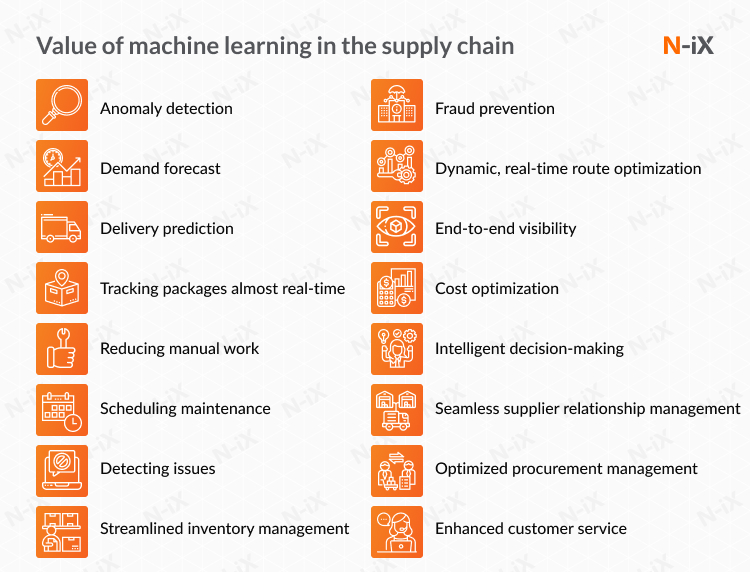
There are thousands more Connecticut manufacturing jobs that need to filled. There are currently 411 factories in Connecticut and 159,000 employees. The state's biggest contributor to the gross state production is manufacturing, which pays a higher than average salary. The Connecticut Business and Industry Association recently released a survey of manufacturing workforce needs. They found that 13,000 state-owned manufacturing jobs are not being filled, and that many companies struggle with younger workers.
Connecticut's manufacturing workforce tends to be older with one-third of its workers over 55. Many manufacturing companies have moved to lower labor costs. Others also started using new machinery, automation, and equipment. Manufacturing used to be dangerous and dirty. But, the reputation has improved. Today, there are many entry-level and apprenticeship positions offered by companies. Manufacturing is Connecticut's third largest job-creator. Its high-tech operations provide a competitive advantage.
Connecticut has a number of public and private education programs designed to help people become qualified for manufacturing jobs. Manufacturing Innovation Fund, which supports comprehensive high school, university, and vocational high school students, is one example. It also provides support for online training programs, preapprenticeships, as well career activities for K-12 student.
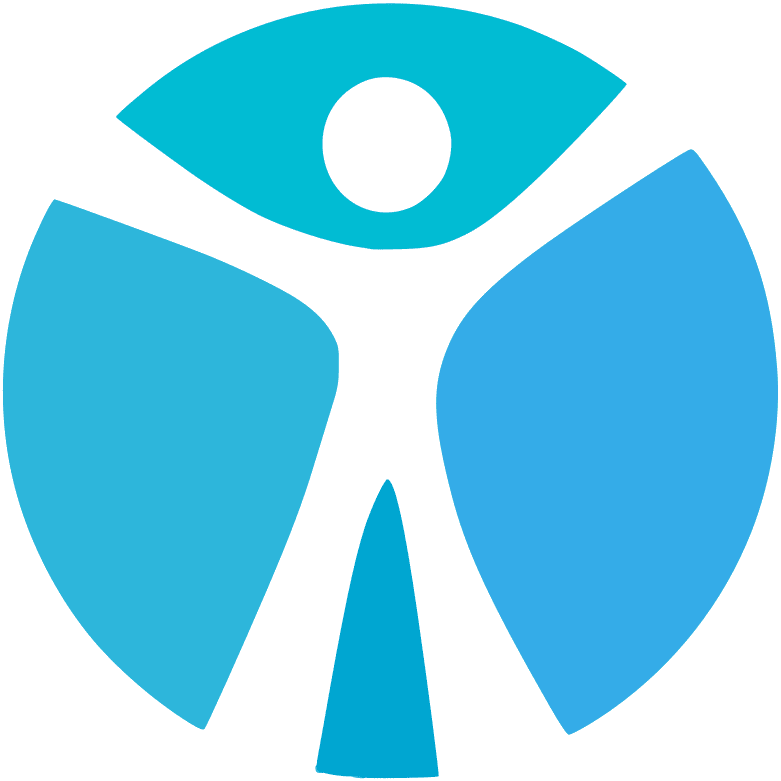
Advanced manufacturing workers come from a wide variety of backgrounds. Some are fresh out of highschool, while others have worked for years in a different field before moving to manufacturing. Some may have gone to school for a degree or have been in the military for many years. Many companies offer tuition reimbursements for advanced manufacturing training, as well as wage subsidies for entry-level training.
