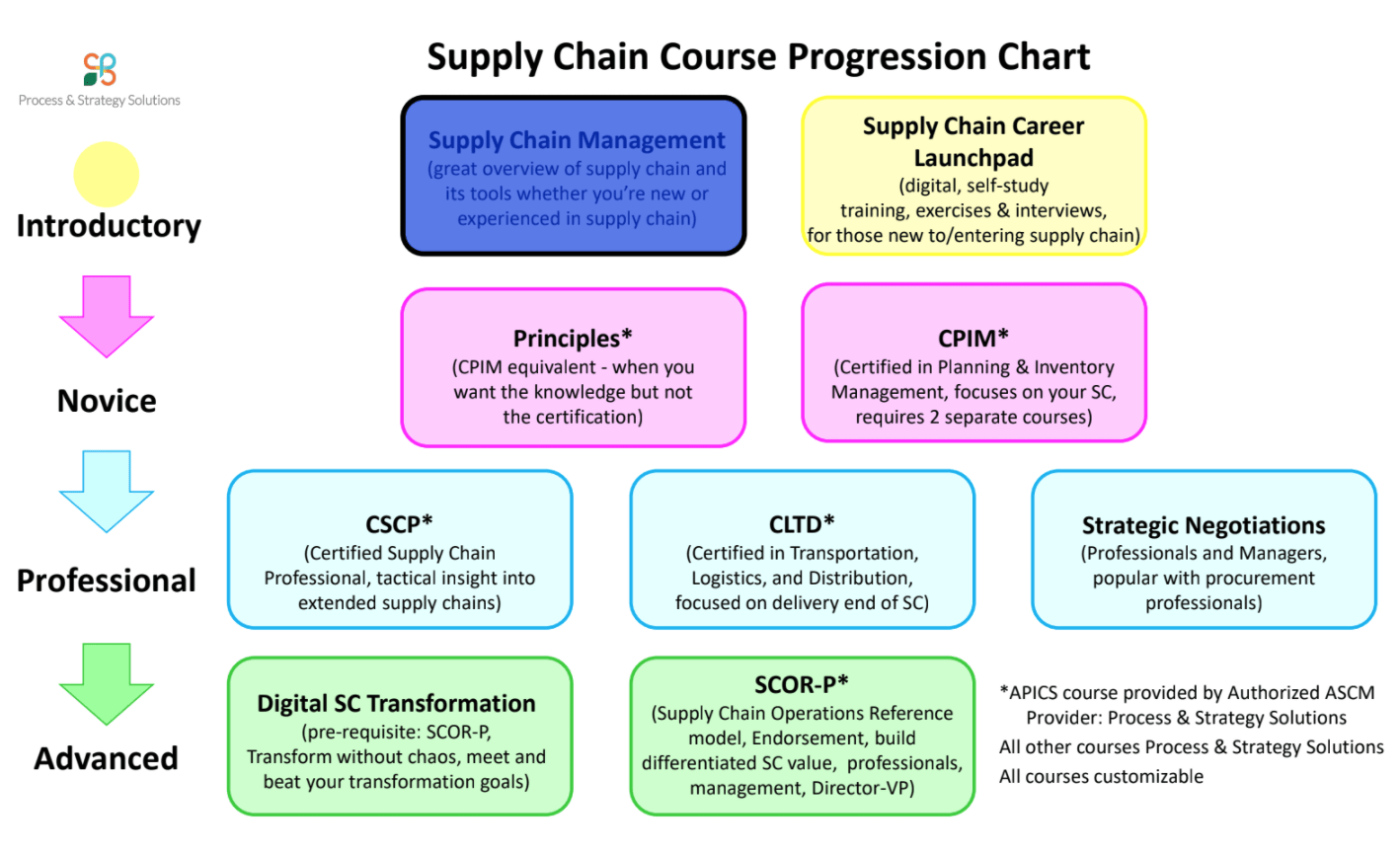
Toyota has never lost sight, no matter how successful it is, of its primary goal to make high quality products. Toyota has been a top-selling automotive brand because of its unwavering dedication to excellence.
Toyota's strategy is built on its core values and encourages smart growth. It emphasizes the importance in building and maintaining relationships with dealers. Toyota is different from other companies that rely only on their stock prices. They place the importance of its customers above all else. Because the automobile industry is competitive, innovation is key to success.
Toyota employees need to be willing to take on new challenges in order for the company to remain successful. Toyota encourages its employees to try new ideas and experiment in order to overcome these obstacles. To do this, Toyota encourages open communication and challenges employees to overcome differences and compromises. On-thejob training helps to accomplish this. Employees are also encouraged to be open about problems and mistakes.
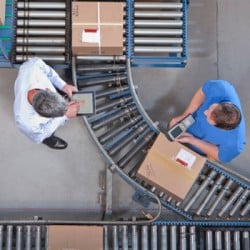
Toyota has another way to be successful is by using continuous improvement, also known as kaizen. The process involves streamlining processes and testing new ideas. This is known as genchi-genbutsu in Japanese. It helps Toyota reach its goals. It is an integral part Toyota’s culture. It has been the foundation of Toyota's success for many decades.
