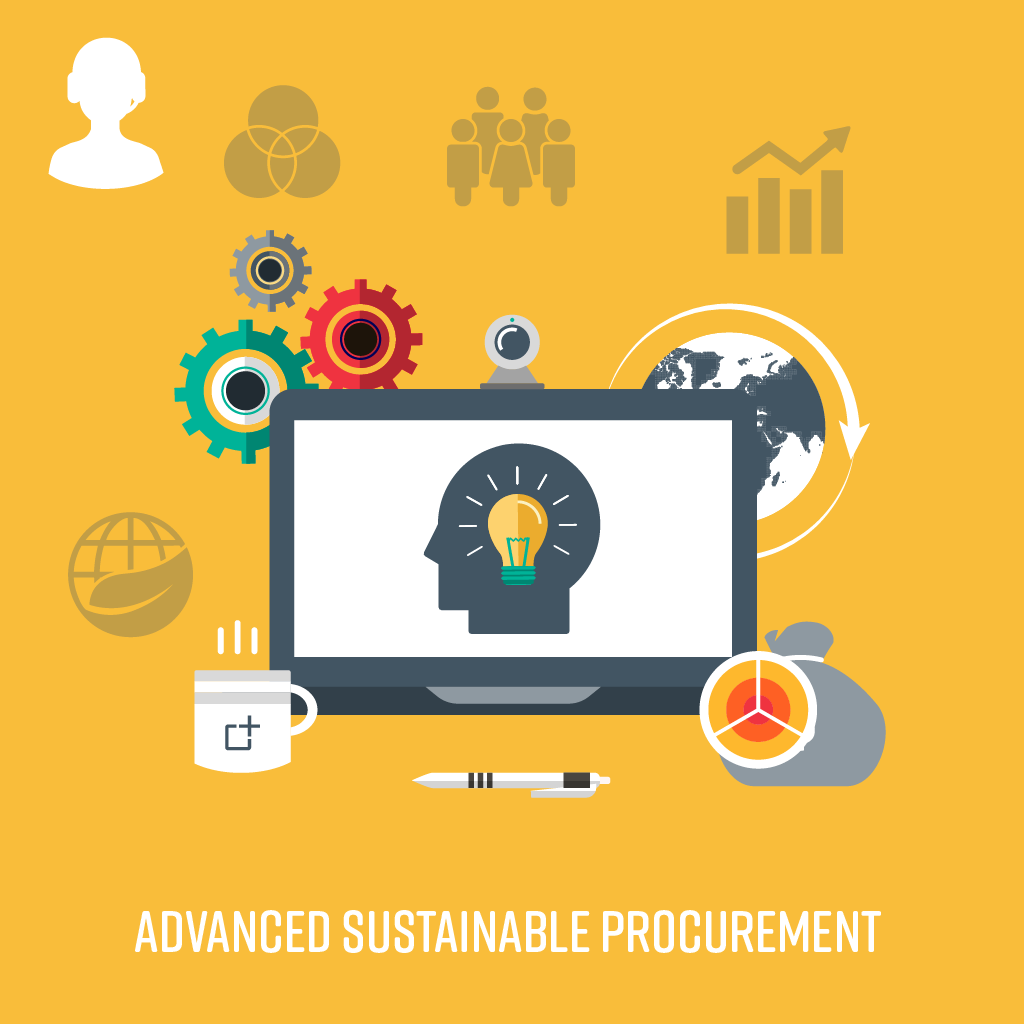
Manufacturing is changing rapidly. This requires new skills, and cutting-edge knowledge. The factory of the future is digital, flexible, responsive, efficient and responsible. It is important to optimize energy consumption and manufacturing processes, develop robots, cobotics, and make sure that manufacturing processes can be traceable. This is where a manufacturing engineer can help. Here are three areas where you need to excel. This article will introduce these key skills and how they will influence the future of your industry.
Analyst perspectives
Analyst perspectives on the future of the industry are essential for understanding current trends as well as assessing its competitive dynamics. These insights are a great way to understand the changing consumer landscape. This includes attitudes and intentions as much as buying behavior. NPD has conducted an annual survey of the industry to get a clear picture of its outlook. The country-specific forecasted categories vary for each industry. This chapter examines the role played by industry analysts in validating and generating market-based knowledge.
Consumer survey data
Prosper surveys are based on the responses of more than 71,000 adults each month. The data is correlated and trended and contains questions on the emotional mindset of consumers, purchasing patterns, and future intentions. It also contains monthly data from hundreds of major brands and retailers over the last 18 years. It is the best way to learn about the spending habits and attitudes of consumers in a particular market. Marketers and business owners can benefit from consumer survey data.
Industries growth patterns
This chapter will focus on the growth patterns in industries and firms. Industry growth is affected by the development of financial markets within developed countries. Finance-hungry areas grow faster in countries where there are financial markets. Conversely, sectors that depend on external financing grow faster after periods with high stock market performance. These patterns match trade and developmental theories which indicate that a country’s product portfolio reflects its economic level. We discuss the major trends that influence industry growth.
Automation
Gartner predicts that automation is going to affect almost every occupation in the next decade. Although only five percent can be fully automated with the current technologies, many other occupations have component activities that can be automated. The reality is that most occupations will be affected by some degree, and their jobs will likely change. Whether they remain human or change will depend on the individual workplace. Here are five ways automation will impact the manufacturing industry.
Hybrid working environment
To create a successful hybrid workplace, companies must listen to their employees and provide many ways to share that feedback. This valuable information can be collected through surveys, focus groups, or one-on-1 conversations. They can also give employees performance incentives such as financial rewards, food deliveries, or tokens of appreciation. Companies can listen to employees and ensure that the transition to the new environment is smooth. This will create a positive experience for all.
