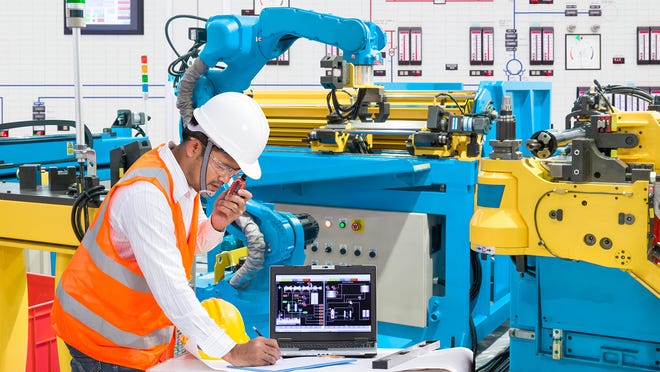
Toyota Production System, originally called Just-in-Time production was an integrated sociotechnical and technological system used to eliminate waste from processes and improve them. It's designed to optimize manufacturing, logistics and customer interaction. It is also a catalyst for continuous improvement and employee training. It is also the foundation of Lean Manufacturing. The Toyota Production System is used in many manufacturing facilities across the United States and internationally.
SakichiToyoda, founder of Toyota was the one who developed Toyota Production System. He examined every stage of his company's production process and removed any unneeded parts. This led to a 20% drop in build times. Toyota was able to make a vehicle in half as fast as GM. However, Toyota was on the verge of bankruptcy by the early 1950s.
Taiichi Ohno was a Toyota executive who observed how supermarket shelves were stockpiled in the mid-1940s. He discovered that Just-in-Time production methods could help save time. Eiji Toyoda was his president and he developed the Toyota Production System. It was created between 1948-1975.
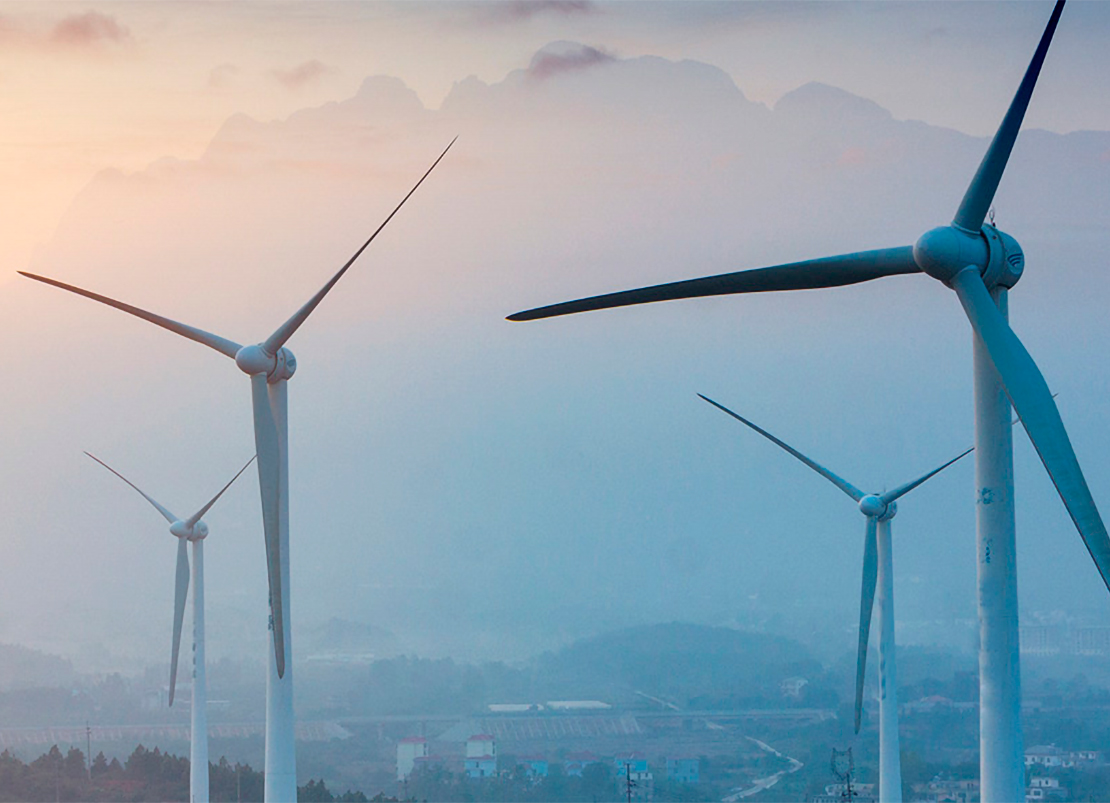
Toyota Production System was developed to eliminate wastefulness and inconsistency. Kaizen, Japanese for continuous improvement is the basis of the overall philosophy. Toyota Production System continues to be improved in order to meet its customers' needs. It drives learning throughout the company and uses simple yet effective low-tech tools combined with advanced production techniques. It also utilizes innovative information technology as well unique social/management techniques.
