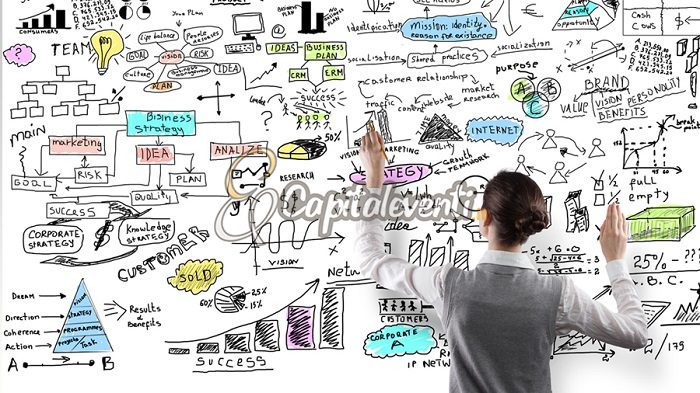
Lean is a term used in manufacturing to describe a series of principles and techniques. It is also a motivating word that encourages improvements in the process.
The Definition of Lean
If a company wants to become more efficient, they may need to eliminate activities that do not add value to their product or service. This can include idle resources, unused equipment, or other resources that have not been used to the fullest extent.
This is the primary goal of lean production management, which is a method designed to eliminate waste. This process is never-ending, which means that it must always be improved and adjusted.
Lean philosophy is based on a belief that businesses should prioritize what their customers need and want rather than what it thinks they do. This way, companies can avoid wasting money or time creating products that are not wanted by their customers.
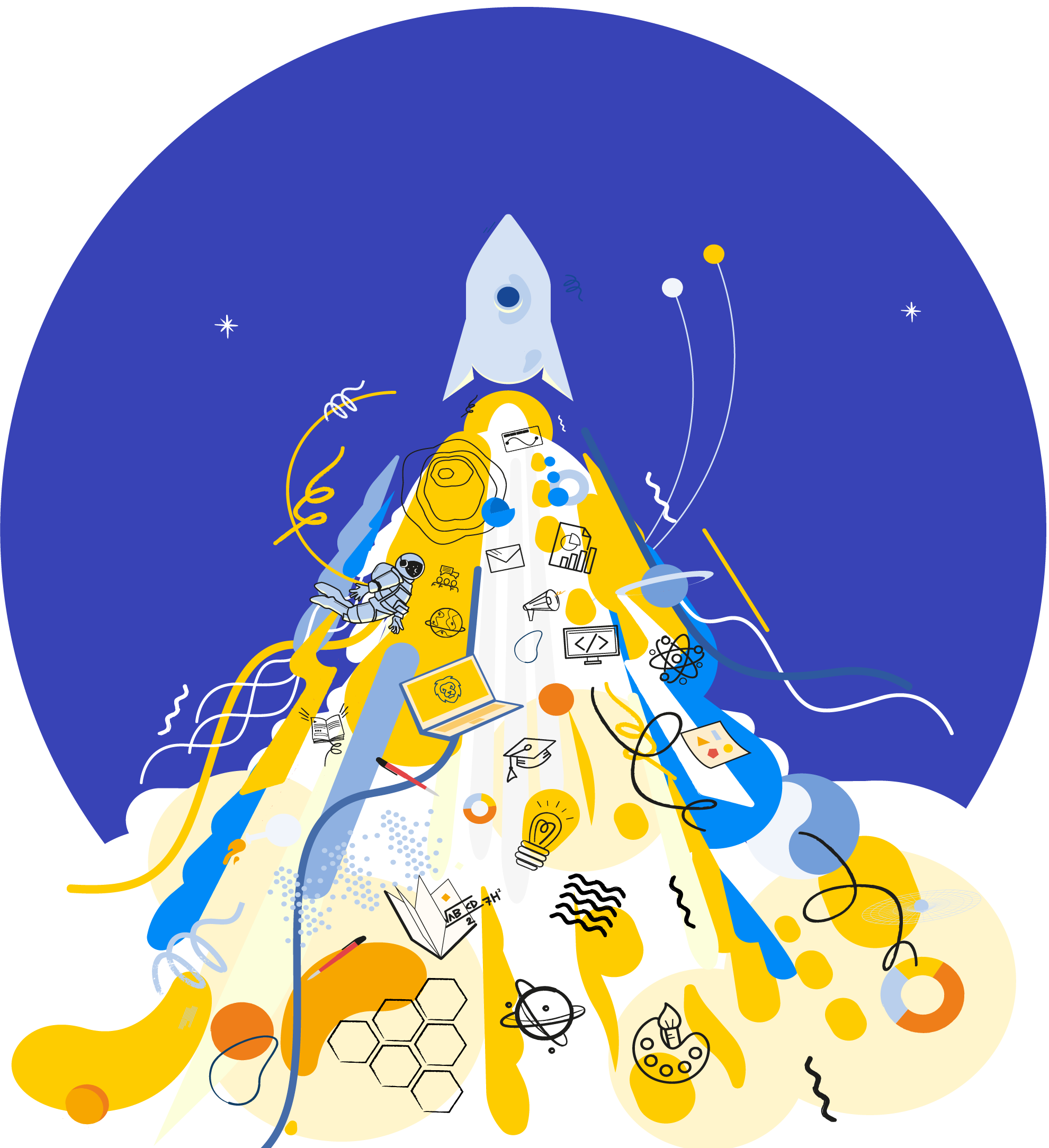
You should be aware that the lean concept can be adapted to any type of industry or production process. This is one of the reasons it has gained so much popularity in different industries.
