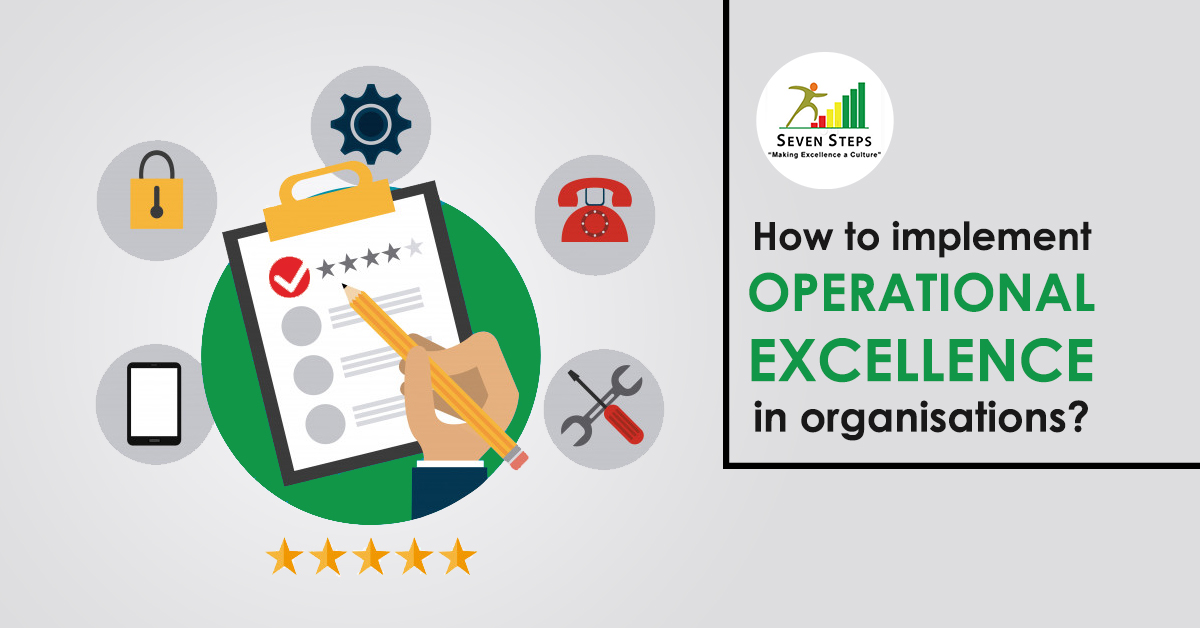
You've found the right place if you are looking for news on manufacturing. Fusion 360 community members discuss the week's happenings and share news regarding manufacturing innovation. Fusion 360 covers all aspects of the industry, including Alexandria Industries and Festo's expansion plans. Fusion 360 covers a broad range of topics, from product launches to news about additive manufacture. Here are some recent articles about manufacturing innovations. Learn more by reading the following articles.
Alexandria Industries
The recent Alexandria Industries, manufacturing news focuses on expanding their operation in Douglas County, Minnesota. While they currently employ 480 people, the company is investing several million dollars in the new facility to grow even more. Although Alexandria Industries has long outpaced employment and revenue levels prior to the recession, they still struggle to find qualified applicants for 50 new jobs. These positions have a starting salary of $15- $30 per hour and include benefits. Alexandria Industries is looking for a new career.
Alexandria Industries recently promoted new management in order to support their growth. Jonathan D. Olson is the new CFO of Alexandria Industries. He is committed investing in the company and its employees. He was also appointed the company's CFO. He is looking to improve the working environment of employees and invest heavily in training programs. Alexandria Plastics, Inc., a manufacturer and distributor of foam-molded and plastic injection parts, will be integrated into this acquisition, which will enhance the company’s capabilities.
Festo U.S. expansion plans
Festo Corp. recently announced expansion plans in North America for its manufacturing operations. The company plans to triple its Mason footprint and create 350 new jobs. This expansion will generate new jobs for the next five-years at a cost of $90million. Festo will offer industrial training solutions as well as support services. The expansion will include a new Didactic learning center to support manufacturing companies and colleges in the Tristate area.
The expansion will create a new facility in Mason, Ohio, dedicated to manufacturing automation components. This new facility will house both the Research and Development Center and Global Production Center. Each facility will have more than 1000 employees when it is completed. In addition to creating jobs, the company plans on establishing a new research-and-development center to improve automation systems. This expansion is part in a larger strategy to concentrate on the U.S. markets.
Additive Manufacturing
With the advancement of technology, manufacturers have begun to see the benefits of additive manufacturing in the manufacturing process. To reach the global marketplace, several companies have made partnerships. Voxeljet and AGC Ceramic are two examples of such partnerships. AGC Ceramic is an American glass and ceramic company. Voxeljet is partnering with AGC Ceramic to bring Brightorb, an innovative ceramic material, to the market and optimize VX1000 for 3D printing ceramic powder. Stratasys has partnered up with Tata Technologies in order to promote additive manufacturing technology in India.