Six core principles form the foundation of Toyota Production System. This system has been modified by many companies, including Boeing and Porsche. These companies reengineered the processes to imitate Toyota's production system.
Toyota Production System includes activities for team building. These activities include safety rounds at the local level, where staff are evaluated on their compliance with safety measures. The team is encouraged to exchange ideas and look for ways to improve. This has influenced the culture of the company.
Jidoka, another concept, refers automating processes with human touch. Jidoka encourages workers check their work, and stop production when they spot problems. Jidoka emphasizes the importance to build things correctly the first time and not ignore problems.
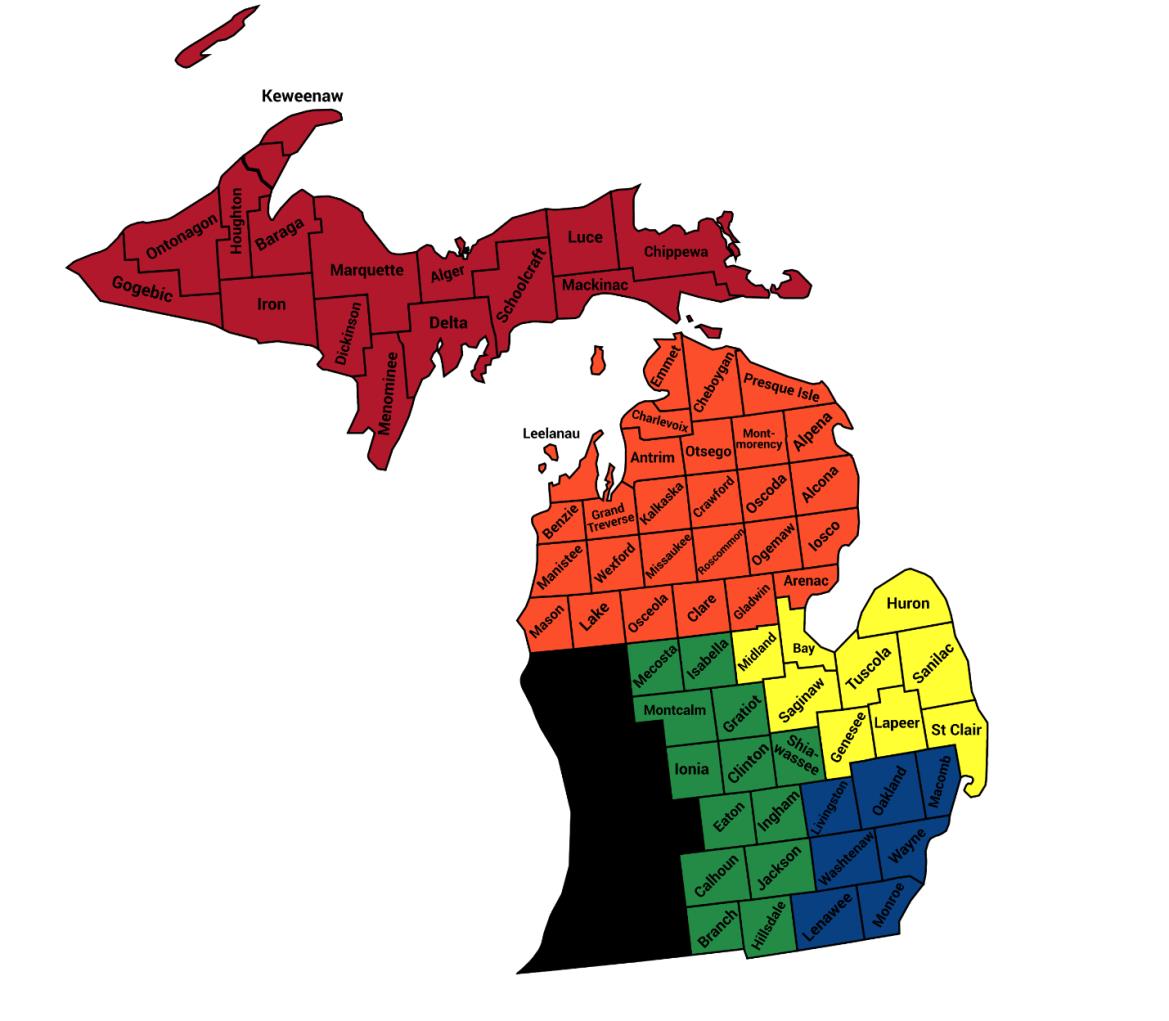
The Toyota Production System also employs visual control. This system makes instructions for workers visible on the factory floor. This ensures that workers follow instructions correctly. To ensure quality standards, the company uses poka yoke devices. These devices can also verify identification of red rabbits.
Toyota Production System can be used to produce plants as well as health care. It can be used to improve patient satisfaction. It can be used in critical care and the operating rooms.
It's possible to improve patient care and satisfaction using the Toyota Production System. In 2003, an EPA case study reported that Toyota's efforts in waste reduction had caught the EPA’s attention. This led to several partnerships with companies including the St. Bernard Project, which employs military vets.
FAQ
Is automation important in manufacturing?
Automation is important not only for manufacturers but also for service providers. They can provide services more quickly and efficiently thanks to automation. It reduces human errors and improves productivity, which in turn helps them lower their costs.
What does warehouse refer to?
A warehouse is an area where goods are stored before being sold. It can be either an indoor or outdoor space. It may also be an indoor space or an outdoor area.
What does it take for a logistics enterprise to succeed?
To run a successful logistics company, you need a lot knowledge and skills. You must have good communication skills to interact effectively with your clients and suppliers. You need to understand how to analyze data and draw conclusions from it. You must be able manage stress and pressure under pressure. You need to be innovative and creative to come up with new ways to increase efficiency. You will need strong leadership skills to motivate and direct your team members towards achieving their organizational goals.