Lean production, which has existed for quite some time, is a way of focusing on delivering quality products in the right quantities and at the right times. It is also a great tool for creating efficiencies in the manufacturing process.
Toyoda defined lean as a concept that aims to eliminate waste from the production process. This includes things like waste in the form of defects, which would not be acceptable to the customer.
Toyoda found a way to solve this problem by using a flow process. This involved workers stopping production lines to inspect and remove parts as necessary. The company was able to optimize each stage of production to reduce defects and increase productivity.
Jidoka is a system that automatically comes to a stop when there is an abnormality in the production process. Kaizen is a vital part of lean production.
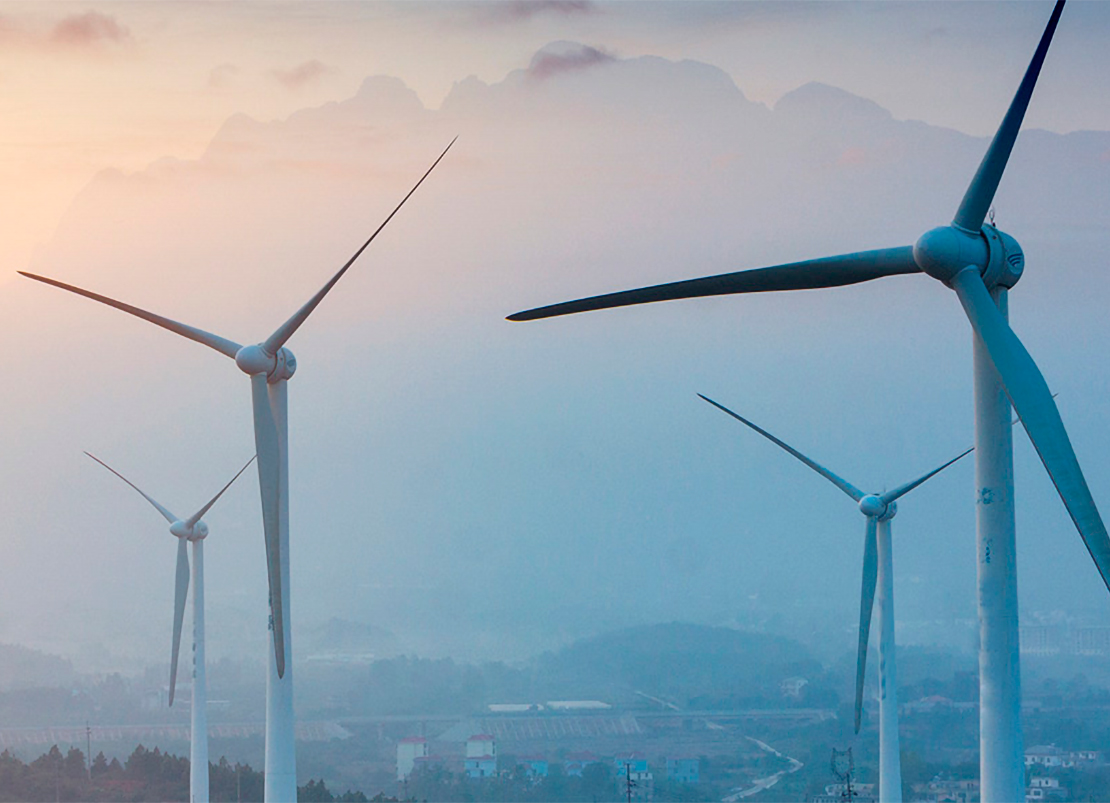
Kaizen is the process of continuous improvement in any process. This can be applied to the production of products or any other area in the business that needs an update.
