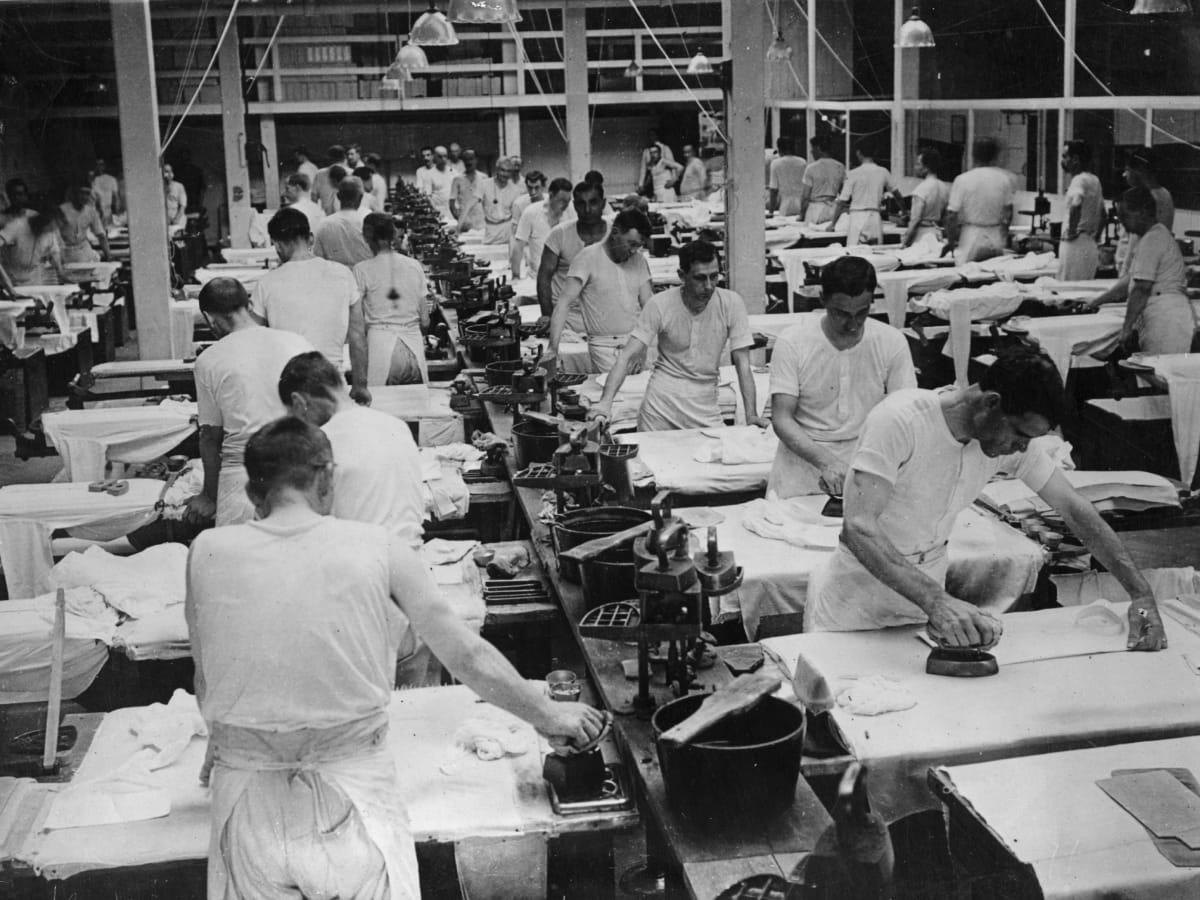
Industrial engineers are specialists who apply their knowledge of manufacturing technology in order to improve processes. They are responsible to develop and implement new methods, analyze existing systems and educate workers on new policies. Because of their experience, they are highly sought after in engineering services, consulting, and research and design firms.
Industrial engineers work in many different settings but their main focus is on reducing waste and improving production processes. They also reduce internal costs. These engineers are creative and use logic to design better processes. Some industrial engineers specialize in automating manufacturing processes.
A vast knowledge base in mathematics and scientific principles is required for industrial engineers. Additionally, they need to be skilled in problem solving and critical thinking. They should also be able to communicate well and work with others. Ideal industrial engineers will have the ability to look at a system from a wide perspective and see potential weaknesses and strengths.
