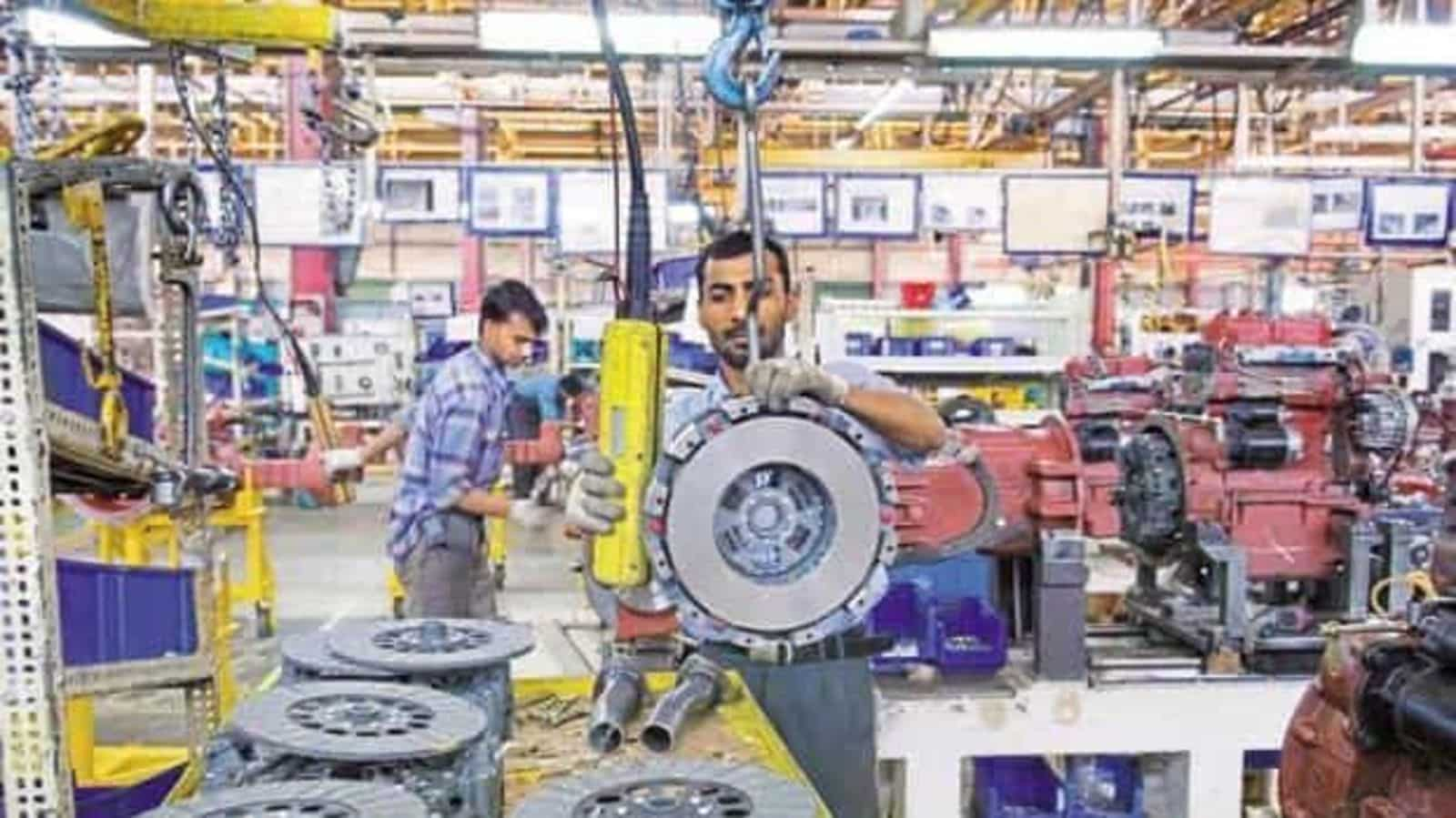
The core qualifications section should be included in the job description of an environmental engineer. This will set out the minimum requirements required for the job in order to attract qualified candidates. These requirements will simplify the hiring process and reduce the risk of applicants not being qualified. It is also beneficial to include a skills section in order to make the hiring process as easy as possible. Continue reading for more information. This job description should be written in a professional, formal language to make the position stand out from others.