The state's Comprehensive High Schools have also begun reintroducing technical education options. One example is Grasso Tech's welding program. This program will be available starting in fall 2019. Employers that recruit through the EB would be interested in hiring students from Connecticut. The Eastern Connecticut Manufacturing Pipeline serves regional advanced manufacturing companies. It is modeled after Eastern Connecticut Workforce Investment Board’s Manufacturing Pipeline.
The Manufacturing Careers Program aims to help job-seekers who are interested manufacturing careers show their readiness for entry level jobs. This program matches pre-screened job candidates with employers and manufacturers. It also includes a CNC Basics class and provides a career path that is industry-infused. The Advanced Manufacturing Employer Partnership offers wage subsidies to entry-level training for those who enroll in the program.
Some young workers may not know much about the manufacturing industry. These people may not be aware of the importance of these programs and might find it difficult to take part in them. These programs are funded by the state with millions of dollars. The programs aren't as accessible because the young don't know they exist.
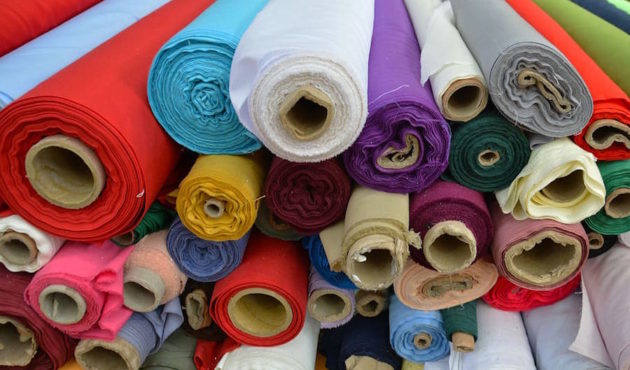
A statewide STEM Town initiative, which is an innovative approach to addressing Connecticut's manufacturing shortage, is one of the solutions. This would require reallocating resources and improving education programs in order to meet the needs for manufacturers.
FAQ
Why automate your warehouse?
Modern warehouses are increasingly dependent on automation. The rise of e-commerce has led to increased demand for faster delivery times and more efficient processes.
Warehouses need to adapt quickly to meet changing needs. Technology investment is necessary to enable warehouses to respond quickly to changing demands. The benefits of automating warehouses are numerous. Here are some benefits of investing in automation
-
Increases throughput/productivity
-
Reduces errors
-
Increases accuracy
-
Safety is boosted
-
Eliminates bottlenecks
-
Allows companies scale more easily
-
Makes workers more efficient
-
Gives you visibility into all that is happening in your warehouse
-
Enhances customer experience
-
Improves employee satisfaction
-
Reduces downtime and improves uptime
-
Ensures quality products are delivered on time
-
Eliminates human error
-
Helps ensure compliance with regulations
What are the 4 types of manufacturing?
Manufacturing refers to the transformation of raw materials into useful products by using machines and processes. It involves many different activities such as designing, building, testing, packaging, shipping, selling, servicing, etc.
What are the requirements to start a logistics business?
To be a successful businessman in logistics, you will need many skills and knowledge. You must have good communication skills to interact effectively with your clients and suppliers. You must be able analyze data and draw out conclusions. You will need to be able handle pressure well and work in stressful situations. To improve efficiency, you must be innovative and creative. You will need strong leadership skills to motivate and direct your team members towards achieving their organizational goals.
It is important to be organized and efficient in order to meet tight deadlines.
Are there any Manufacturing Processes that we should know before we can learn about Logistics?
No. No. But, being familiar with manufacturing processes will give you a better understanding about how logistics works.
What are manufacturing & logistics?
