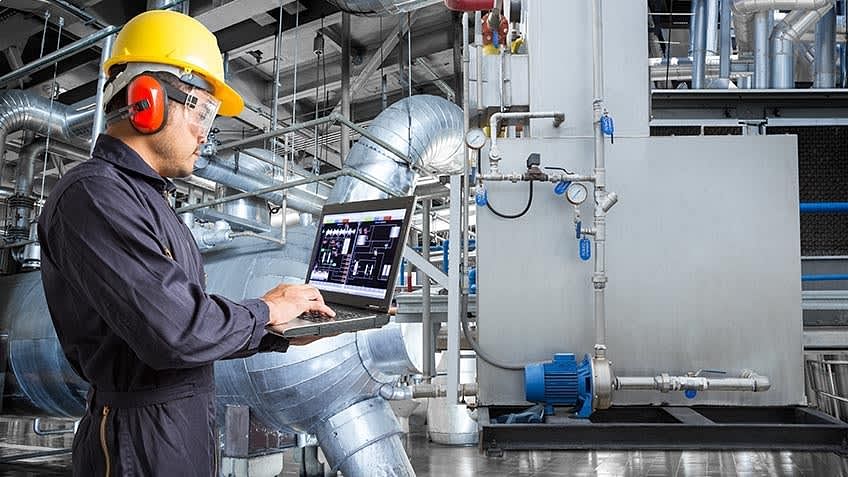
It doesn't matter if you're looking for work or are interested in earning a degree, it is important to understand how much you can make. The pay for industrial engineers can vary depending on what kind of degree you pursue, your industry and your experience. The average industrial engineer income is $95,300. But salaries can be higher in top-paying areas.
The job of an industrial engineer is to develop, design and install systems that improve the efficiency of production processes. They also develop ways to keep workplaces safer. Industrial engineers may also design equipment, plan facilities and analyze the specifications of products. This can be accomplished by assessing how design changes impact production costs.
Industrial engineers can earn a high salary if they have experience. With a master's level in industrial engineering, they may be eligible for a higher income. This degree is highly sought-after by international students. It can lead to a career within manufacturing, engineering services, and healthcare.
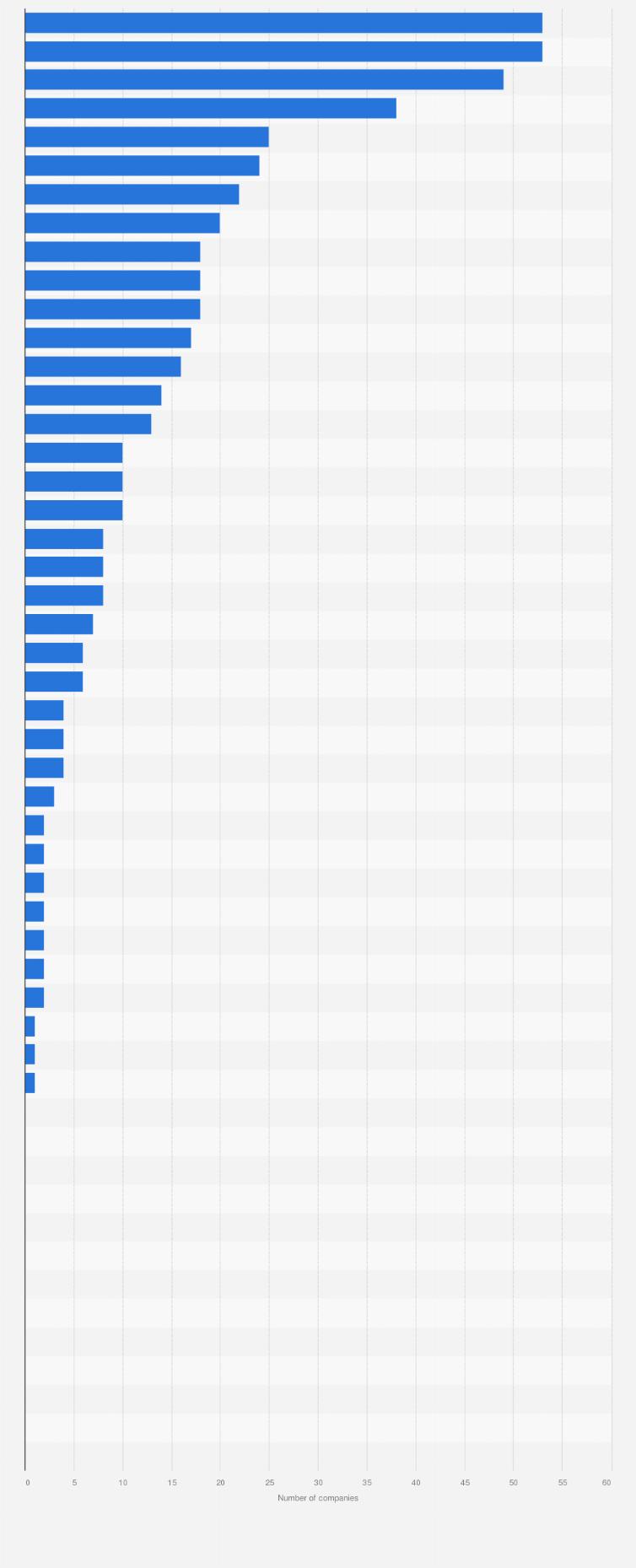
Also, industrial engineers will experience a high rate of employment growth over the next decade. The employment of industrial engineers is expected to rise 10 percent between 2021 and 2031. This is higher that the average for all occupations. The top 10 percent earn over $85,000 annually. With management experience, they are likely to earn more. Industrial engineers with advanced degrees are able to conduct cost-benefit studies, examine cost distribution in operations and negotiate for purchasing decision.
Industrial engineers have the ability to think outside of the box and find creative ways to make processes more efficient. Many industrial engineers are employed in offices. They can also interact with production workers. Industrial engineers can also handle telephone calls, emails and face-to–face conversations. They can also present their plans orally or in written reports.
Industrial engineers are expected to find work in a variety of industries, such as construction, pharmaceuticals, manufacturing, transportation, energy and utilities. Depending on which industry they work for, they might develop systems to reduce production waste.
