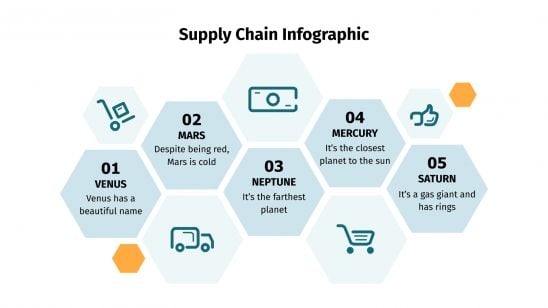
Introducing kaizen into manufacturing processes may not be as easy as some may imagine. This slow process requires inventory to be ordered and everyone must be present. The amount of time needed to improve the manufacturing process depends on the level of participation, the problem area, and the firm. Follow the correct implementation methods and obtain the resources you need to ensure your manufacturing process improvement project is a success. For this strategy to be successful, it is important to establish a strong company culture encouraging continuous improvement.
Creating a culture in the company that is focused on improving
Gallup polls found that 32% of Americans are not engaged in their work. 17.2% of these employees were actively disengaged. Kaizen culture promotes employee engagement. It will help improve processes, decrease turnover, and encourage innovation. Engaged employees will be more open to new ideas and innovative thinking, which leads to increased productivity and customer satisfaction. Kaizen culture has many benefits beyond reducing waste and increasing productivity.
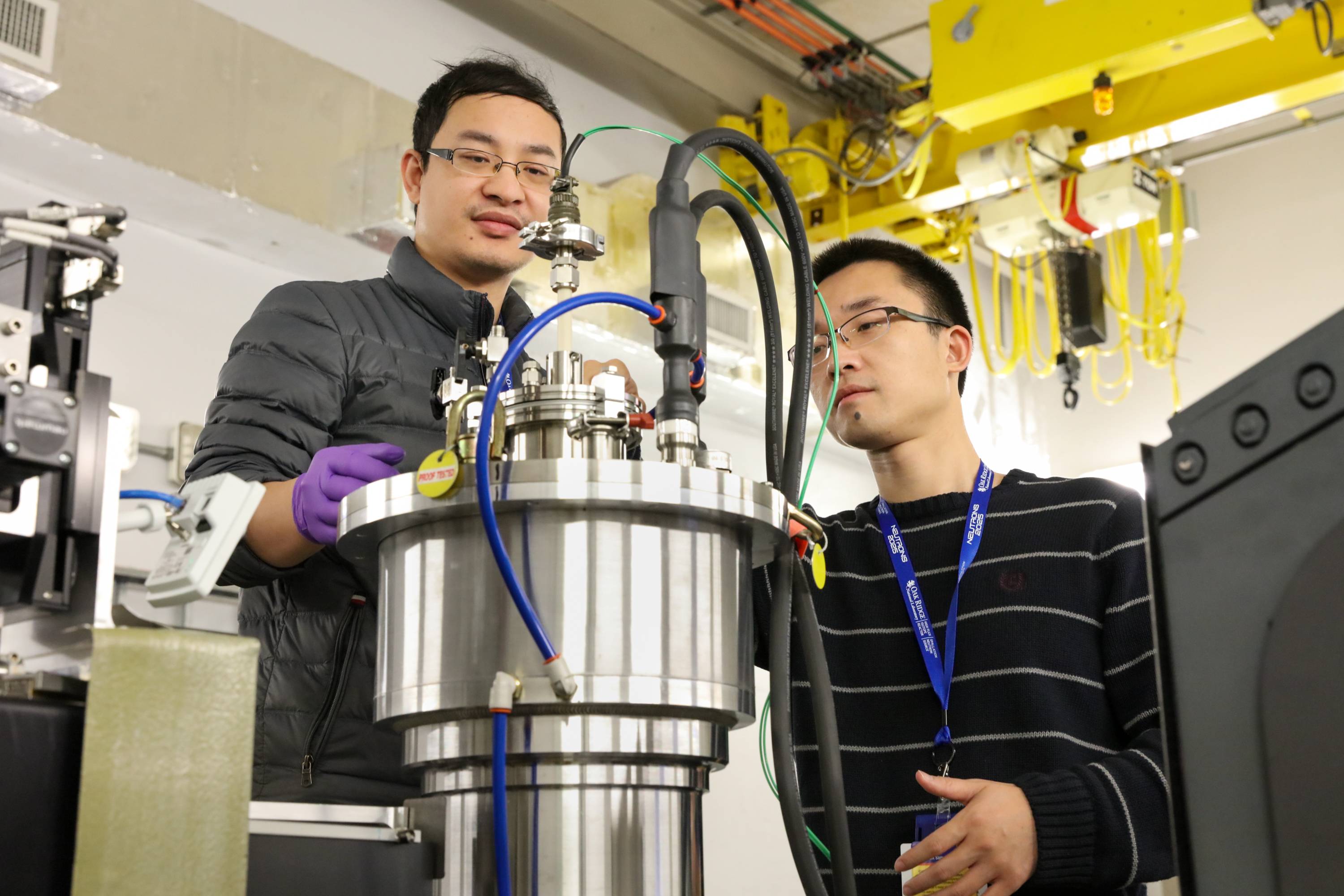
Kaizen stands for continuous improvement in all aspects of a company's business. Rather than making big, sweeping changes that have little to no benefit, Kaizen is a method of incremental improvement. When implemented correctly, Kaizen processes can lead to lower costs, increased productivity, improved quality, and improved customer satisfaction. The philosophy is also effective in improving employee morale and communication.
Implementing kaizen in manufacturing is difficult
While the benefits of implementing kaizen are many, they also have some disadvantages. First, implementing kaizen requires significant changes in a business's management system. It is possible to make the changes again after they have been implemented. Second, many businesses have difficulty changing their work habits, which can be a barrier in implementing kaizen.
Another problem is the fact that many manufacturers work in a "feast or framine" cycle. Machine shops will have trouble if they are unable to find qualified workers and the demand for their product drops. In this situation, the machine shop will need to cut back on employees and close its doors. Implementing kaizen, which is continuous improvement, can help these machine shops steer clear of the "feast/famine" cycle. Implementing kaizen will increase a shop's efficiency and allow it to produce more products.
