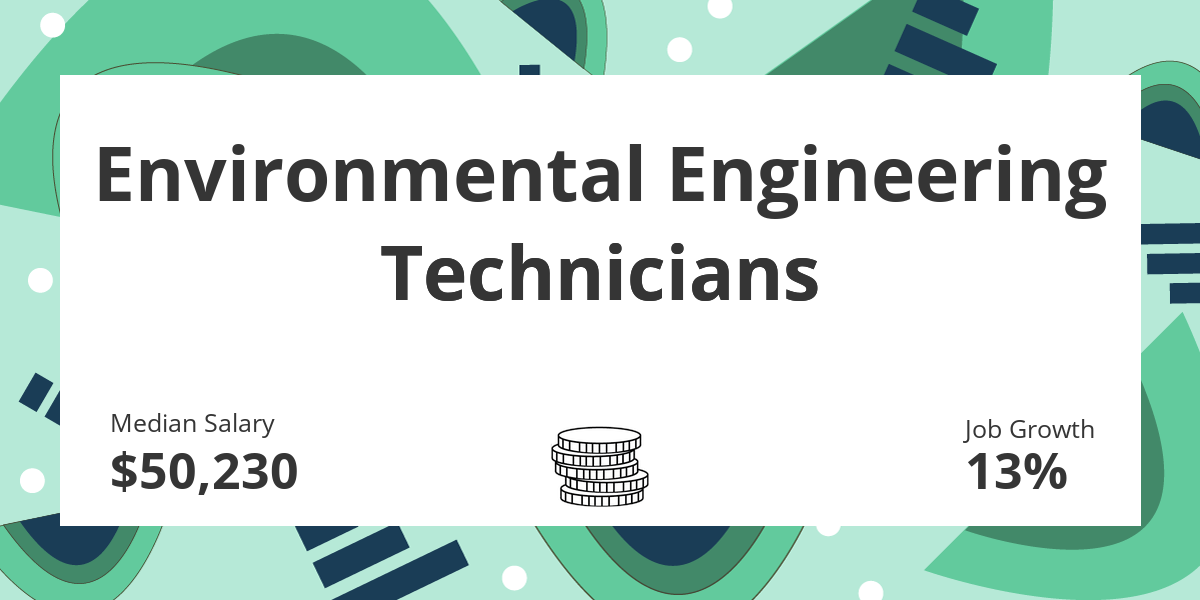
There are many types to choose from, but which one would be best for your company? Learn about Discrete, Process, Job shop, and Continuous manufacturing. Each type has their own advantages and drawbacks. This article will describe the differences among these four types. The best model for you business will depend on your industry and location. Once you have chosen the best type for your business, you must consider sales, production, as well as quality control.
Discrete manufacturing
Discrete production is when distinct products are manufactured. These products include automobiles, toys, and aeroplanes. Discrete manufacturing allows companies the freedom to concentrate on specific products rather than mass production. By integrating multiple manufacturing processes, discrete manufacturing allows you to create unique parts for your aircraft. High-tech products can be made by discrete manufacturing.
Discrete manufacturing produces distinct items. Instead of making multiple identical products, discrete manufacture produces distinct items that can easily be identified using serial numbers, labels, or other numerical attributes. For example, a smartphone could be composed of several parts that were manufactured in different states. Each part is assembled only after the final product has been sold. This is also true for the bag. It may include parts from multiple plants, including the Missouri headquarters.
Process manufacturing
Process manufacturing refers to a type of manufacturing that uses formulas and recipes. The term process manufacturing contrasts with discrete manufacturing, which is concerned with individual units, bills of materials, and the assembly of components. As a result, the two methods of manufacturing have very different goals. Each of these methods is important in the manufacturing process. These are three ways to distinguish between process and discrete manufacturing. Let's take a look at each of them.
Batch process manufacturing is similar to continuous process manufacturing, but it uses larger batches of raw materials and runs around the clock. Batch process manufacturing is used in many industries, including pharmaceuticals, paper production and bookbinding. However, it is not the right choice for every industry. For smaller businesses, it can be too expensive and complex. This is why large-scale companies often use it when they need to make large quantities.
