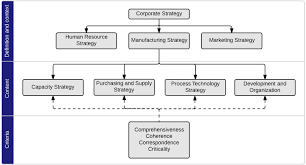
Biomedical engineering is a promising career that can improve the health of the people who choose it. They work in many areas, including pharmaceutical manufacturing, laboratories, and health care facilities. These engineers invent new techniques and products that aid patients.
For a career as a biomedical engineers, you must have a bachelor's in engineering. A solid foundation in science and math is required for biomedical engineers. In addition, they must possess excellent problem-solving skills and strong analytical abilities. To gain practical experience, they can take part in internships. Sometimes employers will require a master's in order to hire them.
Due to the aging population, medical technology advances, and rising demand for biomedical engineering professionals, the demand for these engineers will increase over the next few decades. Biomedical engineers work with other professionals in the medical field to develop and test new technologies. Biomedical engineers can also design, build, and repair medical devices. They can work in hospitals, research facilities or medical equipment sales businesses.
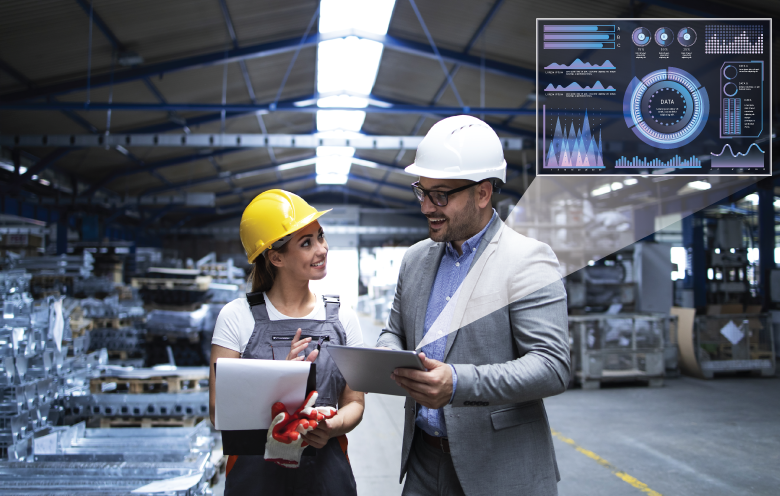
Biomedical engineering uses advanced science and math in order to design equipment, software and other solutions to biological sciences problems. They use advanced math and statistics to build complicated medical devices. Biomedical engineers are responsible for designing new processes and devices, as well as testing new drugs and therapies. Medical equipment must perform at its best.
There is a high demand in biomedical engineering, just like any other engineering field. The field is expected to grow at a faster rate than other engineering specialties. According to the Bureau of Labor Statistics(BLS), jobs in biomedical engineering will grow six percent between 2030 and 2020. This is significantly faster than the average rate of growth for all occupations. As of 2010, biomedical engineers held around 15,700 jobs. The BLS predicts that there will be 1,400 openings each year through 2029. These opportunities are expected to be in the following industries, including healthcare services, manufacturing of medical equipment and supplies, and research services.
Those who want to pursue a career as a biomedical engineer should take advantage of internships. These internships are an opportunity to see how biomedical engineers work and to gain real-life experience. A good idea for students is to take courses on computer programming, drawing, and drafting. Individuals who love science can opt to study biology, human anatomy, and molecular biology.
If you are interested in a career as a biomedical engineering professional, it is advisable to start your preparations as early as high school. While a bachelor's in biomedical engineering degree is important, many employers prefer a master's. A master's degree can expand opportunities and lead to supervisory roles in the field.
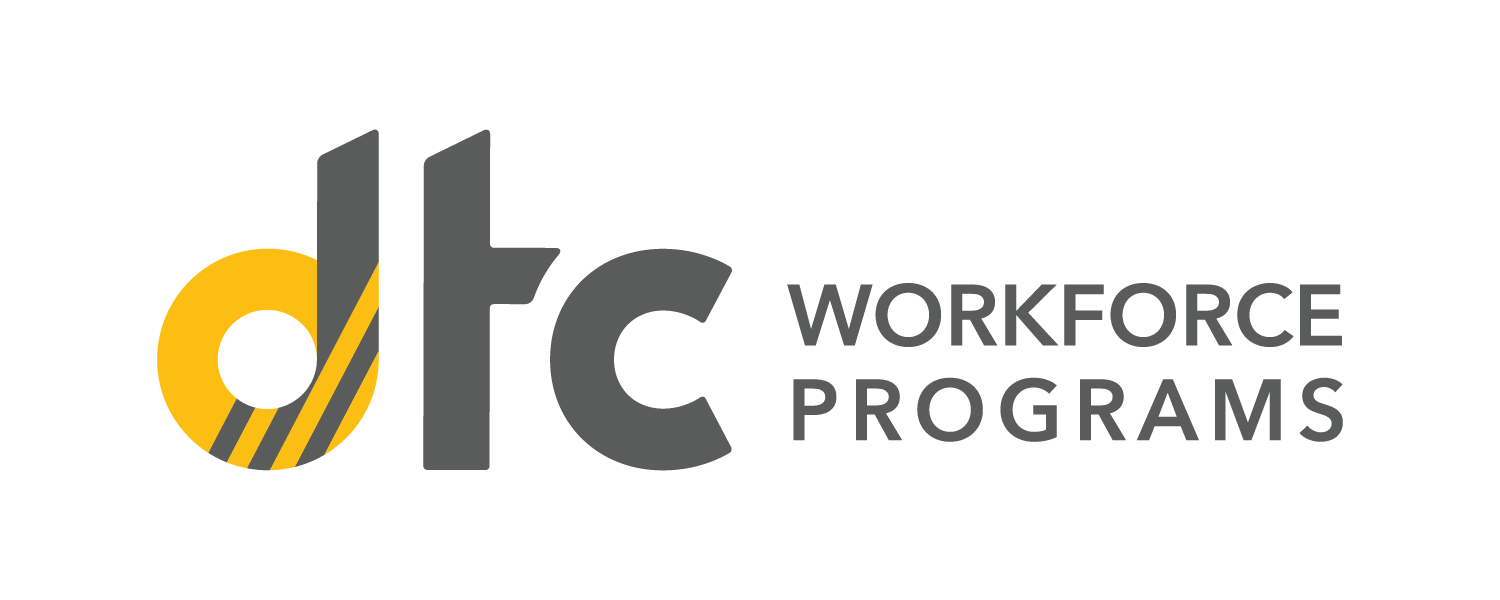
Biomedical engineers need to take courses in mathematics, biology, chemistry and physics. Students studying biomedical engineers study human anatomy, molecular biology, physiology and pharmacology during their undergraduate studies. They also conduct capstone projects that synthesize their engineering skills with problems related to biological science.
FAQ
Why automate your warehouse
Modern warehouses are increasingly dependent on automation. E-commerce has increased the demand for quicker delivery times and more efficient processes.
Warehouses need to adapt quickly to meet changing needs. To do so, they must invest heavily in technology. Automating warehouses is a great way to save money. Here are some of the reasons automation is worth your investment:
-
Increases throughput/productivity
-
Reduces errors
-
Increases accuracy
-
Safety Boosts
-
Eliminates bottlenecks
-
Companies can scale more easily
-
Workers are more productive
-
