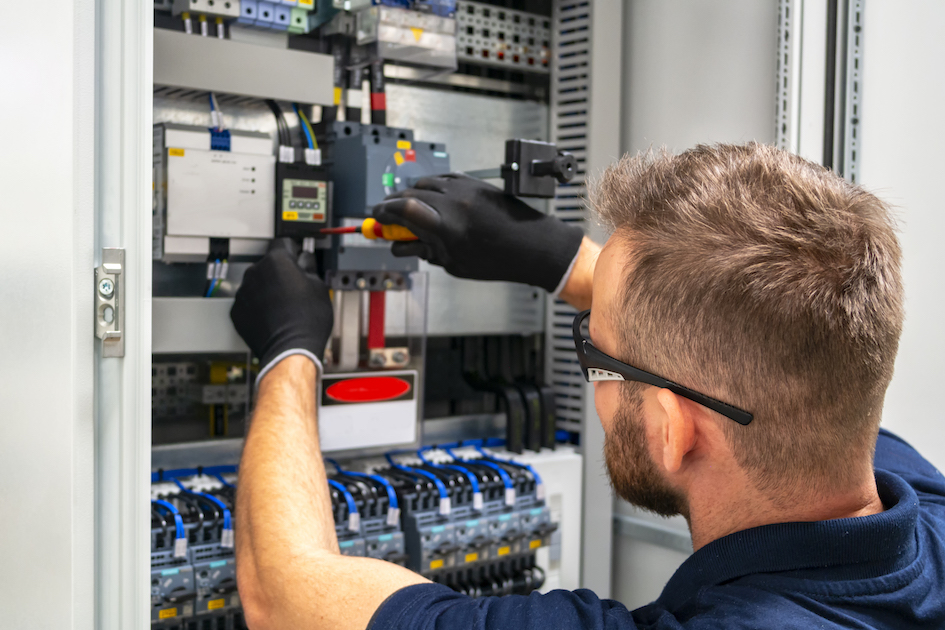
XPO logistics has 145 jobs in Atlanta, GA, US area. Visit their website if you're looking for a job. They are currently searching for the right candidate. They are a fun place to work and you will be rewarded. Aside from Atlanta, they have offices in Dallas, San Antonio and Phoenix, AZ. They offer the most generous benefits and bonuses and the most safety-oriented culture in the industry. The best part is that you can work on your own schedule. You can even use our medical benefits program. XPO's benefits program for healthcare includes a variety benefits, discounts, and plans that can help you succeed at your job.
If you're willing to work hard, Georgia is a great state to do business in. Georgia is home to a skilled workforce and has a friendly business policy. In fact, the state ranks fourth in the nation for jobs and training. The state also has one among the lowest tax rates. XPO Logistics is the best place to find a job or start a new company. With a commitment to your success, you can be assured of a rewarding and satisfying experience.
FAQ
What is the difference between Production Planning and Scheduling?
Production Planning (PP), or production planning, is the process by which you determine what products are needed at any given time. Forecasting and identifying production capacity are two key elements to this process.
Scheduling refers to the process of allocating specific dates to tasks in order that they can be completed within a specified timeframe.
What are the main products of logistics?
Logistics is the process of moving goods from one point to another.
They encompass all aspects transport, including packaging and loading, transporting, storage, unloading.
Logisticians ensure that the product is delivered to the correct place, at the right time, and under safe conditions. Logisticians help companies improve their supply chain efficiency by providing information about demand forecasts and stock levels, production schedules, as well as availability of raw materials.
They monitor shipments in transit, ensure quality standards, manage inventories, replenish orders, coordinate with suppliers and other vendors, and offer support services for sales, marketing, and customer service.
What type of jobs is there in logistics
There are many jobs available in logistics. Here are some:
-
Warehouse workers - They load trucks and pallets.
-
Transport drivers - These are people who drive trucks and trailers to transport goods or perform pick-ups.
-
Freight handlers: They sort and package freight in warehouses.
-
Inventory managers: They are responsible for the inventory and management of warehouses.
-
Sales representatives: They sell products to customers.
-
Logistics coordinators are responsible for organizing and planning logistics operations.
-
Purchasing agents - They purchase goods and services needed for company operations.
-
Customer service representatives – They answer emails and phone calls from customers.
-
Shipping clerks: They process shipping requests and issue bills.
-
Order fillers are people who fill orders based only on what was ordered.
-
Quality control inspectors (QCI) - They inspect all incoming and departing products for potential defects.
-
Others - There are many types of jobs in logistics such as transport supervisors and cargo specialists.
Statistics
- According to a Statista study, U.S. businesses spent $1.63 trillion on logistics in 2019, moving goods from origin to end user through various supply chain network segments. (netsuite.com)
- Job #1 is delivering the ordered product according to specifications: color, size, brand, and quantity. (netsuite.com)
- (2:04) MTO is a production technique wherein products are customized according to customer specifications, and production only starts after an order is received. (oracle.com)
- Many factories witnessed a 30% increase in output due to the shift to electric motors. (en.wikipedia.org)
- You can multiply the result by 100 to get the total percent of monthly overhead. (investopedia.com)
External Links
How To
How to Use 5S for Increasing Productivity in Manufacturing
5S stands as "Sort", Set In Order", Standardize", Separate" and "Store". Toyota Motor Corporation created the 5S methodology in 1954. It improves the work environment and helps companies to achieve greater efficiency.
The basic idea behind this method is to standardize production processes, so they become repeatable, measurable, and predictable. Cleaning, sorting and packing are all done daily. Through these actions, workers can perform their jobs more efficiently because they know what to expect from them.
There are five steps that you need to follow in order to implement 5S. Each step involves a different action which leads to increased efficiency. Sorting things makes it easier to find them later. When you arrange items, you place them together. Next, organize your inventory into categories and store them in containers that are easily accessible. Finally, when you label your containers, you ensure everything is labeled correctly.
This process requires employees to think critically about how they do their job. Employees should understand why they do the tasks they do, and then decide if there are better ways to accomplish them. To be successful in the 5S system, employees will need to acquire new skills and techniques.
The 5S method increases efficiency and morale among employees. They are more motivated to achieve higher efficiency levels as they start to see improvement.