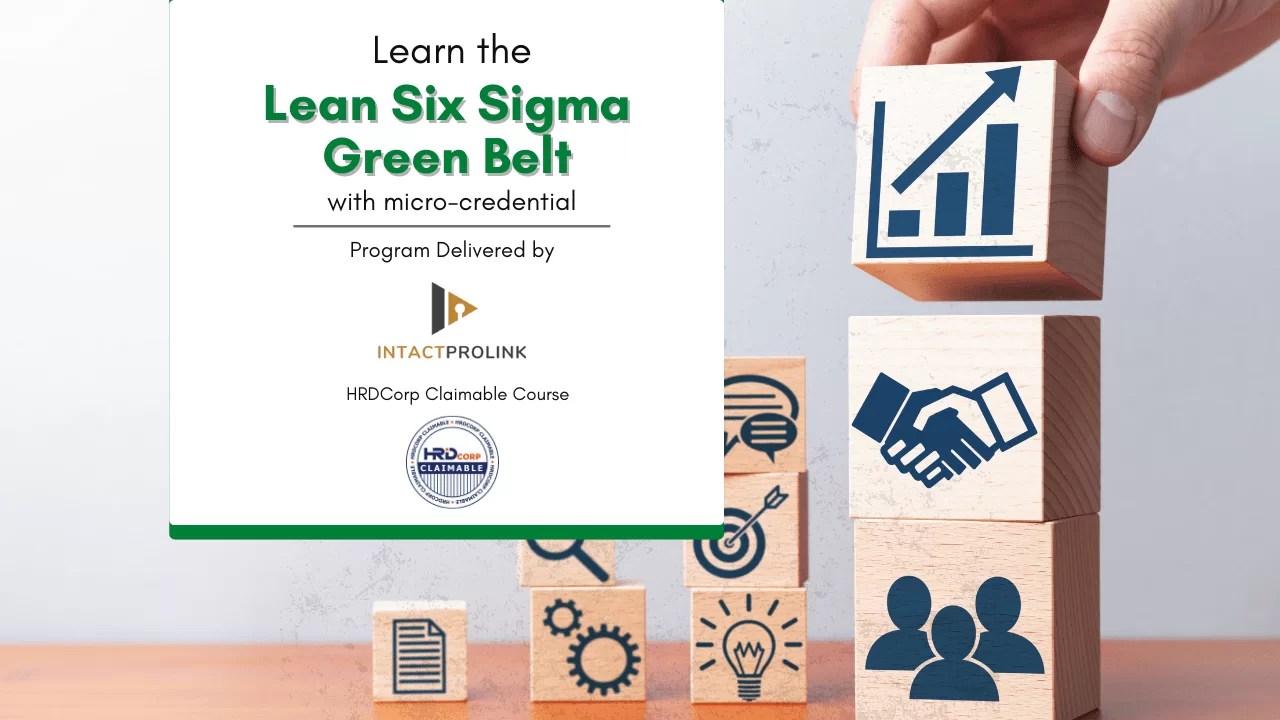
There are a wide variety of logistics jobs in Tampa. Many of these jobs are in the manufacturing, construction or healthcare industries. However you can work in the wholesale trading industry, consulting firms, or other businesses that streamline supply chains.
A degree in logistics could open up many career opportunities. With an associate's degree, you can find entry-level positions like shipping clerks. More advanced jobs are only available to those with bachelor's degrees. You can choose to specialize, depending on your interests and goals, in a particular area of logistics such as supply chain management or warehousing.
Careers in logistics are expanding, with BLS data predicting that employment for these professionals will rise by 5% between 2018 and 2028. Professionals who focus on business operations are projected to see even greater job growth.
A four-year college or community college can offer a degree in logistics. These programs usually offer a wide range of logistics specializations. This allows you to develop more specialized skills, and make you more employable when you advance up the ladder.
