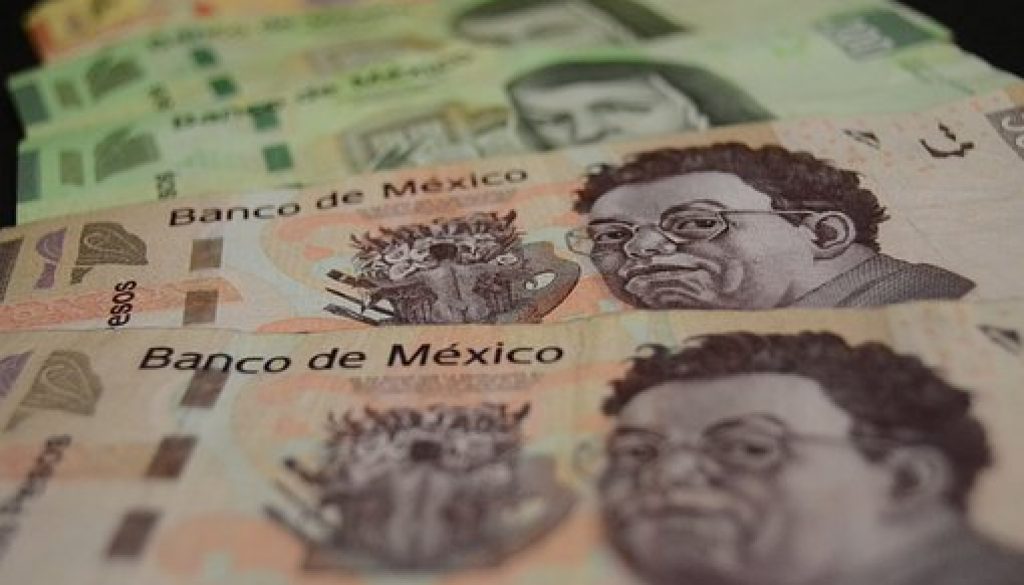
Toyota Production System, formerly known as Just in Time Production, is an integrated sociotechnical system that reduces waste and improves process. It's designed to optimize manufacturing, logistics and customer interaction. It promotes continuous improvement, employee development, and encourages employee advancement. It is also the foundation for Lean Manufacturing. Many American and foreign manufacturing facilities have been equipped with the Toyota Production System.
Sakichi Tomoda, Toyota's founder, developed the Toyota Production System. Sakichi Toyoda studied each production stage of his company and eliminated unnecessary parts. This resulted is a 20% reduction of the build time. It also enabled Toyota to produce a vehicle in half the time of GM. Toyota was however on the verge to go bankrupt in the 1950s.
Taiichi Okno, Toyota's executive in the mid-1940s observed the stocking process at a supermarket. He saw the potential for reducing production time by using Just-in Time methods. Eiji Toyoda was his president and he developed the Toyota Production System. It was created between 1948-1975.
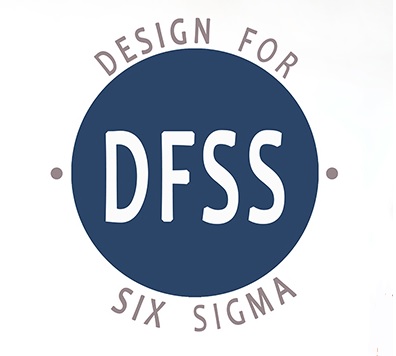
The Toyota Production System was designed to eliminate waste and inconsistency. Kaizen, Japanese for continuous improvement is the basis of the overall philosophy. The Toyota Production System is constantly improved to meet the needs of the company. It promotes learning and utilizes simple, but powerful, low-tech tools that combine with advanced production techniques. It uses innovative information technology and unique management practices.
The Toyota Production System is built on a set of six core principles. Many companies have adapted it, including Boeing, Porsche and Honda. These companies reengineered processes to emulate Toyota's production system.
Toyota Production System includes activities for team building. These activities include weekly local leader safety rounds, which evaluate the performance of staff with key safety initiatives. Everyone is encouraged to contribute ideas and identify opportunities for improvement. This has changed the culture of the company.
Jidoka is another concept. It refers to automation with a human hand. Jidoka encourages workers and managers to review their work and stop making changes when they see problems. Jidoka emphasizes the importance to build things correctly the first time and not ignore problems.
