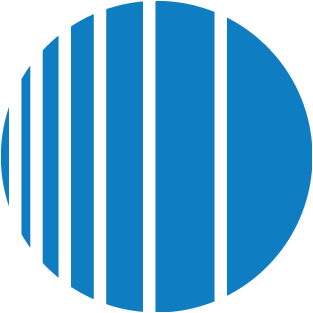
DMAIC is an improvement model that consists of five steps. They are: Define Measure Analyze Improve Control. Six Sigma professionals use it to improve quality in an organization, but you can implement this process independently.
Dmaic is a quality methodology that aims to reduce defects, cost and rework. It is an established method to ensure high-quality products that are consistent and efficient.
DMAIC can be an effective way to resolve issues within a company. It can also be used to improve processes that impact customer satisfaction, quality of products, cost reductions and cycle times. This is a key component of any quality improvement programme.
The DMAIC is a structured method of problem solving that helps organizations eliminate the root causes behind a particular issue. The DMAIC method is a systematic approach with a topdown approach. It helps teams make foolproof and data driven changes.
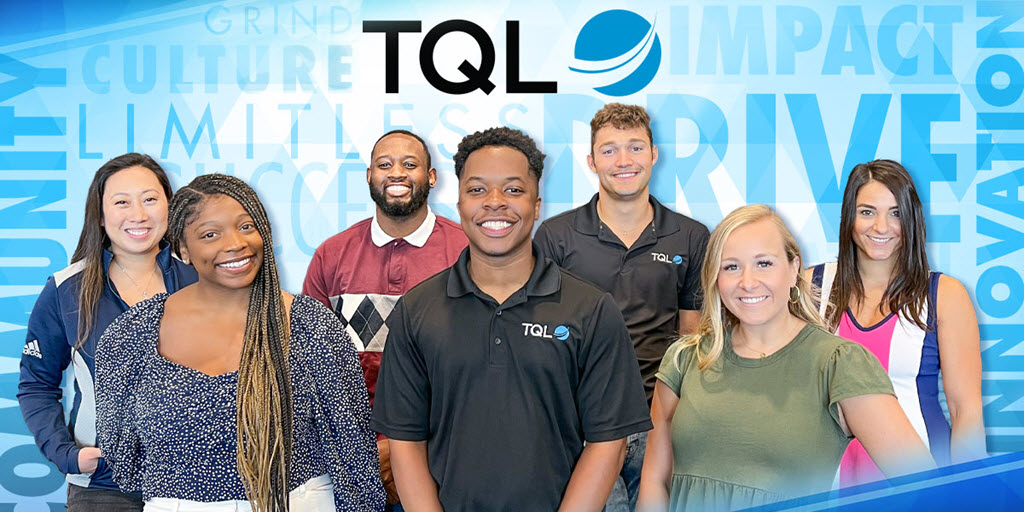
It's a powerful tool for Lean Six Sigma, because it gives teams an organized and well-defined path to take to fix and find quality issues. This is especially true for complex problems, with unclear origins and high risks of inaction.
It is important that you understand the criteria before selecting a DMAIC. It's also important to be aware of the tools available during this process. These include fishbone charts and Pareto chart.
Once you have identified the project's needs and goals, you can then begin the DMAIC method. You should select projects that reflect the current state of your business and meet DMAIC's criteria.
The Define phase of DMAIC involves clearly defining the problem that needs to be addressed and the scope of the improvement. This can either be a formal charter for the project or it can also take a more informal form. This document defines the CTQ issues, core business processes involved, and scope of work.
This step is important in the DMAIC procedure because it enables the team to understand what needs to be done first, and what metrics should be used to track their success. It also helps teams to find their DMAIC champion and sets the stage for success.
