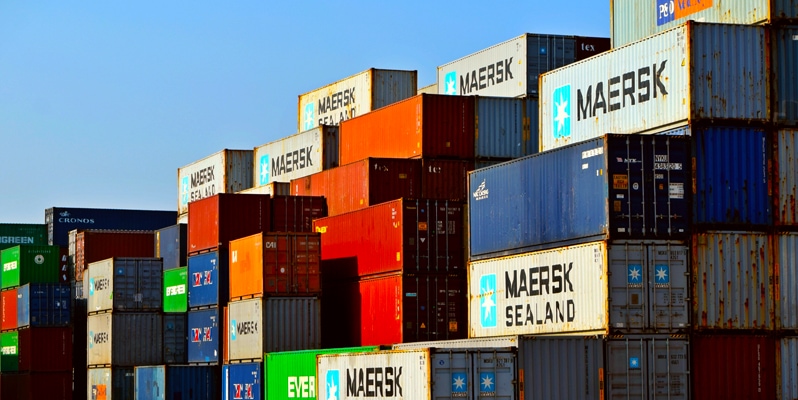
Regardless of what type of engineering career you are interested in, there are plenty of industrial engineering jobs in Dallas. You have many options, including computer and electronic manufacturers as well as transportation equipment manufacturers. Many plants need qualified industrial engineers to ensure smooth production.
Industrial engineers assist in improving processes by identifying potential areas for improvement and then analyzing the results. Industrial engineers often work together with other engineers. These professionals require strong project management skills and math skills in order to implement changes efficiently. Training and reporting are also responsibilities of industrial engineers. They are frequently employed by companies and small- to medium-sized businesses.
Many industrial engineers work as consultants and clients-facing professionals. Some of these roles are in business analysis, data analysis, and software development. Industrial engineers can also be involved in projects that reduce production costs and increase efficiency. Most industrial engineers are hired to work in industries that are focused on manufacturing and transportation equipment. They are also employed in the aviation industry, as well as consumer goods industries. The Bureau of Labor Statistics projects that industrial engineering jobs will grow by 10% in the next decade.
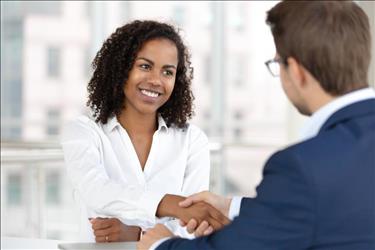
An industrial engineer's most important task is to find wasteful production practices. To identify improvement opportunities, the engineer must work with the right people. They are also responsible to save time and energy. They must be able to use math skills and have a passion for reducing waste. An exciting career as an engineer is possible.
Industrial engineering jobs can be found in Dallas, as well as neighboring cities. Plano McKinney and Frisco all fall within this category. Most of the industrial engineers who work in Dallas are employed in transportation equipment manufacturers. Other industries in need of qualified engineers include professional scientific, technical and engineering services and computer and electronics manufacturing.
Industrial engineers can often be found in multiple roles, from team leader to manager. If you are interested in working in industrial engineering, you may want to begin by applying for a free profile on Monster. This site allows you to set up your resume, create custom job alerts, and receive expert advice. You can start your search today for industrial engineering jobs in Dallas.
You might consider an internship if you are considering a career with industrial engineering. Industrial engineering internships are typically less than 30 minutes away from your home. These internships will help you gain industry experience and valuable skills. Industrial engineers can also take business classes alongside their engineering coursework. Many universities offer business classes as well as parallel IE courses.
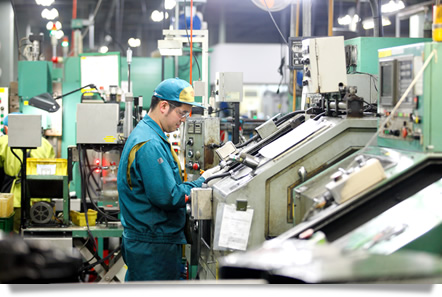
An industrial engineer will be working alongside a team of engineers and analysts to improve processes in your company. You may also be tasked with analyzing labor management standards, tracking labor standards, and maintaining labor management systems.
FAQ
What are the differences between these four types?
Manufacturing refers to the transformation of raw materials into useful products by using machines and processes. Manufacturing can include many activities such as designing and building, testing, packaging shipping, selling, servicing, and other related activities.
Is there anything we should know about Manufacturing Processes prior to learning about Logistics.
No. No. Knowing about manufacturing processes will help you understand how logistics works.
Why is logistics important in manufacturing
Logistics are an essential part of any business. They can help you achieve great success by helping you manage product flow from raw material to finished goods.
Logistics also play a major role in reducing costs and increasing efficiency.
What are the 7 Rs of logistics?
The acronym 7R's of Logistic is an acronym that stands for seven fundamental principles of logistics management. It was developed and published by the International Association of Business Logisticians in 2004 as part of the "Seven Principles of Logistics Management".
The acronym is composed of the following letters.
-
Responsible - ensure that all actions taken are within legal requirements and are not harmful to others.
-
Reliable - You can have confidence that you will fulfill your promises.
-
It is reasonable to use resources efficiently and not waste them.
-
Realistic - Consider all aspects of operations, including environmental impact and cost effectiveness.
-
Respectful - show respect and treat others fairly and fairly
-
Be resourceful: Look for opportunities to save money or increase productivity.
-
Recognizable - Provide value-added services to customers
What's the difference between Production Planning & Scheduling?
Production Planning (PP) is the process of determining what needs to be produced at any given point in time. This is done through forecasting demand and identifying production capacities.
Scheduling involves the assignment of dates and times to tasks in order to complete them within the timeframe.
Statistics
- Many factories witnessed a 30% increase in output due to the shift to electric motors. (en.wikipedia.org)
- Job #1 is delivering the ordered product according to specifications: color, size, brand, and quantity. (netsuite.com)
- It's estimated that 10.8% of the U.S. GDP in 2020 was contributed to manufacturing. (investopedia.com)
- (2:04) MTO is a production technique wherein products are customized according to customer specifications, and production only starts after an order is received. (oracle.com)
- According to the United Nations Industrial Development Organization (UNIDO), China is the top manufacturer worldwide by 2019 output, producing 28.7% of the total global manufacturing output, followed by the United States, Japan, Germany, and India.[52][53] (en.wikipedia.org)
External Links
How To
Six Sigma and Manufacturing
Six Sigma can be described as "the use of statistical process control (SPC), techniques to achieve continuous improvement." Motorola's Quality Improvement Department, Tokyo, Japan, developed it in 1986. Six Sigma's core idea is to improve the quality of processes by standardizing and eliminating defects. This method has been adopted by many companies in recent years as they believe there are no perfect products or services. Six Sigma seeks to reduce variation between the mean production value. This means that if you take a sample of your product, then measure its performance against the average, you can find out what percentage of the time the process deviates from the norm. If this deviation is too big, you know something needs fixing.
Understanding how variability works in your company is the first step to Six Sigma. Once you have this understanding, you will need to identify sources and causes of variation. This will allow you to decide if these variations are random and systematic. Random variations occur when people make mistakes; systematic ones are caused by factors outside the process itself. If you make widgets and some of them end up on the assembly line, then those are considered random variations. If however, you notice that each time you assemble a widget it falls apart in exactly the same spot, that is a problem.
Once you've identified the problem areas you need to find solutions. You might need to change the way you work or completely redesign the process. To verify that the changes have worked, you need to test them again. If they don't work you need to rework them and come up a better plan.