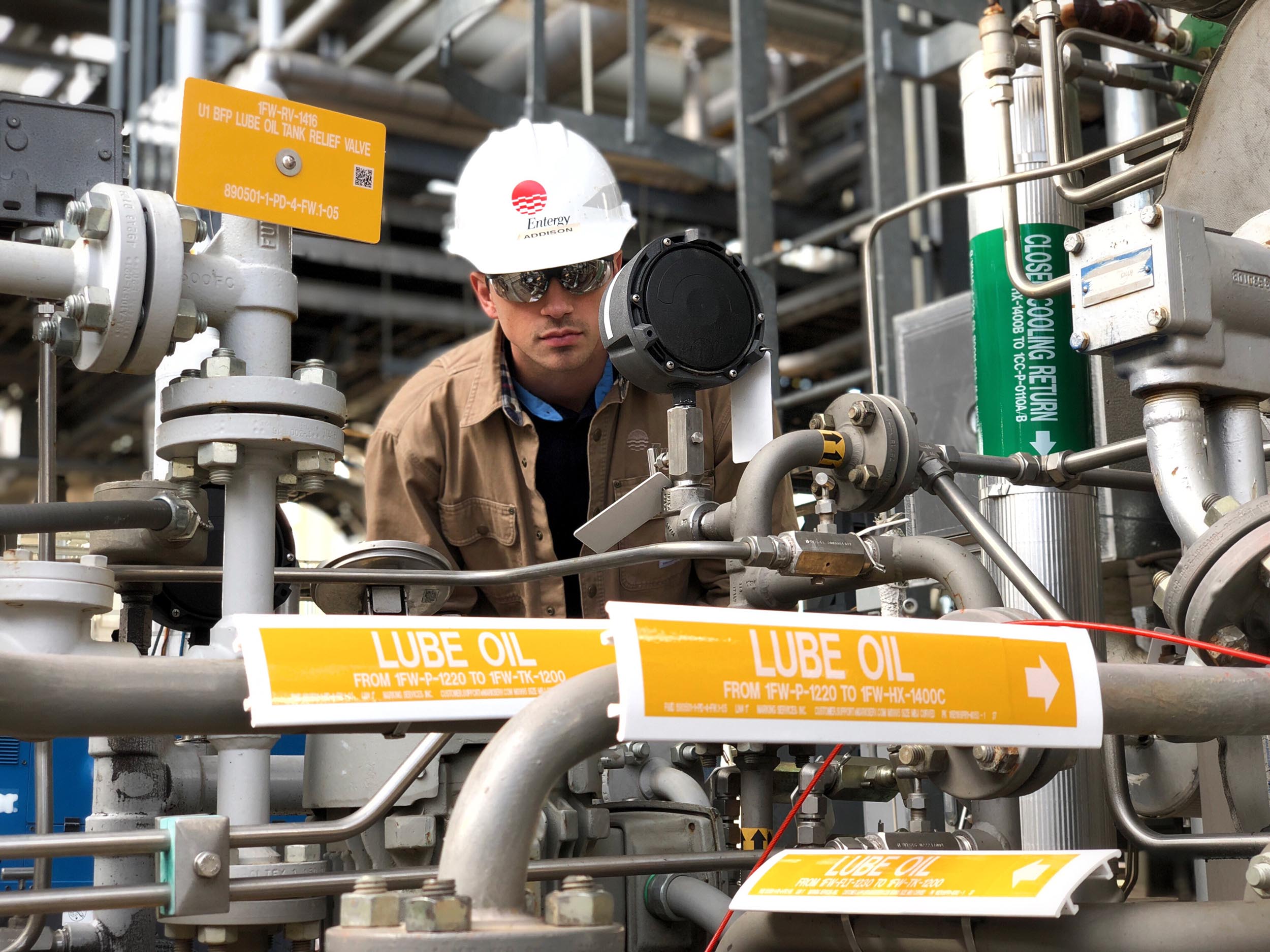
Students should also consider networking and internships in addition to earning a bachelor's. These experiences provide valuable hands-on training in the field and may help you secure your first logistics role.
Logistics has a large and diverse workforce. Job prospects are good. You can find jobs in logistics all over the country, and especially in big and growing states like California or Texas. There are also careers available in specific industries, like oil and gas and aerospace.
When choosing a logistics company, you should consider their size and capabilities. You should choose a 3PL who understands your business, and can provide you with a tailored solution that meets your needs. This will reduce your overall cost and increase your efficiencies.
Your company's supply chain is essential to the success of your business. To ensure that your product arrives at the correct time in perfect condition, you must have the appropriate people and tools. By selecting a third parties logistics provider with experience in your sector and who is able to deliver on time every time, you can increase the efficiency of your supply chains.
Sheer is a Tampa based full-service 3PL. We can help you improve your supply chain's speed and efficiency while lowering costs. We offer our clients a variety services, including transportation management, inventory control, and shipping.
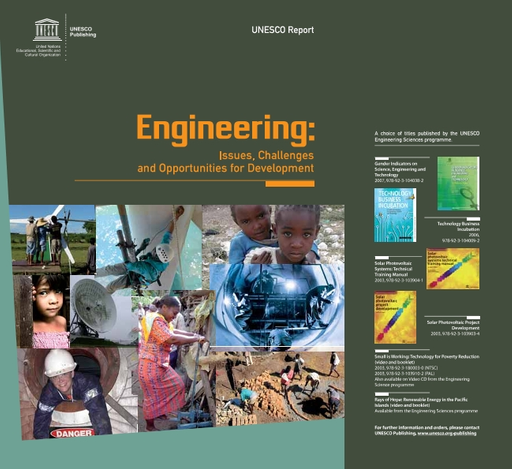
We provide you with a set of technology tools for tracking and managing your supply chains. We offer a suite of cloud-based systems that integrate with your existing ERP system, making it easy to monitor and control all aspects of your business.
