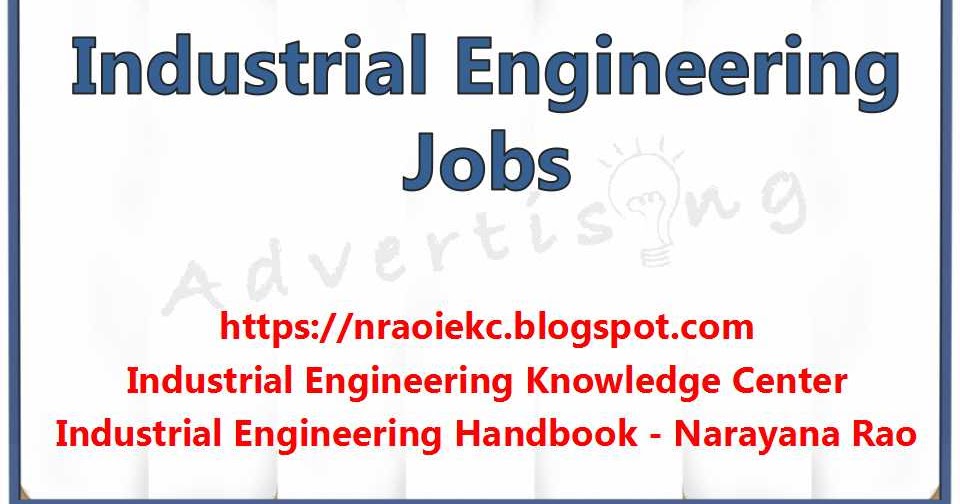
Salary
The average salary for Materials Managers is approximately $78,500. This figure is based off 106 TurboTax user salaries. This includes tips, taxable wages, bonuses and other compensation. The exact salary will vary depending on education and experience. Salary data is adjusted to reflect inflation each year. The typical salary for Materials Managers is found here.
You need to have experience in management before you can become a manager of materials. A good knowledge of logistics, receiving and shipping is essential. A basic understanding of the industry is necessary if you plan to work for a manufacturing company. This will help you negotiate the best prices with suppliers. The experience and training a materials manager has will impact the salary.
FAQ
How can I learn about manufacturing?
The best way to learn about manufacturing is through hands-on experience. But if that is not possible you can always read books and watch educational videos.
What is meant by manufacturing industries?
Manufacturing Industries are those businesses that make products for sale. Consumers are people who purchase these goods. These companies use various processes such as production, distribution, retailing, management, etc., to fulfill this purpose. They make goods from raw materials with machines and other equipment. This includes all types if manufactured goods.
What is production planning?
Production Planning involves developing a plan for all aspects of the production, including scheduling, budgeting, casting, crew, location, equipment, props, etc. It is important to have everything ready and planned before you start shooting. You should also have information to ensure the best possible results on set. This includes shooting schedules, locations, cast lists, crew details, and equipment requirements.
The first step is to outline what you want to film. You might have an idea of where you want to film, or you may have specific locations or sets in mind. Once you have identified the scenes and locations, you can start to determine which elements are required for each scene. One example is if you are unsure of the exact model you want but decide that you require a car. If this is the case, you might start searching online for car models and then narrow your options by selecting from different makes.
After you have selected the car you want, you can begin to think about additional features. Do you need people sitting in the front seats? You might also need someone to help you get around the back. Maybe you'd like to change the interior from black to a white color. These questions will help determine the look and feel you want for your car. It is also worth considering the types of shots that you wish to take. Do you want to film close-ups, or wider angles? Maybe you want to show your engine or the steering wheel. These details will help identify the exact car you wish to film.
Once you have all the information, you are ready to create a plan. You can create a schedule that will outline when you must start and finish your shoots. Each day will include the time when you need to arrive at the location, when you need to leave and when you need to return home. So everyone is clear about what they need to do. You can also make sure to book extra staff in advance if you have to hire them. It's not worth paying someone to show up if you haven't told him.
You will need to factor in the days that you have to film when creating your schedule. Some projects may only take a couple of days, while others could last for weeks. You should consider whether you will need more than one shot per week when creating your schedule. Multiple takes at the same place will result in higher costs and longer completion times. If you aren't sure whether you need multiple shots, it is best to take fewer photos than you would like.