Provides visibility into everything that happens in the warehouse
-
Enhances customer experience
-
Improves employee satisfaction
-
It reduces downtime, and increases uptime
-
This ensures that quality products are delivered promptly
-
Eliminates human error
-
Helps ensure compliance with regulations
What is the importance of logistics in manufacturing?
Logistics are an integral part any business. They can help you achieve great success by helping you manage product flow from raw material to finished goods.
Logistics play a key role in reducing expenses and increasing efficiency.
What are the differences between these four types?
Manufacturing refers to the transformation of raw materials into useful products by using machines and processes. It involves many different activities such as designing, building, testing, packaging, shipping, selling, servicing, etc.
Are there any Manufacturing Processes that we should know before we can learn about Logistics?
No. You don't have to know about manufacturing processes before learning about logistics. However, knowing about manufacturing processes will definitely give you a better understanding of how logistics works.
What is the difference between Production Planning, Scheduling and Production Planning?
Production Planning (PP) refers to the process of determining how much production is needed at any given moment. This can be done by forecasting demand and identifying production capabilities.
Scheduling refers the process by which tasks are assigned dates so that they can all be completed within the given timeframe.
Statistics
- You can multiply the result by 100 to get the total percent of monthly overhead. (investopedia.com)
- It's estimated that 10.8% of the U.S. GDP in 2020 was contributed to manufacturing. (investopedia.com)
- In 2021, an estimated 12.1 million Americans work in the manufacturing sector.6 (investopedia.com)
- In the United States, for example, manufacturing makes up 15% of the economic output. (twi-global.com)
- According to the United Nations Industrial Development Organization (UNIDO), China is the top manufacturer worldwide by 2019 output, producing 28.7% of the total global manufacturing output, followed by the United States, Japan, Germany, and India.[52][53] (en.wikipedia.org)
External Links
How To
How to Use Six Sigma in Manufacturing
Six Sigma is defined as "the application of statistical process control (SPC) techniques to achieve continuous improvement." Motorola's Quality Improvement Department in Tokyo, Japan developed Six Sigma in 1986. Six Sigma's core idea is to improve the quality of processes by standardizing and eliminating defects. In recent years, many companies have adopted this method because they believe there is no such thing as perfect products or services. Six Sigma's primary goal is to reduce variation from the average value of production. If you take a sample and compare it with the average, you will be able to determine how much of the production process is different from the norm. If this deviation is too big, you know something needs fixing.
Understanding the dynamics of variability within your business is the first step in Six Sigma. Once you understand that, it is time to identify the sources of variation. You'll also want to determine whether these variations are random or systematic. Random variations occur when people make mistakes; systematic ones are caused by factors outside the process itself. For example, if you're making widgets, and some of them fall off the assembly line, those would be considered random variations. It would be considered a systematic problem if every widget that you build falls apart at the same location each time.
After identifying the problem areas, you will need to devise solutions. This could mean changing your approach or redesigning the entire process. After implementing the new changes, you should test them again to see if they worked. If they don't work, you will need to go back to the drawing boards and create a new plan.