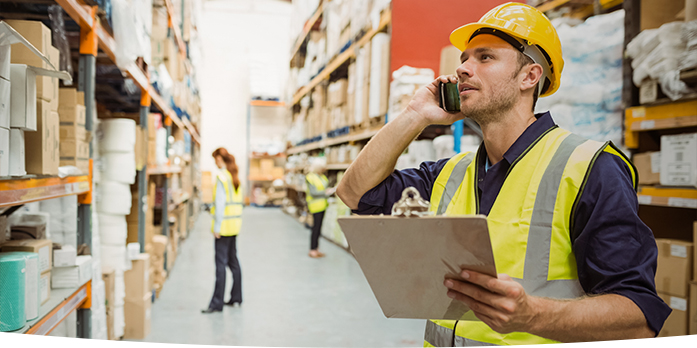
It's easy to overlook the fact that many things are still made in America, especially when globalization has forced factories out of the country. The United States produces a wide range of popular products, such as candy and reliable vehicles. It also produces some of the most loved beers in the United States.
Find American-Made Products
Made in America is an iconic label that evokes patriotism while also delivering a silent promise of high quality. It's a sign that the company is ensuring the safety of its workers and the future of its country.
The labeling process is equally important. The Federal Trade Commission sets strict guidelines for how manufacturers use this phrase.
In general, it's only possible to claim that a product is made in America if all of the significant components, labor, and processing were done in the United States. A manufacturer may make a qualified claim to let consumers know, however that the item was made in America, but from only certain parts.
Some companies that advertise "Made in the USA" may not have met all of these requirements, according to FTC attorney Julia Solomon Ensor. This is especially true in the case of products that are assembled in the United States but then shipped to a distribution center in another country, like a gas grill.
The Federal Trade Commission cracks down on companies who claim to be "Made in the USA", but do not meet the requirements. The Federal Trade commission explains the need for the terms to be clearly defined. They must also cover the entire product.
Searching for items that were made in the United States can be done by both category and country. For example, if you're shopping for bedding or furniture, you can shop through our link and narrow your search by country of origin.
If you want to know if a certain item is made in the United States, you can search for the manufacturer's name in the search field. This is a way to show the companies you support that they should do more to promote American manufacturing.
Check out the Made in the USA site from a company such as Wayfair. They do a great job labeling their products according to country of origin. There is a whole section on their website dedicated to products made in the United States.
The websites of these companies are full of items made in the United States. But if there is anything you want to know about a particular item, feel free to contact them by clicking on our link. They'll respond as soon a possible.
It's worth checking these retailers out to see if you can find something you need for your home, whether it's clothing, toys, books, or anything else. There are over 500 "Made in USA" products on their website, making it a great starting point for your search.
FAQ
What are manufacturing and logistics?
Manufacturing is the act of producing goods from raw materials using machines and processes. Logistics is the management of all aspects of supply chain activities, including procurement, production planning, distribution, warehousing, inventory control, transportation, and customer service. Manufacturing and logistics are often considered together as a broader term that encompasses both the process of creating products and delivering them to customers.
What does the term manufacturing industries mean?
Manufacturing Industries is a group of businesses that produce goods for sale. Consumers are those who purchase these products. These companies use various processes such as production, distribution, retailing, management, etc., to fulfill this purpose. They produce goods from raw materials by using machines and other machinery. This includes all types manufactured goods such as clothing, building materials, furniture, electronics, tools and machinery.
What are the goods of logistics?
Logistics refers to all activities that involve moving goods from A to B.
They include all aspects of transport, including packaging, loading, transporting, unloading, storing, warehousing, inventory management, customer service, distribution, returns, and recycling.
Logisticians ensure that the right product reaches the right place at the right time and under safe conditions. They provide information on demand forecasts as well stock levels, production schedules and availability of raw material.
They keep track and monitor the transit of shipments, maintain quality standards, order replenishment and inventories, coordinate with suppliers, vendors, and provide support for sales and marketing.
What is it like to manage a logistics company?
It takes a lot of skills and knowledge to run a successful logistics business. Good communication skills are essential to effectively communicate with your suppliers and clients. You need to understand how to analyze data and draw conclusions from it. You must be able to work well under pressure and handle stressful situations. You need to be innovative and creative to come up with new ways to increase efficiency. You will need strong leadership skills to motivate and direct your team members towards achieving their organizational goals.
To meet tight deadlines, you must also be efficient and organized.
What is the role of a manager in manufacturing?
A manufacturing manager has to ensure that all manufacturing processes work efficiently and effectively. They should be alert for any potential problems in the company and react accordingly.
They should also learn how to communicate effectively with other departments, including sales and marketing.
They should be informed about industry trends and be able make use of this information to improve their productivity and efficiency.
Statistics
- It's estimated that 10.8% of the U.S. GDP in 2020 was contributed to manufacturing. (investopedia.com)
- Many factories witnessed a 30% increase in output due to the shift to electric motors. (en.wikipedia.org)
- [54][55] These are the top 50 countries by the total value of manufacturing output in US dollars for its noted year according to World Bank.[56] (en.wikipedia.org)
- In 2021, an estimated 12.1 million Americans work in the manufacturing sector.6 (investopedia.com)
- According to a Statista study, U.S. businesses spent $1.63 trillion on logistics in 2019, moving goods from origin to end user through various supply chain network segments. (netsuite.com)
External Links
How To
How to use 5S to increase Productivity in Manufacturing
5S stands to stand for "Sort", “Set In Order", “Standardize", and "Store". Toyota Motor Corporation developed the 5S method in 1954. It assists companies in improving their work environments and achieving higher efficiency.
This method has the basic goal of standardizing production processes to make them repeatable. It means tasks like cleaning, sorting or packing, labeling, and storing are done every day. Through these actions, workers can perform their jobs more efficiently because they know what to expect from them.
Implementing 5S involves five steps: Sort, Set in Order, Standardize Separate, Store, and Each step involves a different action which leads to increased efficiency. You can make it easy for people to find things later by sorting them. You arrange items by placing them in an order. After you have divided your inventory into groups you can store them in easy-to-reach containers. Finally, when you label your containers, you ensure everything is labeled correctly.
This process requires employees to think critically about how they do their job. Employees need to understand the reasons they do certain jobs and determine if there is a better way. To be successful in the 5S system, employees will need to acquire new skills and techniques.
The 5S method increases efficiency and morale among employees. As they begin to see improvements, they feel motivated to continue working towards the goal of achieving higher levels of efficiency.