Collaboration agreements are not the only thing that is being done for additive manufacturing. New technologies are also being developed. Optimus 3D has acquired a fourth Renishaw metal additive manufacturing system. The company has expanded its 3D printing equipment portfolio to include powder metal. This development will ensure that additive manufacturing becomes an integral part advanced PLM. Advanced PLM will be more IoT-oriented, integrated, and flexible. These innovations will facilitate the rapid growth and diversification of many industries.
Collaborative Manufacturing
What is collaborative manufacturing? Collaborative manufacturing is based on input directly from the plant floor systems. This information is a key part of the management system. It also involves an interactive process between the manufacturing and design team. Collaborative Manufacturing can improve productivity, quality, and reduce the number required to perform each production process. But what are the benefits of collaborative manufacturing? Let's take a look at some examples. How can collaborative production improve plant performance? Learn more.
Collaboration is a growing trend in many industries. It can be used to improve product design, reduce costs, increase product development, and sync inventory with the supply chain. Collaborative manufacturing also helps reduce time to market and volume. It can also cut down on the manufacturing cycle time between designated suppliers. Collaborative manufacturing can bring significant benefits to everyone, so it is crucial for companies. But it is not for every company. Be sure to consider the benefits before you adopt collaborative manufacturing.
FAQ
What are the 7 Rs of logistics management?
The 7R's of Logistics is an acronym for the seven basic principles of logistics management. It was published in 2004 by the International Association of Business Logisticians as part of their "Seven Principles of Logistics Management" series.
The acronym consists of the following letters:
-
Responsible - to ensure that all actions are within the legal requirements and are not detrimental to others.
-
Reliable - Have confidence in your ability to fulfill all of your commitments.
-
Use resources effectively and sparingly.
-
Realistic - consider all aspects of operations, including cost-effectiveness and environmental impact.
-
Respectful - show respect and treat others fairly and fairly
-
Resourceful - look for opportunities to save money and increase productivity.
-
Recognizable - provide customers with value-added services.
What are manufacturing and logistic?
Manufacturing refers to the process of making goods using raw materials and machines. Logistics manages all aspects of the supply chain, including procurement, production planning and distribution, inventory control, transportation, customer service, and transport. Manufacturing and logistics can often be grouped together to describe a larger term that covers both the creation of products, and the delivery of them to customers.
What are the products of logistics?
Logistics involves the transportation of goods from point A and point B.
They encompass all aspects transport, including packaging and loading, transporting, storage, unloading.
Logisticians ensure that products reach the right destination at the right moment and under safe conditions. Logisticians assist companies in managing their supply chains by providing information such as demand forecasts, stock levels and production schedules.
They keep track and monitor the transit of shipments, maintain quality standards, order replenishment and inventories, coordinate with suppliers, vendors, and provide support for sales and marketing.
Is it necessary to be familiar with Manufacturing Processes before we learn about Logistics.
No. No. Understanding the manufacturing process will allow you to better understand logistics.
What are the responsibilities of a manufacturing manager
A manufacturing manager has to ensure that all manufacturing processes work efficiently and effectively. They should be alert for any potential problems in the company and react accordingly.
They should also be able communicate with other departments, such as sales or marketing.
They should also be aware of the latest trends in their industry and be able to use this information to help improve productivity and efficiency.
What is the distinction between Production Planning or Scheduling?
Production Planning (PP) is the process of determining what needs to be produced at any given point in time. This can be done by forecasting demand and identifying production capabilities.
Scheduling is the process of assigning specific dates to tasks so they can be completed within the specified timeframe.
Statistics
- Many factories witnessed a 30% increase in output due to the shift to electric motors. (en.wikipedia.org)
- (2:04) MTO is a production technique wherein products are customized according to customer specifications, and production only starts after an order is received. (oracle.com)
- In the United States, for example, manufacturing makes up 15% of the economic output. (twi-global.com)
- Job #1 is delivering the ordered product according to specifications: color, size, brand, and quantity. (netsuite.com)
- According to a Statista study, U.S. businesses spent $1.63 trillion on logistics in 2019, moving goods from origin to end user through various supply chain network segments. (netsuite.com)
External Links
How To
How to Use 5S for Increasing Productivity in Manufacturing
5S stands for "Sort", "Set In Order", "Standardize", "Separate" and "Store". Toyota Motor Corporation was the first to develop the 5S approach in 1954. This methodology helps companies improve their work environment to increase efficiency.
This method aims to standardize production processes so that they are repeatable, measurable and predictable. This means that daily tasks such as cleaning and sorting, storage, packing, labeling, and packaging are possible. These actions allow workers to perform their job more efficiently, knowing what to expect.
Five steps are required to implement 5S: Sort, Set In Order, Standardize. Separate. Each step involves a different action which leads to increased efficiency. You can make it easy for people to find things later by sorting them. When you arrange items, you place them together. After you have divided your inventory into groups you can store them in easy-to-reach containers. Make sure everything is correctly labeled when you label your containers.
This requires employees to critically evaluate how they work. Employees need to understand the reasons they do certain jobs and determine if there is a better way. To be successful in the 5S system, employees will need to acquire new skills and techniques.
The 5S method not only increases efficiency but also boosts morale and teamwork. They feel more motivated to work towards achieving greater efficiency as they see the results.