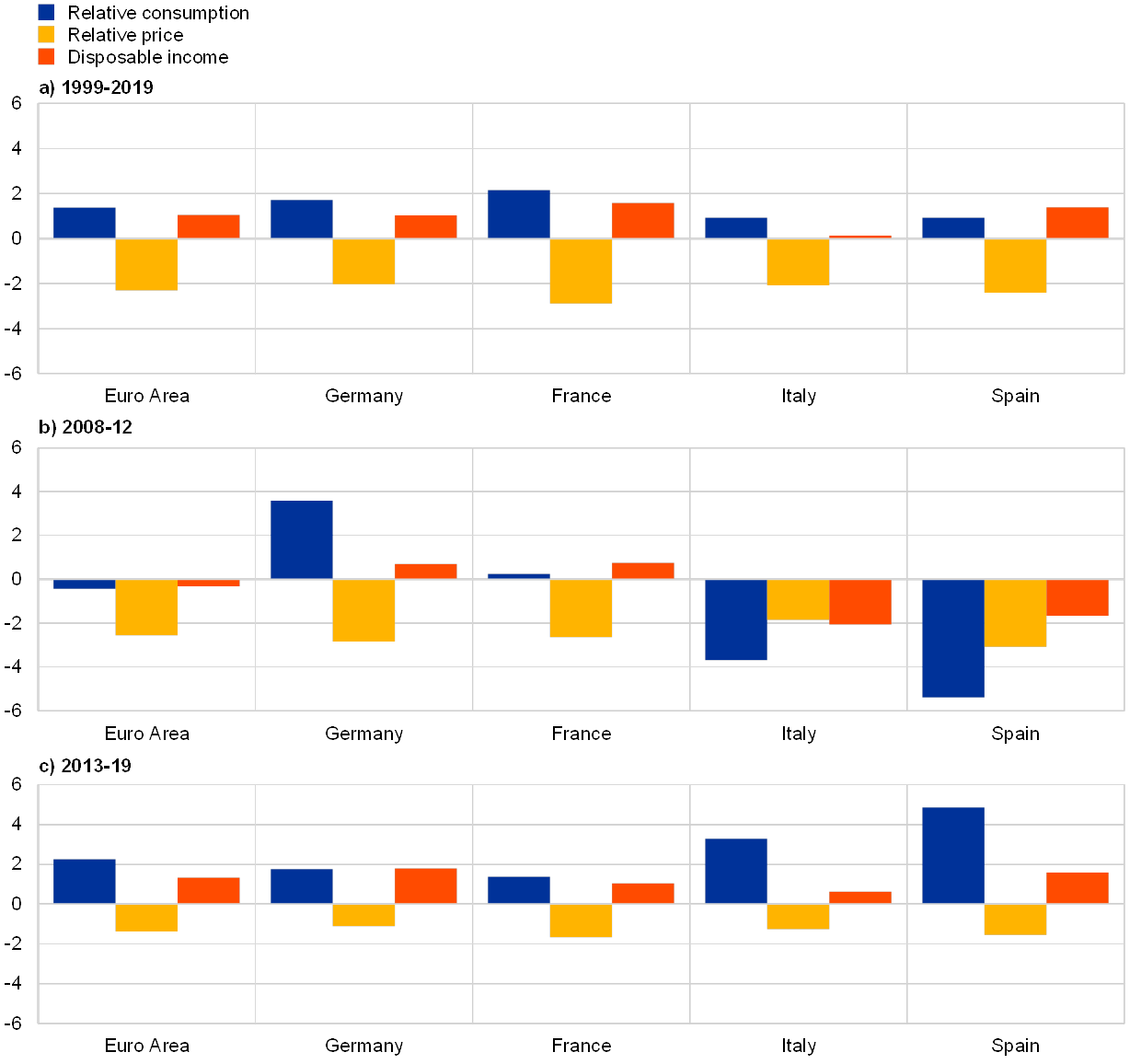
Advanced manufacturing is where companies use innovative technologies to produce better products and processes. These technologies are called innovative, cutting-edge, and advanced. More companies integrate these technologies into operations. Some of these technologies are: Robotics, Material deposition, and Additive manufacturing. Find out more about these technologies.
Additive manufacturing
Advanced manufacturing through additive manufacturing is the future for many manufacturing businesses. This type manufacturing makes use of additive manufacturing technology, also known 3D printing. This type manufacturing is more flexible and has lower inventory costs. This method of manufacturing reduces the need to import labor intensive parts and components.
