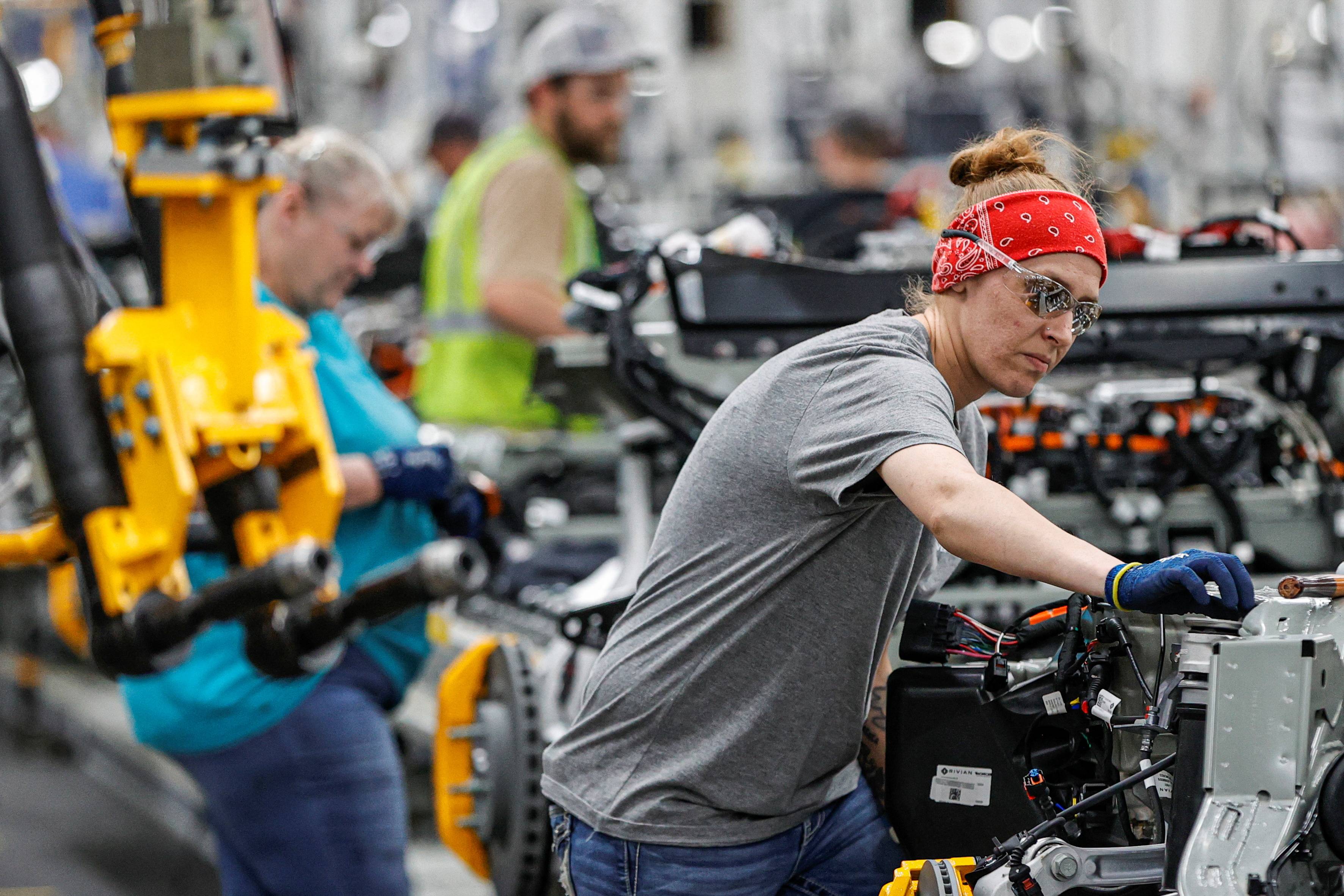
Logistics coordinators are responsible for ensuring goods arrive at their destination on time, and in the most cost-effective manner possible. This field will help you ensure that goods arrive at your customer's doorstep in a timely manner. This article will provide more information about logistics. In this article, you'll learn more about the roles and responsibilities of inventory analysts, customer service specialists, and supply-chain managers. These are just a few of the most prestigious jobs you'll find in logistics.
Logistics coordinator
If you want to start a career as a logistics coordinator, you can find thousands of jobs on Monster. This job requires lots of hands-on experience. Candidates who have little or no industry experience will be expected to complete the apprenticeship or internship. If you have extensive previous experience in the logistics field, you may also want to consider applying for a job as a logistics coordinator.