Toyota started a research lab as one of its major moves. Kiichiro Tokyoda, the company's founder, believed that innovation was essential for automobile manufacturing to continue to thrive. He set up a research lab in the late 1930s. He had a vision of a Japan producing its own automobiles and using Japanese technology.
Toyota made a series strategic moves in the 1950s. It started diversifying its product line and exporting cars all over the globe. It established a separate sales organization and a network for dealers. It began to get a better understanding of the international car market. It saw that American and European automakers would outnumber Toyota if Toyota wanted to compete in global markets.
Another major move that Toyota made in the '50s was to launch its own American division. Because it saw that American workers were nine-times more productive than Japanese workers, the company made this move. It also realized that fuel-efficient cars were a must in the marketplace. It had to convince American citizens that Japanese cars were a worthwhile investment. It also had to overcome a major strike that crippled the company in the 1950s. It had to take out loans and cut staff.
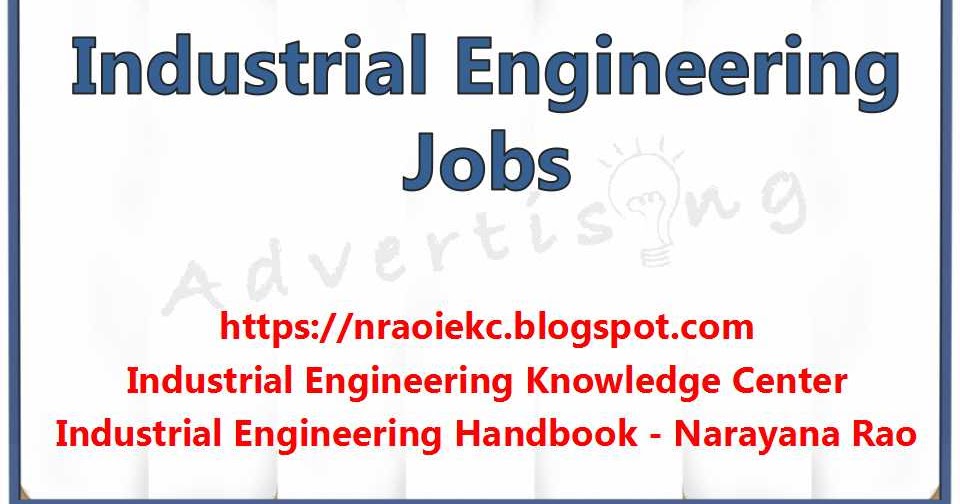
Finally, Toyota created a "driving school" to help citizens obtain drivers' licenses. It also designed a line specifically for the U.S. markets. These initiatives helped the company attract more customers to its dealerships.
Toyota's success as an automobile manufacturer depends on its ability and willingness to innovate and create value. It is also dependent on its ability to establish relationships with suppliers, dealers, and other stakeholders.
FAQ
What are the logistics products?
Logistics refers to the movement of goods from one place to another.
They encompass all aspects transport, including packaging and loading, transporting, storage, unloading.
Logisticians ensure that products reach the right destination at the right moment and under safe conditions. They provide information on demand forecasts as well stock levels, production schedules and availability of raw material.
They keep track and monitor the transit of shipments, maintain quality standards, order replenishment and inventories, coordinate with suppliers, vendors, and provide support for sales and marketing.
What are the 7 Rs of logistics?
The acronym 7R's for Logistics stands to represent the seven basic principles in logistics management. It was developed by the International Association of Business Logisticians (IABL) and published in 2004 as part of its "Seven Principles of Logistics Management" series.
The acronym is composed of the following letters.
-
Responsive - ensure all actions are legal and not harmful to others.
-
Reliable: Have faith in your ability or the ability to honor any promises made.
-
Use resources effectively and sparingly.
-
Realistic - Consider all aspects of operations, including environmental impact and cost effectiveness.
-
Respectful - treat people fairly and equitably.
-
You are resourceful and look for ways to save money while increasing productivity.
-
Recognizable provides value-added products and services to customers
What are the responsibilities for a manufacturing manager
A manufacturing manager has to ensure that all manufacturing processes work efficiently and effectively. They should also be aware and responsive to any company problems.
They should also learn how to communicate effectively with other departments, including sales and marketing.
They should be up to date on the latest trends and be able apply this knowledge to increase productivity and efficiency.
Why automate your warehouse
Modern warehousing is becoming more automated. E-commerce has brought increased demand for more efficient and quicker delivery times.
Warehouses should be able adapt quickly to new needs. They must invest heavily in technology to do this. Automation of warehouses offers many benefits. Here are some benefits of investing in automation
-
Increases throughput/productivity
-
Reduces errors
-
Improves accuracy
-
Safety Boosts
-
Eliminates bottlenecks
-
This allows companies to scale easily
-
This makes workers more productive
-
The warehouse can be viewed from all angles.