High success rate in kaizen implementation during manufacturing
Statistics show that the success rate of Kaizen implementation in the manufacturing sector is relatively low. Only 10% percent of manufacturing companies have reported positive Kaizen outcomes. However, this doesn't mean that implementation is futile. Implementing kaizen is an essential component of the lean manufacturing process. Here are some tips to increase your manufacturing business's success rate:
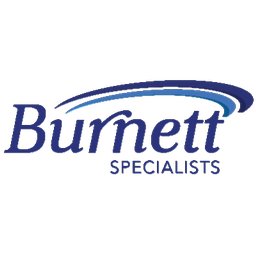
Understanding the state of the world is essential to kaizen. To identify the most important priorities, data must be collected and analyzed during the first step. Then, improvements are tested and verified by doing a before-and-after comparison. The benefit-to–cost analysis can be used to evaluate the effect of any improvement or the entire process. It is important to track the results over 60-90 day to determine the program's effectiveness.
FAQ
Why is logistics important in manufacturing
Logistics are an essential component of any business. They are essential to any business's success.
Logistics plays a significant role in reducing cost and increasing efficiency.
What makes a production planner different from a project manger?
The major difference between a Production Planner and a Project Manager is that a Project Manager is often the person responsible for organizing and planning the entire project. While a Production Planner is involved mainly in the planning stage,
What does it take to run a logistics business?
You need to have a lot of knowledge and skills to manage a successful logistic business. Good communication skills are essential to effectively communicate with your suppliers and clients. You should be able analyse data and draw inferences. You need to be able work under pressure and manage stressful situations. You must be creative and innovative to develop new ideas to improve efficiency. You need to have strong leadership qualities to motivate team members and direct them towards achieving organizational goals.
It is also important to be efficient and well organized in order meet deadlines.
What is the difference between Production Planning and Scheduling?
Production Planning (PP), or production planning, is the process by which you determine what products are needed at any given time. This is done through forecasting demand and identifying production capacities.
