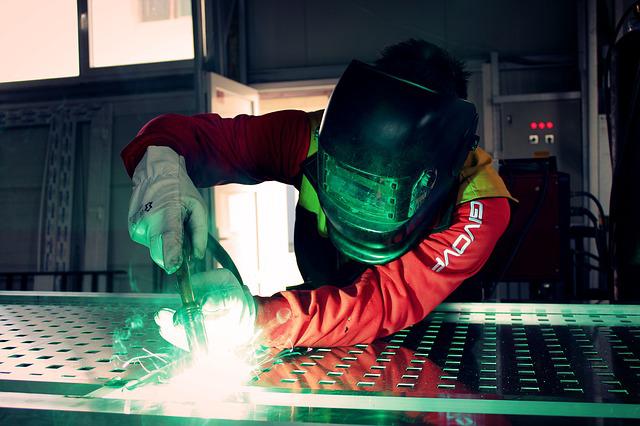
Industrial engineers are professionals who use their expertise in manufacturing technology to improve processes. They are responsible to develop and implement new methods, analyze existing systems and educate workers on new policies. As a result of their expertise, they are highly valuable in research and development firms, engineering services, and consulting.
Industrial engineers work in many different settings but their main focus is on reducing waste and improving production processes. They also reduce internal costs. These engineers are creative and use logic to design better processes. Some industrial engineers focus on automated manufacturing processes.
A vast knowledge base in mathematics and scientific principles is required for industrial engineers. They must also be skilled at problem-solving as well as critical thinking. They must have interpersonal skills, and be able work well with other people. Industrial engineers will need to be able see the entire system and recognize strengths and weaknesses of possible solutions.
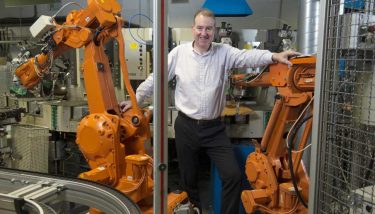
For industrial engineering careers, you must have a bachelor's degree with at least 4 years of experience. You can then apply for certification through the Society of Manufacturing Engineers. You will be able to specialize by completing a master's in this field.
The demand for industrial engineers is high. Their job openings will grow faster than the average national rate over the next ten year. The projected increase in employment for this profession is 10%. The majority of work is done full-time, though hours can vary depending on the project. The median salary for industrial engineers in Nashville is $73,856. But, wages can vary greatly depending on the employer and the individual's qualifications.
If you're looking for an Industrial Engineering job in Nashville, make sure to highlight your educational and professional achievements. Also, you should take advantage of any industry-specific certifications. For example, if you're planning to work for a government agency, you may need a professional engineer license.
Many companies employ interns to teach them the intricacies of industrial engineering. Interns will learn about lean manufacturing, value-stream mapping, and kaizen. You may be able, depending on your skills and company, to move up to management.
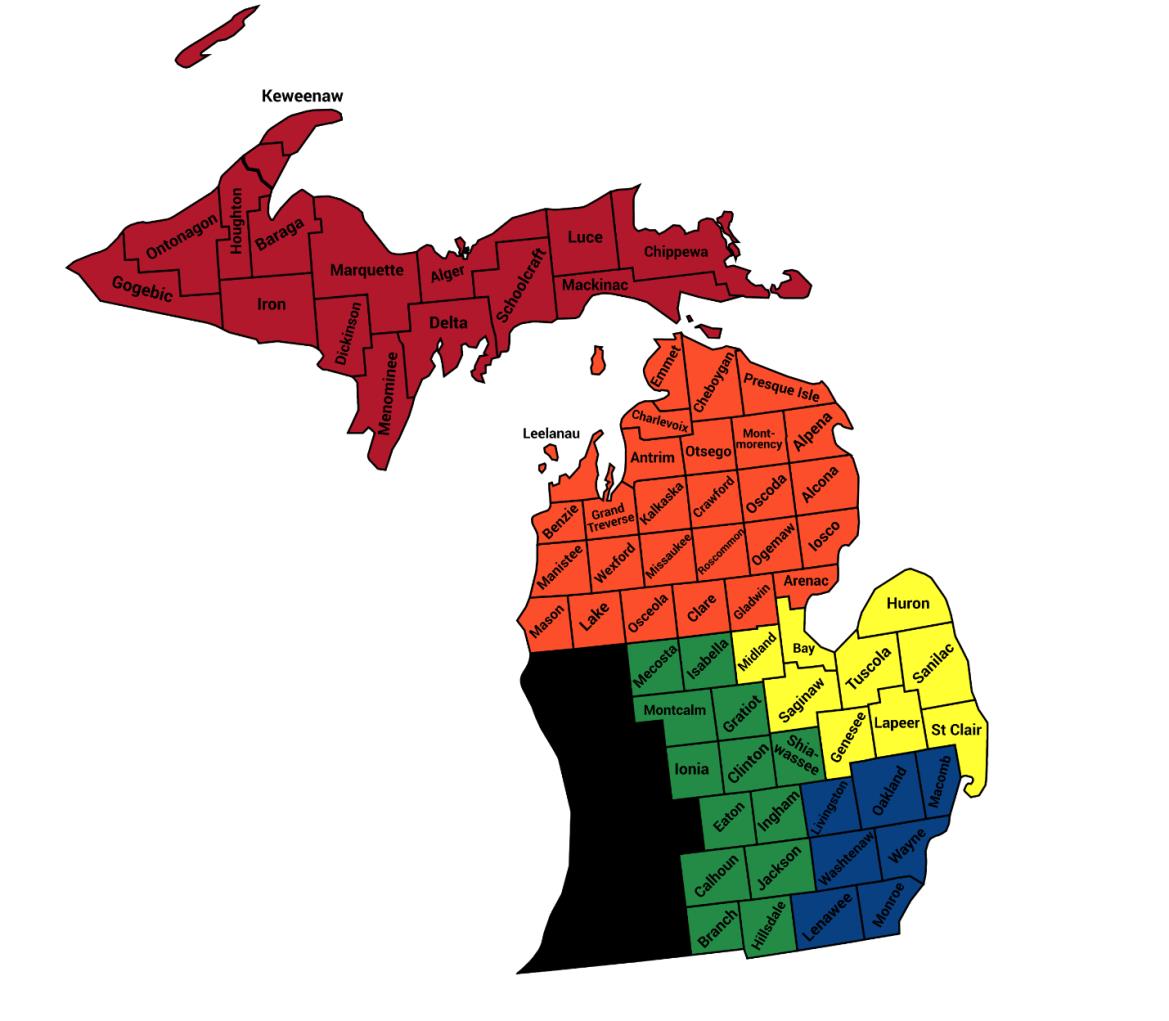
No matter if you work in a lab, an office, or both, you will need to have interpersonal communication skills to effectively communicate with your colleagues and managers. Besides communicating with fellow workers, you'll also need to be able to work with customers and vendors.
