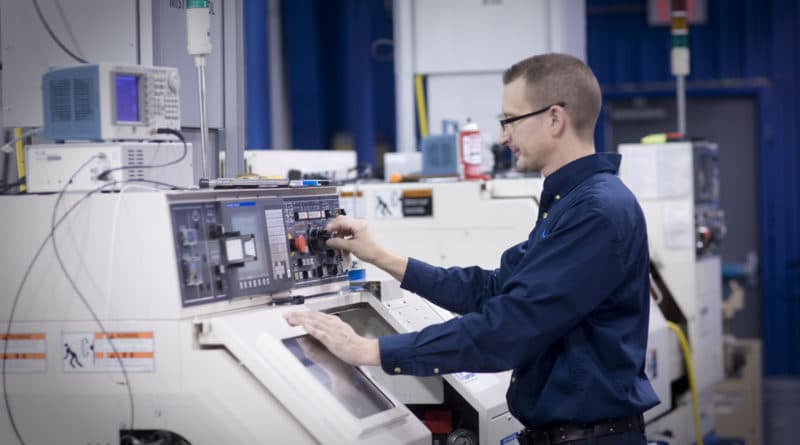
The duties and responsibilities of a mechanical engineering technician depend on their employer. They may be required to test equipment, review blueprints, create purchase requests, and conduct research in order to improve mechanical processes. They may also be exposed at times to potentially hazardous substances. These risks are minimized with the use of proper procedures.
Although they are usually supervised by an engineer, a mechanical engineering technician can perform their duties on their own. They are responsible for maintaining and repairing machinery and equipment. They must not only adhere to safety guidelines and company policies, but also meet customers' needs.
A mechanical engineer technician with the right skills will be able solve problems and calculate accurately. They will also work closely with engineers to improve production processes. They may also design or test new equipment.
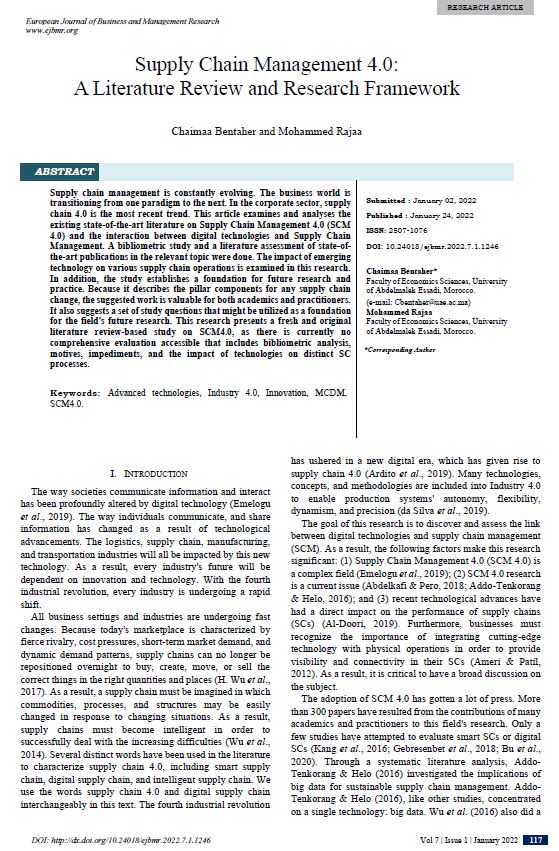
Mechanical engineering technicians must be well-versed in the principles and practices of engineering to obtain the best job. A mechanical engineering technician should be proficient in using CAD software for designing and analysing mechanical systems. They must also be able maintain service records. They must also have excellent time management skills.
A mechanical engineering technician's most important duties are to test equipment and make estimates. They may also do research to improve manufacturing processes. These results are often recorded and evaluated, which makes them an integral part of the job description for a mechanical engineer technician.
Another job of a mechanical engineer technician is to prepare drawings for components, interpret instructions, write work orders and interpret instructions. In order to test and verify the operation of equipment and electrical systems, mechanical engineers might also test materials, equipment, or other devices. They may also design machinery for power generation plants and other related equipment. They may also be able to perform statistical studies in order to evaluate the production's costs.
You will need to have solid knowledge about mechanical engineering principles and critical thinking skills. You may also need to demonstrate a knowledge of new technology. Engineers will require you to draw and test mechanical systems under different operating conditions.
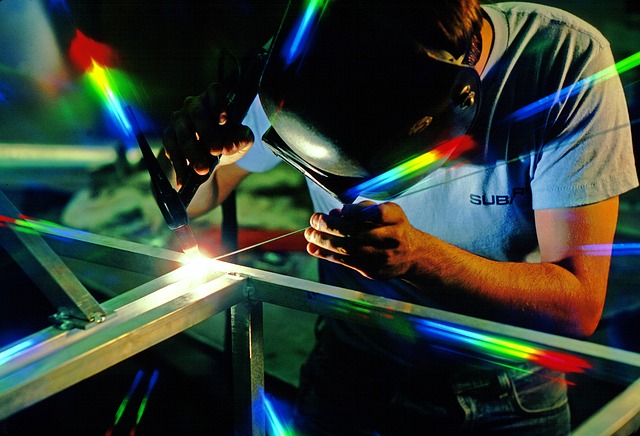
Quality control analysis, another essential component of a technician in mechanical engineering, is also important. In this process, engineers evaluate the performance of tool drawings by comparing the designs to the original specifications. Engineers may make design improvements or suggestions and then record the results. They may even submit the results to the engineering department.