-
Enhances customer experience
-
Improves employee satisfaction
-
Reduces downtime and improves uptime
-
This ensures that quality products are delivered promptly
-
Eliminates human error
-
It helps ensure compliance with regulations
How can we reduce manufacturing overproduction?
Better inventory management is key to reducing excess production. This would reduce the time needed to manage inventory. This would allow us to use our resources for more productive tasks.
A Kanban system is one way to achieve this. A Kanban board, a visual display to show the progress of work, is called a Kanban board. Kanban systems are where work items travel through a series of states until reaching their final destination. Each state represents an individual priority level.
To illustrate, work can move from one stage or another when it is complete enough for it to be moved to a new stage. But if a task remains in the beginning stages it will stay that way until it reaches its end.
This keeps work moving and ensures no work is lost. Managers can see how much work has been done and the status of each task at any time with a Kanban Board. This data allows them adjust their workflow based upon real-time data.
Lean manufacturing, another method to control inventory levels, is also an option. Lean manufacturing focuses on eliminating waste throughout the entire production chain. Anything that does not contribute to the product's value is considered waste. Here are some examples of common types.
-
Overproduction
-
Inventory
-
Unnecessary packaging
-
Excess materials
Manufacturers can reduce their costs and improve their efficiency by using these ideas.
What is the job of a production plan?
Production planners make sure that every aspect of the project is delivered on-time, within budget, and within schedule. They also ensure the quality of the product and service meets the client's requirements.
Statistics
- [54][55] These are the top 50 countries by the total value of manufacturing output in US dollars for its noted year according to World Bank.[56] (en.wikipedia.org)
- According to a Statista study, U.S. businesses spent $1.63 trillion on logistics in 2019, moving goods from origin to end user through various supply chain network segments. (netsuite.com)
- In 2021, an estimated 12.1 million Americans work in the manufacturing sector.6 (investopedia.com)
- You can multiply the result by 100 to get the total percent of monthly overhead. (investopedia.com)
- In the United States, for example, manufacturing makes up 15% of the economic output. (twi-global.com)
External Links
How To
How to Use lean manufacturing in the Production of Goods
Lean manufacturing is a management system that aims at increasing efficiency and reducing waste. It was developed by Taiichi Okono in Japan, during the 1970s & 1980s. TPS founder Kanji Takoda awarded him the Toyota Production System Award (TPS). Michael L. Watkins published the first book on lean manufacturing in 1990.
Lean manufacturing can be described as a set or principles that are used to improve quality, speed and cost of products or services. It emphasizes the elimination of defects and waste throughout the value stream. Just-in-time (JIT), zero defect (TPM), and 5S are all examples of lean manufacturing. Lean manufacturing emphasizes reducing non-value-added activities like inspection, rework and waiting.
Lean manufacturing improves product quality and costs. It also helps companies reach their goals quicker and decreases employee turnover. Lean manufacturing has been deemed one of the best ways to manage the entire value-chain, including customers, distributors as well retailers and employees. Lean manufacturing is widely practiced in many industries around the world. For example, Toyota's philosophy underpins its success in automobiles, electronics, appliances, healthcare, chemical engineering, aerospace, paper, food, etc.
Lean manufacturing includes five basic principles:
-
Define Value: Identify the social value of your business and what sets you apart.
-
Reduce waste - Get rid of any activity that does not add value to the supply chain.
-
Create Flow - Ensure work moves smoothly through the process without interruption.
-
Standardize and simplify - Make your processes as consistent as possible.
-
Build Relationships - Establish personal relationships with both internal and external stakeholders.
Lean manufacturing, although not new, has seen renewed interest in the economic sector since 2008. To increase their competitiveness, many businesses have turned to lean manufacturing. According to some economists, lean manufacturing could be a significant factor in the economic recovery.
Lean manufacturing, which has many benefits, is now a standard practice in the automotive industry. These include improved customer satisfaction, reduced inventory levels, lower operating costs, increased productivity, and better overall safety.
It can be applied to any aspect of an organisation. Because it makes sure that all value chains are efficient and effectively managed, Lean Manufacturing is particularly helpful for organizations.
There are three types of lean manufacturing.
-
Just-in Time Manufacturing: This lean manufacturing method is commonly called "pull systems." JIT stands for a system where components are assembled on the spot rather than being made in advance. This strategy aims to decrease lead times, increase availability of parts and reduce inventory.
-
Zero Defects Manufacturing: ZDM ensures that no defective units leave the manufacturing plant. It is better to repair a part than have it removed from the production line if it needs to be fixed. This applies to finished goods that may require minor repairs before shipment.
-
Continuous Improvement (CI), also known as Continuous Improvement, aims at improving the efficiency of operations through continuous identification and improvement to minimize or eliminate waste. Continuous Improvement (CI) involves continuous improvement in processes, people, tools, and infrastructure.