Qualifications
If you're considering changing careers to become an environmental engineer, you should know the details of the job. This position involves designing and implementing systems to control air and water quality, perform site remediation, and use pollution control technology. This position often requires collaboration with other professionals, such as environmental specialists and hazardous waste technicians. Many environmental engineers are called upon to assist in environmental litigation and other remediation projects. They also monitor the progress of environmental improvement programs and contribute to the development of environmental journals.
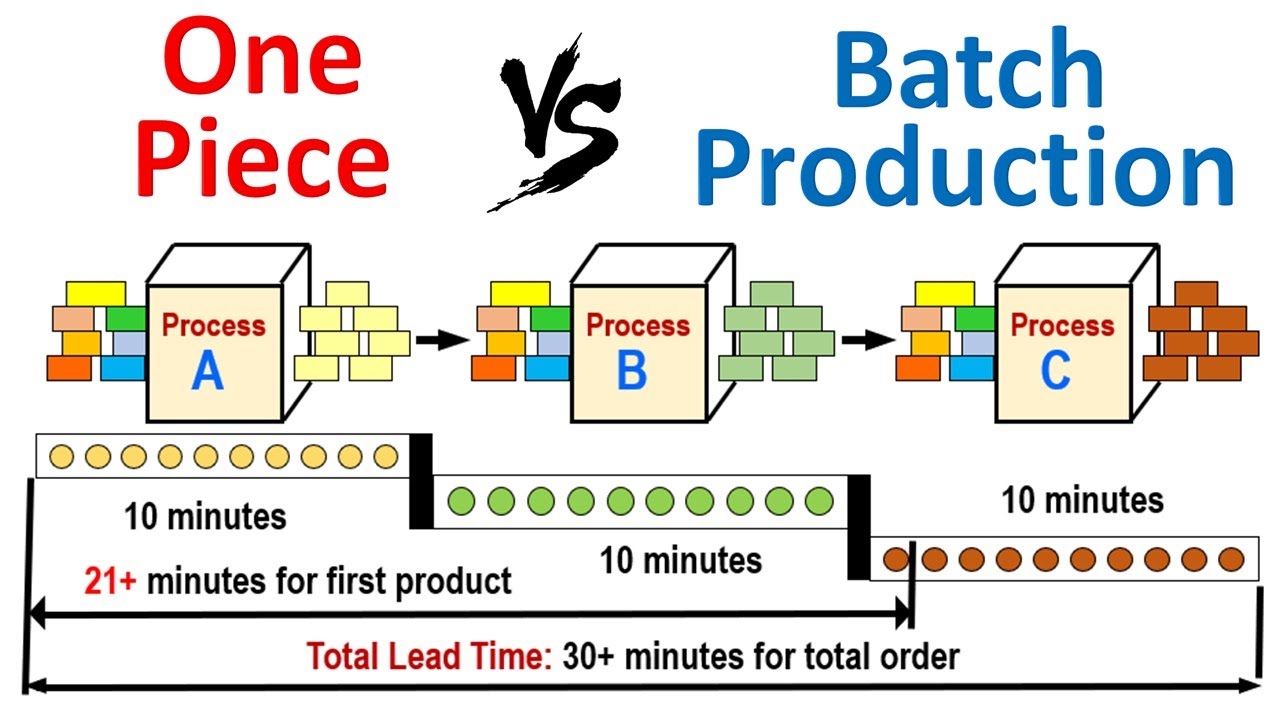
A role as an environmental engineer requires extensive field and office work. An environmental engineer may be responsible for field inspections, characterizing and evaluating materials, or working with subcontractors on site. A thorough knowledge of environmental regulations is essential for their job. Additionally, they might be required to create and maintain spreadsheets as well as other parts of a report. They can participate in a variety projects and can even advance from related professions to their own.