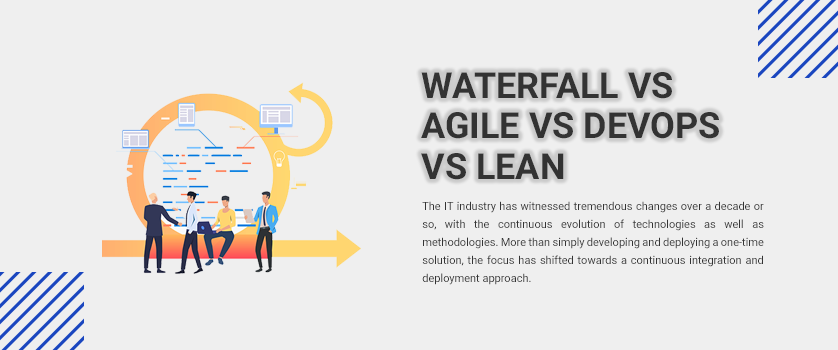
In the Measurement phase, teams collect the data and compare it with the goal state. The teams then use the information they have collected to identify gaps between two states and opportunities for improvement. This can be achieved by implementing different tools such as frequency plots, scatterplots or statistical analyses.
After analyzing the data, teams identify potential solutions to the problem and test them to make sure they are working. They also implement and verify that results are measurable.
FAQ
What's the difference between Production Planning & Scheduling?
Production Planning (PP), or production planning, is the process by which you determine what products are needed at any given time. Forecasting and identifying production capacity are two key elements to this process.
Scheduling is the process that assigns dates to tasks so they can get completed within a given timeframe.
What does warehouse mean?
A warehouse is a place where goods are stored until they are sold. It can be an indoor space or an outdoor area. In some cases, it may be a combination of both.
What are the responsibilities for a manufacturing manager
The manufacturing manager should ensure that every manufacturing process is efficient and effective. They should be aware of any issues within the company and respond accordingly.
They should also be able and comfortable communicating with other departments like sales and marketing.
They should be informed about industry trends and be able make use of this information to improve their productivity and efficiency.
What is the role of a production manager?
A production planner makes sure all project elements are delivered on schedule, within budget, as well as within the agreed scope. They also ensure that the product/service meets the client’s needs.
What is production planning?
Production Planning includes planning for all aspects related to production. This document is designed to make sure everything is ready for when you're ready to shoot. This document should include information about how to achieve the best results on-set. This information includes locations, crew details and equipment requirements.
First, you need to plan what you want to film. You may have decided where to shoot or even specific locations you want to use. Once you've identified the locations and scenes you want to use, you can begin to plan what elements you need for each scene. You might decide you need a car, but not sure what make or model. This is where you can look up car models online and narrow down your options by choosing from different makes and models.
After you have selected the car you want, you can begin to think about additional features. Do you have people who need to be seated in the front seat? Maybe you need someone to move around in the back. Perhaps you would like to change the interior colour from black to white. These questions will help to determine the style and feel of your car. The type of shots that you are looking for is another thing to consider. Do you want to film close-ups, or wider angles? Maybe you want to show the engine and the steering wheel. All of these things will help you identify the exact style of car you want to film.
Once you have made all the necessary decisions, you can start to create a schedule. A schedule will tell you when you need to start shooting and when you need to finish. Every day will have a time for you to arrive at the location, leave when you are leaving and return home when you are done. Everyone knows exactly what they should do and when. It is possible to make arrangements in advance for additional staff if you are looking to hire. There is no point in hiring someone who won't turn up because you didn't let him know.
When creating your schedule, you will also need to consider the number of days you need to film. Some projects are quick and easy, while others take weeks. When creating your schedule, be aware of whether you need more shots per day. Multiple shots at the same location can increase costs and make it more difficult to complete. You can't be certain if you will need multiple takes so it is better not to shoot too many.
Budget setting is an important part of production planning. As it will allow you and your team to work within your financial means, setting a realistic budget is crucial. Remember that you can always reduce the budget later on if you run into unforeseen problems. However, you shouldn't overestimate the amount of money you will spend. If you underestimate how much something costs, you'll have less money to pay for other items.
Production planning is a very detailed process, but once you understand how everything works together, it becomes easier to plan future projects.
How can overproduction in manufacturing be reduced?