A variety of industries are looking for skilled industrial engineers. These include equipment manufacturers, electronics and transportation manufacturers, as well engineering service firms. Many colleges offer 5-year industrial engineering degrees. While many graduates are able to find entry-level positions in multiple industries, a few are more focused on certain specialty areas, such as automated manufacturing processes.
FAQ
What skills is required for a production planner?
Production planners must be flexible, organized, and able handle multiple tasks. Also, you must be able and willing to communicate with clients and coworkers.
What is the difference between manufacturing and logistics
Manufacturing is the act of producing goods from raw materials using machines and processes. Logistics encompasses the management of all aspects associated with supply chain activities such as procurement, production planning, distribution and inventory control. It also includes customer service. Sometimes manufacturing and logistics are combined to refer to a wider term that includes both the process of creating products as well as their delivery to customers.
Is automation important for manufacturing?
Automation is essential for both manufacturers and service providers. They can provide services more quickly and efficiently thanks to automation. It also helps to reduce costs and improve productivity.
What is the responsibility of a manufacturing manager?
A manufacturing manager has to ensure that all manufacturing processes work efficiently and effectively. They should be alert for any potential problems in the company and react accordingly.
They should also know how to communicate with other departments such as sales and marketing.
They must also keep up-to-date with the latest trends in their field and be able use this information to improve productivity and efficiency.
How can we increase manufacturing efficiency?
First, we need to identify which factors are most critical in affecting production times. The next step is to identify the most important factors that affect production time. If you don’t know where to begin, consider which factors have the largest impact on production times. Once you identify them, look for solutions.
What is the responsibility of a production planner?
A production planner ensures all aspects of the project are delivered on time, within budget, and within scope. They also ensure that the product/service meets the client’s needs.
Are there ways to automate parts of manufacturing?
Yes! Yes! Automation has existed since ancient times. The Egyptians discovered the wheel thousands and years ago. To help us build assembly lines, we now have robots.
In fact, there are several applications of robotics in manufacturing today. These include:
-
Robots for assembly line
-
Robot welding
-
Robot painting
-
Robotics inspection
-
Robots that create products
Automation can be applied to manufacturing in many other ways. For example, 3D printing allows us to make custom products without having to wait for weeks or months to get them manufactured.
Statistics
- You can multiply the result by 100 to get the total percent of monthly overhead. (investopedia.com)
- Many factories witnessed a 30% increase in output due to the shift to electric motors. (en.wikipedia.org)
- In 2021, an estimated 12.1 million Americans work in the manufacturing sector.6 (investopedia.com)
- In the United States, for example, manufacturing makes up 15% of the economic output. (twi-global.com)
- (2:04) MTO is a production technique wherein products are customized according to customer specifications, and production only starts after an order is received. (oracle.com)
External Links
How To
Six Sigma: How to Use it in Manufacturing
Six Sigma is defined as "the application of statistical process control (SPC) techniques to achieve continuous improvement." It was developed by Motorola's Quality Improvement Department at their plant in Tokyo, Japan, in 1986. Six Sigma's main goal is to improve process quality by standardizing processes and eliminating defects. Many companies have adopted Six Sigma in recent years because they believe that there are no perfect products and services. Six Sigma seeks to reduce variation between the mean production value. It is possible to measure the performance of your product against an average and find the percentage of time that it differs from the norm. If you notice a large deviation, then it is time to fix it.
The first step toward implementing Six Sigma is understanding how variability works in your business. Once you understand this, you can then identify the causes of variation. You'll also want to determine whether these variations are random or systematic. Random variations occur when people make mistakes; systematic ones are caused by factors outside the process itself. Random variations would include, for example, the failure of some widgets to fall from the assembly line. But if you notice that every widget you make falls apart at the exact same place each time, this would indicate that there is a problem.
Once you have identified the problem, you can design solutions. You might need to change the way you work or completely redesign the process. You should then test the changes again after they have been implemented. If they don't work, you will need to go back to the drawing boards and create a new plan.