Scheduling is the process of assigning specific dates to tasks so they can be completed within the specified timeframe.
Do we need to know about Manufacturing Processes before learning about Logistics?
No. It doesn't matter if you don't know anything about manufacturing before you learn about logistics. Understanding the manufacturing process will allow you to better understand logistics.
What are the 4 types manufacturing?
Manufacturing is the process that transforms raw materials into useful products. It can involve many activities like designing, manufacturing, testing packaging, shipping, selling and servicing.
Statistics
- Job #1 is delivering the ordered product according to specifications: color, size, brand, and quantity. (netsuite.com)
- According to the United Nations Industrial Development Organization (UNIDO), China is the top manufacturer worldwide by 2019 output, producing 28.7% of the total global manufacturing output, followed by the United States, Japan, Germany, and India.[52][53] (en.wikipedia.org)
- [54][55] These are the top 50 countries by the total value of manufacturing output in US dollars for its noted year according to World Bank.[56] (en.wikipedia.org)
- In 2021, an estimated 12.1 million Americans work in the manufacturing sector.6 (investopedia.com)
- (2:04) MTO is a production technique wherein products are customized according to customer specifications, and production only starts after an order is received. (oracle.com)
External Links
How To
How to Use Lean Manufacturing for the Production of Goods
Lean manufacturing is a management style that aims to increase efficiency and reduce waste through continuous improvement. It was first developed in Japan in the 1970s/80s by Taiichi Ahno, who was awarded the Toyota Production System (TPS), award from KanjiToyoda, the founder of TPS. Michael L. Watkins published the "The Machine That Changed the World", the first book about lean manufacturing. It was published in 1990.
Lean manufacturing can be described as a set or principles that are used to improve quality, speed and cost of products or services. It emphasizes reducing defects and eliminating waste throughout the value chain. Lean manufacturing is called just-in-time (JIT), zero defect, total productive maintenance (TPM), or 5S. Lean manufacturing seeks to eliminate non-value added activities, such as inspection, work, waiting, and rework.
Lean manufacturing improves product quality and costs. It also helps companies reach their goals quicker and decreases employee turnover. Lean Manufacturing is one of the most efficient ways to manage the entire value chains, including suppliers and customers as well distributors and retailers. Lean manufacturing is widely practiced in many industries around the world. Toyota's philosophy has been a key driver of success in many industries, including automobiles and electronics.
Five principles are the basis of lean manufacturing:
-
Define Value- Identify the added value your company brings to society. What makes you stand out from your competitors?
-
Reduce Waste - Remove any activity which doesn't add value to your supply chain.
-
Create Flow - Make sure work runs smoothly without interruptions.
-
Standardize and Simplify – Make processes as consistent, repeatable, and as simple as possible.
-
Develop Relationships: Establish personal relationships both with internal and external stakeholders.
Lean manufacturing is not a new concept, but it has been gaining popularity over the last few years due to a renewed interest in the economy following the global financial crisis of 2008. Many businesses have adopted lean production techniques to make them more competitive. Many economists believe lean manufacturing will play a major role in economic recovery.
Lean manufacturing has many benefits in the automotive sector. These include higher customer satisfaction levels, reduced inventory levels as well as lower operating costs.
It can be applied to any aspect of an organisation. Because it makes sure that all value chains are efficient and effectively managed, Lean Manufacturing is particularly helpful for organizations.
There are three types of lean manufacturing.
-
Just-in Time Manufacturing: This lean manufacturing method is commonly called "pull systems." JIT is a method in which components are assembled right at the moment of use, rather than being manufactured ahead of time. This approach is designed to reduce lead times and increase the availability of components. It also reduces inventory.
-
Zero Defects Manufacturing - ZDM: ZDM focuses its efforts on making sure that no defective units leave a manufacturing facility. If a part is required to be repaired on the assembly line, it should not be scrapped. This is true even for finished products that only require minor repairs prior to shipping.
-
Continuous Improvement (CI), also known as Continuous Improvement, aims at improving the efficiency of operations through continuous identification and improvement to minimize or eliminate waste. Continuous improvement involves continuous improvement of processes and people as well as tools.