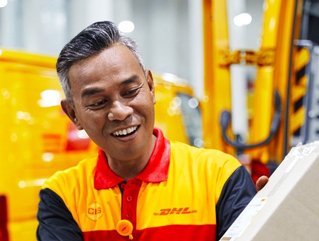
Customer service specialist
A customer service specialist oversees the delivery and management of customer service. They maintain contact with customers, coordinate inland transport, and address customer concerns and complaints. In addition to managing customer relationships, they also coordinate appointments, document special service needs, and schedule transportation and warehousing processes. As a customer services specialist, you will also coordinate the documentation and ensure that all necessary documents are properly documented to ensure timely delivery and budget compliance.
Analyst for inventory
An Inventory Analyst is responsible to maintain service level and improve inventory productivity. Their primary responsibilities include the overall order fulfillment for TSC Feed programs, as well as managing the day-to-day activities of inventory replenishment. They support assortment and merchandise plans by managing inventory levels in their assigned product categories. They collect data and analyze trends to plan article-site replenishment at stores. They may also assist in promotion and marketing. They are responsible for analyzing sales data, and developing new strategies to increase business efficiency.
Supply chain manager
A supply chain manager oversees the movement and distribution of materials and goods from suppliers, manufacturers, customers, and other parties. The job requires a broad set of skills. Employers also prefer applicants with a master's degree in business administration. There are many options to get a job as a supply chain manager. Learn more about this field. If you're thinking of going into supply chain management, consider getting an associate's degree in business administration first.
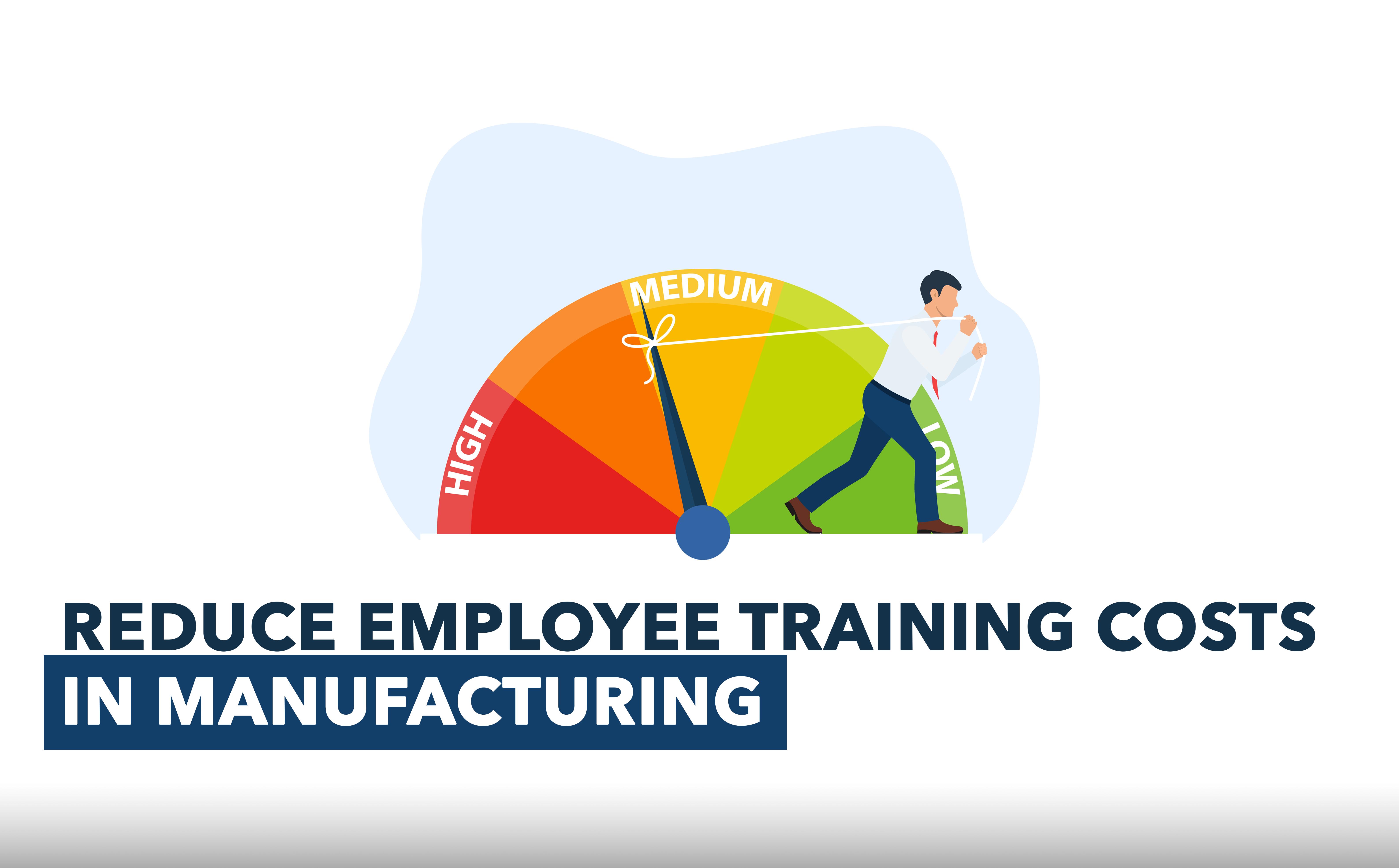
Freight agent
Make sure you include a section on the responsibilities of your freight agent and cargo when creating your job descriptions. A job description should list the essential responsibilities of the position so that potential applicants are able to easily see what they will need to do each day. Make sure to use strong action verbs in your description to get the attention of qualified applicants. Your job description should include a detailed list indicating the qualifications you will need to fill this role.
FAQ
What does warehouse mean?
A warehouse or storage facility is where goods are stored before they are sold. It can be an indoor space or an outdoor area. It may also be an indoor space or an outdoor area.
What are the responsibilities of a manufacturing manager
A manufacturing manager must ensure that all manufacturing processes are efficient and effective. They should also be aware and responsive to any company problems.
They should also know how to communicate with other departments such as sales and marketing.
They should be informed about industry trends and be able make use of this information to improve their productivity and efficiency.
What is the difference between Production Planning and Scheduling?
Production Planning (PP) is the process of determining what needs to be produced at any given point in time. This is done through forecasting demand and identifying production capacities.