Advancements in additive manufacturing technology have significantly increased the speed and flexibility of manufacturing. They allow companies to quickly respond to supply chain disruptions. They can create custom parts in a matter of hours, or even days. This process is especially useful in industries where there are supply-chain bottlenecks. Advanced manufacturing is capable of producing parts with complex geometries.
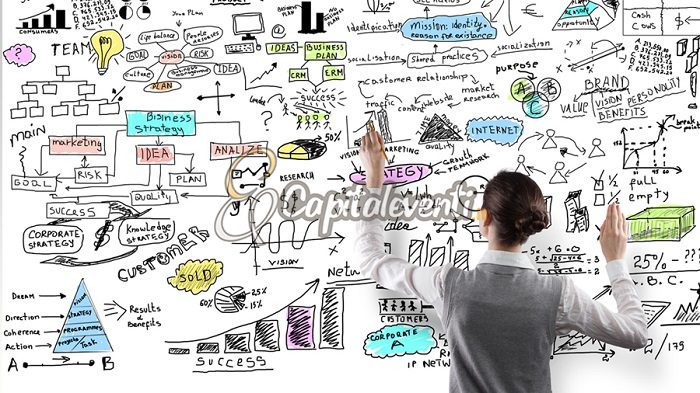
A manufacturer can also make very small quantities. A custom-made set of dental appliances can be made using additive manufacturing. Additionally, complex structures can be manufactured using the additive manufacturing process, including internal heat channels. Advanced manufacturing with additive manufacturing reduces inventory and the need to manufacture specialized components. It can cut materials costs by ninety percent and energy consumption in half.
Robotics
Industrial producers are aware of the potential for advanced robots and want to implement them in factories. They aren't satisfied with the current performance and progress made in their implementation. They point to the limitations and high costs of current technology as the barriers to greater deployment. They lack the key enablers necessary to fully deploy advanced robotics within their factories.
To effectively integrate advanced robotics, manufacturers must evaluate their system architecture. These systems need to include infrastructure, analytics and data management. After these capabilities are established, companies can select strategic robotics vendors. These partners can help companies determine the best technologies and processes for their operation. Simulation models can help with robotics.
The use of advanced robotics is rapidly evolving across numerous industries. Robotic automation is currently being used in a variety of industries, including aerospace, automotive, and medical manufacturing. This technology is revolutionizing the manufacturing industry. Advanced robotic automation not only reduces labor costs but also saves energy because it works 24 hours a days and doesn't require lights.
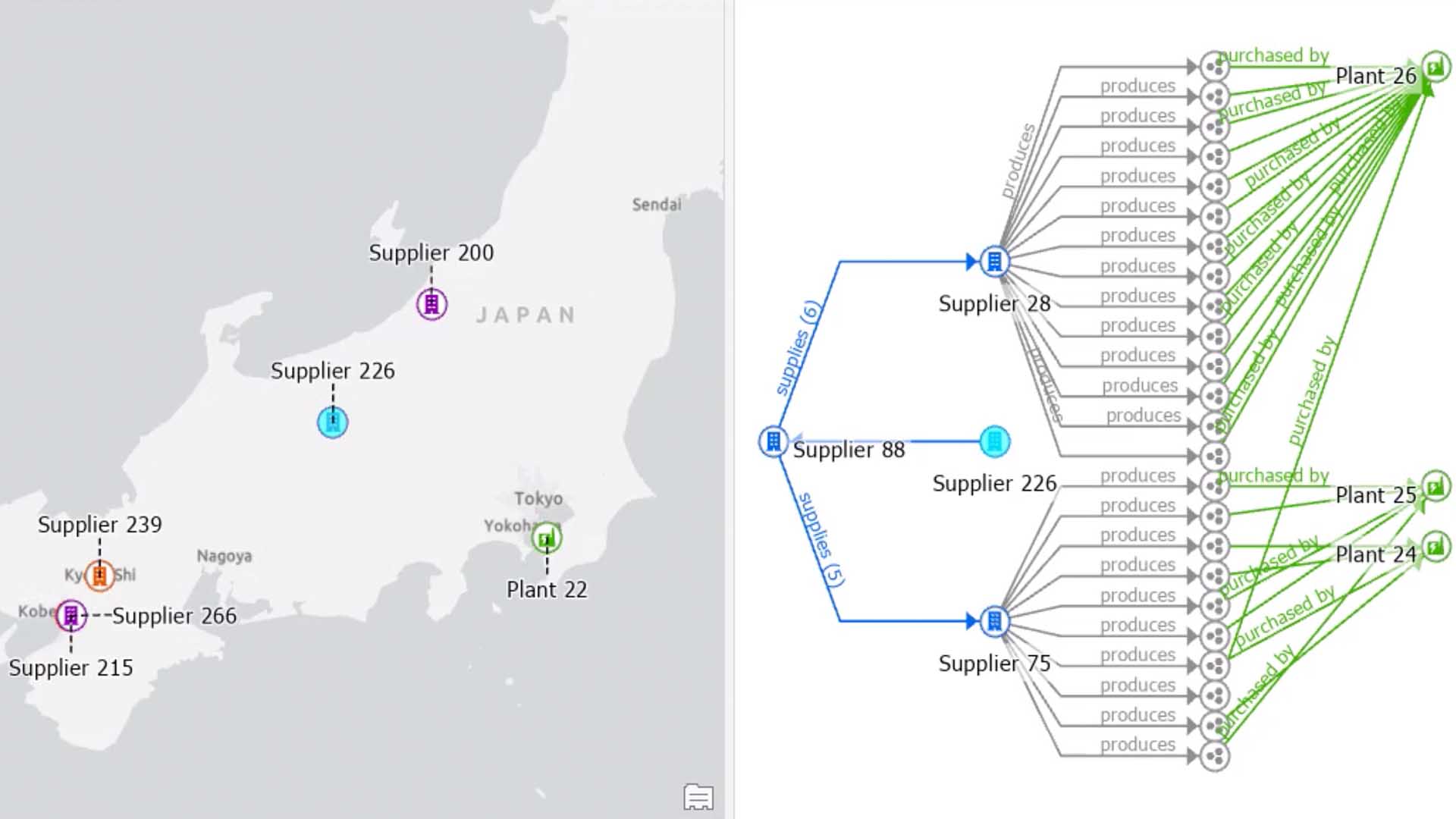
Material deposition
In the field of advanced manufacturing, material deposition is an important technique. This involves the use of both arc plasma energy sources and laser beam to deposit thin film of a substance on a target. The substrate is typically made of powder or wire. Deposition happens in an inert gases or vacuum. You can also find other sources of energy.