Factory job shop
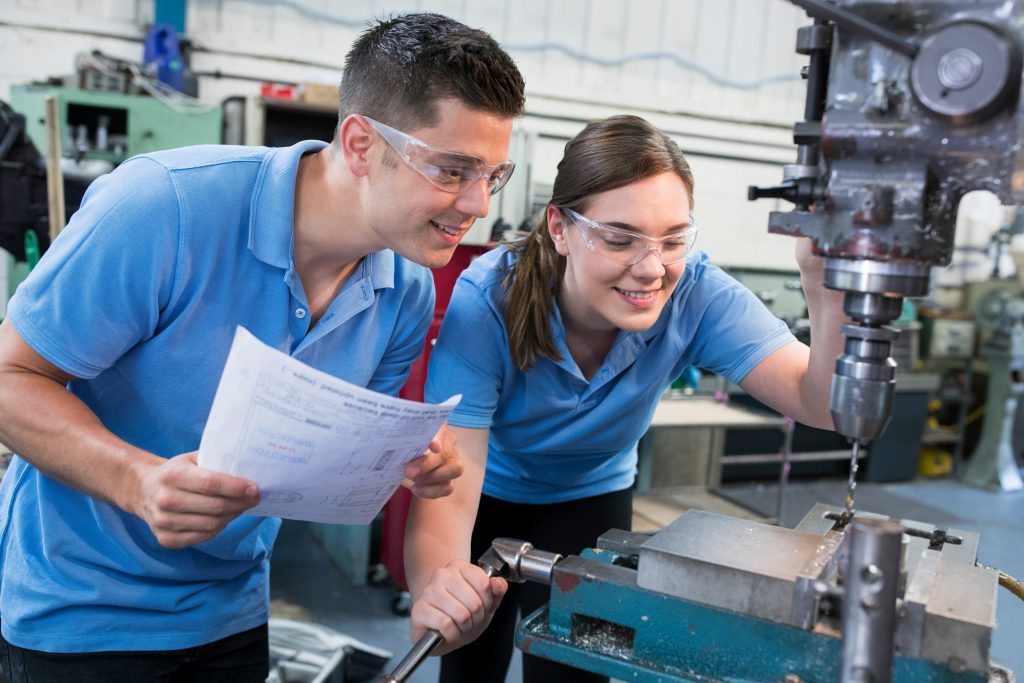
Job shop manufacturing is small-scale manufacturing that specializes in custom, semi-custom, and batch manufacturing. After each job is complete, job shop systems can move to the next. This type of production is also known lean manufacturing. It is more efficient to use a single shift than many other methods. Here are some of the benefits of job shop manufacturing. Learn more about this manufacturing method. It might be a good option for your business if you need to manufacture products or services.
First, job shop efficiency must be improved. A critical factor in achieving a lean manufacturing system is incorporating new manufacturing principles. These principles are particularly relevant for high-volume operations and emphasize quality control and just in-time production. Job shops can increase productivity and decrease costs by adopting new manufacturing methods. Also, each job should be completed one by one, so there shouldn't be any queues.
Continuous manufacturing
Continuous manufacturing's greatest benefit is its flexibility in tracking. This is particularly helpful when it comes to product failure, since the quantity of raw input material and the time stamp on each production line can help to identify when a batch of drug is defective. This allows the manufacturer to reduce waste and minimize the possibility of a product shortage by allowing for better tracking. In the pharmaceutical industry, continuous manufacturing is also gaining popularity.
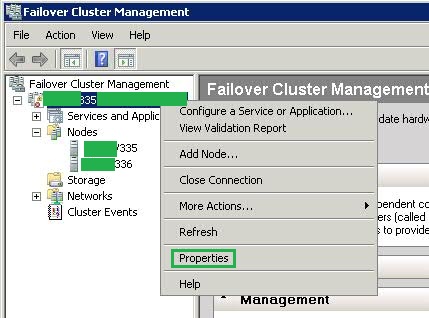
Although continuous manufacturing has many benefits, implementation can be difficult. The fact that continuous manufacturing is not fully integrated into the company is often what hinders its implementation. Continuous manufacturing is a great opportunity for the pharmaceutical industry. The process must be seamless and integrate with continuous flow and end to end integration for it to be effective. The pharmaceutical industry has long recognized the benefits of continuous manufacturing, but implementation has been slow.
FAQ
What is the difference between Production Planning and Scheduling?
Production Planning (PP), is the process of deciding what production needs to take place at any given time. Forecasting demand is one way to do this.
Scheduling involves the assignment of dates and times to tasks in order to complete them within the timeframe.
How can we reduce manufacturing overproduction?
It is essential to find better ways to manage inventory to reduce overproduction. This would reduce the time needed to manage inventory. We could use these resources to do other productive tasks.
You can do this by adopting a Kanban method. A Kanban board, a visual display to show the progress of work, is called a Kanban board. Kanban systems allow work items to move through different states until they reach their final destination. Each state is assigned a different priority.
If work is moving from one stage to the other, then the current task can be completed and moved on to the next. It is possible to keep a task in the beginning stages until it gets to the end.