Scheduling is the process that assigns dates to tasks so they can get completed within a given timeframe.
What is the responsibility of a production planner?
Production planners make sure that every aspect of the project is delivered on-time, within budget, and within schedule. They make sure that the product and services meet client expectations.
How can manufacturing efficiency improved?
First, determine which factors have the greatest impact on production time. We must then find ways that we can improve these factors. If you aren't sure where to begin, think about the factors that have the greatest impact on production time. Once you identify them, look for solutions.
Statistics
- In 2021, an estimated 12.1 million Americans work in the manufacturing sector.6 (investopedia.com)
- According to the United Nations Industrial Development Organization (UNIDO), China is the top manufacturer worldwide by 2019 output, producing 28.7% of the total global manufacturing output, followed by the United States, Japan, Germany, and India.[52][53] (en.wikipedia.org)
- Job #1 is delivering the ordered product according to specifications: color, size, brand, and quantity. (netsuite.com)
- [54][55] These are the top 50 countries by the total value of manufacturing output in US dollars for its noted year according to World Bank.[56] (en.wikipedia.org)
- It's estimated that 10.8% of the U.S. GDP in 2020 was contributed to manufacturing. (investopedia.com)
External Links
How To
How to Use Six Sigma in Manufacturing
Six Sigma is "the application statistical process control (SPC), techniques for continuous improvement." It was developed by Motorola's Quality Improvement Department at their plant in Tokyo, Japan, in 1986. Six Sigma's main goal is to improve process quality by standardizing processes and eliminating defects. In recent years, many companies have adopted this method because they believe there is no such thing as perfect products or services. Six Sigma aims to reduce variation in the production's mean value. You can calculate the percentage of deviation from the norm by taking a sample of your product and comparing it to the average. If this deviation is too big, you know something needs fixing.
Understanding how variability works in your company is the first step to Six Sigma. Once you have a good understanding of the basics, you can identify potential sources of variation. Also, you will need to identify the sources of variation. Random variations occur when people make mistakes; systematic ones are caused by factors outside the process itself. These are, for instance, random variations that occur when widgets are made and some fall off the production line. You might notice that your widgets always fall apart at the same place every time you put them together.
Once you have identified the problem, you can design solutions. It might mean changing the way you do business or redesigning it entirely. To verify that the changes have worked, you need to test them again. If they don’t work, you’ll need to go back and rework the plan.