A bachelor's degree is usually required for industrial engineers. A master's degree can be obtained in industrial engineering for a career as an engineer consultant or manufacturer. Many programs provide courses in general engineering, mathematics, science and general engineering. The program can take anywhere from two to seven to complete.
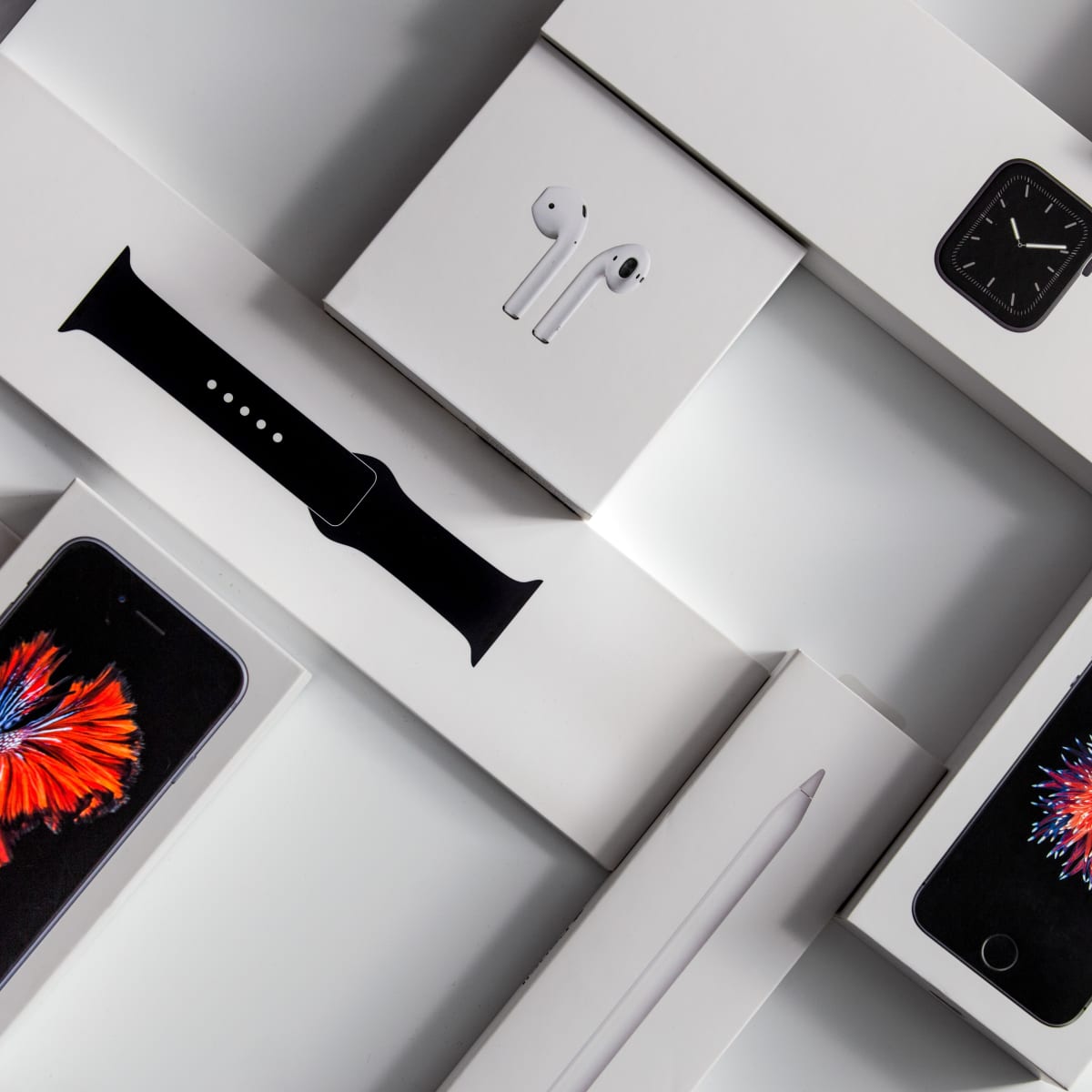
The average income for an entry-level industrialist is $65,000 - $75,000. However, it increases with experience. A salary for an experienced industrial engineering engineer is $86,809 per annum. An industrial engineer's annual salary can rise if they are awarded a masters or doctorate in the field.
Engineers need to be able to communicate well and have technical knowledge. They must be able think outside the box in order to solve problems. They should be able combine materials, equipment, workers and workers to create efficient solutions. They must have strong interpersonal skills. This job can be challenging but rewarding.
FAQ
How can I learn about manufacturing?
Practical experience is the best way of learning about manufacturing. But if that is not possible you can always read books and watch educational videos.
How is a production manager different from a producer planner?
The primary difference between a producer planner and a manager of a project is that the manager usually plans and organizes the whole project, while a production planner is only involved in the planning stage.
What does the term manufacturing industries mean?
Manufacturing Industries are businesses that produce products for sale. Consumers are the people who purchase these products. These companies employ many processes to achieve this purpose, such as production and distribution, retailing, management and so on. These companies produce goods using raw materials and other equipment. This includes all types of manufactured goods, including food items, clothing, building supplies, furniture, toys, electronics, tools, machinery, vehicles, pharmaceuticals, medical devices, chemicals, and many others.
