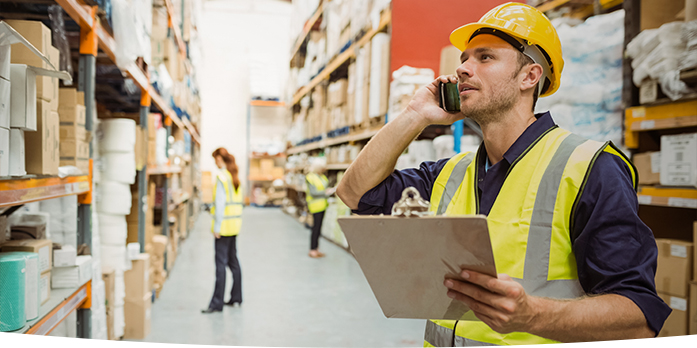
It can help improve your manufacturing processes. However, it is not an easy task. This involves mapping product families and their products. To do it properly, your team needs training, and you might even have a value stream manager. You should also get buy-in from the leadership, so that your team can implement the strategy. Larger companies often have their own value stream managers who oversee the mapping process. While smaller companies can get by without a VSM manager, it can be beneficial to show the leadership the improvements that can be made.
Lean Six Sigma
Value Stream Mapping in Lean Six Sigma will allow you to document the flow information from customers to suppliers. Your customer should be the first thing on your value stream map. Start at the shipping point and work your way upstream. Include a box with customer data. This will let you know how often products must be produced to meet demand. You'll also need to know the Takt time (the amount of time it takes to produce a product), and how it compares to the cycle time of the product. A bottleneck is when Takt time exceeds the cycle time.
Value Stream Maps help companies identify waste at all stages of their operations. Value stream mapping is a way to identify non-value-added activities, analyze the flow of information and identify threats and opportunities in your business. It can also be used to identify bottlenecks and determine where improvements can made to improve efficiency. The benefits of using Value Stream Mapping in Lean Six Sigma go beyond simply improving the flow of information - a Value Stream Map can be a valuable tool in helping you implement Lean Six Sigma and improve your bottom line.
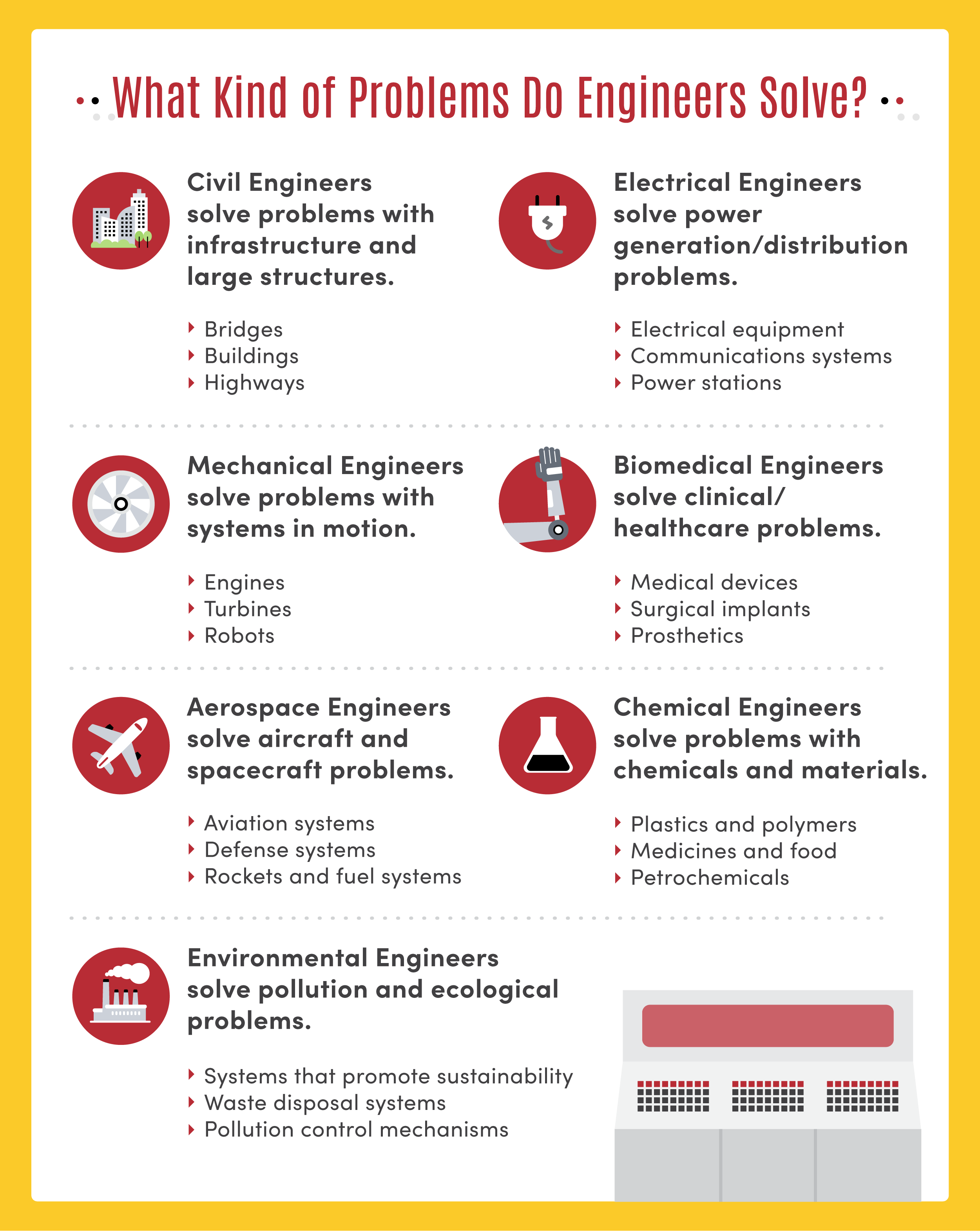
Lean Healthcare
Value stream mapping is a tool that helps improve the coordination of activities in medical fields. It helps to identify areas of improvement and provides strategies for implementation. A map might show a patient’s flow from the time they arrive at the hospital up to the time they leave after their treatment. By visualizing these flow paths, you can create a timeline for the whole process and identify value-added activities and waste-generating steps.