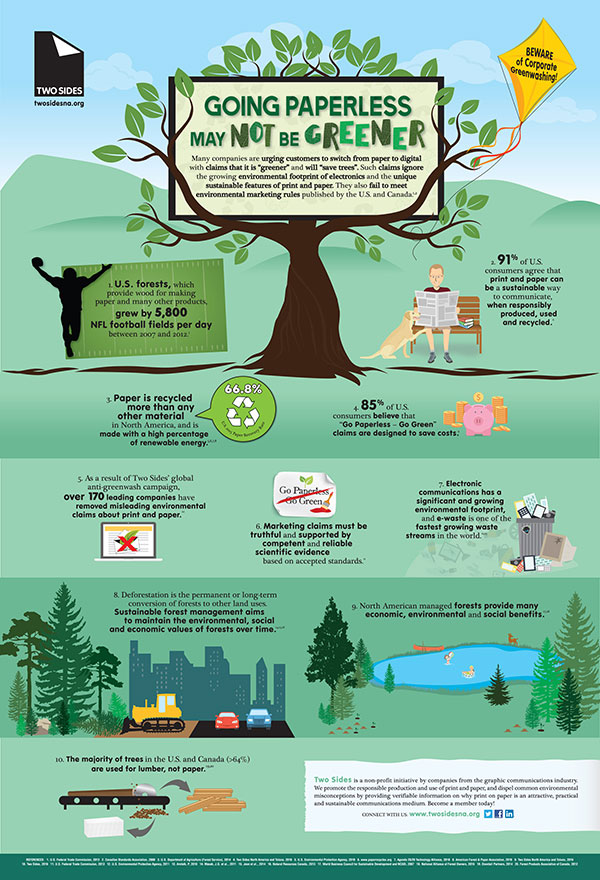
Visual control is also used in the Toyota Production System. It makes work instructions visible on the factory floor. This ensures workers follow the instructions exactly. To ensure quality standards, the company uses poka yoke devices. These devices can also help to identify a red bunny.
The Toyota Production System is not only applicable to manufacturing plants, but also health care. It can also be used to increase patient satisfaction. It can also be applied to critical care and the operating room.
It is possible to improve patient satisfaction as well as health care delivery by using the Toyota Production System. In 2003, the EPA published a study that revealed how Toyota's advancements in waste minimization caught their attention. This resulted in a partnership with many companies, including the St. Bernard Project which employs military veterans.
FAQ
What are the main products of logistics?
Logistics are the activities involved in moving goods from point A to point B.
These include all aspects related to transport such as packaging, loading and transporting, storing, transporting, unloading and warehousing inventory management, customer service. Distribution, returns, recycling are some of the options.
Logisticians ensure that the product is delivered to the correct place, at the right time, and under safe conditions. They assist companies with their supply chain efficiency through information on demand forecasts. Stock levels, production times, and availability.
They coordinate with vendors and suppliers, keep track of shipments, monitor quality standards and perform inventory and order replenishment.
What is the distinction between Production Planning or Scheduling?
Production Planning (PP), or production planning, is the process by which you determine what products are needed at any given time. Forecasting and identifying production capacity are two key elements to this process.
Scheduling is the process of assigning specific dates to tasks so they can be completed within the specified timeframe.
What is the responsibility for a logistics manager
Logistics managers are responsible for ensuring that all goods arrive in perfect condition and on time. This is achieved by using their knowledge and experience with the products of the company. He/she should make sure that enough stock is on hand to meet the demands.
Statistics
- You can multiply the result by 100 to get the total percent of monthly overhead. (investopedia.com)
- In 2021, an estimated 12.1 million Americans work in the manufacturing sector.6 (investopedia.com)
- (2:04) MTO is a production technique wherein products are customized according to customer specifications, and production only starts after an order is received. (oracle.com)
- According to a Statista study, U.S. businesses spent $1.63 trillion on logistics in 2019, moving goods from origin to end user through various supply chain network segments. (netsuite.com)
- According to the United Nations Industrial Development Organization (UNIDO), China is the top manufacturer worldwide by 2019 output, producing 28.7% of the total global manufacturing output, followed by the United States, Japan, Germany, and India.[52][53] (en.wikipedia.org)
External Links
How To
Six Sigma in Manufacturing
Six Sigma is "the application statistical process control (SPC), techniques for continuous improvement." Motorola's Quality Improvement Department developed it at their Tokyo plant in Japan in 1986. Six Sigma is a method to improve quality through standardization and elimination of defects. This method has been adopted by many companies in recent years as they believe there are no perfect products or services. Six Sigma's main objective is to reduce variations from the production average. If you take a sample and compare it with the average, you will be able to determine how much of the production process is different from the norm. If you notice a large deviation, then it is time to fix it.
Understanding how variability works in your company is the first step to Six Sigma. Once you understand this, you can then identify the causes of variation. These variations can also be classified as random or systematic. Random variations are caused when people make mistakes. While systematic variations are caused outside of the process, they can occur. If you make widgets and some of them end up on the assembly line, then those are considered random variations. If however, you notice that each time you assemble a widget it falls apart in exactly the same spot, that is a problem.
Once you identify the problem areas, it is time to create solutions. You might need to change the way you work or completely redesign the process. Once you have implemented the changes, it is important to test them again to ensure they work. If they fail, you can go back to the drawing board to come up with a different plan.