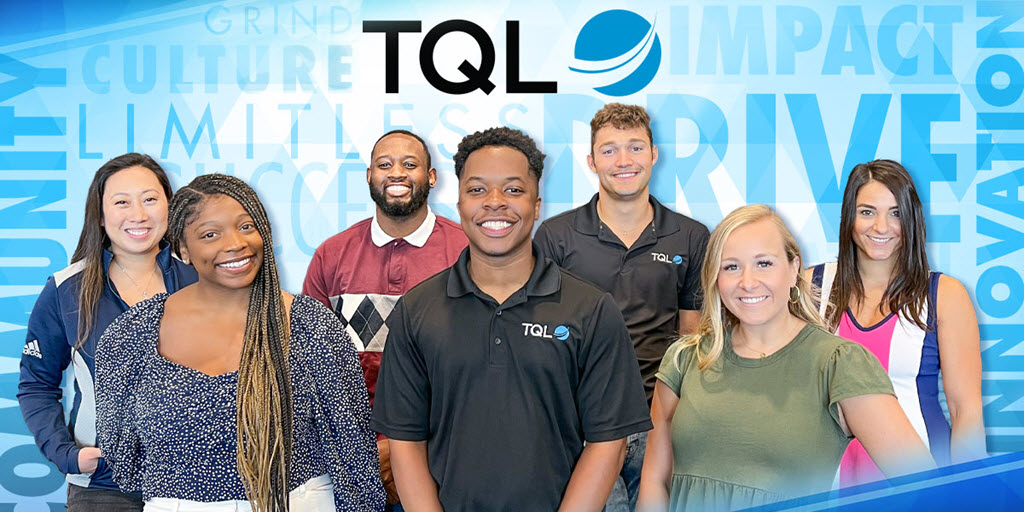
If you want to pursue an industrial engineering career, you'll need to complete a bachelor's degree and gain at least four years of experience. The Society of Manufacturing Engineers will allow you to become certified. The master's degree will enable you to specialize in your chosen field.
They are highly sought-after and are expected to see their employment opportunities grow faster than average over the next ten. This will lead to a 10 percent increase in the employment of industrial engineers. The majority of the work can be done on a full-time basis. Hours may vary depending on what the project calls for. The median salary for industrial engineers in Nashville is $73,856. However, depending on your geographic location, the employer, and your personal qualifications, the wage could vary from one employer the next.
It is important to showcase your professional and educational credentials when searching for an industrial engineer job in Nashville. You'll also need to make sure to take advantage of industry-specific certifications. For example, if you're planning to work for a government agency, you may need a professional engineer license.
Many companies hire interns in order to help them understand the intricacies behind industrial engineering. Interns learn about lean manufacturing, value stream mapping, and kaizen. Depending on your skill set and the company, you may be able to advance your career to a management position.
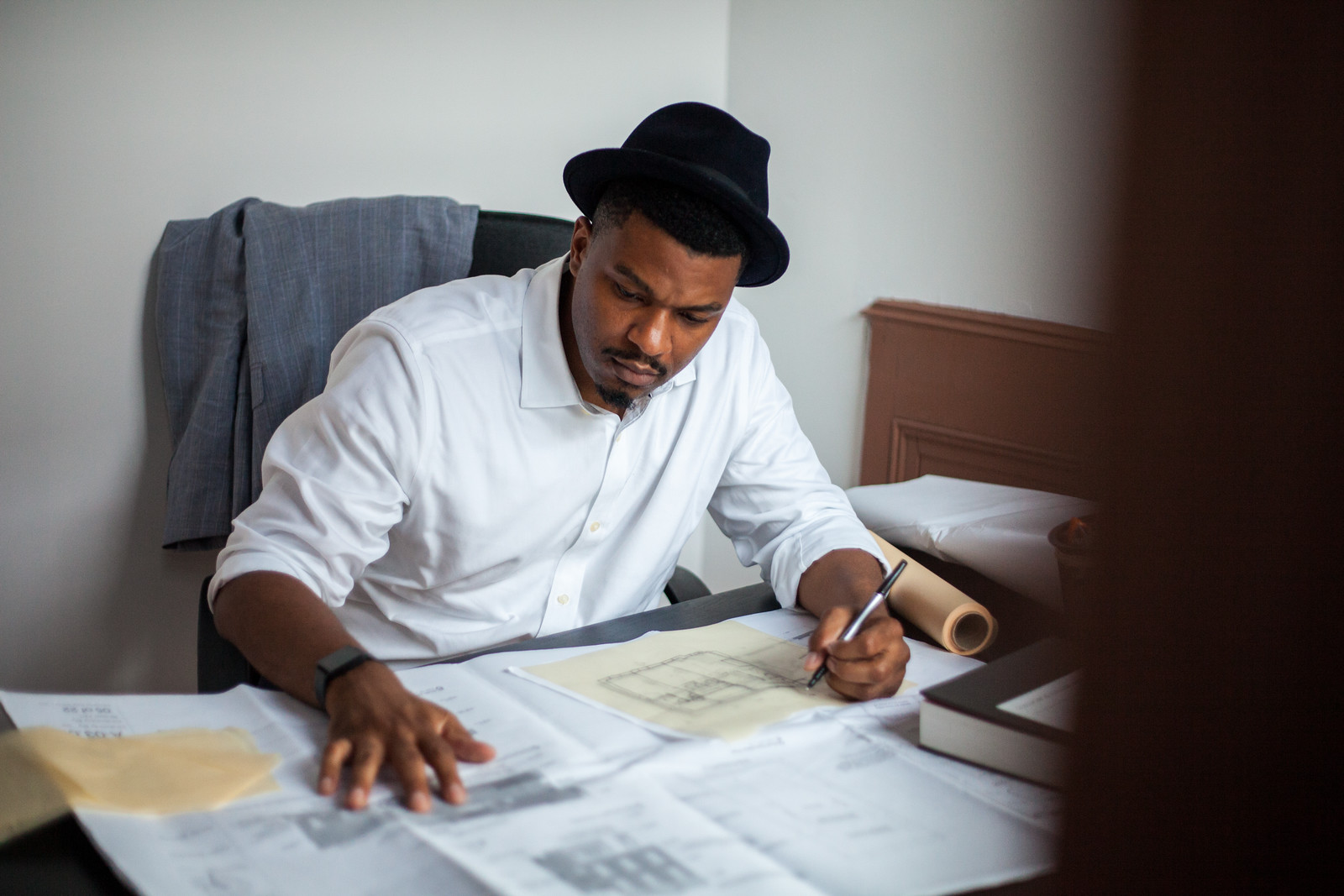
No matter whether you're in an office or lab, you need to learn interpersonal communication skills so you can communicate effectively with coworkers and managers. Other than communicating with colleagues, you must also be able communicate with customers and suppliers.