The authors recommend creating clear definitions of terms and phrases to help make VSM in Lean Healthcare better. They also recommend establishing appropriate indicators and sharing examples of success and failure. These will allow the results to be replicated and modified for specific situations. Healthcare sector lean methods are more likely produce positive outcomes. This methodology can be used to improve the quality of healthcare. The authors suggest that everyone agree on the definition of value stream mapping.
Lean Manufacturing
To begin implementing value stream mapping, it is important to gather input from key stakeholders within a process. This group should include those responsible for meeting customer needs. They should also include people who perform critical tasks and activities to ensure the flow of information. This value stream mapping process can be used to identify waste and increase efficiency by gathering input from key stakeholders. Before you begin, it is important to define the scope and purpose of the value stream mapping process.
Next, identify the product/process you wish to improve. Then, train your team on value stream mapping. The mapping process begins with customer needs. It includes everything from when the customer is contacted to the decision making and communication that follows. Value stream mapping seeks to eliminate waste, make the process more efficient, and improve customer satisfaction. Lean manufacturing, which identifies the factors that affect customer satisfaction and removes them, can be a viable and sustainable solution to the problems facing any company.
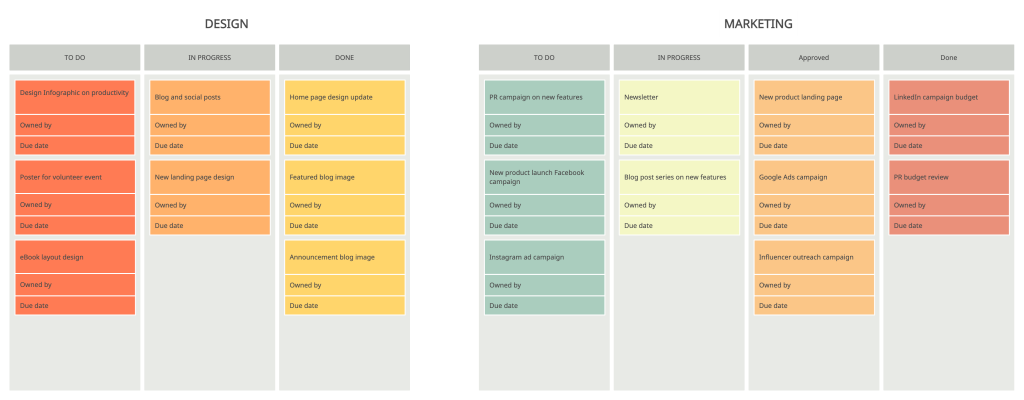
Future state value stream mapping
Future state value streaming mapping is an excellent tool to identify waste. This type is used to find the causes of and eliminate waste. Future state ideas will be marked with the same symbols used in current state mapping. Takt Time is important to be aware of when planning for future state value streams mapping. It helps you allocate resources efficiently and identify waste areas. The future state-value stream map can also be a powerful tool in your company's arsenal.
Once you've determined where problems are and how they relate to the future state, it's time to map the steps you need to take to get there. Teams can use a future map as a reference tool to help them complete their projects and achieve the target values. You should update your future value stream mapping every six- to twelve months to be able to measure your progress. As new projects are completed and modifications are made, the future state map should always be updated.
FAQ
Can we automate some parts of manufacturing?
