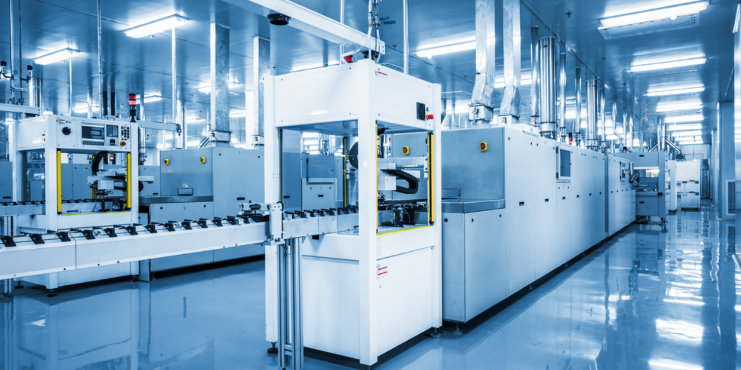
Throughout the years, global supply chains have undergone several changes. They have gone from being an industrial problem into a serious economic problem. It is worth keeping an eye on new developments. Global supply chains are a complex system that interact in many ways.
Global value chains contain a combination of capital, intangibles, flows, and other resources. They are the result of economies, specialization, long-standing relationships, scale, and relationships. Some value chains are capital-intensive while others are more localized.
Global supply chains have become more complex, dynamic and multidimensional. They are an essential component of global trade and the functioning of economies. They are also susceptible for disruptions. These disruptions can be short-term or permanent. It is essential to have a diverse, flexible, and resilient supply network in order to avoid these disruptions. This requires a holistic approach that includes structural reform and strategic initiatives as well as prudent risk management. Identifying the biggest challenges and assessing the solutions is the first step towards building a supply chain that can withstand the next storm.
In addition to assessing the risks of supply chain disruptions, companies should consider the risks associated with manufacturing, labor, energy and materials. In order to assess their impact, they should also simulate extreme supply and demand disruptions. They need to review their critical materials inventories and ensure that they have enough supply to meet any foreseeable demand. To develop a resilient supply system, it requires a strategic approach. This could include prioritizing production, moving manufacturing to more flexible locations and improving supply chain technology.
The COVID-19 outbreak caused major disruptions to global supply networks. Many countries imposed tariffs against one another, while other countries imposed sanctions on the other. These tariffs, as well as other sanctions, have increased trade frictions. They made it difficult for the United States of America to sell certain goods to China and other nations. These disruptions have led to an increase in price inflation. However, they have made companies more aware that their supply networks are fragile and have caused them to rethink how they design and implement their supply systems.
The COVID-19 outbreak caused disruption in global supply networks, but its effects still are being felt. For instance, supply chain disruptions resulting from the Suez Canal blocking have been ongoing for six months. The result has been a dramatic rise in freight costs. In the UK, annual inflation has reached 9%.
It is difficult to ignore that China and the United States are currently in a trade dispute. Supply chain leaders have to question the logic of relying so heavily on outsourced networks. They must consider the risks associated to labor shortages as a result of economic shocks. The benefits of new cross-border regulation and finance, which can increase global integration, should be considered by supply chain leaders.
Even with all the turmoil, the world is still a highly interconnected place. Global integration can be realized when firms take a holistic approach to their supply chain.
FAQ
What are the 7 Rs of logistics?
The acronym 7Rs of Logistics refers to the seven core principles of logistics management. It was created by the International Association of Business Logisticians and published in 2004 under its "Seven Principles of Logistics Management".
The following letters form the acronym:
-
Responsible - ensure that all actions taken are within legal requirements and are not harmful to others.
-
Reliable – have faith in your ability and capability to keep promises.
-
It is reasonable to use resources efficiently and not waste them.
-
Realistic - consider all aspects of operations, including cost-effectiveness and environmental impact.
-
Respectful: Treat others with fairness and equity
-
Resourceful - look for opportunities to save money and increase productivity.
-
Recognizable - provide customers with value-added services.
What is the importance of logistics in manufacturing?
Logistics are an essential part of any business. They enable you to achieve outstanding results by helping manage product flow from raw materials through to finished goods.
Logistics play an important role in reducing costs as well as increasing efficiency.
Why automate your warehouse?
Modern warehousing is becoming more automated. E-commerce has increased the demand for quicker delivery times and more efficient processes.
Warehouses must adapt quickly to meet changing customer needs. In order to do this, they need to invest in technology. Automating warehouses has many benefits. These are just a few reasons to invest in automation.
-
Increases throughput/productivity
-
Reduces errors
-
Accuracy is improved
-
Safety increases
-
Eliminates bottlenecks
-
Allows companies scale more easily
-
Increases efficiency of workers
-
The warehouse can be viewed from all angles.