It is important to be organized and efficient in order to meet tight deadlines.
Statistics
- [54][55] These are the top 50 countries by the total value of manufacturing output in US dollars for its noted year according to World Bank.[56] (en.wikipedia.org)
- (2:04) MTO is a production technique wherein products are customized according to customer specifications, and production only starts after an order is received. (oracle.com)
- In 2021, an estimated 12.1 million Americans work in the manufacturing sector.6 (investopedia.com)
- You can multiply the result by 100 to get the total percent of monthly overhead. (investopedia.com)
- In the United States, for example, manufacturing makes up 15% of the economic output. (twi-global.com)
External Links
How To
How to Use the 5S to Increase Productivity In Manufacturing
5S stands to stand for "Sort", “Set In Order", “Standardize", and "Store". Toyota Motor Corporation invented the 5S strategy in 1954. It allows companies to improve their work environment, thereby achieving greater efficiency.
This method has the basic goal of standardizing production processes to make them repeatable. Cleaning, sorting and packing are all done daily. Through these actions, workers can perform their jobs more efficiently because they know what to expect from them.
There are five steps that you need to follow in order to implement 5S. Each step requires a different action, which increases efficiency. By sorting, for example, you make it easy to find the items later. You arrange items by placing them in an order. Next, organize your inventory into categories and store them in containers that are easily accessible. Finally, when you label your containers, you ensure everything is labeled correctly.
Employees must be able to critically examine their work practices. Employees need to understand the reasons they do certain jobs and determine if there is a better way. In order to use the 5S system effectively, they must be able to learn new skills.
In addition to increasing efficiency, the 5S method also improves morale and teamwork among employees. They will feel motivated to strive for higher levels of efficiency once they start to see results.