While a mechanical engineering technician may have to spend a lot of time working alone, they will typically work regular hours. They may also be required to work overtime. They may work in a lab, research facility, or manufacturing plant. They may work a variety of hours and be exposed to potentially hazardous materials.
A mechanical engineering technician may also have to deal with hydraulics and other power systems. They will need to use power tools on a daily base and rigging equipment in order to meet the needs their customers.
FAQ
How does a Production Planner differ from a Project Manager?
A production planner is more involved in the planning phase of the project than a project manger.
What skills do production planners need?
A production planner must be organized, flexible, and able multitask to succeed. Effective communication with clients and colleagues is essential.
What is the job of a manufacturer manager?
Manufacturing managers must ensure that manufacturing processes are efficient, effective, and cost-effective. They should be aware of any issues within the company and respond accordingly.
They should also be able and comfortable communicating with other departments like sales and marketing.
They should also be knowledgeable about the latest trends in the industry so they can use this information for productivity and efficiency improvements.
What is the difference in Production Planning and Scheduling, you ask?
Production Planning (PP) is the process of determining what needs to be produced at any given point in time. This can be done by forecasting demand and identifying production capabilities.
Scheduling is the process that assigns dates to tasks so they can get completed within a given timeframe.
Statistics
- (2:04) MTO is a production technique wherein products are customized according to customer specifications, and production only starts after an order is received. (oracle.com)
- According to the United Nations Industrial Development Organization (UNIDO), China is the top manufacturer worldwide by 2019 output, producing 28.7% of the total global manufacturing output, followed by the United States, Japan, Germany, and India.[52][53] (en.wikipedia.org)
- According to a Statista study, U.S. businesses spent $1.63 trillion on logistics in 2019, moving goods from origin to end user through various supply chain network segments. (netsuite.com)
- In 2021, an estimated 12.1 million Americans work in the manufacturing sector.6 (investopedia.com)
- Many factories witnessed a 30% increase in output due to the shift to electric motors. (en.wikipedia.org)
External Links
How To
How to Use Lean Manufacturing in the Production of Goods
Lean manufacturing refers to a method of managing that seeks to improve efficiency and decrease waste. It was developed in Japan during the 1970s and 1980s by Taiichi Ohno, who received the Toyota Production System (TPS) award from TPS founder Kanji Toyoda. Michael L. Watkins published the original book on lean manufacturing, "The Machine That Changed the World," in 1990.
Lean manufacturing is often described as a set if principles that help improve the quality and speed of products and services. It emphasizes eliminating waste and defects throughout the value stream. Lean manufacturing is called just-in-time (JIT), zero defect, total productive maintenance (TPM), or 5S. Lean manufacturing emphasizes reducing non-value-added activities like inspection, rework and waiting.
Lean manufacturing not only improves product quality but also reduces costs. Companies can also achieve their goals faster by reducing employee turnover. Lean manufacturing is a great way to manage the entire value chain including customers, suppliers, distributors and retailers as well as employees. Lean manufacturing is widely practiced in many industries around the world. For example, Toyota's philosophy underpins its success in automobiles, electronics, appliances, healthcare, chemical engineering, aerospace, paper, food, etc.
Five fundamental principles underlie lean manufacturing.
-
Define Value - Identify the value your business adds to society and what makes you different from competitors.
-
Reduce waste - Get rid of any activity that does not add value to the supply chain.
-
Create Flow - Ensure work moves smoothly through the process without interruption.
-
Standardize & Simplify - Make processes as consistent and repeatable as possible.
-
Build relationships - Develop and maintain personal relationships with both your internal and external stakeholders.
Lean manufacturing isn’t new, but it has seen a renewed interest since 2008 due to the global financial crisis. Many companies have adopted lean manufacturing methods to increase their marketability. Some economists even believe that lean manufacturing can be a key factor in economic recovery.
With many benefits, lean manufacturing is becoming more common in the automotive industry. These include improved customer satisfaction, reduced inventory levels, lower operating costs, increased productivity, and better overall safety.
The principles of lean manufacturing can be applied in almost any area of an organization. Lean manufacturing is most useful in the production sector of an organisation because it ensures that each step in the value-chain is efficient and productive.
There are three main types of lean manufacturing:
-
Just-in-Time Manufacturing: Also known as "pull systems", this type of lean manufacturing uses just-in-time manufacturing (JIT). JIT means that components are assembled at the time of use and not manufactured in advance. This approach is designed to reduce lead times and increase the availability of components. It also reduces inventory.
-
Zero Defects Manufacturing: ZDM ensures that no defective units leave the manufacturing plant. It is better to repair a part than have it removed from the production line if it needs to be fixed. This is also true for finished products that require minor repairs before shipping.
-
Continuous Improvement (CI): CI aims to improve the efficiency of operations by continuously identifying problems and making changes in order to eliminate or minimize waste. Continuous improvement refers to continuous improvement of processes as well people and tools.