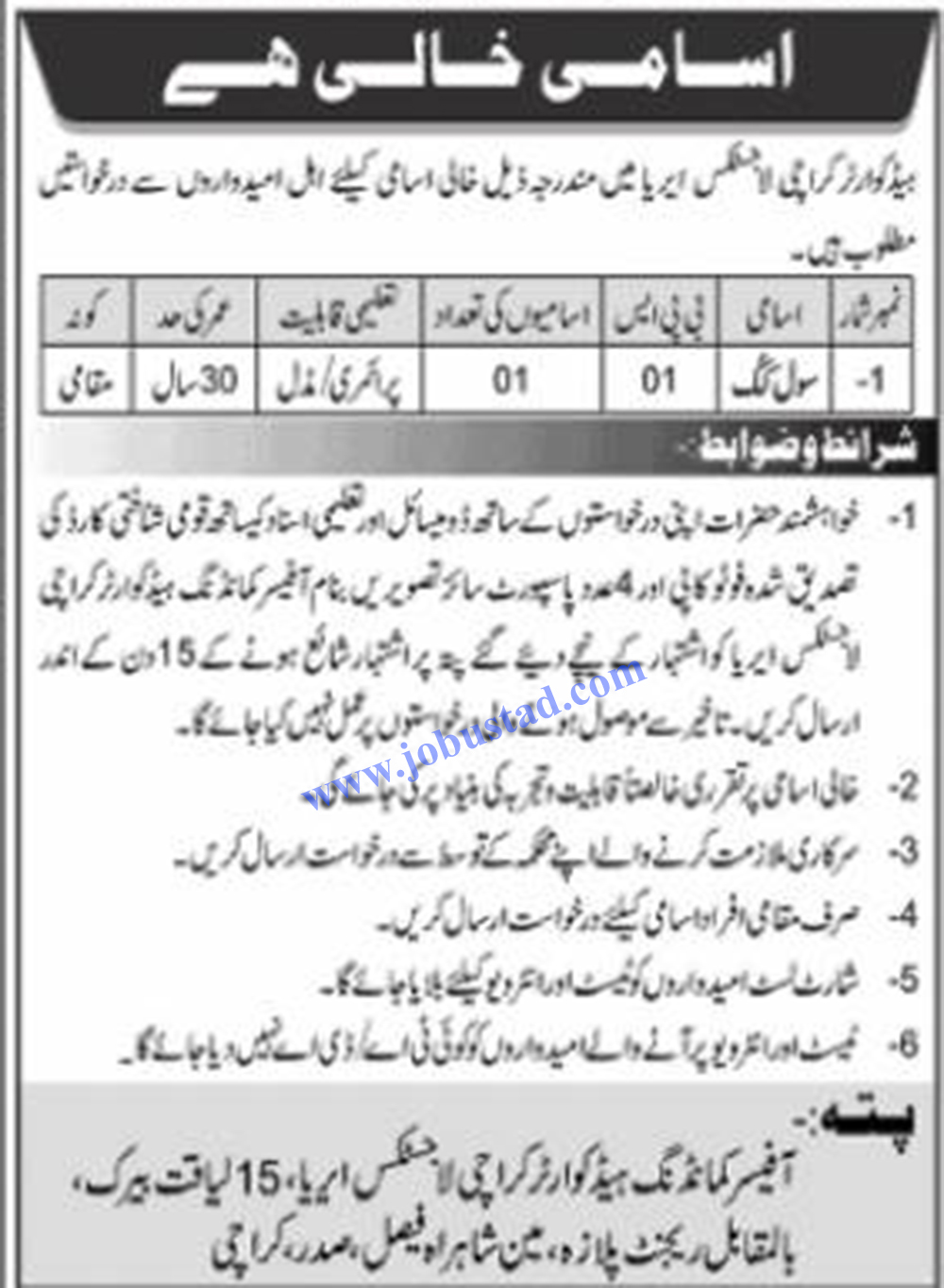
Study engineers use creativity and science to design and build things that can improve the lives of others. Whether you design bridges, equipment for medical treatment or methods to clean up toxic substances, your work will impact the lives and livelihoods of many.
Engineering is a vast and versatile academic field, so choosing the right course is important. Kingston University offers undergraduate degree programs in engineering including chemical, electrical, civil, and mechanical engineering.