This allows you to keep work moving along while making sure that no work gets neglected. Managers can monitor the work being done by Kanban boards to see what is happening at any given time. This allows them the ability to adjust their workflow using real-time data.
Lean manufacturing can also be used to reduce inventory levels. Lean manufacturing focuses on eliminating waste throughout the entire production chain. Anything that doesn't add value to the product is considered waste. The following are examples of common waste types:
-
Overproduction
-
Inventory
-
Unnecessary packaging
-
Exceed materials
These ideas can help manufacturers improve efficiency and reduce costs.
What are the 7 Rs of logistics management?
The acronym 7R's of Logistic is an acronym that stands for seven fundamental principles of logistics management. It was developed and published by the International Association of Business Logisticians in 2004 as part of the "Seven Principles of Logistics Management".
The following letters form the acronym:
-
Responsible - ensure that all actions taken are within legal requirements and are not harmful to others.
-
Reliable - You can have confidence that you will fulfill your promises.
-
Use resources effectively and sparingly.
-
Realistic - Take into consideration all aspects of operations including cost-effectiveness, environmental impact, and other factors.
-
Respectful - treat people fairly and equitably.
-
Be resourceful: Look for opportunities to save money or increase productivity.
-
Recognizable provides value-added products and services to customers
What are the four types in manufacturing?
Manufacturing is the process that transforms raw materials into useful products. It includes many different activities like designing, building and testing, packaging, shipping and selling, as well as servicing.
Statistics
- Many factories witnessed a 30% increase in output due to the shift to electric motors. (en.wikipedia.org)
- In 2021, an estimated 12.1 million Americans work in the manufacturing sector.6 (investopedia.com)
- According to the United Nations Industrial Development Organization (UNIDO), China is the top manufacturer worldwide by 2019 output, producing 28.7% of the total global manufacturing output, followed by the United States, Japan, Germany, and India.[52][53] (en.wikipedia.org)
- In the United States, for example, manufacturing makes up 15% of the economic output. (twi-global.com)
- Job #1 is delivering the ordered product according to specifications: color, size, brand, and quantity. (netsuite.com)
External Links
How To
How to Use the Just In Time Method in Production
Just-in-time (JIT) is a method that is used to reduce costs and maximize efficiency in business processes. It's the process of obtaining the right amount and timing of resources when you need them. This means that only what you use is charged to your account. Frederick Taylor developed the concept while working as foreman in early 1900s. After observing how workers were paid overtime for late work, he realized that overtime was a common practice. He then concluded that if he could ensure that workers had enough time to do their job before starting to work, this would improve productivity.
JIT is an acronym that means you need to plan ahead so you don’t waste your money. Look at your entire project, from start to end. Make sure you have enough resources in place to deal with any unexpected problems. If you anticipate that there might be problems, you'll have enough people and equipment to fix them. This will prevent you from spending extra money on unnecessary things.
There are several types of JIT techniques:
-
Demand-driven: This JIT is where you place regular orders for the parts/materials that are needed for your project. This will allow for you to track the material that you have left after using it. This will allow to you estimate the time it will take for more to be produced.
-
Inventory-based: This type allows you to stock the materials needed for your projects ahead of time. This allows you predict the amount you can expect to sell.
-
Project-driven : This is a method where you make sure that enough money is set aside to pay the project's cost. Once you have an idea of how much material you will need, you can purchase the necessary materials.
-
Resource-based JIT : This is probably the most popular type of JIT. You assign certain resources based off demand. If you have many orders, you will assign more people to manage them. If you don't receive many orders, then you'll assign fewer employees to handle the load.
-
Cost-based: This is a similar approach to resource-based but you are not only concerned with how many people you have, but also how much each one costs.
-
Price-based: This approach is very similar to the cost-based method except that you don't look at individual workers costs but the total cost of the company.
-
Material-based: This is very similar to cost-based but instead of looking at total costs of the company you are concerned with how many raw materials you use on an average.
-
Time-based JIT: A variation on resource-based JIT. Instead of focusing on how much each employee costs, you focus on how long it takes to complete the project.
-
Quality-based JIT is another variant of resource-based JIT. Instead of thinking about the cost of each employee or the time it takes to produce something, you focus on how good your product quality.
-
Value-based JIT : This is the newest type of JIT. In this scenario, you're not concerned about how products perform or whether customers expect them to meet their expectations. Instead, you're focused on how much value you add to the market.
-
Stock-based. This method is inventory-based and focuses only on the actual production at any given point. This method is useful when you want to increase production while decreasing inventory.
-
Just-in time (JIT), planning: This is a combination JIT/supply chain management. This refers to the scheduling of the delivery of components as soon after they are ordered. It reduces lead times and improves throughput.