Budget setting is an important part of production planning. You will be able to manage your resources if you have a realistic budget. If you have to reduce your budget due to unexpected circumstances, you can always lower it later. However, it is important not to overestimate the amount that you will spend. If you underestimate the cost of something, you will have less money left after paying for other items.
Production planning is a detailed process. But, once you understand the workings of everything, it becomes easier for future projects to be planned.
Can certain manufacturing steps be automated?
Yes! Yes. The wheel was invented by the Egyptians thousands of years ago. We now use robots to help us with assembly lines.
There are many uses of robotics today in manufacturing. These include:
-
Assembly line robots
-
Robot welding
-
Robot painting
-
Robotics inspection
-
Robots that create products
Manufacturing could also benefit from automation in other ways. For example, 3D printing allows us to make custom products without having to wait for weeks or months to get them manufactured.
What are the responsibilities of a production planner
Production planners make sure that every aspect of the project is delivered on-time, within budget, and within schedule. They make sure that the product and services meet client expectations.
What is the difference between Production Planning and Scheduling?
Production Planning (PP), is the process of deciding what production needs to take place at any given time. Forecasting demand is one way to do this.
Scheduling refers to the process of allocating specific dates to tasks in order that they can be completed within a specified timeframe.
How can excess manufacturing production be reduced?
It is essential to find better ways to manage inventory to reduce overproduction. This would reduce the amount of time spent on unnecessary activities such as purchasing, storing, and maintaining excess stock. This would allow us to use our resources for more productive tasks.
This can be done by using a Kanban system. A Kanban board can be used to monitor work progress. Kanban systems are where work items travel through a series of states until reaching their final destination. Each state has a different priority level.
For instance, when work moves from one stage to another, the current task is complete enough to be moved to the next stage. If a task is still in its beginning stages, it will continue to be so until it reaches the end.
This allows for work to continue moving forward, while also ensuring that there is no work left behind. Managers can see how much work has been done and the status of each task at any time with a Kanban Board. This information allows managers to adjust their workflow based off real-time data.
Lean manufacturing is another option to control inventory levels. Lean manufacturing is about eliminating waste from all stages of the production process. Anything that does not contribute to the product's value is considered waste. There are several types of waste that you might encounter:
-
Overproduction
-
Inventory
-
Packaging not required
-
Excess materials
These ideas can help manufacturers improve efficiency and reduce costs.
Statistics
- Many factories witnessed a 30% increase in output due to the shift to electric motors. (en.wikipedia.org)
- In 2021, an estimated 12.1 million Americans work in the manufacturing sector.6 (investopedia.com)
- It's estimated that 10.8% of the U.S. GDP in 2020 was contributed to manufacturing. (investopedia.com)
- (2:04) MTO is a production technique wherein products are customized according to customer specifications, and production only starts after an order is received. (oracle.com)
- According to a Statista study, U.S. businesses spent $1.63 trillion on logistics in 2019, moving goods from origin to end user through various supply chain network segments. (netsuite.com)
External Links
How To
How to Use the 5S to Increase Productivity In Manufacturing
5S stands to stand for "Sort", “Set In Order", “Standardize", and "Store". Toyota Motor Corporation created the 5S methodology in 1954. It allows companies to improve their work environment, thereby achieving greater efficiency.
This approach aims to standardize production procedures, making them predictable, repeatable, and easily measurable. This means that tasks such as cleaning, sorting, storing, packing, and labeling are performed daily. Workers can be more productive by knowing what to expect.
There are five steps to implementing 5S, including Sort, Set In Order, Standardize, Separate and Store. Each step requires a different action, which increases efficiency. You can make it easy for people to find things later by sorting them. Once you have placed items in an ordered fashion, you will put them together. Once you have separated your inventory into groups and organized them, you will store these groups in easily accessible containers. Finally, label all containers correctly.
Employees must be able to critically examine their work practices. Employees need to be able understand their motivations and discover alternative ways to do them. They must learn new skills and techniques in order to implement the 5S system.
The 5S method not only increases efficiency but also boosts morale and teamwork. They are more motivated to achieve higher efficiency levels as they start to see improvement.