A bachelor's in engineering is a prerequisite for becoming a licensed engineer. This includes courses in math, science, and humanities that can be used for a variety of careers.
Some engineers earn a master's or doctorate degree to specialize in a particular area. They can expand your options for a career and increase your job prospects.
You can also choose to take a course that is specific to your industry, like oil and gas or mining. These courses will teach you to assess underground resources, such as metals and petroleum.
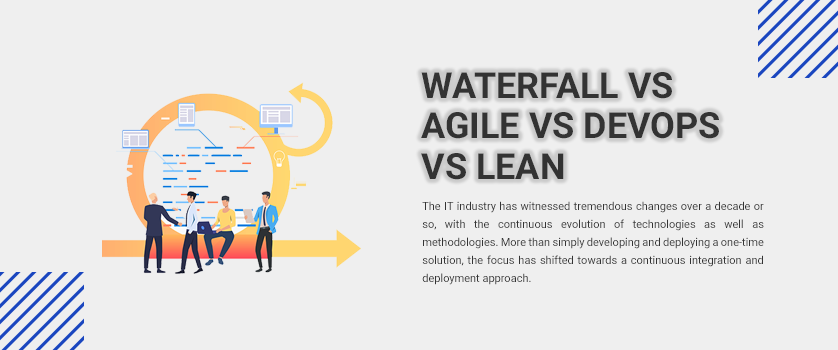
Manufacturing is the process of turning raw materials into finished products for sale in stores or markets. You'll learn how to plan a production line and the fundamentals of manufacturing.
As an engineer, you'll need to be able to work under pressure and handle a variety of responsibilities. You will need to manage your schedule and prioritize tasks to ensure that you complete all of them within the timeframe.
You'll want to select a college with an accredited engineering program if you plan on pursuing a degree in the field. This signifies that the school has met certain standards established by ABET. ABET accredits all engineering programs in the United States.
You'll be required to enroll in college full-time during the four-year period and complete at least 60 credit hour each semester. You'll also need to pass an examination and complete a work-experience internship in the engineering field you choose.
The average salary for a study engineering is $94,463 annually. An entry-level salary is about $30,000, and a senior researcher engineer's salary is about $123,325 per year.
As a research engineer, your work will include identifying technology that can be used to produce more cost-effective or efficient products. It may also involve developing designs, testing prototypes, and checking for functionality, usability, and durability. It may also include collaborating with product development and marketing to refine existing products or developing new ones.
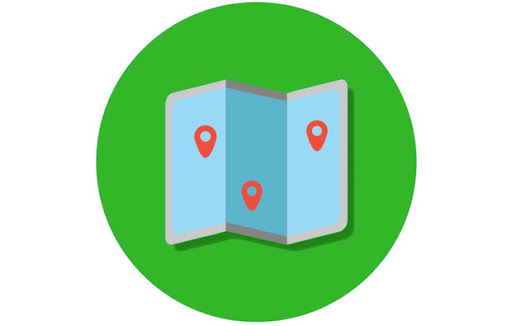
During your work as a study engineer, you'll need to spend a significant amount of time in the lab and on the job. You'll need to be able to perform complex analyses of data and develop a solid understanding of the science behind your engineering projects.
You should have a passion for science and a desire to solve complex problems if you plan to study engineering. You will also need a solid background in math, chemistry and physics.
It is best to enroll in an accredited engineering program, and then to take the FE test after graduating. Then you'll have to get some work experience in the engineering field before you take your PE exam and become licensed.
FAQ
What are manufacturing and logistics?
Manufacturing refers the process of producing goods from raw materials through machines and processes. Logistics includes all aspects related to supply chain management, such as procurement, distribution planning, inventory control and transportation. Manufacturing and logistics are often considered together as a broader term that encompasses both the process of creating products and delivering them to customers.
What does the term manufacturing industries mean?
Manufacturing Industries are companies that manufacture products. The people who buy these products are called consumers. These companies use a variety processes such as distribution, retailing and management to accomplish their purpose. They create goods from raw materials, using machines and various other equipment. This includes all types manufactured goods such as clothing, building materials, furniture, electronics, tools and machinery.
What are the main products of logistics?
Logistics refers to the movement of goods from one place to another.
They cover all aspects of transportation, such as packing, loading, transporting and unloading.
Logisticians ensure the product reaches its destination in the most efficient manner. They provide information on demand forecasts as well stock levels, production schedules and availability of raw material.
