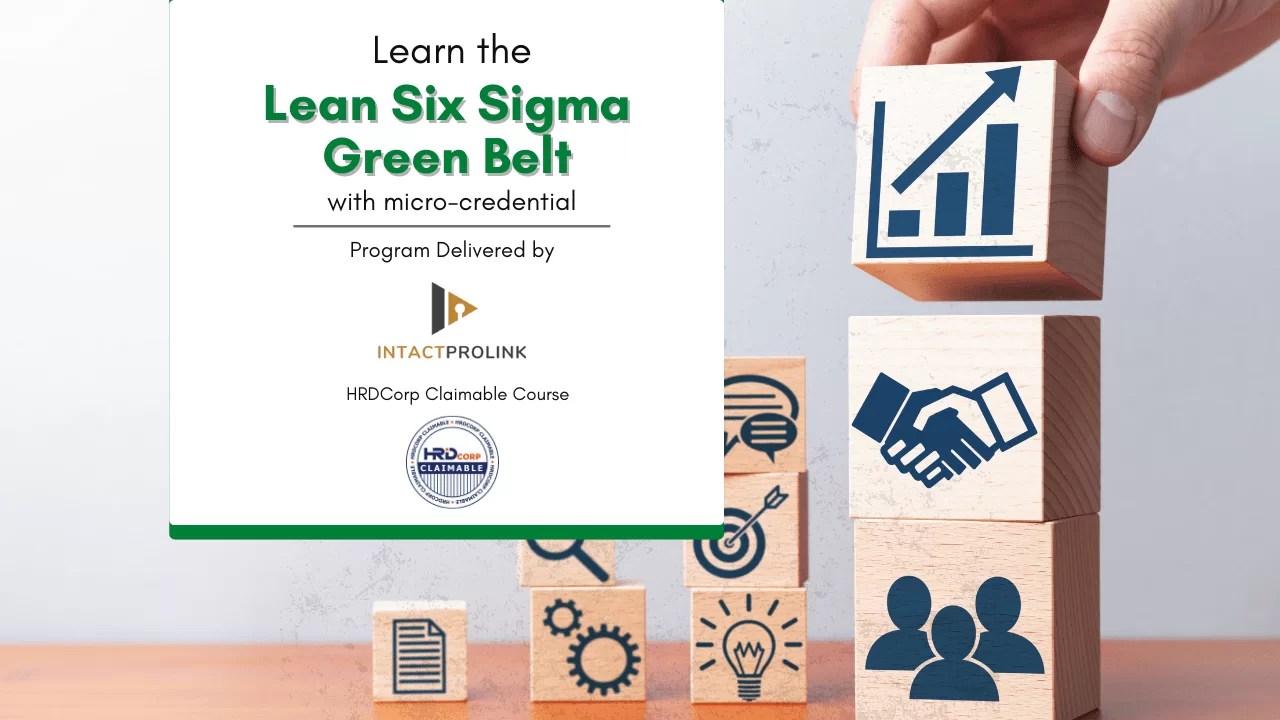
The job of a logistics coordinator involves ensuring that goods are in the right place at the right time and arrive in the most efficient and cost-effective way possible. In this field, you'll ensure that goods are delivered efficiently to your customer's door. Our article provides more information on logistics. Also, learn about the job of a customer support specialist, inventory analyst, or supply chain manager. Here are some of the most important jobs you will find in logistics.
Logistics coordinator
Monster has thousands upon thousands of job openings for logistic coordinators. This job requires extensive training. Candidates with minimal experience can usually take up training through an internship or apprenticeship, although they may also need to have some industry experience. You might also be interested in applying for a job at the logistics coordinator position if your previous experience is extensive.
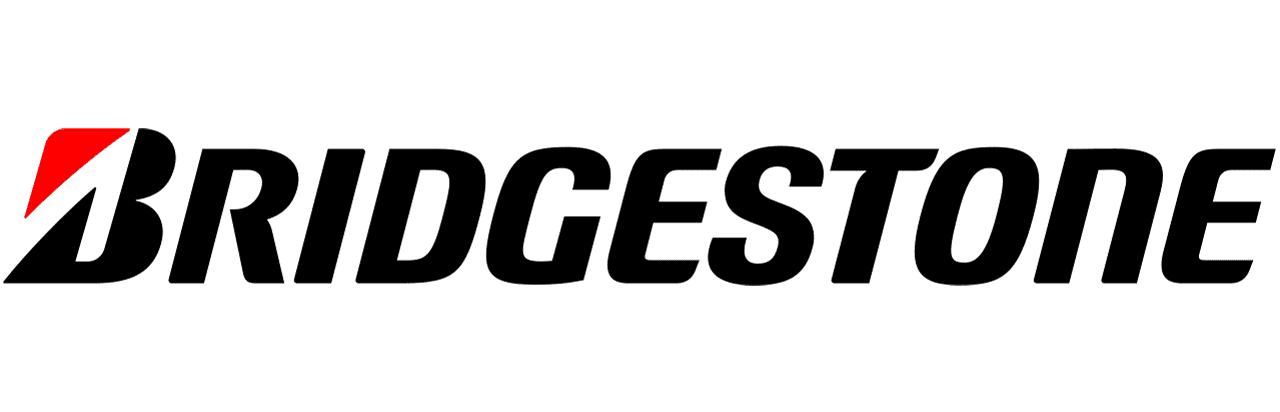
Customer service specialist
Customer service specialists are responsible for managing and delivering customer service. They maintain contact with customers, coordinate inland transport, and address customer concerns and complaints. They also manage customer relationships and coordinate appointments. As a customer support specialist, you will also coordinate all necessary documents and documentation to ensure timely and affordable delivery.
