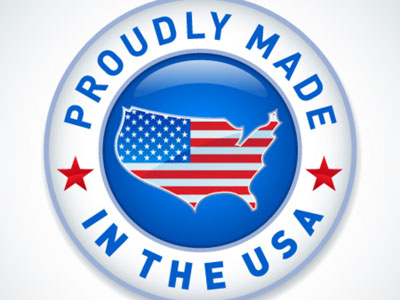
Both part-time and full time logistics jobs are available at the federal and state levels. There are many advantages to working in these jobs. They provide stable income, excellent benefits, and a good income. Government careers can also be a great way to obtain experience in the industry.
A Logistics Management Specialist, for example, is responsible for coordinating the supply chain. They monitor deliveries, manage contracts and perform audits. They are also responsible for identifying supply chain issues and creating contingency plan. You will need to have strong communication skills, good typing skills, and knowledge about government procurement regulations.
Supply Chain Managers can either work for the Department of Veterans Affairs (DVA) or the Department of Homeland Security. For the former, you will need to have a thorough understanding of federal procurement regulations. The latter requires knowledge in managing logistics operations and sourcing supplies. Candidates are required to hold a bachelor's level or higher depending on the job. Candidates should also be familiar with the regulations and business culture in the state they are applying for. Certain positions may require security clearances. In these cases, a background check may be necessary.
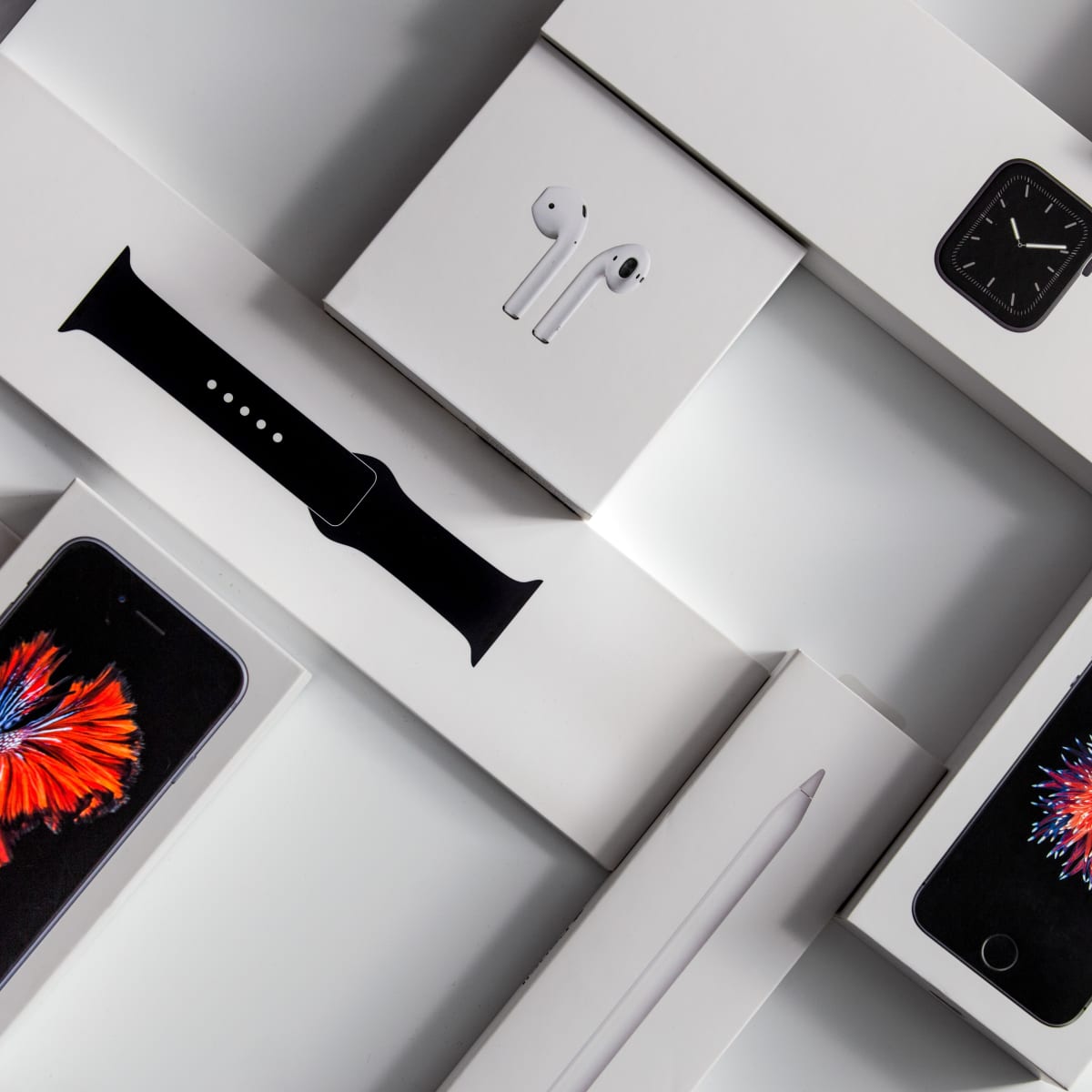
Another job for government logistics specialists is to quickly deploy materials after an emergency. A distribution role in disaster logistics is offered by the North Carolina Department of Public Safety. Candidates must have at least four years' experience in the relevant field. Candidates must be able to manage a team of people and work in stressful situations.
The departmental level also requires Logistics Management Specialists. The typical logistics management specialist role closely resembles that of the Federal Aviation Administration. The qualifications include an advanced degree, specialized knowledge in operations or project managing, and a background of logistics management.