Statistics
- You can multiply the result by 100 to get the total percent of monthly overhead. (investopedia.com)
- In the United States, for example, manufacturing makes up 15% of the economic output. (twi-global.com)
- According to a Statista study, U.S. businesses spent $1.63 trillion on logistics in 2019, moving goods from origin to end user through various supply chain network segments. (netsuite.com)
- In 2021, an estimated 12.1 million Americans work in the manufacturing sector.6 (investopedia.com)
- Many factories witnessed a 30% increase in output due to the shift to electric motors. (en.wikipedia.org)
External Links
How To
How to Use 5S for Increasing Productivity in Manufacturing
5S stands for "Sort", "Set In Order", "Standardize", "Separate" and "Store". Toyota Motor Corporation invented the 5S strategy in 1954. It improves the work environment and helps companies to achieve greater efficiency.
This method aims to standardize production processes so that they are repeatable, measurable and predictable. This means that every day tasks such cleaning, sorting/storing, packing, and labeling can be performed. Workers can be more productive by knowing what to expect.
Implementing 5S involves five steps: Sort, Set in Order, Standardize Separate, Store, and Each step requires a different action, which increases efficiency. If you sort items, it makes them easier to find later. Once you have placed items in an ordered fashion, you will put them together. Next, organize your inventory into categories and store them in containers that are easily accessible. Labeling your containers will ensure that everything is correctly labeled.
Employees must be able to critically examine their work practices. Employees must be able to see why they do what they do and find a way to achieve them without having to rely on their old methods. They will need to develop new skills and techniques in order for the 5S system to be implemented.
The 5S method increases efficiency and morale among employees. As they begin to see improvements, they feel motivated to continue working towards the goal of achieving higher levels of efficiency.