Inventory analyst
An Inventory Analyst is responsible to maintain service level and improve inventory productivity. Their primary responsibilities include order fulfillment for TSC Feed programmes, as well managing the day to day activities of inventory replenishment. They manage inventory levels for their respective product categories to support assortment and merchandise planning. They monitor trends and make plans for article-site replenishment. They can also be involved in marketing and promotion activities. They often analyze sales data and create new strategies to improve business efficiency.
Supply chain manager
The supply chain manager manages the flow of goods and materials from suppliers to customers and manufacturers. The role requires a wide range of skills, and a bachelor's degree is typically required. Some employers also prefer candidates with master's degrees in business administration. You can apply for the job of supply chain manager in many ways. Learn more about this career. Consider getting an associate's in business administration if you are interested in a career in supply chain management.
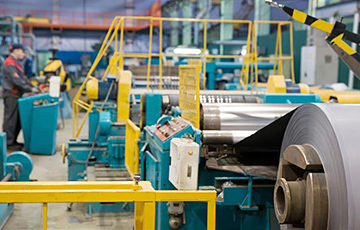
Freight agent
Your cargo and freight agent responsibilities should be included in your job description. To make it easy for potential applicants to understand what they are required to do daily, the job description must include a list listing all of the key responsibilities. Use strong action verbs to grab the attention of qualified candidates. Your job description should include a detailed list indicating the qualifications you will need to fill this role.
FAQ
What are the differences between these four types?
Manufacturing refers to the transformation of raw materials into useful products by using machines and processes. Manufacturing involves many activities, including designing, building, testing and packaging, shipping, selling, service, and so on.
What are the responsibilities of a manufacturing manager
Manufacturing managers must ensure that manufacturing processes are efficient, effective, and cost-effective. They must also be alert to any potential problems and take appropriate action.
They should also know how to communicate with other departments such as sales and marketing.
They should be informed about industry trends and be able make use of this information to improve their productivity and efficiency.
What is production planning?
Production Planning is the creation of a plan to cover all aspects, such as scheduling, budgeting. Location, crew, equipment, props and other details. This document is designed to make sure everything is ready for when you're ready to shoot. It should also provide information about how best to produce the best results while on set. This includes information on shooting times, locations, cast lists and crew details.
First, you need to plan what you want to film. You may have decided where to shoot or even specific locations you want to use. Once you have determined your scenes and locations, it is time to start figuring out the elements that you will need for each scene. Perhaps you have decided that you need to buy a car but aren't sure which model. In this case, you could start looking up cars online to find out what models are available and then narrow your choices by choosing between different makes and models.
Once you have found the right car, you can start thinking about extras. Do you have people who need to be seated in the front seat? Or maybe you just need someone to push the car around. Maybe you'd like to change the interior from black to a white color. These questions can help you decide the right look for your car. Another thing you can do is think about what type of shots are desired. Will you be filming close-ups or wide angles? Maybe you want to show the engine and the steering wheel. This will allow you to determine the type of car you want.
Once you've determined the above, it is time to start creating a calendar. You can use a schedule to determine when and where you need it to be shot. Each day will include the time when you need to arrive at the location, when you need to leave and when you need to return home. So everyone is clear about what they need to do. If you need to hire extra staff, you can make sure you book them in advance. It's not worth paying someone to show up if you haven't told him.
Your schedule will also have to be adjusted to reflect the number of days required to film. Some projects only take one or two days, while others may last weeks. When creating your schedule, be aware of whether you need more shots per day. Shooting multiple takes over the same location will increase costs and take longer to complete. If you are unsure if you need multiple takes, it is better to err on the side of caution and shoot fewer takes rather than risk wasting money.
Another important aspect of production planning is setting budgets. Setting a realistic budget is essential as it will allow you to work within your means. Keep in mind that you can always reduce your budget if you face unexpected difficulties. But, don't underestimate how much money you'll spend. If you underestimate how much something costs, you'll have less money to pay for other items.
Planning production is a tedious process. Once you have a good understanding of how everything works together, planning future projects becomes easy.
Statistics
- (2:04) MTO is a production technique wherein products are customized according to customer specifications, and production only starts after an order is received. (oracle.com)
- Many factories witnessed a 30% increase in output due to the shift to electric motors. (en.wikipedia.org)
- You can multiply the result by 100 to get the total percent of monthly overhead. (investopedia.com)
- According to a Statista study, U.S. businesses spent $1.63 trillion on logistics in 2019, moving goods from origin to end user through various supply chain network segments. (netsuite.com)
- Job #1 is delivering the ordered product according to specifications: color, size, brand, and quantity. (netsuite.com)
External Links
How To
How to Use 5S for Increasing Productivity in Manufacturing
5S stands for "Sort", 'Set In Order", 'Standardize', & Separate>. Toyota Motor Corporation created the 5S methodology in 1954. It improves the work environment and helps companies to achieve greater efficiency.
The idea behind standardizing production processes is to make them repeatable and measurable. This means that every day tasks such cleaning, sorting/storing, packing, and labeling can be performed. Because workers know what they can expect, this helps them perform their jobs more efficiently.
Five steps are required to implement 5S: Sort, Set In Order, Standardize. Separate. Each step requires a different action, which increases efficiency. By sorting, for example, you make it easy to find the items later. Once you have placed items in an ordered fashion, you will put them together. After you have divided your inventory into groups you can store them in easy-to-reach containers. Finally, when you label your containers, you ensure everything is labeled correctly.
This requires employees to critically evaluate how they work. Employees must be able to see why they do what they do and find a way to achieve them without having to rely on their old methods. They must learn new skills and techniques in order to implement the 5S system.
In addition to increasing efficiency, the 5S method also improves morale and teamwork among employees. They will feel motivated to strive for higher levels of efficiency once they start to see results.