In order to reduce excess production, you need to develop better inventory management methods. This would reduce the amount of time spent on unnecessary activities such as purchasing, storing, and maintaining excess stock. By doing this, we could free up resources for other productive tasks.
Kanban systems are one way to achieve this. A Kanban board is a visual display used to track work in progress. A Kanban system allows work items to move through several states before reaching their final destination. Each state represents a different priority level.
To illustrate, work can move from one stage or another when it is complete enough for it to be moved to a new stage. If a task is still in its beginning stages, it will continue to be so until it reaches the end.
This allows for work to continue moving forward, while also ensuring that there is no work left behind. Managers can see how much work has been done and the status of each task at any time with a Kanban Board. This information allows them to adjust their workflow based on real-time data.
Lean manufacturing is another option to control inventory levels. Lean manufacturing is about eliminating waste from all stages of the production process. Any product that isn't adding value can be considered waste. These are some of the most common types.
-
Overproduction
-
Inventory
-
Unnecessary packaging
-
Material surplus
Manufacturers can reduce their costs and improve their efficiency by using these ideas.
Statistics
- It's estimated that 10.8% of the U.S. GDP in 2020 was contributed to manufacturing. (investopedia.com)
- Job #1 is delivering the ordered product according to specifications: color, size, brand, and quantity. (netsuite.com)
- According to a Statista study, U.S. businesses spent $1.63 trillion on logistics in 2019, moving goods from origin to end user through various supply chain network segments. (netsuite.com)
- Many factories witnessed a 30% increase in output due to the shift to electric motors. (en.wikipedia.org)
- You can multiply the result by 100 to get the total percent of monthly overhead. (investopedia.com)
External Links
How To
How to use the Just-In Time Method in Production
Just-in-time is a way to cut costs and increase efficiency in business processes. It allows you to get the right amount resources at the right time. This means that only what you use is charged to your account. Frederick Taylor developed the concept while working as foreman in early 1900s. He noticed that workers were often paid overtime when they had to work late. He decided to ensure workers have enough time to do their jobs before starting work to improve productivity.
JIT is an acronym that means you need to plan ahead so you don’t waste your money. The entire project should be looked at from start to finish. You need to ensure you have enough resources to tackle any issues that might arise. You'll be prepared to handle any potential problems if you know in advance. This will ensure that you don't spend more money on things that aren't necessary.
There are many types of JIT methods.
-
Demand-driven JIT: This is a JIT that allows you to regularly order the parts/materials necessary for your project. This will let you track the amount of material left over after you've used it. You'll also be able to estimate how long it will take to produce more.
-
Inventory-based: This is a type where you stock the materials required for your projects in advance. This allows you to forecast how much you will sell.
-
Project-driven: This is an approach where you set aside enough funds to cover the cost of your project. When you know how much you need, you'll purchase the appropriate amount of materials.
-
Resource-based JIT : This is probably the most popular type of JIT. You allocate resources based on the demand. For example, if there is a lot of work coming in, you will have more people assigned to them. If you don’t have many orders you will assign less people to the work.
-
Cost-based: This is similar to resource-based, except that here you're not just concerned about how many people you have but how much each person costs.
-
Price-based: This approach is very similar to the cost-based method except that you don't look at individual workers costs but the total cost of the company.
-
Material-based is an alternative to cost-based. Instead of looking at the total cost in the company, this method focuses on the average amount of raw materials that you consume.
-
Time-based: Another variation of resource-based JIT. Instead of worrying about how much each worker costs, you can focus on how long the project takes.
-
Quality-based JIT is another variant of resource-based JIT. Instead of looking at the labor costs and time it takes to make a product, think about its quality.
-
Value-based JIT: This is the latest form of JIT. In this case, you're not concerned with how well the products perform or whether they meet customer expectations. Instead, you're focused on how much value you add to the market.
-
Stock-based. This method is inventory-based and focuses only on the actual production at any given point. This method is useful when you want to increase production while decreasing inventory.
-
Just-intime planning (JIT), is a combination JIT/sales chain management. It is the process of scheduling components' delivery as soon as they have been ordered. It's important because it reduces lead times and increases throughput.