Sheer can help you transform your supply chain into an asset by utilizing our multimodal freight network. We can ensure that your products will be delivered on time, safely and securely every single time.
FAQ
What type of jobs is there in logistics
There are many types of jobs in logistics. These are some of the jobs available in logistics:
-
Warehouse workers: They load and unload trucks, pallets, and other cargo.
-
Transport drivers - These are people who drive trucks and trailers to transport goods or perform pick-ups.
-
Freight handlers – They sort and package freight at warehouses.
-
Inventory managers - These are responsible for overseeing the stock of goods in warehouses.
-
Sales reps are people who sell products to customers.
-
Logistics coordinators are responsible for organizing and planning logistics operations.
-
Purchasing agents - They buy goods and services that are necessary for company operations.
-
Customer service representatives - Answer calls and email from customers.
-
Shipping clerks: They process shipping requests and issue bills.
-
Order fillers - These people fill orders based on what has been ordered.
-
Quality control inspectors - They check incoming and outgoing products for defects.
-
Others - There are many types of jobs in logistics such as transport supervisors and cargo specialists.
What is the difference between Production Planning, Scheduling and Production Planning?
Production Planning (PP) is the process of determining what needs to be produced at any given point in time. This can be done by forecasting demand and identifying production capabilities.
Scheduling is the process of assigning specific dates to tasks so they can be completed within the specified timeframe.
What do we need to know about Manufacturing Processes in order to learn more about Logistics?
No. No. But, being familiar with manufacturing processes will give you a better understanding about how logistics works.
Statistics
- Many factories witnessed a 30% increase in output due to the shift to electric motors. (en.wikipedia.org)
- Job #1 is delivering the ordered product according to specifications: color, size, brand, and quantity. (netsuite.com)
- In the United States, for example, manufacturing makes up 15% of the economic output. (twi-global.com)
- You can multiply the result by 100 to get the total percent of monthly overhead. (investopedia.com)
- In 2021, an estimated 12.1 million Americans work in the manufacturing sector.6 (investopedia.com)
External Links
How To
How to Use the Just-In-Time Method in Production
Just-intime (JIT), a method used to lower costs and improve efficiency in business processes, is called just-in-time. This is where you have the right resources at the right time. This means that you only pay the amount you actually use. Frederick Taylor first coined this term while working in the early 1900s as a foreman. After observing how workers were paid overtime for late work, he realized that overtime was a common practice. He decided to ensure workers have enough time to do their jobs before starting work to improve productivity.
JIT is about planning ahead. You should have all the necessary resources ready to go so that you don’t waste money. The entire project should be looked at from start to finish. You need to ensure you have enough resources to tackle any issues that might arise. You'll be prepared to handle any potential problems if you know in advance. You won't have to pay more for unnecessary items.
There are many JIT methods.
-
Demand-driven: This JIT is where you place regular orders for the parts/materials that are needed for your project. This will allow to track how much material has been used up. This will allow to you estimate the time it will take for more to be produced.
-
Inventory-based: This is a type where you stock the materials required for your projects in advance. This allows for you to anticipate how much you can sell.
-
Project-driven: This approach involves setting aside sufficient funds to cover your project's costs. Knowing how much money you have available will help you purchase the correct amount of materials.
-
Resource-based: This is the most common form of JIT. Here you can allocate certain resources based purely on demand. For instance, if you have a lot of orders coming in, you'll assign more people to handle them. If you don't receive many orders, then you'll assign fewer employees to handle the load.
-
Cost-based: This approach is very similar to resource-based. However, you don't just care about the number of people you have; you also need to consider how much each person will cost.
-
Price-based: This is similar to cost-based but instead of looking at individual workers' salaries, you look at the total company price.
-
Material-based: This is quite similar to cost-based, but instead of looking at the total cost of the company, you're concerned with how much raw materials you spend on average.
-
Time-based JIT: A variation on resource-based JIT. Instead of focusing only on how much each employee is costing, you should focus on how long it takes to complete your project.
-
Quality-based: This is yet another variation of resource-based JIT. Instead of thinking about the cost of each employee or the time it takes to produce something, you focus on how good your product quality.
-
Value-based JIT is the newest form of JIT. You don't worry about whether the products work or if they meet customer expectations. Instead, you're focused on how much value you add to the market.
-
Stock-based: This is an inventory-based method that focuses on the actual number of items being produced at any given time. It's useful when you want maximum production and minimal inventory.
-
Just-in time (JIT), planning: This is a combination JIT/supply chain management. This refers to the scheduling of the delivery of components as soon after they are ordered. It's important as it reduces leadtimes and increases throughput.