-
Enhances customer experience
-
Improves employee satisfaction
-
This reduces downtime while increasing uptime
-
Ensures quality products are delivered on time
-
Removing human error
-
It ensures compliance with regulations
How can we increase manufacturing efficiency?
First, determine which factors have the greatest impact on production time. Then we need to find ways to improve these factors. If you aren't sure where to begin, think about the factors that have the greatest impact on production time. Once you've identified them, try to find solutions for each of those factors.
What is meant by manufacturing industries?
Manufacturing Industries are those businesses that make products for sale. Consumers are the people who purchase these products. To accomplish this goal, these companies employ a range of processes including distribution, sales, management, and production. They create goods from raw materials, using machines and various other equipment. This covers all types of manufactured goods including clothing, food, building supplies and furniture, as well as electronics, tools, machinery, vehicles and pharmaceuticals.
Statistics
- (2:04) MTO is a production technique wherein products are customized according to customer specifications, and production only starts after an order is received. (oracle.com)
- [54][55] These are the top 50 countries by the total value of manufacturing output in US dollars for its noted year according to World Bank.[56] (en.wikipedia.org)
- Job #1 is delivering the ordered product according to specifications: color, size, brand, and quantity. (netsuite.com)
- It's estimated that 10.8% of the U.S. GDP in 2020 was contributed to manufacturing. (investopedia.com)
- According to the United Nations Industrial Development Organization (UNIDO), China is the top manufacturer worldwide by 2019 output, producing 28.7% of the total global manufacturing output, followed by the United States, Japan, Germany, and India.[52][53] (en.wikipedia.org)
External Links
How To
How to Use Lean Manufacturing for the Production of Goods
Lean manufacturing is a management system that aims at increasing efficiency and reducing waste. It was developed in Japan during the 1970s and 1980s by Taiichi Ohno, who received the Toyota Production System (TPS) award from TPS founder Kanji Toyoda. Michael L. Watkins published the "The Machine That Changed the World", the first book about lean manufacturing. It was published in 1990.
Lean manufacturing is often defined as a set of principles used to improve the quality, speed, and cost of products and services. It emphasizes the elimination and minimization of waste in the value stream. The five-steps of Lean Manufacturing are just-in time (JIT), zero defect and total productive maintenance (TPM), as well as 5S. Lean manufacturing seeks to eliminate non-value added activities, such as inspection, work, waiting, and rework.
Lean manufacturing improves product quality and costs. It also helps companies reach their goals quicker and decreases employee turnover. Lean manufacturing is considered one of the most effective ways to manage the entire value chain, including suppliers, customers, distributors, retailers, and employees. Many industries worldwide use lean manufacturing. Toyota's philosophy is the foundation of its success in automotives, electronics and appliances, healthcare, chemical engineers, aerospace, paper and food, among other industries.
Five basic principles of Lean Manufacturing are included in lean manufacturing
-
Define Value - Identify the value your business adds to society and what makes you different from competitors.
-
Reduce Waste - Eliminate any activity that doesn't add value along the supply chain.
-
Create Flow. Ensure that your work is uninterrupted and flows seamlessly.
-
Standardize and simplify – Make processes as repeatable and consistent as possible.
-
Build Relationships- Develop personal relationships with both internal as well as external stakeholders.
Lean manufacturing, although not new, has seen renewed interest in the economic sector since 2008. To increase their competitiveness, many businesses have turned to lean manufacturing. Some economists even believe that lean manufacturing can be a key factor in economic recovery.
Lean manufacturing has many benefits in the automotive sector. These include improved customer satisfaction, reduced inventory levels, lower operating costs, increased productivity, and better overall safety.
The principles of lean manufacturing can be applied in almost any area of an organization. This is because it ensures efficiency and effectiveness in all stages of the value chain.
There are three main types of lean manufacturing:
-
Just-in Time Manufacturing (JIT), also known as "pull system": This form of lean manufacturing is often referred to simply as "pull". JIT is a method in which components are assembled right at the moment of use, rather than being manufactured ahead of time. This approach reduces lead time, increases availability and reduces inventory.
-
Zero Defects Manufacturing (ZDM),: ZDM is a system that ensures no defective units are left the manufacturing facility. Repairing a part that is damaged during assembly should be done, not scrapping. This is true even for finished products that only require minor repairs prior to shipping.
-
Continuous Improvement (CI), also known as Continuous Improvement, aims at improving the efficiency of operations through continuous identification and improvement to minimize or eliminate waste. Continuous improvement refers to continuous improvement of processes as well people and tools.