They can also track shipments in transit and monitor quality standards.
Is automation important for manufacturing?
Automation is essential for both manufacturers and service providers. Automation allows them to deliver services quicker and more efficiently. It helps them to lower costs by reducing human errors, and improving productivity.
What are the 7 Rs of logistics?
The 7R's of Logistics is an acronym for the seven basic principles of logistics management. It was developed and published by the International Association of Business Logisticians in 2004 as part of the "Seven Principles of Logistics Management".
The following letters form the acronym:
-
Responsive - ensure all actions are legal and not harmful to others.
-
Reliable – have faith in your ability and capability to keep promises.
-
Use resources effectively and sparingly.
-
Realistic – consider all aspects of operations, from cost-effectiveness to environmental impact.
-
Respectful - treat people fairly and equitably.
-
Be resourceful: Look for opportunities to save money or increase productivity.
-
Recognizable - provide customers with value-added services.
What is the difference between a production planner and a project manager?
The major difference between a Production Planner and a Project Manager is that a Project Manager is often the person responsible for organizing and planning the entire project. While a Production Planner is involved mainly in the planning stage,
Statistics
- [54][55] These are the top 50 countries by the total value of manufacturing output in US dollars for its noted year according to World Bank.[56] (en.wikipedia.org)
- According to the United Nations Industrial Development Organization (UNIDO), China is the top manufacturer worldwide by 2019 output, producing 28.7% of the total global manufacturing output, followed by the United States, Japan, Germany, and India.[52][53] (en.wikipedia.org)
- Many factories witnessed a 30% increase in output due to the shift to electric motors. (en.wikipedia.org)
- In the United States, for example, manufacturing makes up 15% of the economic output. (twi-global.com)
- (2:04) MTO is a production technique wherein products are customized according to customer specifications, and production only starts after an order is received. (oracle.com)
External Links
How To
How to use the Just In-Time Production Method
Just-in time (JIT), is a process that reduces costs and increases efficiency in business operations. This is where you have the right resources at the right time. This means that you only pay for what you actually use. The term was first coined by Frederick Taylor, who developed his theory while working as a foreman in the early 1900s. He noticed that workers were often paid overtime when they had to work late. He then concluded that if he could ensure that workers had enough time to do their job before starting to work, this would improve productivity.
JIT is an acronym that means you need to plan ahead so you don’t waste your money. Look at your entire project, from start to end. Make sure you have enough resources in place to deal with any unexpected problems. If you anticipate that there might be problems, you'll have enough people and equipment to fix them. You won't have to pay more for unnecessary items.
There are several types of JIT techniques:
-
Demand-driven: This JIT is where you place regular orders for the parts/materials that are needed for your project. This will allow to track how much material has been used up. This will allow you to calculate how long it will take to make more.
-
Inventory-based: You stock materials in advance to make your projects easier. This allows you to predict how much you can expect to sell.
-
Project-driven : This is a method where you make sure that enough money is set aside to pay the project's cost. When you know how much you need, you'll purchase the appropriate amount of materials.
-
Resource-based JIT: This type of JIT is most commonly used. Here you can allocate certain resources based purely on demand. For instance, if you have a lot of orders coming in, you'll assign more people to handle them. You'll have fewer orders if you have fewer.
-
Cost-based: This is a similar approach to resource-based but you are not only concerned with how many people you have, but also how much each one costs.
-
Price-based pricing: This is similar in concept to cost-based but instead you look at how much each worker costs, it looks at the overall company's price.
-
Material-based: This is very similar to cost-based but instead of looking at total costs of the company you are concerned with how many raw materials you use on an average.
-
Time-based: Another variation of resource-based JIT. Instead of focusing solely on the amount each employee costs, focus on how long it takes for the project to be completed.
-
Quality-based JIT is another variant of resource-based JIT. Instead of focusing on the cost of each worker or how long it takes, think about how high quality your product is.
-
Value-based: This is one of the newest forms of JIT. In this scenario, you're not concerned about how products perform or whether customers expect them to meet their expectations. Instead, you are focused on adding value to the marketplace.
-
Stock-based: This is an inventory-based method that focuses on the actual number of items being produced at any given time. It is used when production goals are met while inventory is kept to a minimum.
-
Just-intime planning (JIT), is a combination JIT/sales chain management. This refers to the scheduling of the delivery of components as soon after they are ordered. This is important as it reduces lead time and increases throughput.