Plasma metal deposition is one of the most promising direct energy deposition techniques. It uses a plasma source for metals to be deposited. This process can be used to create large, complex parts from wire, powder or both. The benefits of this process include reduced machining and a shorter lead time.
This process can be used on ceramics, metals, and polymers. Metals are generally used in powder or wire form.
FAQ
How does a production planner differ from a project manager?
A production planner is more involved in the planning phase of the project than a project manger.
What is the importance of logistics in manufacturing?
Logistics are an essential component of any business. Logistics can help you achieve amazing results by helping to manage product flow from raw materials to finished products.
Logistics plays a significant role in reducing cost and increasing efficiency.
Why automate your warehouse
Modern warehousing has seen automation take center stage. E-commerce has increased the demand for quicker delivery times and more efficient processes.
Warehouses must be able to quickly adapt to changing demands. To do so, they must invest heavily in technology. The benefits of automating warehouses are numerous. Here are some benefits of investing in automation
-
Increases throughput/productivity
-
Reduces errors
-
Improves accuracy
-
Safety Boosts
-
Eliminates bottlenecks
-
This allows companies to scale easily
-
This makes workers more productive
-
Provides visibility into everything that happens in the warehouse
-
Enhances customer experience
-
Improves employee satisfaction
-
Minimizes downtime and increases uptime
-
This ensures that quality products are delivered promptly
-
Eliminates human error
-
It ensures compliance with regulations
What are the essential elements of running a logistics firm?
To run a successful logistics company, you need a lot knowledge and skills. Good communication skills are essential to effectively communicate with your suppliers and clients. You will need to know how to interpret data and draw conclusions. You must be able and able to handle stress situations and work under pressure. You must be creative and innovative to develop new ideas to improve efficiency. You will need strong leadership skills to motivate and direct your team members towards achieving their organizational goals.
It is important to be organized and efficient in order to meet tight deadlines.
How can manufacturing avoid production bottlenecks
You can avoid bottlenecks in production by making sure that everything runs smoothly throughout the production cycle, from the moment you receive an order to the moment the product is shipped.
This includes planning for capacity requirements as well as quality control measures.
Continuous improvement techniques like Six Sigma are the best way to achieve this.