With an increasing demand for industrial engineering professionals, you can expect to find jobs in a variety of industries. These include engineering service businesses, computer and electronics manufacturers, transportation equipment manufacturers and computer and electronics manufacturers. Several colleges offer 5-year degree programs in industrial engineering. While many graduates are able to find entry-level positions in multiple industries, a few are more focused on certain specialty areas, such as automated manufacturing processes.
FAQ
What is the role of a logistics manager
Logistics managers make sure all goods are delivered on schedule and without damage. This is done by using his/her experience and knowledge of the company's products. He/she should ensure that sufficient stock is available in order to meet customer demand.
What is the importance of automation in manufacturing?
Not only is automation important for manufacturers, but it's also vital for service providers. It allows them to offer services faster and more efficiently. In addition, it helps them reduce costs by reducing human errors and improving productivity.
What are the responsibilities of a manufacturing manager
A manufacturing manager has to ensure that all manufacturing processes work efficiently and effectively. They should be alert for any potential problems in the company and react accordingly.
They should also know how to communicate with other departments such as sales and marketing.
They should be up to date on the latest trends and be able apply this knowledge to increase productivity and efficiency.
What are the 7 Rs of logistics.
The 7R's of Logistics is an acronym for the seven basic principles of logistics management. It was created by the International Association of Business Logisticians and published in 2004 under its "Seven Principles of Logistics Management".
The acronym is composed of the following letters.
-
Responsive - ensure all actions are legal and not harmful to others.
-
Reliable - Have confidence in your ability to fulfill all of your commitments.
-
Be responsible - Use resources efficiently and avoid wasting them.
-
Realistic - Take into consideration all aspects of operations including cost-effectiveness, environmental impact, and other factors.
-
Respectful - show respect and treat others fairly and fairly
-
Resourceful - look for opportunities to save money and increase productivity.
-
Recognizable is a company that provides customers with value-added solutions.
Statistics
- You can multiply the result by 100 to get the total percent of monthly overhead. (investopedia.com)
- It's estimated that 10.8% of the U.S. GDP in 2020 was contributed to manufacturing. (investopedia.com)
- According to a Statista study, U.S. businesses spent $1.63 trillion on logistics in 2019, moving goods from origin to end user through various supply chain network segments. (netsuite.com)
- According to the United Nations Industrial Development Organization (UNIDO), China is the top manufacturer worldwide by 2019 output, producing 28.7% of the total global manufacturing output, followed by the United States, Japan, Germany, and India.[52][53] (en.wikipedia.org)
- Job #1 is delivering the ordered product according to specifications: color, size, brand, and quantity. (netsuite.com)
External Links
How To
How to use 5S to increase Productivity in Manufacturing
5S stands as "Sort", Set In Order", Standardize", Separate" and "Store". Toyota Motor Corporation developed the 5S method in 1954. It assists companies in improving their work environments and achieving higher efficiency.
This approach aims to standardize production procedures, making them predictable, repeatable, and easily measurable. This means that every day tasks such cleaning, sorting/storing, packing, and labeling can be performed. This knowledge allows workers to be more efficient in their work because they are aware of what to expect.
Implementing 5S involves five steps: Sort, Set in Order, Standardize Separate, Store, and Each step involves a different action which leads to increased efficiency. Sorting things makes it easier to find them later. When you arrange items, you place them together. You then organize your inventory in groups. Make sure everything is correctly labeled when you label your containers.
This process requires employees to think critically about how they do their job. Employees must understand why they do certain tasks and decide if there's another way to accomplish them without relying on the old ways of doing things. They will need to develop new skills and techniques in order for the 5S system to be implemented.
In addition to improving efficiency, the 5S system also increases morale and teamwork among employees. They are more motivated to achieve higher efficiency levels as they start to see improvement.