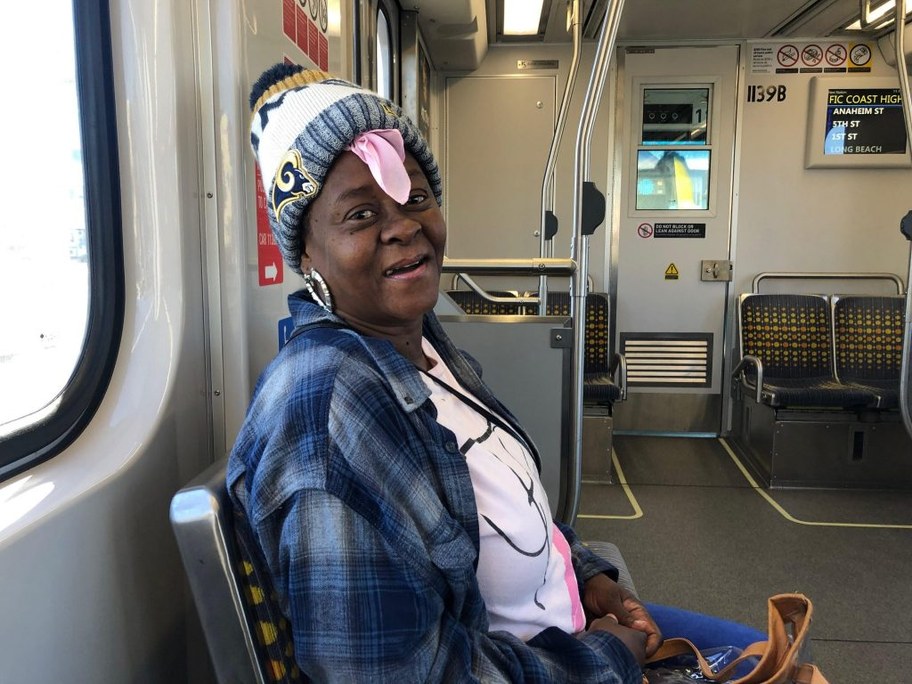
The highest salaries for biochemists are $84,365. These professionals research drugs and the effects they have on living organisms. They also design and develop new chemical compounds. They can work as faculty members at colleges or for companies.
Biochemists have different education requirements depending on their job. Many employers prefer candidates with advanced degrees. Some companies only require a bachelor's degree. A master's degree may be necessary for positions in biophysics, which is the study of physical laws and biological phenomena.
Biochemists do research on new chemical compounds. They also design quality control procedures. Biochemists often collaborate with biophysicists. They study the relationship between physical laws, biological phenomena, and how they relate to each other. They may also work alongside chemical biologists, responsible for the preparation of samples and the development of medicinal chemistry strategies.
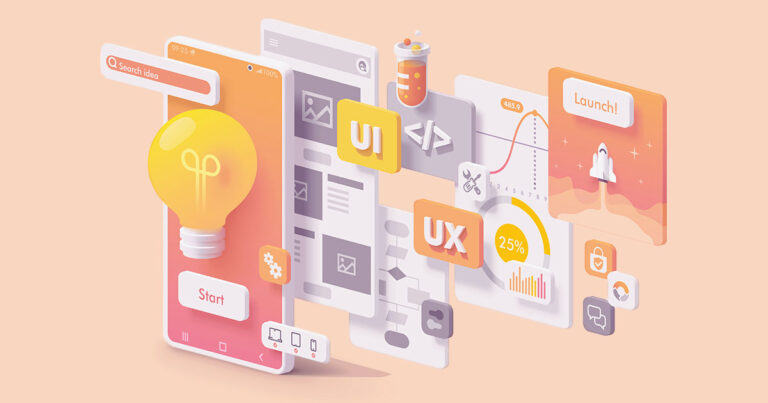
Biochemists may work in the pharmaceutical industry or the manufacturing industry. The top employers include Pfizer, GlaxoSmithkline, and Amgen. These companies are known for their high-paying jobs, but it is not easy to find a job. Companies such as Genentech are also difficult to secure, although their salaries are comparable. Eurofins and Siemens Healthineers also have biochemist jobs.
A biochemist may also serve as a professor at a college. These professionals educate students about biology, and other organisms. These biochemists can also help with environmental restoration. They might be able to develop new chemical substances or formulations that address environmental problems. Biochemists could also investigate the effects on organisms of hormones or drugs.
Many biochemists promote the study biochemistry. Advocates can receive degrees from universities such Western Illinois University (Trinity University), Western Illinois University (Kean University) and others. They may also get internships at research laboratories. These internships can help students build contacts in the field and gain hands-on experience. They can later apply for roles as a research associate or lecturer.
A biochemist typically holds a bachelor's and a doctorate. These degrees are required to hold entry-level positions within biochemistry. For biochemists without a college education, obtaining a license might be necessary. For jobs that require direct contact with patients, a license might be necessary. Medical assistant positions may also require a license. These positions might be part of a small group, but there may be opportunities for advancement.