You'll need to have the ability to handle large volumes of international travel if your goal is to become a government logistics manager. Additionally, you will need to have some experience managing procurement negotiations and making bids for suppliers. Candidates must have at minimum two years relevant experience.
You can also apply for a variety other supply chain management roles in the federal government. Those positions are in the areas of air transport, road transport, warehousing, and distribution. Nearly 25% of these positions are offered through the federal government. Eight percent are offered via the states.
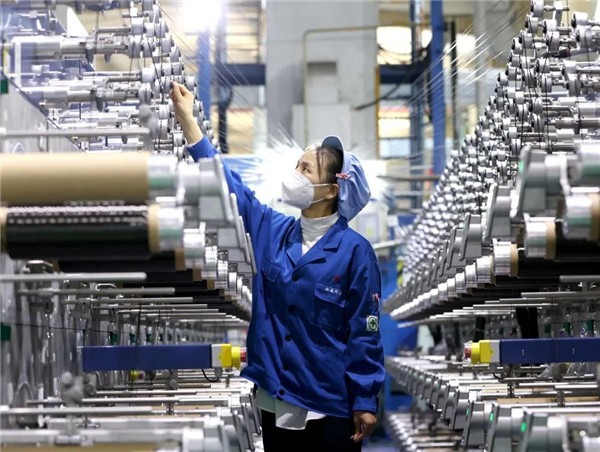
Several jobs can be found by browsing the federal government's website, USAJOBS. You can also search based on title and degree type. Most of these positions require at least a bachelor's degree, though some of them may require a master's. You can also find jobs as supply chain specialists in smaller organizations. For most supply chain professionals, a minimum of one year of specialized work experience is required before they can apply to a position.
Data scientists can choose from a variety of positions. Data Scientists assist with the development of strategic plans as well as supporting government programs.
FAQ
How can we improve manufacturing efficiency?
First, identify the factors that affect production time. We must then find ways that we can improve these factors. If you aren't sure where to begin, think about the factors that have the greatest impact on production time. Once you have identified them, it is time to identify solutions.
How can manufacturing avoid production bottlenecks
Production bottlenecks can be avoided by ensuring that processes are running smoothly during the entire production process, starting with the receipt of an order and ending when the product ships.
This includes planning for both capacity requirements and quality control measures.
Continuous improvement techniques like Six Sigma are the best way to achieve this.
Six Sigma management is a system that improves quality and reduces waste within your organization.
It seeks to eliminate variation and create consistency in your work.