Six Sigma Management System is a method to increase quality and reduce waste throughout your organization.
It's all about eliminating variation and creating consistency in work.
What does manufacturing mean?
Manufacturing Industries refers to businesses that manufacture products. The people who buy these products are called consumers. These companies use various processes such as production, distribution, retailing, management, etc., to fulfill this purpose. They produce goods from raw materials by using machines and other machinery. This includes all types manufactured goods such as clothing, building materials, furniture, electronics, tools and machinery.
What is the difference between manufacturing and logistics
Manufacturing is the process of creating goods from raw materials by using machines and processes. Logistics is the management of all aspects of supply chain activities, including procurement, production planning, distribution, warehousing, inventory control, transportation, and customer service. Manufacturing and logistics are often considered together as a broader term that encompasses both the process of creating products and delivering them to customers.
Statistics
- According to the United Nations Industrial Development Organization (UNIDO), China is the top manufacturer worldwide by 2019 output, producing 28.7% of the total global manufacturing output, followed by the United States, Japan, Germany, and India.[52][53] (en.wikipedia.org)
- (2:04) MTO is a production technique wherein products are customized according to customer specifications, and production only starts after an order is received. (oracle.com)
- According to a Statista study, U.S. businesses spent $1.63 trillion on logistics in 2019, moving goods from origin to end user through various supply chain network segments. (netsuite.com)
- [54][55] These are the top 50 countries by the total value of manufacturing output in US dollars for its noted year according to World Bank.[56] (en.wikipedia.org)
- Many factories witnessed a 30% increase in output due to the shift to electric motors. (en.wikipedia.org)
External Links
How To
How to Use Lean Manufacturing in the Production of Goods
Lean manufacturing is a management system that aims at increasing efficiency and reducing waste. It was developed in Japan during the 1970s and 1980s by Taiichi Ohno, who received the Toyota Production System (TPS) award from TPS founder Kanji Toyoda. Michael L. Watkins published the original book on lean manufacturing, "The Machine That Changed the World," in 1990.
Lean manufacturing is often described as a set if principles that help improve the quality and speed of products and services. It emphasizes the elimination and minimization of waste in the value stream. The five-steps of Lean Manufacturing are just-in time (JIT), zero defect and total productive maintenance (TPM), as well as 5S. Lean manufacturing emphasizes reducing non-value-added activities like inspection, rework and waiting.
Lean manufacturing not only improves product quality but also reduces costs. Companies can also achieve their goals faster by reducing employee turnover. Lean manufacturing can be used to manage all aspects of the value chain. Customers, suppliers, distributors, retailers and employees are all included. Lean manufacturing practices are widespread in many industries. For example, Toyota's philosophy underpins its success in automobiles, electronics, appliances, healthcare, chemical engineering, aerospace, paper, food, etc.
Lean manufacturing includes five basic principles:
-
Define Value - Determine the value that your business brings to society. Also, identify what sets you apart from your competitors.
-
Reduce Waste - Remove any activity which doesn't add value to your supply chain.
-
Create Flow: Ensure that the work process flows without interruptions.
-
Standardize & Simplify - Make processes as consistent and repeatable as possible.
-
Build Relationships- Develop personal relationships with both internal as well as external stakeholders.
Lean manufacturing, although not new, has seen renewed interest in the economic sector since 2008. To increase their competitiveness, many businesses have turned to lean manufacturing. In fact, some economists believe that lean manufacturing will be an important factor in economic recovery.
Lean manufacturing has many benefits in the automotive sector. These include higher customer satisfaction, lower inventory levels, lower operating expenses, greater productivity, and improved overall safety.
Any aspect of an enterprise can benefit from Lean manufacturing. This is because it ensures efficiency and effectiveness in all stages of the value chain.
There are three main types:
-
Just-in Time Manufacturing: This lean manufacturing method is commonly called "pull systems." JIT refers to a system in which components are assembled at the point of use instead of being produced ahead of time. This approach aims to reduce lead times, increase the availability of parts, and reduce inventory.
-
Zero Defects Manufacturing (ZDM),: ZDM is a system that ensures no defective units are left the manufacturing facility. You should repair any part that needs to be repaired during an assembly line. This applies to finished goods that may require minor repairs before shipment.
-
Continuous Improvement (CI), also known as Continuous Improvement, aims at improving the efficiency of operations through continuous identification and improvement to minimize or eliminate waste. Continuous improvement involves continuous improvement of processes and people as well as tools.