Yes! Yes. The Egyptians discovered the wheel thousands and years ago. Nowadays, we use robots for assembly lines.
Actually, robotics can be used in manufacturing for many purposes. They include:
-
Automated assembly line robots
-
Robot welding
-
Robot painting
-
Robotics inspection
-
Robots that make products
Automation could also be used to improve manufacturing. 3D printing makes it possible to produce custom products in a matter of days or weeks.
What are the products and services of logistics?
Logistics refers to all activities that involve moving goods from A to B.
These include all aspects related to transport such as packaging, loading and transporting, storing, transporting, unloading and warehousing inventory management, customer service. Distribution, returns, recycling are some of the options.
Logisticians ensure that the right product reaches the right place at the right time and under safe conditions. Logisticians assist companies in managing their supply chains by providing information such as demand forecasts, stock levels and production schedules.
They coordinate with vendors and suppliers, keep track of shipments, monitor quality standards and perform inventory and order replenishment.
What does manufacturing industry mean?
Manufacturing Industries are businesses that produce products for sale. Consumers are those who purchase these products. These companies employ many processes to achieve this purpose, such as production and distribution, retailing, management and so on. They produce goods from raw materials by using machines and other machinery. This includes all types manufactured goods such as clothing, building materials, furniture, electronics, tools and machinery.
Why is logistics so important in manufacturing?
Logistics are an essential part of any business. They help you achieve great results by helping you manage all aspects of product flow, from raw materials to finished goods.
Logistics play an important role in reducing costs as well as increasing efficiency.
Statistics
- According to the United Nations Industrial Development Organization (UNIDO), China is the top manufacturer worldwide by 2019 output, producing 28.7% of the total global manufacturing output, followed by the United States, Japan, Germany, and India.[52][53] (en.wikipedia.org)
- (2:04) MTO is a production technique wherein products are customized according to customer specifications, and production only starts after an order is received. (oracle.com)
- According to a Statista study, U.S. businesses spent $1.63 trillion on logistics in 2019, moving goods from origin to end user through various supply chain network segments. (netsuite.com)
- It's estimated that 10.8% of the U.S. GDP in 2020 was contributed to manufacturing. (investopedia.com)
- Job #1 is delivering the ordered product according to specifications: color, size, brand, and quantity. (netsuite.com)
External Links
How To
How to use the Just-In Time Method in Production
Just-in time (JIT), is a process that reduces costs and increases efficiency in business operations. It's a way to ensure that you get the right resources at just the right time. This means that only what you use is charged to your account. Frederick Taylor, a 1900s foreman, first coined the term. Taylor observed that overtime was paid to workers if they were late in working. He then concluded that if he could ensure that workers had enough time to do their job before starting to work, this would improve productivity.
The idea behind JIT is that you should plan ahead and have everything ready so you don't waste money. Also, you should look at the whole project from start-to-finish and make sure you have the resources necessary to address any issues. If you expect problems to arise, you will be able to provide the necessary equipment and personnel to address them. This will prevent you from spending extra money on unnecessary things.
There are several types of JIT techniques:
-
Demand-driven: This JIT is where you place regular orders for the parts/materials that are needed for your project. This will allow you to track how much material you have left over after using it. This will allow to you estimate the time it will take for more to be produced.
-
Inventory-based: You stock materials in advance to make your projects easier. This allows you to predict how much you can expect to sell.
-
Project-driven: This approach involves setting aside sufficient funds to cover your project's costs. When you know how much you need, you'll purchase the appropriate amount of materials.
-
Resource-based JIT is the most widespread form. Here you can allocate certain resources based purely on demand. You will, for example, assign more staff to deal with large orders. If you don't receive many orders, then you'll assign fewer employees to handle the load.
-
Cost-based: This approach is very similar to resource-based. However, you don't just care about the number of people you have; you also need to consider how much each person will cost.
-
Price-based: This is similar to cost-based but instead of looking at individual workers' salaries, you look at the total company price.
-
Material-based: This approach is similar to cost-based. However, instead of looking at the total cost for the company, you look at how much you spend on average on raw materials.
-
Time-based: Another variation of resource-based JIT. Instead of focusing only on how much each employee is costing, you should focus on how long it takes to complete your project.
-
Quality-based: This is yet another variation of resource-based JIT. Instead of thinking about how much each employee costs or how long it takes to manufacture something, you think about how good the quality of your product is.
-
Value-based: This is one of the newest forms of JIT. In this case, you're not concerned with how well the products perform or whether they meet customer expectations. Instead, your focus is on the value you bring to the market.
-
Stock-based is an inventory-based system that measures the number of items produced at any given moment. It is used when production goals are met while inventory is kept to a minimum.
-
Just-intime planning (JIT), is a combination JIT/sales chain management. It refers to the process of scheduling the delivery of components as soon as they are ordered. It is essential because it reduces lead-times and increases throughput.