Manufacturing is the process of creating goods from raw materials by using machines and processes. Logistics covers all aspects involved in managing supply chains, including procurement and production planning. Manufacturing and logistics are often considered together as a broader term that encompasses both the process of creating products and delivering them to customers.
What are the responsibilities of a manufacturing manager
Manufacturing managers must ensure that manufacturing processes are efficient, effective, and cost-effective. They must also be alert to any potential problems and take appropriate action.
They should also be able communicate with other departments, such as sales or marketing.
They should be informed about industry trends and be able make use of this information to improve their productivity and efficiency.
What are the 7 Rs of logistics?
The acronym 7Rs of Logistics refers to the seven core principles of logistics management. It was developed by International Association of Business Logisticians (IABL), and published as part of their "Seven Principles of Logistics Management Series" in 2004.
The acronym is made up of the following letters:
-
Responsible - ensure that all actions taken are within legal requirements and are not harmful to others.
-
Reliable – have faith in your ability and capability to keep promises.
-
Be responsible - Use resources efficiently and avoid wasting them.
-
Realistic - Consider all aspects of operations, including environmental impact and cost effectiveness.
-
Respectful: Treat others with fairness and equity
-
Reliable - Find ways to save money and increase your productivity.
-
Recognizable provides value-added products and services to customers
Statistics
- You can multiply the result by 100 to get the total percent of monthly overhead. (investopedia.com)
- (2:04) MTO is a production technique wherein products are customized according to customer specifications, and production only starts after an order is received. (oracle.com)
- Many factories witnessed a 30% increase in output due to the shift to electric motors. (en.wikipedia.org)
- It's estimated that 10.8% of the U.S. GDP in 2020 was contributed to manufacturing. (investopedia.com)
- According to a Statista study, U.S. businesses spent $1.63 trillion on logistics in 2019, moving goods from origin to end user through various supply chain network segments. (netsuite.com)
External Links
How To
How to Use the Just In Time Method in Production
Just-in-time is a way to cut costs and increase efficiency in business processes. This is where you have the right resources at the right time. This means that you only pay the amount you actually use. Frederick Taylor, a 1900s foreman, first coined the term. He noticed that workers were often paid overtime when they had to work late. He concluded that if workers were given enough time before they start work, productivity would increase.
JIT is a way to plan ahead and make sure you don't waste any money. Also, you should look at the whole project from start-to-finish and make sure you have the resources necessary to address any issues. If you anticipate that there might be problems, you'll have enough people and equipment to fix them. You won't have to pay more for unnecessary items.
There are many JIT methods.
-
Demand-driven: This JIT is where you place regular orders for the parts/materials that are needed for your project. This will allow to track how much material has been used up. You'll also be able to estimate how long it will take to produce more.
-
Inventory-based: This allows you to store the materials necessary for your projects in advance. This allows you to predict how much you can expect to sell.
-
Project-driven : This is a method where you make sure that enough money is set aside to pay the project's cost. Once you have an idea of how much material you will need, you can purchase the necessary materials.
-
Resource-based JIT: This is the most popular form of JIT. You allocate resources based on the demand. You will, for example, assign more staff to deal with large orders. If you don’t have many orders you will assign less people to the work.
-
Cost-based: This is the same as resource-based except that you don't care how many people there are but how much each one of them costs.
-
Price-based: This is a variant of cost-based. However, instead of focusing on the individual workers' costs, this looks at the total price of the company.
-
Material-based: This is quite similar to cost-based, but instead of looking at the total cost of the company, you're concerned with how much raw materials you spend on average.
-
Time-based JIT: A variation on resource-based JIT. Instead of focusing solely on the amount each employee costs, focus on how long it takes for the project to be completed.
-
Quality-based JIT: This is another variation of resource based JIT. Instead of worrying about the costs of each employee or how long it takes for something to be made, you should think about how quality your product is.
-
Value-based: This is one of the newest forms of JIT. In this instance, you are not concerned about the product's performance or meeting customer expectations. Instead, you are focused on adding value to the marketplace.
-
Stock-based: This stock-based method focuses on the actual quantity of products being made at any given time. This is used to increase production and minimize inventory.
-
Just-intime planning (JIT), is a combination JIT/sales chain management. It refers to the process of scheduling the delivery of components as soon as they are ordered. It reduces lead times and improves throughput.