What is the job of a logistics manger?
Logistics managers ensure that goods arrive on time and are unharmed. This is accomplished by using the experience and knowledge gained from working with company products. He/she should also ensure enough stock is available to meet demand.
How can excess manufacturing production be reduced?
In order to reduce excess production, you need to develop better inventory management methods. This would reduce the time spent on unproductive activities like purchasing, storing and maintaining excess stock. This would allow us to use our resources for more productive tasks.
Kanban systems are one way to achieve this. A Kanban board is a visual display used to track work in progress. Work items are moved through various states to reach their destination in a Kanban system. Each state represents an individual priority level.
As an example, if work is progressing from one stage of the process to another, then the current task is complete and can be transferred to the next. But if a task remains in the beginning stages it will stay that way until it reaches its end.
This helps to keep work moving forward while ensuring that no work is left behind. Managers can monitor the work being done by Kanban boards to see what is happening at any given time. This allows them the ability to adjust their workflow using real-time data.
Lean manufacturing can also be used to reduce inventory levels. Lean manufacturing seeks to eliminate waste from every step of the production cycle. Anything that does nothing to add value to a product is waste. Here are some examples of common types.
-
Overproduction
-
Inventory
-
Unnecessary packaging
-
Material surplus
Manufacturers can reduce their costs and improve their efficiency by using these ideas.
How is a production manager different from a producer planner?
The major difference between a Production Planner and a Project Manager is that a Project Manager is often the person responsible for organizing and planning the entire project. While a Production Planner is involved mainly in the planning stage,
What are the four types in manufacturing?
Manufacturing is the process that transforms raw materials into useful products. It involves many different activities such as designing, building, testing, packaging, shipping, selling, servicing, etc.
What does it take for a logistics enterprise to succeed?
To be a successful businessman in logistics, you will need many skills and knowledge. To communicate effectively with clients and suppliers, you must be able to communicate well. You need to understand how to analyze data and draw conclusions from it. You will need to be able handle pressure well and work in stressful situations. To increase efficiency and creativity, you need to be creative. You will need strong leadership skills to motivate and direct your team members towards achieving their organizational goals.
You must be organized to meet tight deadlines.
Statistics
- You can multiply the result by 100 to get the total percent of monthly overhead. (investopedia.com)
- (2:04) MTO is a production technique wherein products are customized according to customer specifications, and production only starts after an order is received. (oracle.com)
- Many factories witnessed a 30% increase in output due to the shift to electric motors. (en.wikipedia.org)
- According to the United Nations Industrial Development Organization (UNIDO), China is the top manufacturer worldwide by 2019 output, producing 28.7% of the total global manufacturing output, followed by the United States, Japan, Germany, and India.[52][53] (en.wikipedia.org)
- [54][55] These are the top 50 countries by the total value of manufacturing output in US dollars for its noted year according to World Bank.[56] (en.wikipedia.org)
External Links
How To
Six Sigma and Manufacturing
Six Sigma is defined by "the application SPC (statistical process control) techniques to achieve continuous improvements." Motorola's Quality Improvement Department created Six Sigma at their Tokyo plant, Japan in 1986. Six Sigma's basic concept is to improve quality and eliminate defects through standardization. Many companies have adopted this method in recent years. They believe there is no such thing a perfect product or service. Six Sigma's primary goal is to reduce variation from the average value of production. If you take a sample and compare it with the average, you will be able to determine how much of the production process is different from the norm. If this deviation is too big, you know something needs fixing.
Understanding the dynamics of variability within your business is the first step in Six Sigma. Once you've understood that, you'll want to identify sources of variation. It is important to identify whether the variations are random or systemic. Random variations are caused when people make mistakes. While systematic variations are caused outside of the process, they can occur. You could consider random variations if some widgets fall off the assembly lines. You might notice that your widgets always fall apart at the same place every time you put them together.
Once you have identified the problem, you can design solutions. It might mean changing the way you do business or redesigning it entirely. After implementing the new changes, you should test them again to see if they worked. If they don't work you need to rework them and come up a better plan.