Responsibilities
The responsibilities of an environmental engineer are varied and diverse. Engineers may develop technologies to manage pollution or make recommendations about clean-up procedures. They may also work with legal counsel and other experts, such as those in the fields of law and business. They may also be responsible for administrative tasks, such as creating spreadsheets or other components of reports. Environmental engineers may advise federal, regional, and local government agencies in matters of environmental protection.
Another responsibility of an environmental engineer is to assist in the development of and implementation plans and programs that will be used for the conservation and management natural resources. They analyze the impact of a commercial activity on land and other resources. They are also responsible for general administrative tasks such as the preparation of project documentation, training staff and aiding in budget implementation. An environmental engineer may also advise policymakers on environmental issues and best practices.
Perspectives on employment
Positive employment prospects are available for environmental engineers. Engineers are needed to help companies comply and find alternative ways to remove pollutants. Due to increasing population and the focus on prevention, environmental engineers will be in high demand. There will be more job openings as employees move to other areas or retire. This is a job that won't disappoint. These are some of the jobs that you could apply for in future.
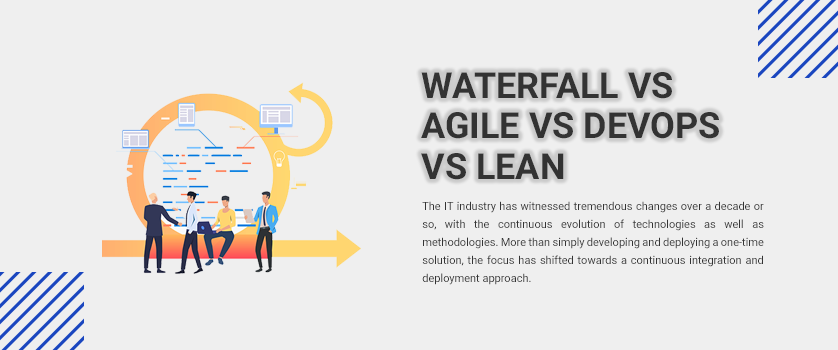
The majority of environmental engineers work in labs and offices. While many work indoors, some spend time outdoors or travel to construction sites. These professionals usually work a forty-hour week. Some jobs require travel, so your schedule may vary. If deadlines are required, the work can be very demanding. The environment is the primary concern of environmental engineers. They should be aware and comfortable with their physical limitations. This occupation is often subject to high levels of stress and long working hours.
FAQ
How can manufacturing efficiency improved?
First, identify the factors that affect production time. Then we need to find ways to improve these factors. If you aren't sure where to begin, think about the factors that have the greatest impact on production time. Once you identify them, look for solutions.
What is the responsibility of a production planner?
A production planner makes sure all project elements are delivered on schedule, within budget, as well as within the agreed scope. They also ensure the quality of the product and service meets the client's requirements.
What do you mean by warehouse?
A warehouse, or storage facility, is where goods are stored prior to being sold. It can be an outdoor or indoor area. It could be one or both.
What jobs are available in logistics?
There are many jobs available in logistics. Here are some examples:
-
Warehouse workers: They load and unload trucks, pallets, and other cargo.
-
Transportation drivers – They drive trucks or trailers to transport goods and perform pick-ups.
-
Freight handlers - They sort and pack freight in warehouses.
-
Inventory managers: They are responsible for the inventory and management of warehouses.
-
Sales representatives - They sell products.
-
Logistics coordinators: They plan and manage logistics operations.
-
Purchasing agents - They purchase goods and services needed for company operations.
-
Customer service agents - They answer phone calls and respond to emails.