Streaming media
The streaming media industry, a new business model is in its infancy, is not yet certain. Many media conglomerates sell short-term streaming rights to three different services. Although streaming was an emerging market initially, it is poised to become the dominant viewing platform in the next few year. In 2025, almost every production of the four media conglomerates should only be available through their streaming services.
Automotive industry
What's the Automotive industry's future? Many experts believe that it will slowly start to recover in the next decade. Automakers face many challenges right now. But, connected vehicles and other technologies could offer new income streams. The government can reduce emissions laws. Automobile companies can improve resilience and accelerate R&D. There are several reasons why the Automotive industry could begin to recover slowly in the coming decade.
FAQ
What skills do production planners need?
Being a production planner is not easy. You need to be organized and flexible. Also, you must be able and willing to communicate with clients and coworkers.
What do we need to know about Manufacturing Processes in order to learn more about Logistics?
No. No. However, knowing about manufacturing processes will definitely give you a better understanding of how logistics works.
What is the importance of logistics in manufacturing?
Logistics are an integral part any business. Logistics can help you achieve amazing results by helping to manage product flow from raw materials to finished products.
Logistics are also important in reducing costs and improving efficiency.
How can I find out more about manufacturing?
The best way to learn about manufacturing is through hands-on experience. But if that is not possible you can always read books and watch educational videos.
What is the role of a production manager?
Production planners ensure all aspects of the project are delivered within time and budget. They also ensure the quality of the product and service meets the client's requirements.
Can certain manufacturing steps be automated?
Yes! Yes. The wheel was invented by the Egyptians thousands of years ago. Robots are now used to assist us in assembly lines.
There are many uses of robotics today in manufacturing. These include:
-
Automated assembly line robots
-
Robot welding
-
Robot painting
-
Robotics inspection
-
Robots create products
There are many other examples of how manufacturing could benefit from automation. 3D printing is a way to make custom products quickly and without waiting weeks or months for them to be manufactured.
Statistics
- According to a Statista study, U.S. businesses spent $1.63 trillion on logistics in 2019, moving goods from origin to end user through various supply chain network segments. (netsuite.com)
- In 2021, an estimated 12.1 million Americans work in the manufacturing sector.6 (investopedia.com)
- You can multiply the result by 100 to get the total percent of monthly overhead. (investopedia.com)
- Many factories witnessed a 30% increase in output due to the shift to electric motors. (en.wikipedia.org)
- According to the United Nations Industrial Development Organization (UNIDO), China is the top manufacturer worldwide by 2019 output, producing 28.7% of the total global manufacturing output, followed by the United States, Japan, Germany, and India.[52][53] (en.wikipedia.org)
External Links
How To
How to use lean manufacturing in the production of goods
Lean manufacturing (or lean manufacturing) is a style of management that aims to increase efficiency, reduce waste and improve performance through continuous improvement. It was developed in Japan during the 1970s and 1980s by Taiichi Ohno, who received the Toyota Production System (TPS) award from TPS founder Kanji Toyoda. Michael L. Watkins published the first book on lean manufacturing in 1990.
Lean manufacturing refers to a set of principles that improve the quality, speed and costs of products and services. It emphasizes reducing defects and eliminating waste throughout the value chain. Lean manufacturing is also known as just in time (JIT), zero defect total productive maintenance(TPM), and five-star (S). Lean manufacturing emphasizes reducing non-value-added activities like inspection, rework and waiting.
Lean manufacturing not only improves product quality but also reduces costs. Companies can also achieve their goals faster by reducing employee turnover. Lean manufacturing has been deemed one of the best ways to manage the entire value-chain, including customers, distributors as well retailers and employees. Lean manufacturing is widely practiced in many industries around the world. Toyota's philosophy is the foundation of its success in automotives, electronics and appliances, healthcare, chemical engineers, aerospace, paper and food, among other industries.
Lean manufacturing includes five basic principles:
-
Define Value- Identify the added value your company brings to society. What makes you stand out from your competitors?
-
Reduce waste - Stop any activity that isn't adding value to the supply chains.
-
Create Flow - Ensure work moves smoothly through the process without interruption.
-
Standardize & Simplify - Make processes as consistent and repeatable as possible.
-
Develop Relationships: Establish personal relationships both with internal and external stakeholders.
Although lean manufacturing isn't a new concept in business, it has gained popularity due to renewed interest in the economy after the 2008 global financial crisis. Many businesses have adopted lean manufacturing techniques to help them become more competitive. Some economists even believe that lean manufacturing can be a key factor in economic recovery.
Lean manufacturing is becoming a popular practice in automotive. It has many advantages. These include higher customer satisfaction levels, reduced inventory levels as well as lower operating costs.
Any aspect of an enterprise can benefit from Lean manufacturing. Lean manufacturing is most useful in the production sector of an organisation because it ensures that each step in the value-chain is efficient and productive.
There are three types principally of lean manufacturing:
-
Just-in-Time Manufacturing (JIT): This type of lean manufacturing is commonly referred to as "pull systems." JIT is a process in which components can be assembled at the point they are needed, instead of being made ahead of time. This method reduces lead times, increases availability, and decreases inventory.
-
Zero Defects Manufacturing: ZDM ensures that no defective units leave the manufacturing plant. If a part needs to be fixed during the assembly line, it should be repaired rather than scrapped. This applies to finished goods that may require minor repairs before shipment.
-
Continuous Improvement (CI: Continuous improvement aims to increase the efficiency of operations by constantly identifying and making improvements to reduce or eliminate waste. Continuous improvement involves continuous improvement of processes and people as well as tools.