Lean is not well understood by many people, but it's a wonderful concept that improves the way businesses are run. It can help companies save money and time by improving their processes, and it can help them build a better reputation with customers.
To be successful, lean does not exist in isolation. It is a continuous process that requires the involvement of all employees. It is important to include all employees so that they can share their ideas and make sure that the process runs smoothly.
FAQ
What is the best way to learn about manufacturing?
The best way to learn about manufacturing is through hands-on experience. You can also read educational videos or take classes if this isn't possible.
Why should you automate your warehouse?
Modern warehousing is becoming more automated. With the rise of ecommerce, there is a greater demand for faster delivery times as well as more efficient processes.
Warehouses have to be flexible to meet changing requirements. They must invest heavily in technology to do this. Automating warehouses is a great way to save money. These are some of the benefits that automation can bring to warehouses:
-
Increases throughput/productivity
-
Reduces errors
-
Improves accuracy
-
Boosts safety
-
Eliminates bottlenecks
-
Companies can scale more easily
-
Increases efficiency of workers
-
Provides visibility into everything that happens in the warehouse
-
Enhances customer experience
-
Improves employee satisfaction
-
This reduces downtime while increasing uptime
-
This ensures that quality products are delivered promptly
-
Eliminates human error
-
This helps to ensure compliance with regulations
What is the role of a production manager?
Production planners make sure that every aspect of the project is delivered on-time, within budget, and within schedule. A production planner ensures that the service and product meet the client's expectations.
How can manufacturing reduce production bottlenecks?
Production bottlenecks can be avoided by ensuring that processes are running smoothly during the entire production process, starting with the receipt of an order and ending when the product ships.
This includes planning for capacity requirements as well as quality control measures.
Continuous improvement techniques such Six Sigma can help you achieve this.
Six Sigma management is a system that improves quality and reduces waste within your organization.
It emphasizes consistency and eliminating variance in your work.
Statistics
- You can multiply the result by 100 to get the total percent of monthly overhead. (investopedia.com)
- Job #1 is delivering the ordered product according to specifications: color, size, brand, and quantity. (netsuite.com)
- It's estimated that 10.8% of the U.S. GDP in 2020 was contributed to manufacturing. (investopedia.com)
- According to a Statista study, U.S. businesses spent $1.63 trillion on logistics in 2019, moving goods from origin to end user through various supply chain network segments. (netsuite.com)
- Many factories witnessed a 30% increase in output due to the shift to electric motors. (en.wikipedia.org)
External Links
How To
How to Use Six Sigma in Manufacturing
Six Sigma is defined by "the application SPC (statistical process control) techniques to achieve continuous improvements." Motorola's Quality Improvement Department developed it at their Tokyo plant in Japan in 1986. Six Sigma's main goal is to improve process quality by standardizing processes and eliminating defects. Many companies have adopted this method in recent years. They believe there is no such thing a perfect product or service. Six Sigma's primary goal is to reduce variation from the average value of production. You can calculate the percentage of deviation from the norm by taking a sample of your product and comparing it to the average. If it is too large, it means that there are problems.
Understanding how variability works in your company is the first step to Six Sigma. Once you understand this, you can then identify the causes of variation. This will allow you to decide if these variations are random and systematic. Random variations happen when people make errors; systematic variations are caused externally. Random variations would include, for example, the failure of some widgets to fall from the assembly line. But if you notice that every widget you make falls apart at the exact same place each time, this would indicate that there is a problem.
Once you've identified where the problems lie, you'll want to design solutions to eliminate those problems. That solution might involve changing the way you do things or redesigning the process altogether. You should then test the changes again after they have been implemented. If they don't work you need to rework them and come up a better plan.