-
Shippers clerks - They process shipping order and issue bills.
-
Order fillers - They fill orders based on what is ordered and shipped.
-
Quality control inspectors (QCI) - They inspect all incoming and departing products for potential defects.
-
Others – There are many other types available in logistics. They include transport supervisors, cargo specialists and others.
What does manufacturing industry mean?
Manufacturing Industries refers to businesses that manufacture products. Consumers are the people who purchase these products. These companies employ many processes to achieve this purpose, such as production and distribution, retailing, management and so on. They create goods from raw materials, using machines and various other equipment. This includes all types manufactured goods such as clothing, building materials, furniture, electronics, tools and machinery.
Statistics
- Job #1 is delivering the ordered product according to specifications: color, size, brand, and quantity. (netsuite.com)
- You can multiply the result by 100 to get the total percent of monthly overhead. (investopedia.com)
- According to the United Nations Industrial Development Organization (UNIDO), China is the top manufacturer worldwide by 2019 output, producing 28.7% of the total global manufacturing output, followed by the United States, Japan, Germany, and India.[52][53] (en.wikipedia.org)
- [54][55] These are the top 50 countries by the total value of manufacturing output in US dollars for its noted year according to World Bank.[56] (en.wikipedia.org)
- (2:04) MTO is a production technique wherein products are customized according to customer specifications, and production only starts after an order is received. (oracle.com)
External Links
How To
How to use the Just In-Time Production Method
Just-intime (JIT), which is a method to minimize costs and maximize efficiency in business process, is one way. It's the process of obtaining the right amount and timing of resources when you need them. This means that only what you use is charged to your account. Frederick Taylor developed the concept while working as foreman in early 1900s. Taylor observed that overtime was paid to workers if they were late in working. He concluded that if workers were given enough time before they start work, productivity would increase.
The idea behind JIT is that you should plan ahead and have everything ready so you don't waste money. The entire project should be looked at from start to finish. You need to ensure you have enough resources to tackle any issues that might arise. If you expect problems to arise, you will be able to provide the necessary equipment and personnel to address them. This way you won't be spending more on things that aren’t really needed.
There are many JIT methods.
-
Demand-driven JIT: You order the parts and materials you need for your project every other day. This will allow for you to track the material that you have left after using it. You'll also be able to estimate how long it will take to produce more.
-
Inventory-based : You can stock the materials you need in advance. This allows one to predict how much they will sell.
-
Project-driven: This approach involves setting aside sufficient funds to cover your project's costs. Once you have an idea of how much material you will need, you can purchase the necessary materials.
-
Resource-based JIT : This is probably the most popular type of JIT. This is where you assign resources based upon demand. If you have many orders, you will assign more people to manage them. If you don't have many orders, you'll assign fewer people to handle the workload.
-
Cost-based: This is similar to resource-based, except that here you're not just concerned about how many people you have but how much each person costs.
-
Price-based: This is similar to cost-based but instead of looking at individual workers' salaries, you look at the total company price.
-
Material-based - This is a variant of cost-based. But instead of looking at the total company cost, you focus on how much raw material you spend per year.
-
Time-based JIT: This is another variant of resource-based JIT. Instead of focusing only on how much each employee is costing, you should focus on how long it takes to complete your project.
-
Quality-based JIT - This is another form of resource-based JIT. Instead of thinking about the cost of each employee or the time it takes to produce something, you focus on how good your product quality.
-
Value-based JIT is the newest form of JIT. This is where you don't care about how the products perform or whether they meet customers' expectations. Instead, you're focused on how much value you add to the market.
-
Stock-based: This inventory-based approach focuses on how many items are being produced at any one time. This is used to increase production and minimize inventory.
-
Just-intime (JIT), planning is a combination JIT management and supply chain management. This refers to the scheduling of the delivery of components as soon after they are ordered. This is important as it reduces lead time and increases throughput.