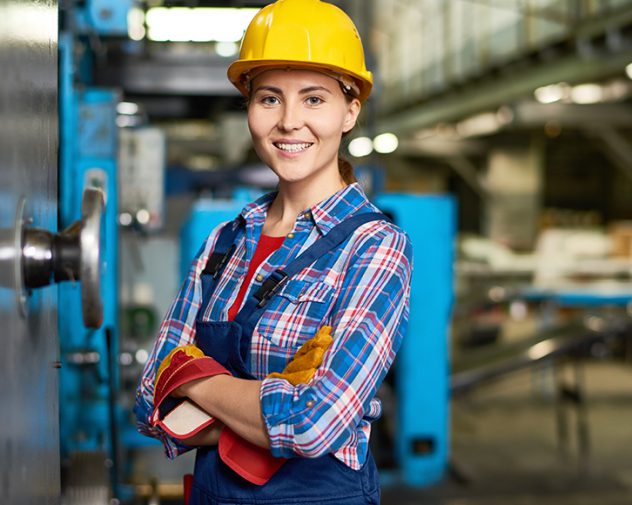
Biochemist salaries can vary greatly. The median annual income is $76,806; the average salary, $95,998, is $95,998. The salary of biochemists will rise by 2020. The top employers in the health care industry, such as Pfizer, Eurofins, and Amgen, all pay their employees a high salary. GlaxoSmithkline and Siemens Healthineers also offer salaries for biochemists that are comparable to other professionals.
In pharma companies, biochemists can work as chemical biologists. These professionals analyse samples and prepare reports. They also supervise lab operations. They have to have strong experimental skills, and they must be able produce samples and present findings to stakeholders.
FAQ
What is the role of a logistics manager
A logistics manager makes sure that all goods are delivered on-time and in good condition. This is done by using his/her experience and knowledge of the company's products. He/she should ensure that sufficient stock is available in order to meet customer demand.
What skills do production planners need?
You must be flexible and organized to become a productive production planner. It is also important to be able communicate with colleagues and clients.
What do you mean by warehouse?
A warehouse, or storage facility, is where goods are stored prior to being sold. It can be indoors or out. In some cases, it may be a combination of both.
Why is logistics important in manufacturing?
Logistics are an integral part any business. They enable you to achieve outstanding results by helping manage product flow from raw materials through to finished goods.
Logistics plays a significant role in reducing cost and increasing efficiency.
How can manufacturing excess production be decreased?
It is essential to find better ways to manage inventory to reduce overproduction. This would reduce time spent on activities such as purchasing, stocking, and maintaining excess stock. This could help us free up our time for other productive tasks.
One way to do this is to adopt a Kanban system. A Kanban board, a visual display to show the progress of work, is called a Kanban board. A Kanban system allows work items to move through several states before reaching their final destination. Each state is assigned a different priority.
If work is moving from one stage to the other, then the current task can be completed and moved on to the next. But if a task remains in the beginning stages it will stay that way until it reaches its end.
This allows you to keep work moving along while making sure that no work gets neglected. Managers can see how much work has been done and the status of each task at any time with a Kanban Board. This allows them the ability to adjust their workflow using real-time data.
Lean manufacturing is another way to manage inventory levels. Lean manufacturing focuses on eliminating waste throughout the entire production chain. Anything that does not contribute to the product's value is considered waste. These are some of the most common types.
-
Overproduction
-
Inventory
-
Packaging that is not necessary
-
Excess materials
These ideas can help manufacturers improve efficiency and reduce costs.
Statistics
- You can multiply the result by 100 to get the total percent of monthly overhead. (investopedia.com)
- Many factories witnessed a 30% increase in output due to the shift to electric motors. (en.wikipedia.org)
- [54][55] These are the top 50 countries by the total value of manufacturing output in US dollars for its noted year according to World Bank.[56] (en.wikipedia.org)
- In 2021, an estimated 12.1 million Americans work in the manufacturing sector.6 (investopedia.com)
- (2:04) MTO is a production technique wherein products are customized according to customer specifications, and production only starts after an order is received. (oracle.com)
External Links
How To
Six Sigma in Manufacturing
Six Sigma is defined by "the application SPC (statistical process control) techniques to achieve continuous improvements." Motorola's Quality Improvement Department created Six Sigma at their Tokyo plant, Japan in 1986. Six Sigma's core idea is to improve the quality of processes by standardizing and eliminating defects. This method has been adopted by many companies in recent years as they believe there are no perfect products or services. Six Sigma aims to reduce variation in the production's mean value. This means that you can take a sample from your product and then compare its performance to the average to find out how often the process differs from the norm. If it is too large, it means that there are problems.
The first step toward implementing Six Sigma is understanding how variability works in your business. Once you understand that, it is time to identify the sources of variation. Also, you will need to identify the sources of variation. Random variations occur when people do mistakes. Symmetrical variations are caused due to factors beyond the process. If you make widgets and some of them end up on the assembly line, then those are considered random variations. However, if you notice that every time you assemble a widget, it always falls apart at exactly the same place, then that would be a systematic problem.
Once you identify the problem areas, it is time to create solutions. The solution could involve changing how you do things, or redesigning your entire process. Once you have implemented the changes, it is important to test them again to ensure they work. If they don't work you need to rework them and come up a better plan.